As I used to be wrapping up my evaluation of the No.22 Nice Divide, an thought struck me. Why not return it in individual and take a look at the way it was made, too?
I’m all the time down for a street journey, and upstate New York is a beautiful space to trip, so a number of emails later, plans had been set and luggage had been packed. Right here’s how No.22 Bicycles makes their attractive titanium street and gravel bikes and produces among the finest anodized finishes within the enterprise…
A little bit of backstory
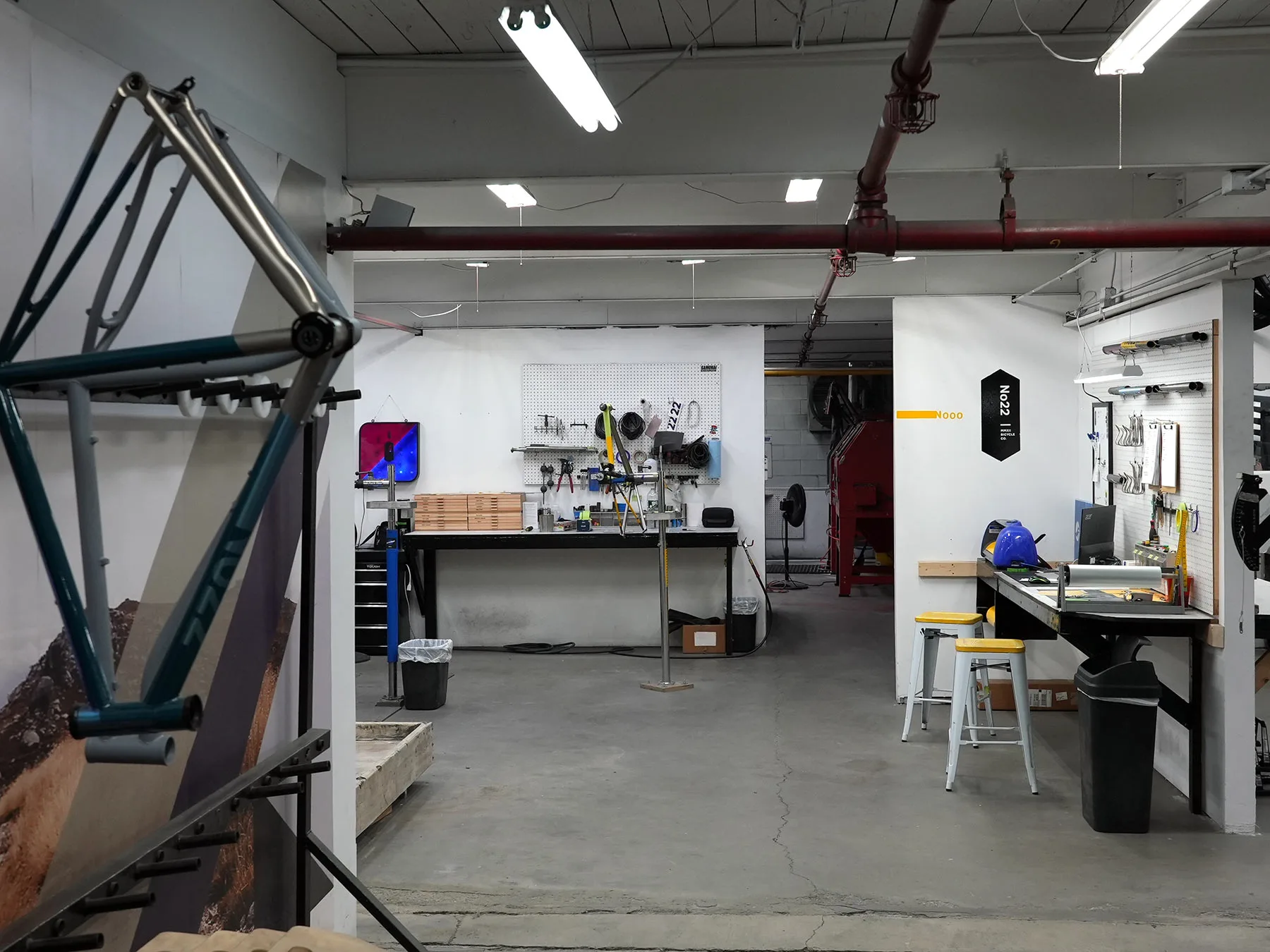
If beginning a hand-crafted bicycle firm from scratch looks as if a giant, difficult course of, you could be stunned to know that they shipped their first bike inside weeks of opening this house.
That’s partly as a result of they began out small. There was solely energy line to the breaker field, which fed a number of lights and retailers.
Whereas co-founders Mike and Bryce got here from the fanatic aspect somewhat than the biking business, they introduced a number of of the designers and builders from Saratoga Frameworks (previously Serrotta). Whereas that founding crew got here from a longtime operation, right here that they had to determine the place to place issues, get energy to them, and create their very own processes that may make No.22 distinctive. (Learn our interview with Mike for a deeper dive on their origin story)
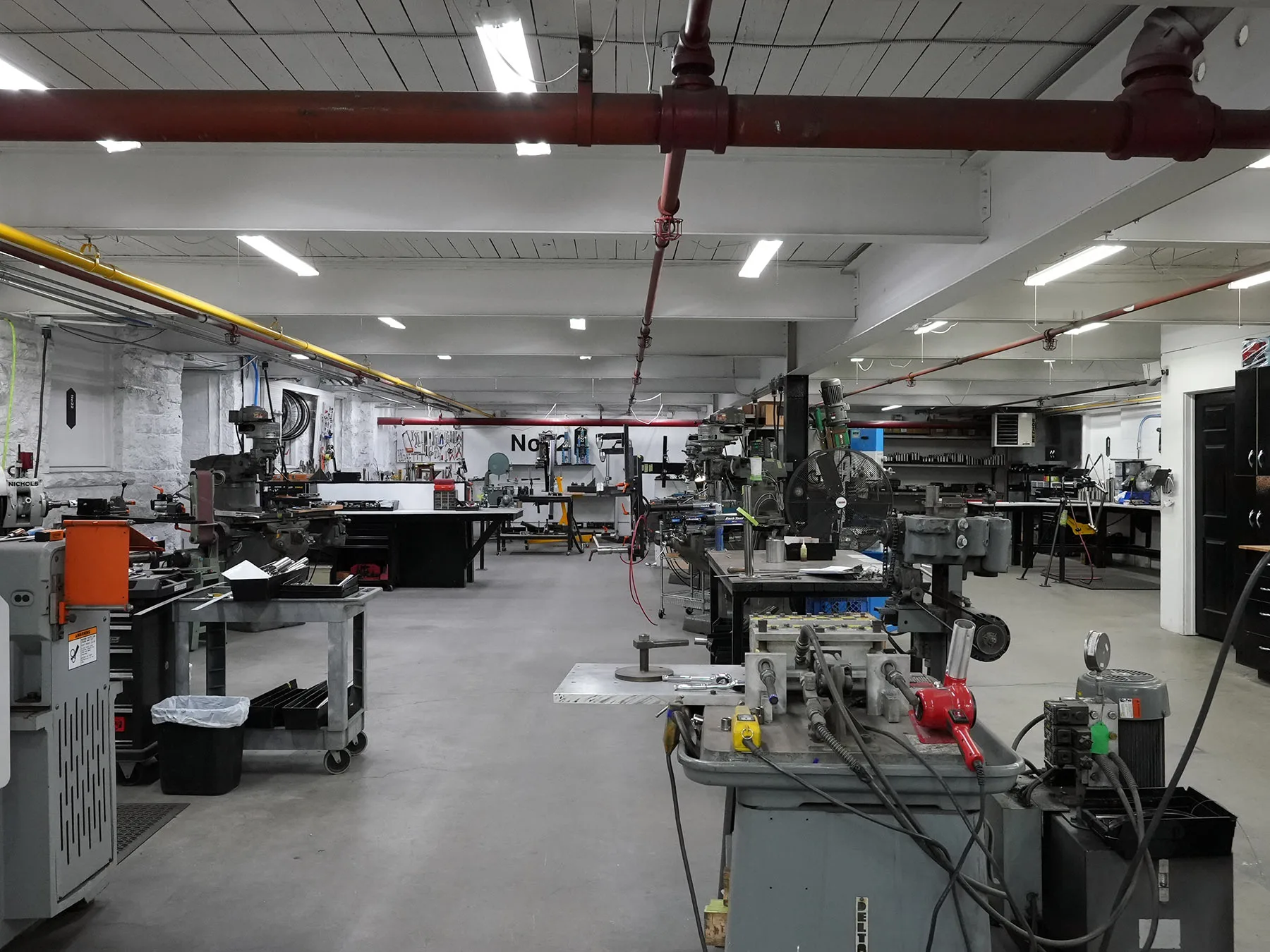
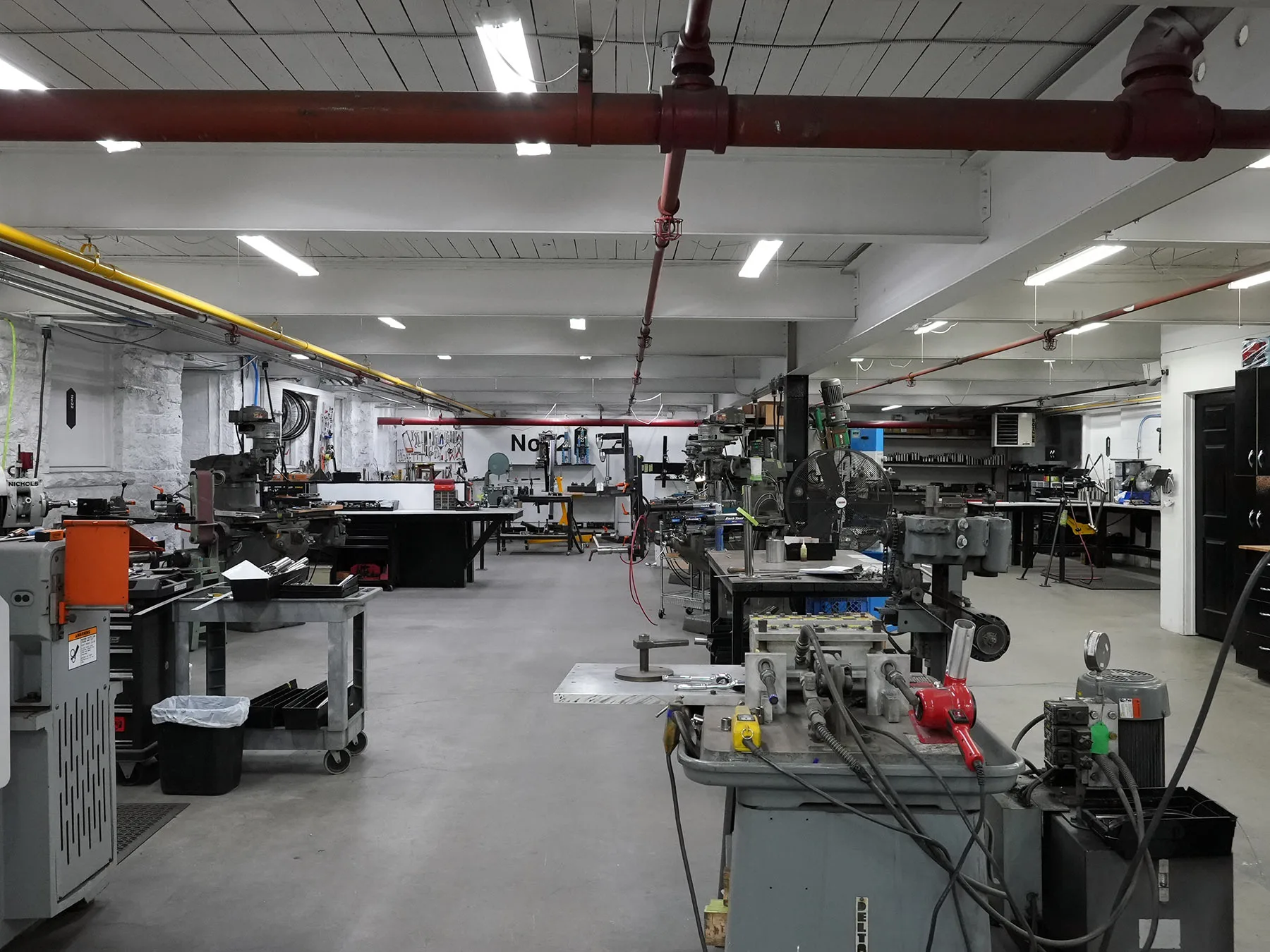
It began with simply 5 folks, in a smaller a part of this house, and everybody was mainly in the identical room. They stored every little thing shut in order that they didn’t need to stroll all the way in which throughout the constructing. However as they’ve grown, issues have unfold out and extra machines had been added.
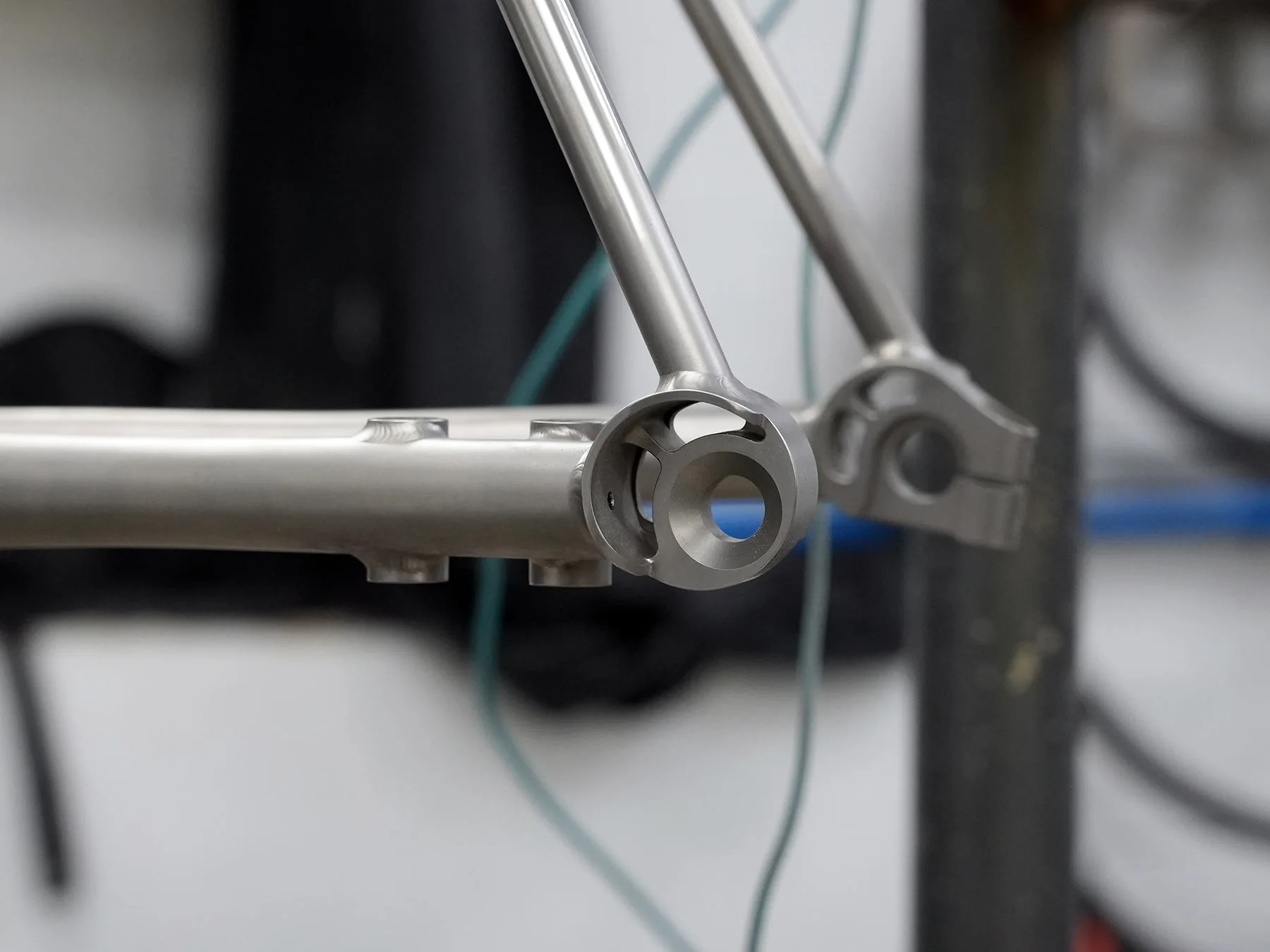
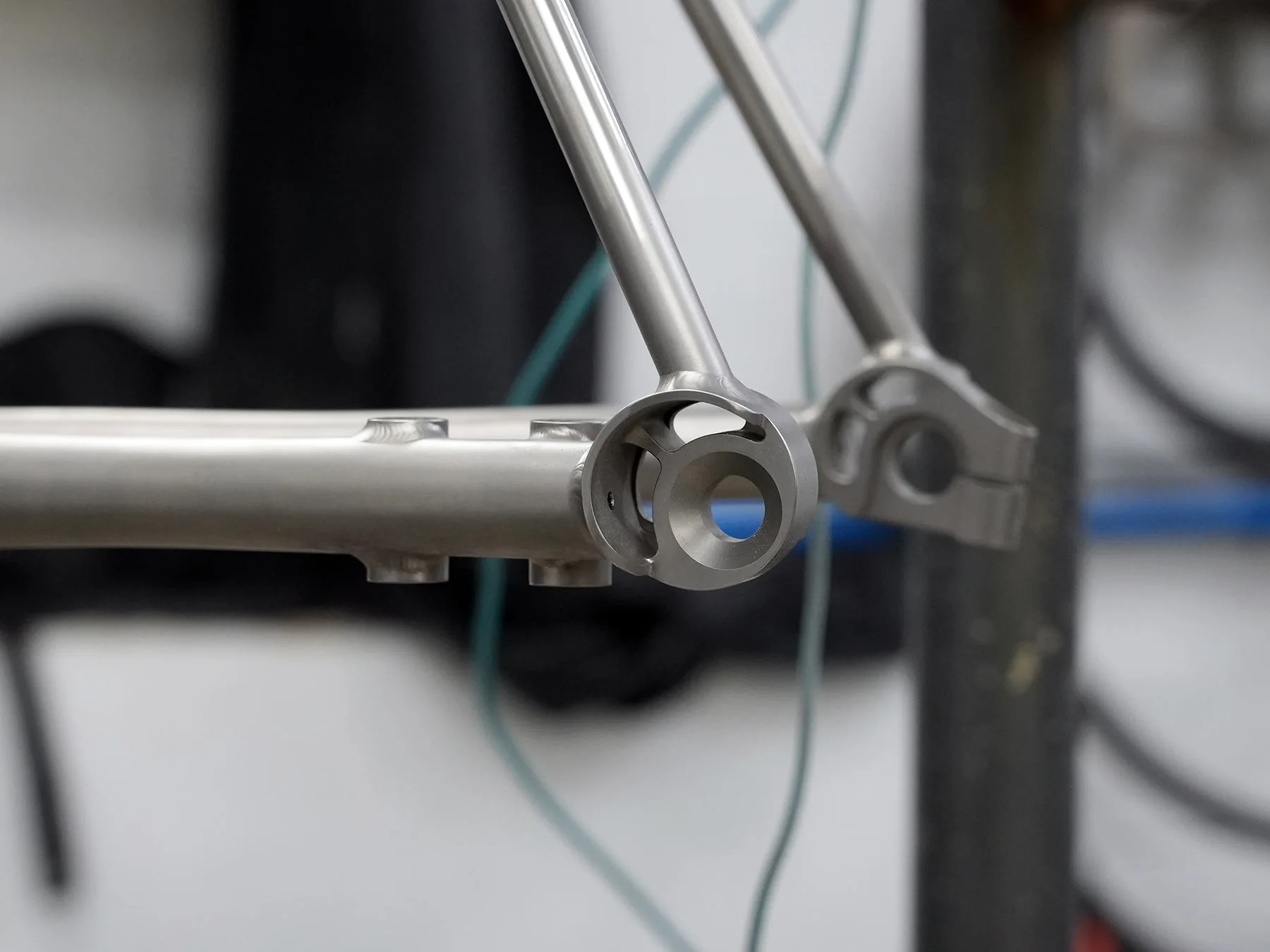
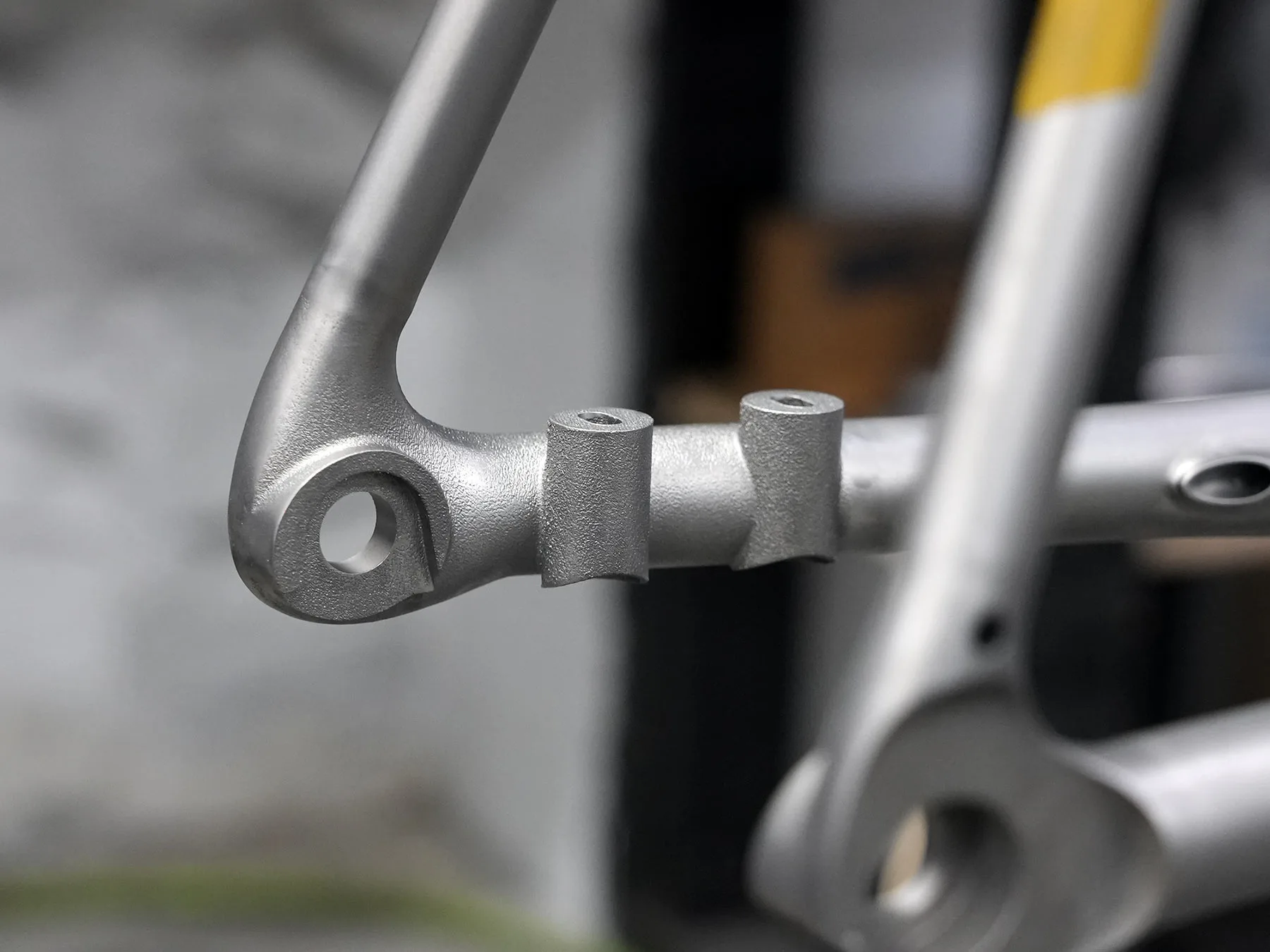
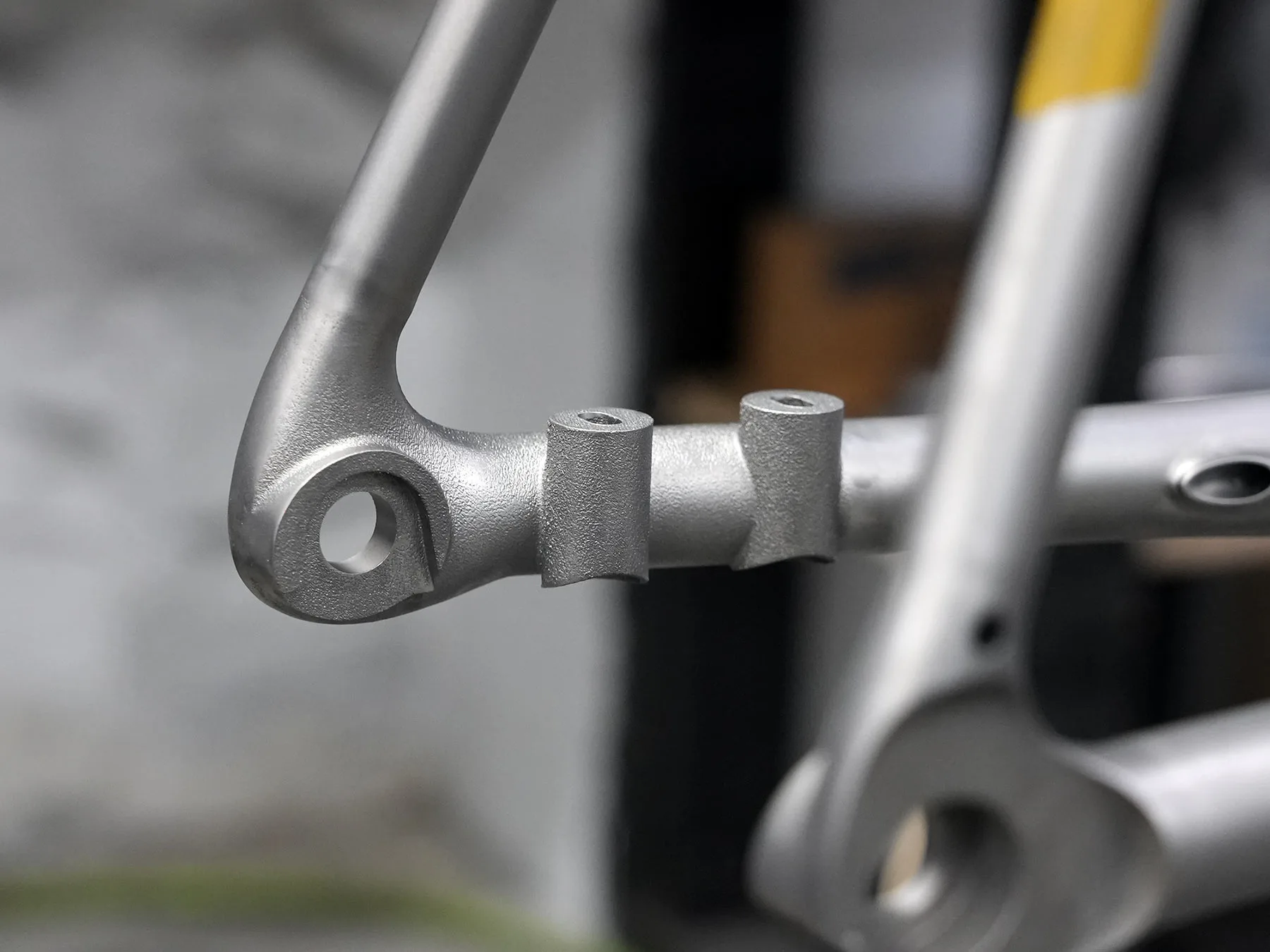
Now, they do every little thing in home besides the 3D printing of their stem and dropouts, these are carried out at Silca.
Proven above are earlier machined dropouts (left), however they’ve switched to 3D printed components (proper) to get extra constant (and ideal) alignment between brake caliper mounts and the via axle.
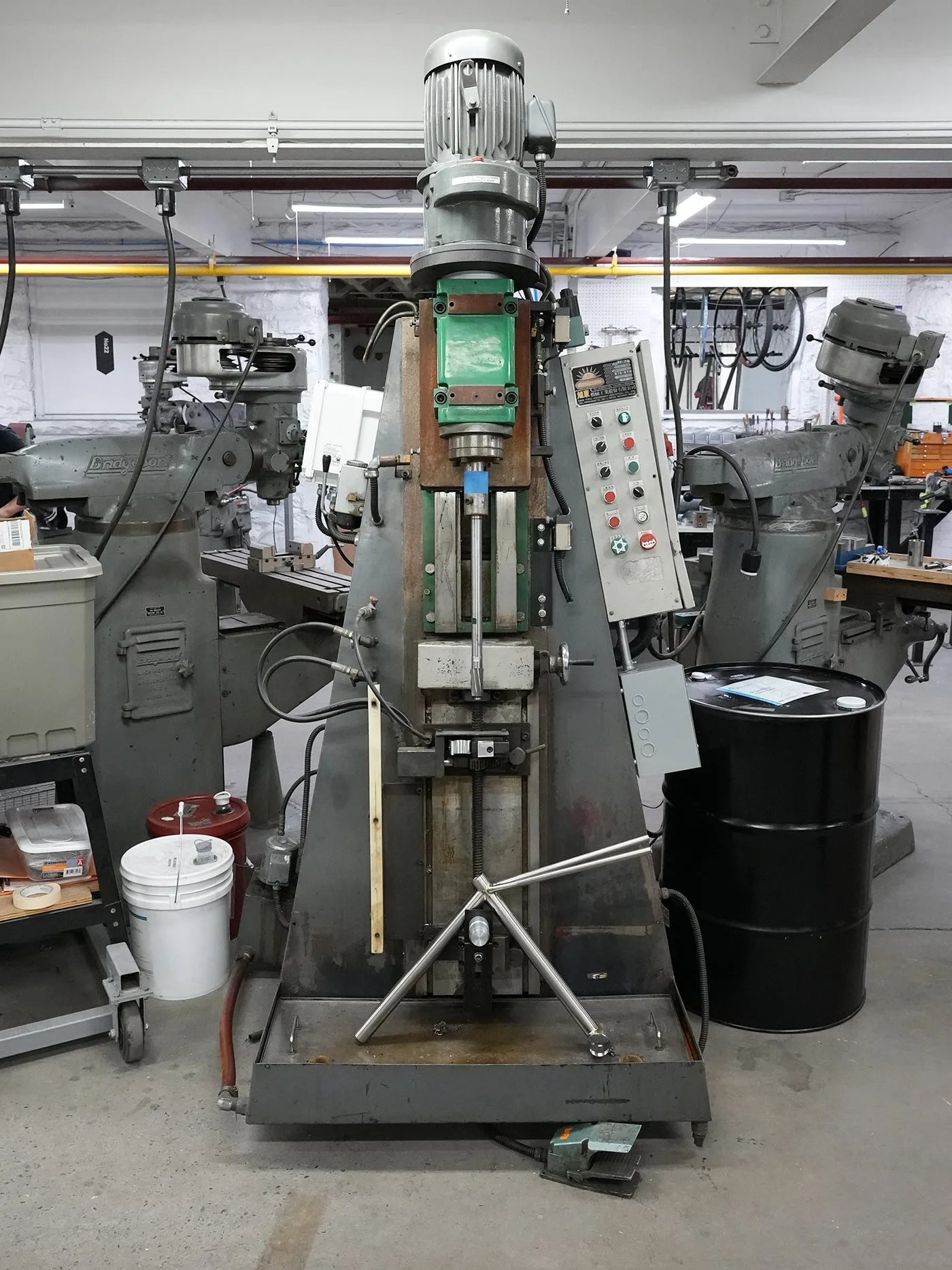
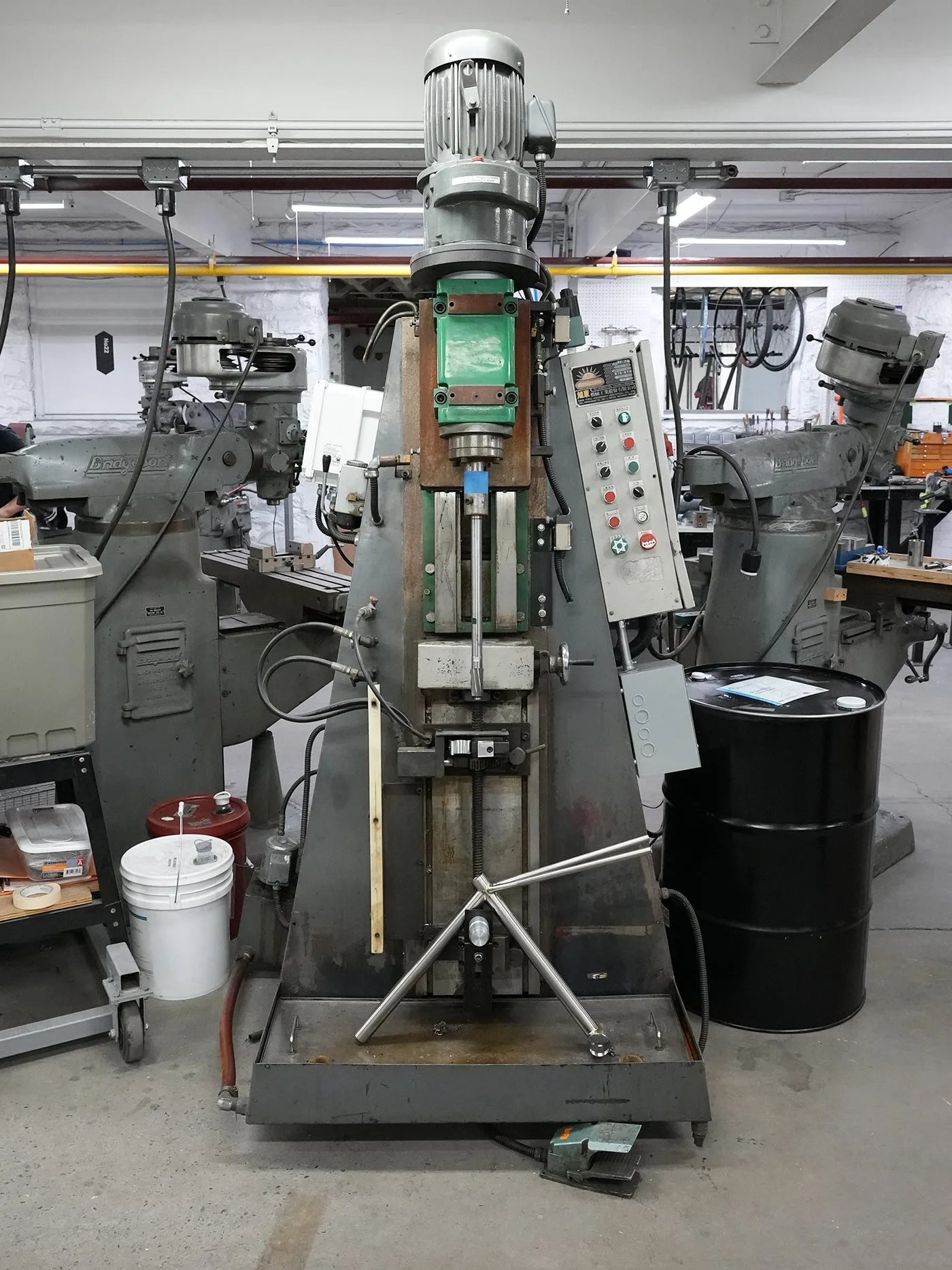
Throughout COVID, they couldn’t are available and work as a workforce, in order that they used that downtime to maneuver the heavy equipment, paint the whole inside and add extra, brighter lighting. All of the machines had been put nearer to the place they wanted to be, making everybody extra environment friendly. The result’s the manufacturing facility you see right here.
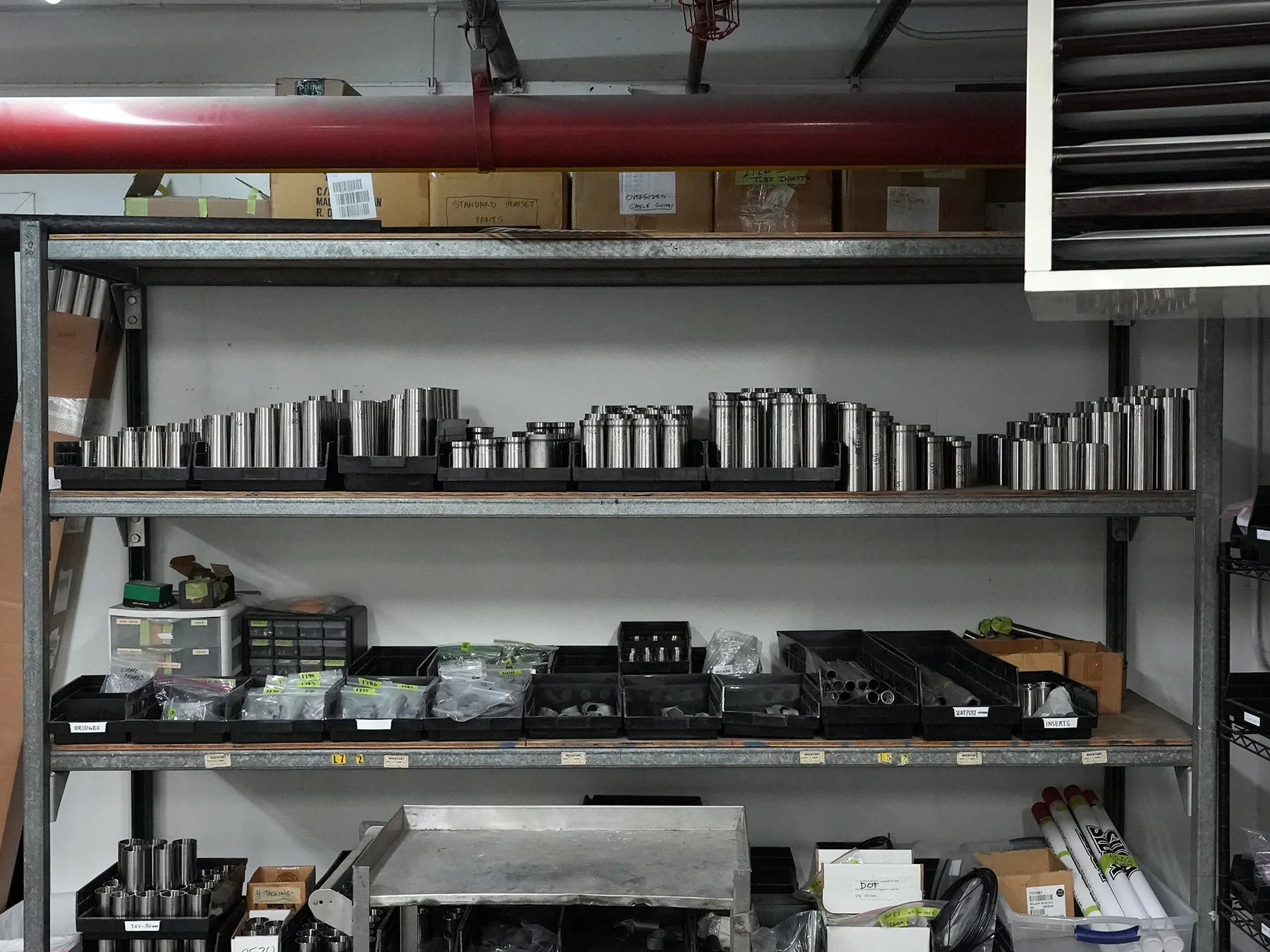
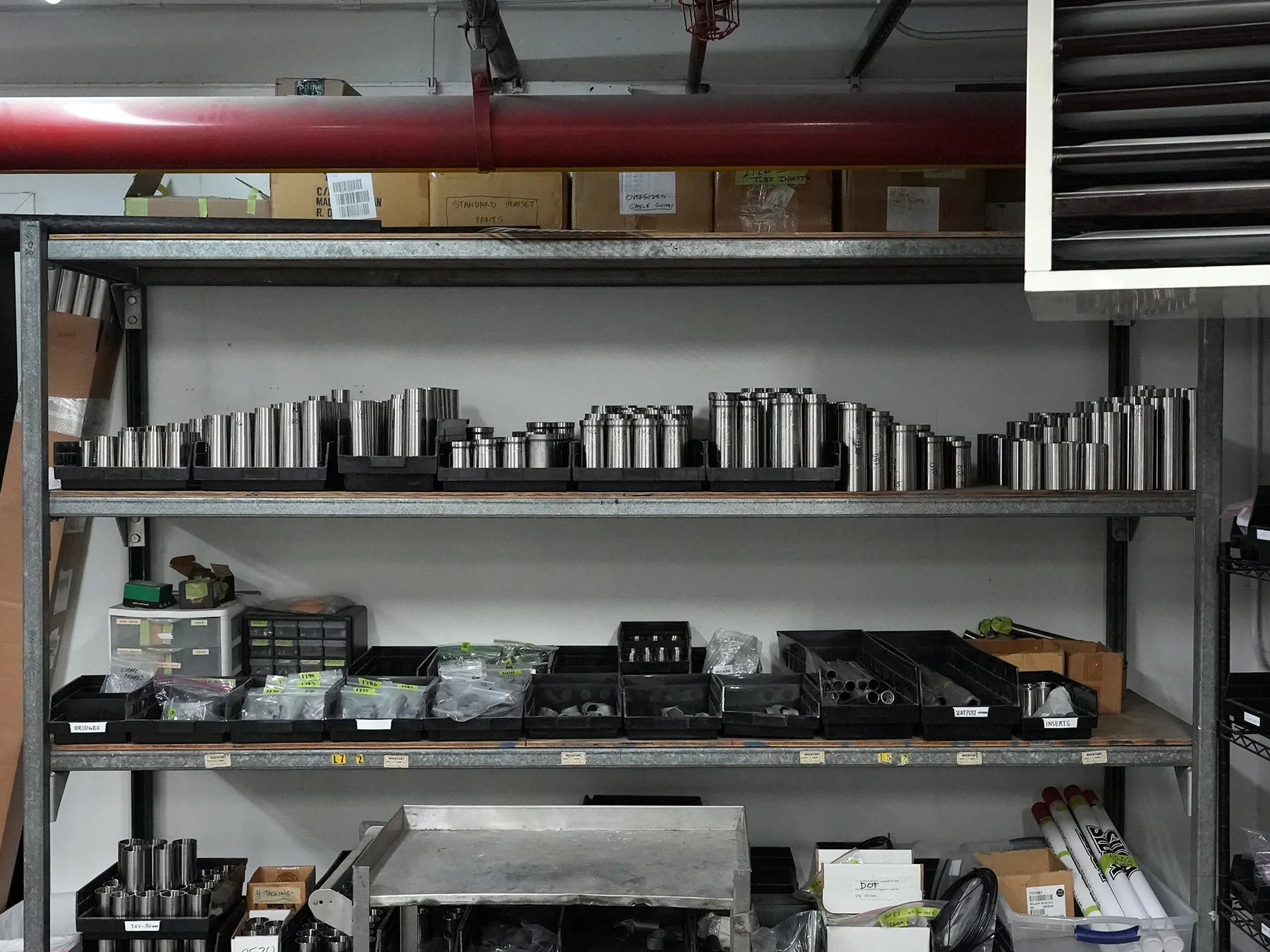
After they first began, they had been ordering a pair bikes’ price of tubing at a time, as a result of that’s all they may afford. Which meant each tube was from a special batch, which meant they anodized in a different way, which was a problem.
Now, they’re ordering six months or extra price of tubing, and making extra bikes. It’s nonetheless a comparatively small quantity – at Serrotta, they had been making 12 frames a day. Right here, they make 4 every week.
Skipping Forward to Paint & Anodizing
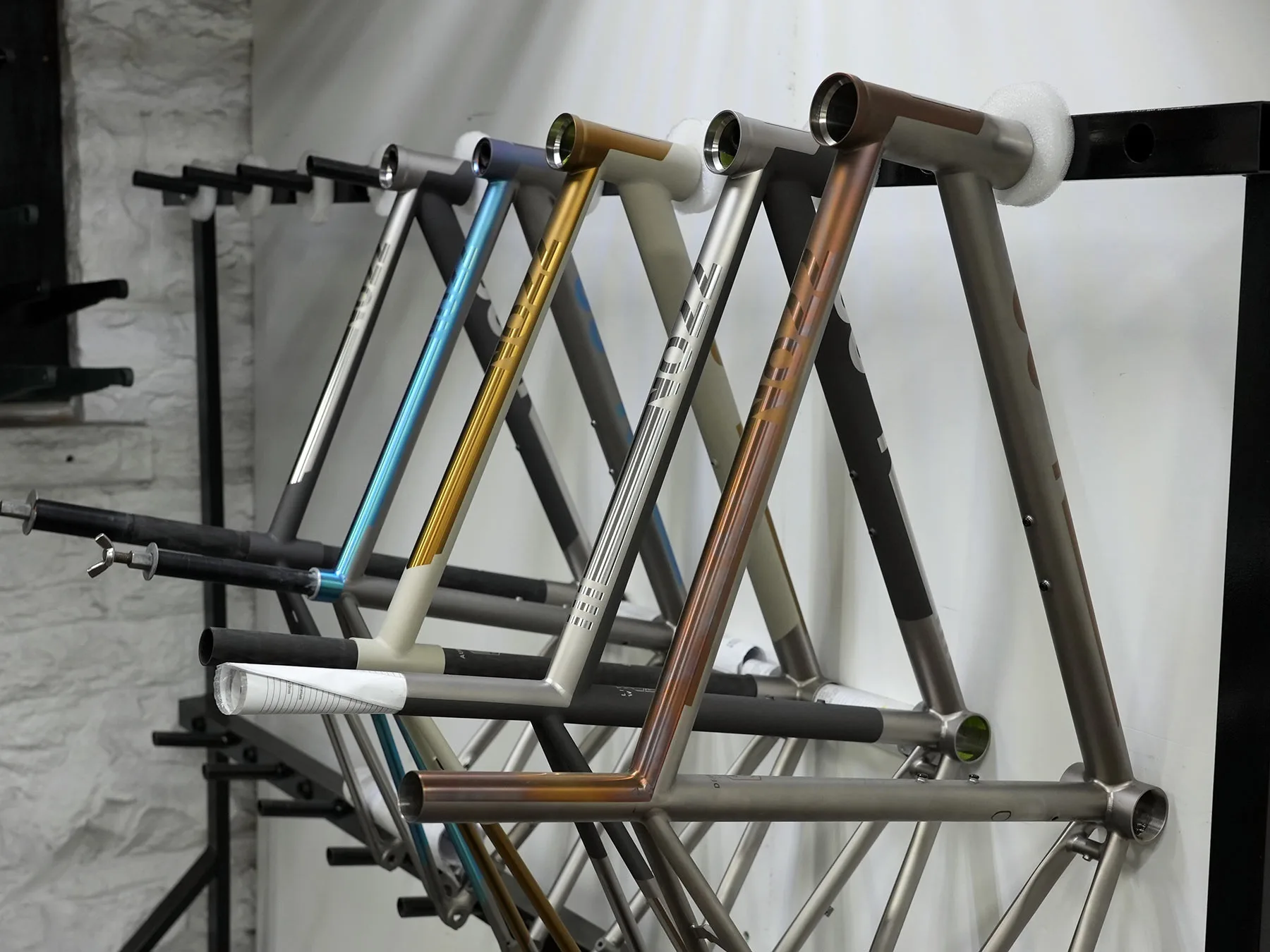
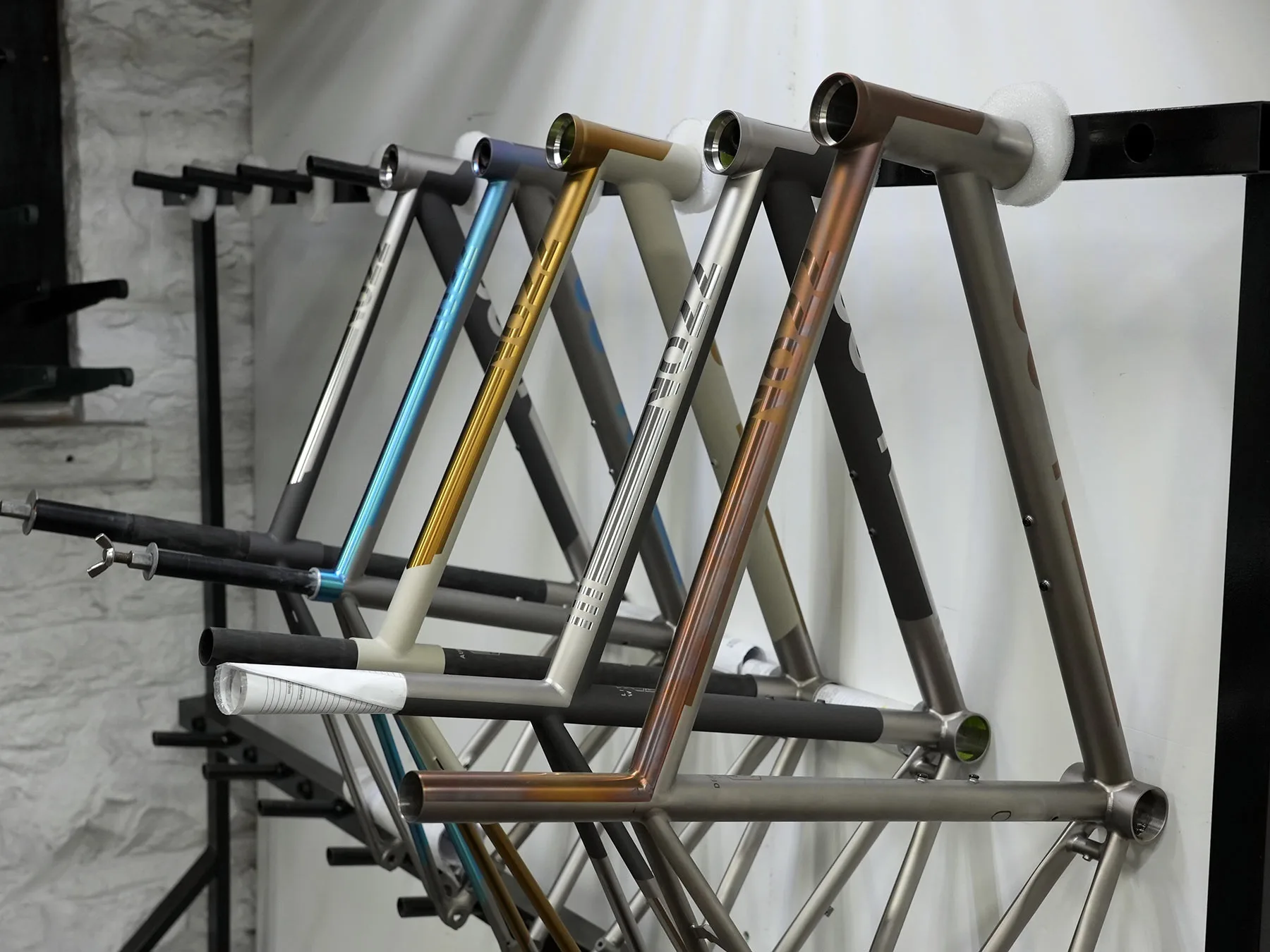
Whereas we’re on manufacturing quantity, they famous that they used to provide extra bikes per week, however have slowed down just a little since shifting all ending in-house. Earlier than, they’d outsource it, however the high quality and consistency of the work wasn’t all the time what they wished.
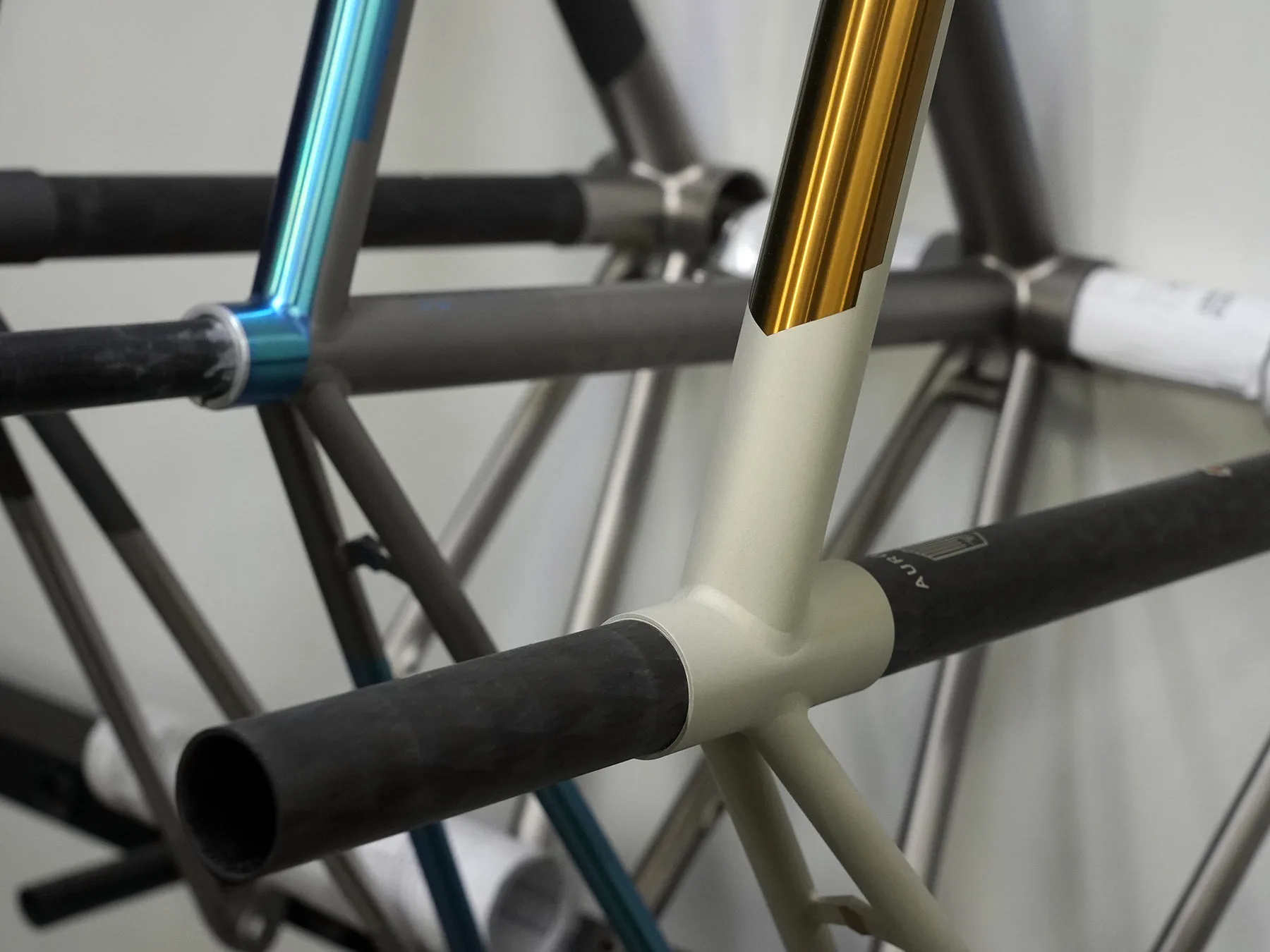
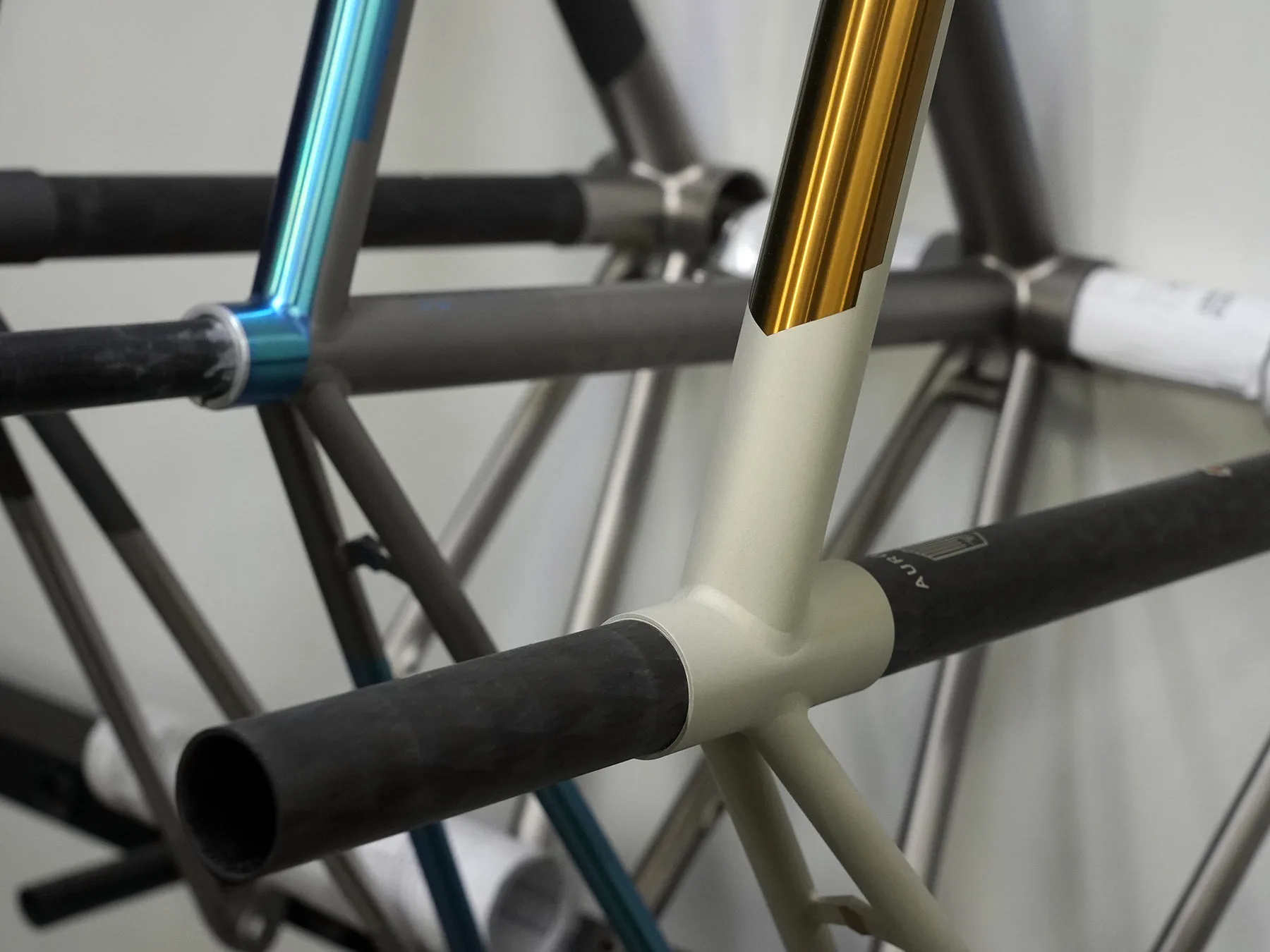
So that they introduced it in-house, and now do all anodizing and Cerakote portray on website. That offers them full management, however takes longer. However that management is necessary as a result of Cerakote is laid instantly on the titanium with no base coat or primer, so it’ll present any imperfections within the tube, in order that they have to shine and end all tubes and welds to absolute perfection first.
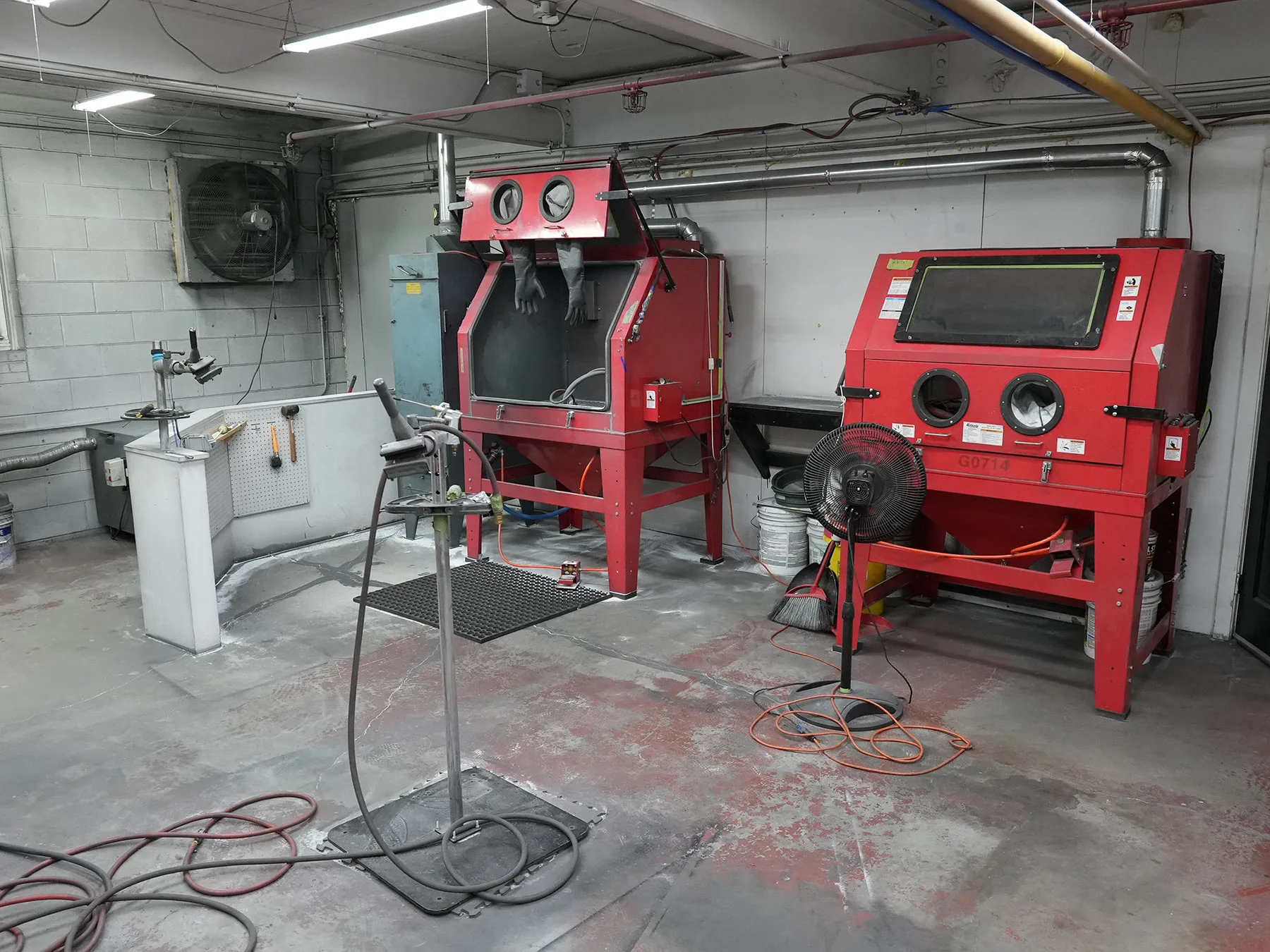
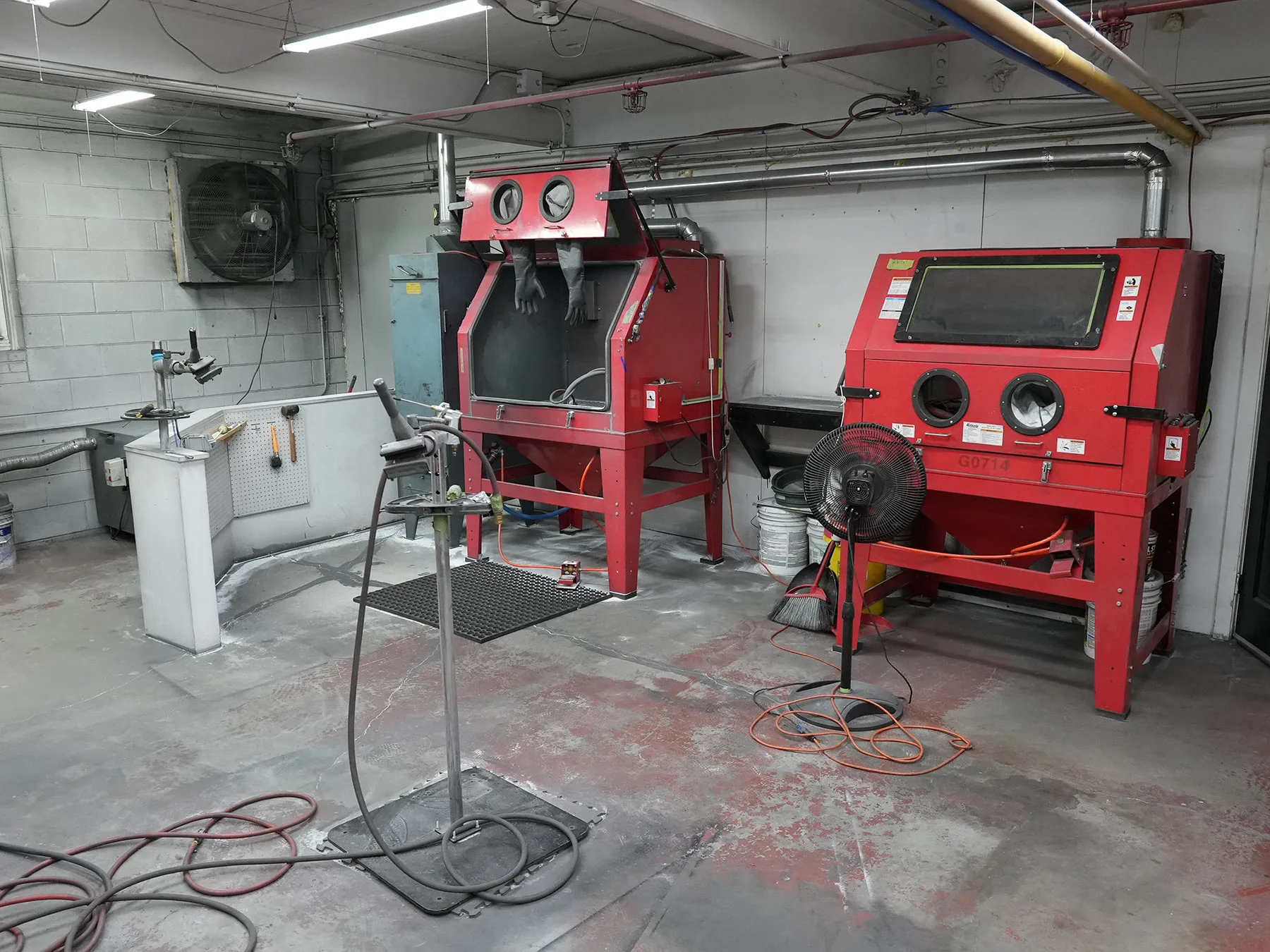
Media blasting cubicles allow them to give some frames (or components of frames) a matte end, whereas others (or different components) are polished for a excessive gloss end.
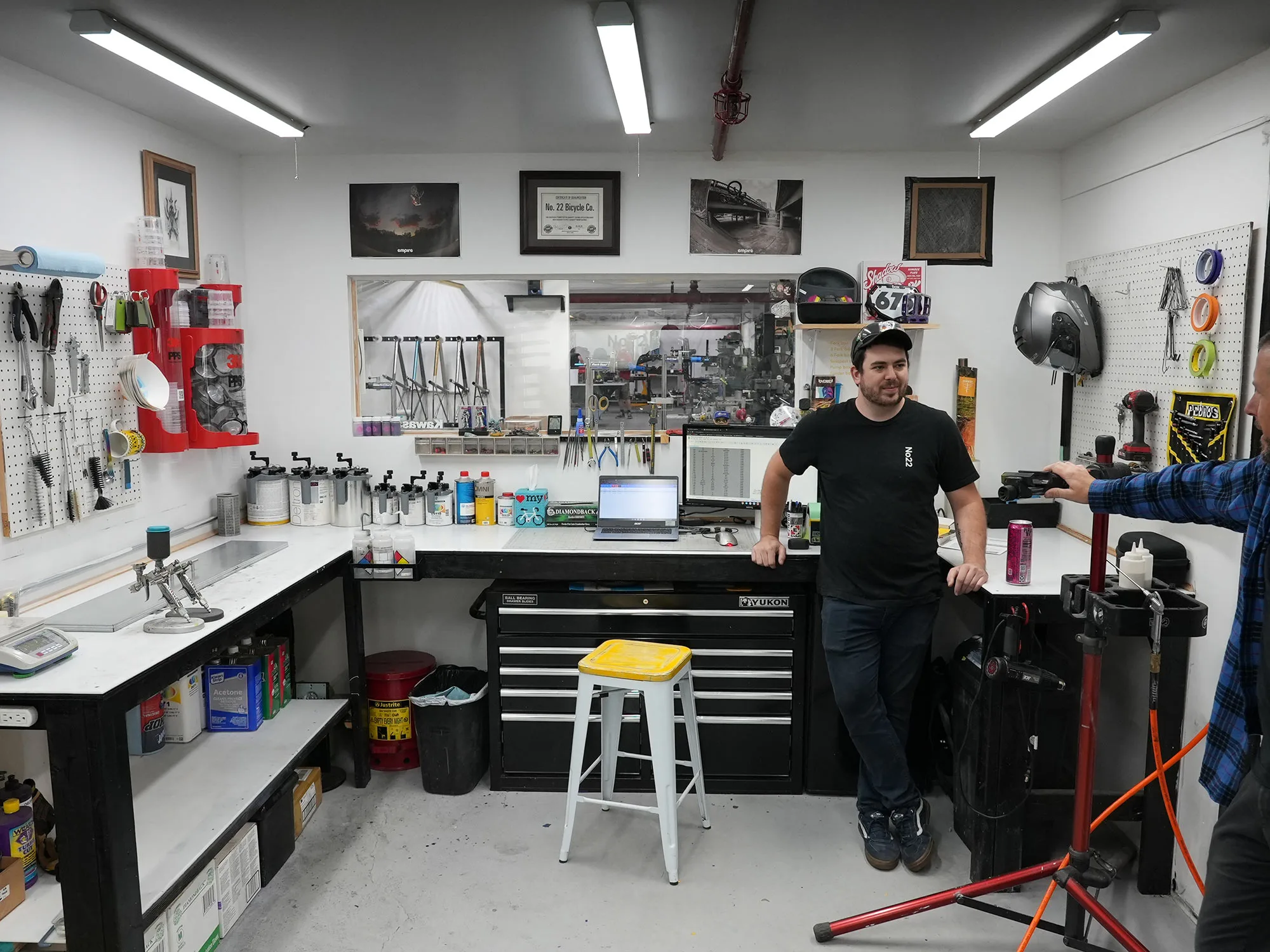
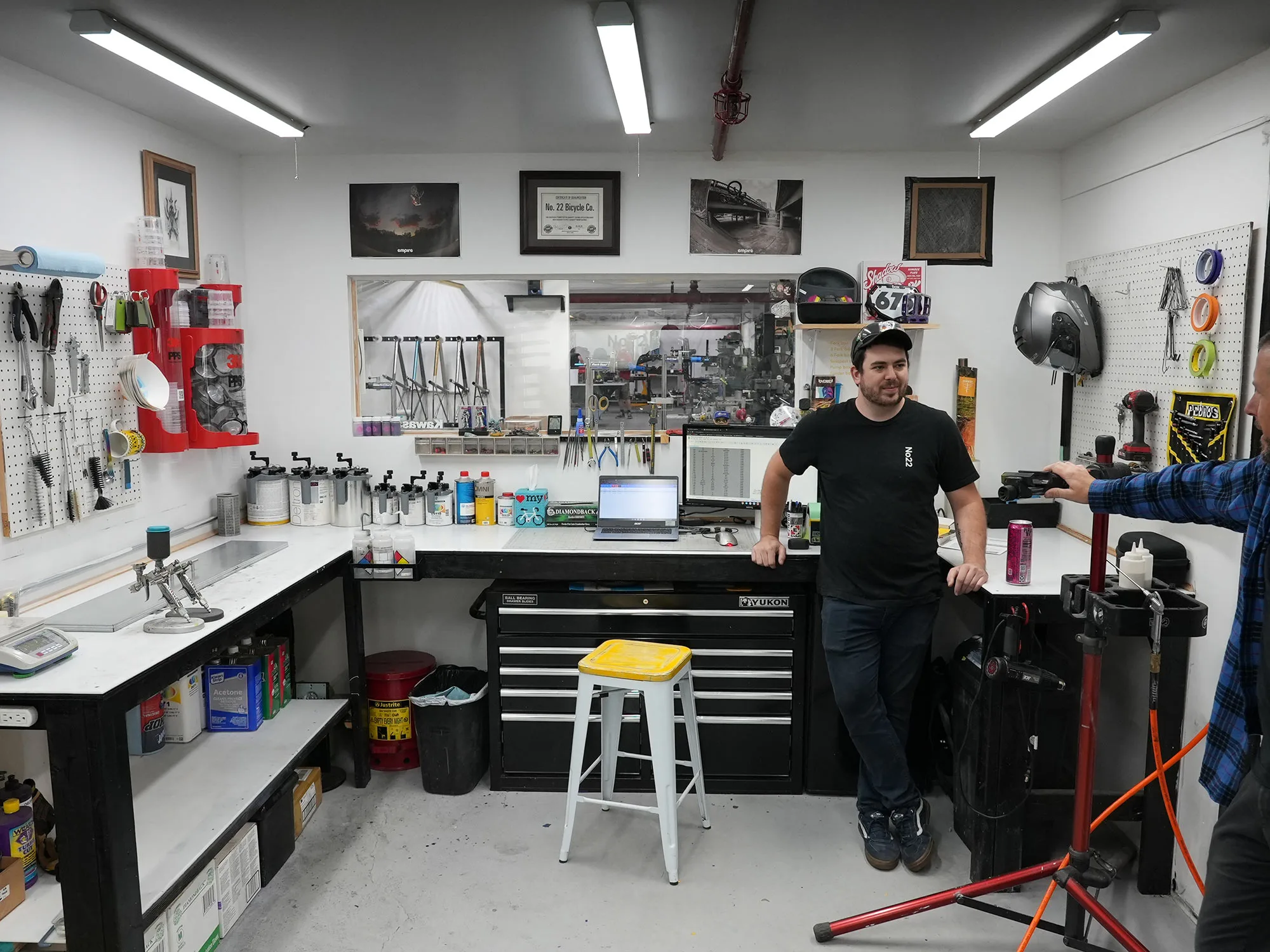
Cerakote is available in all kinds of colours, and so they’re all combined and prepped on website.
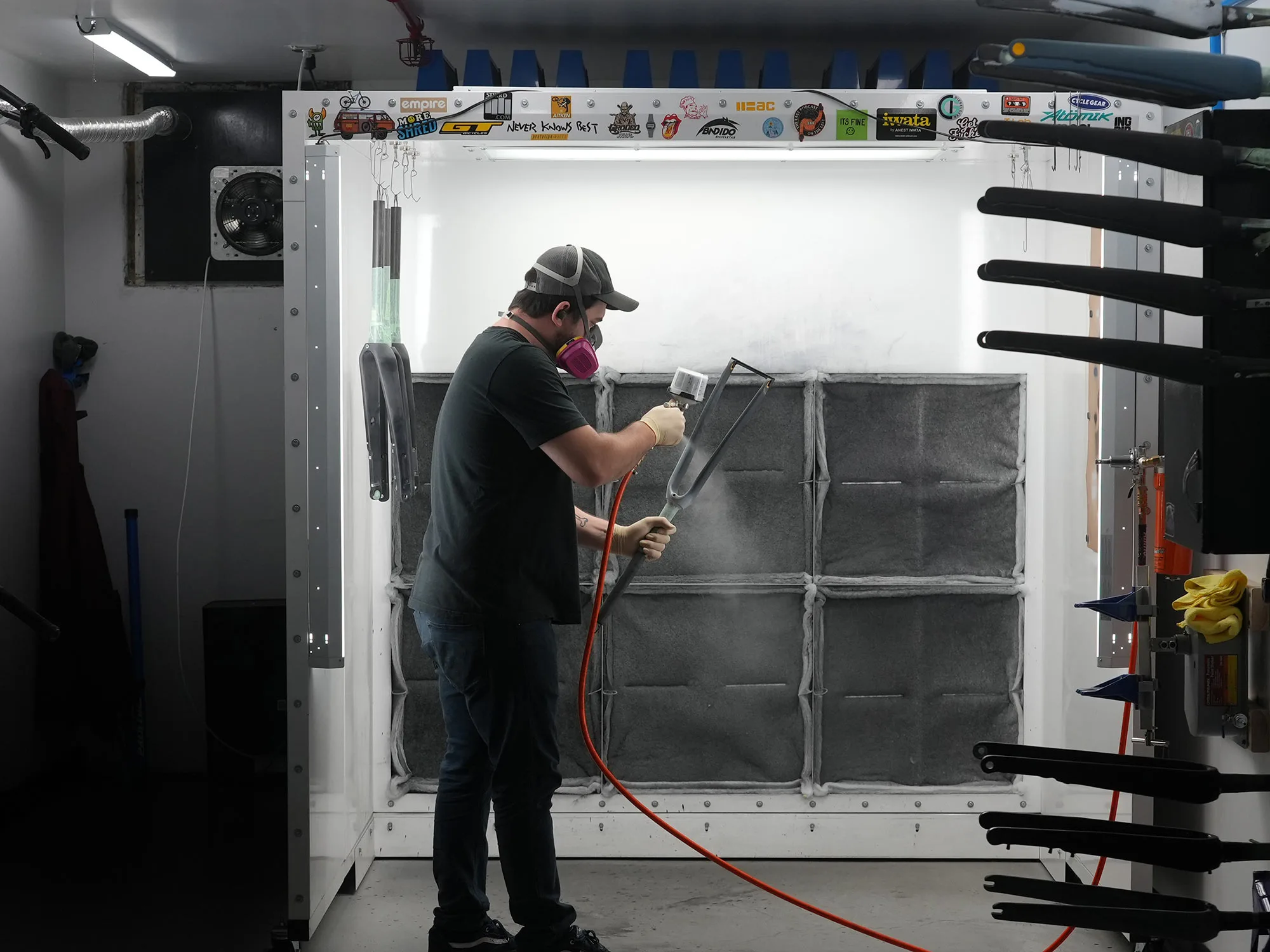
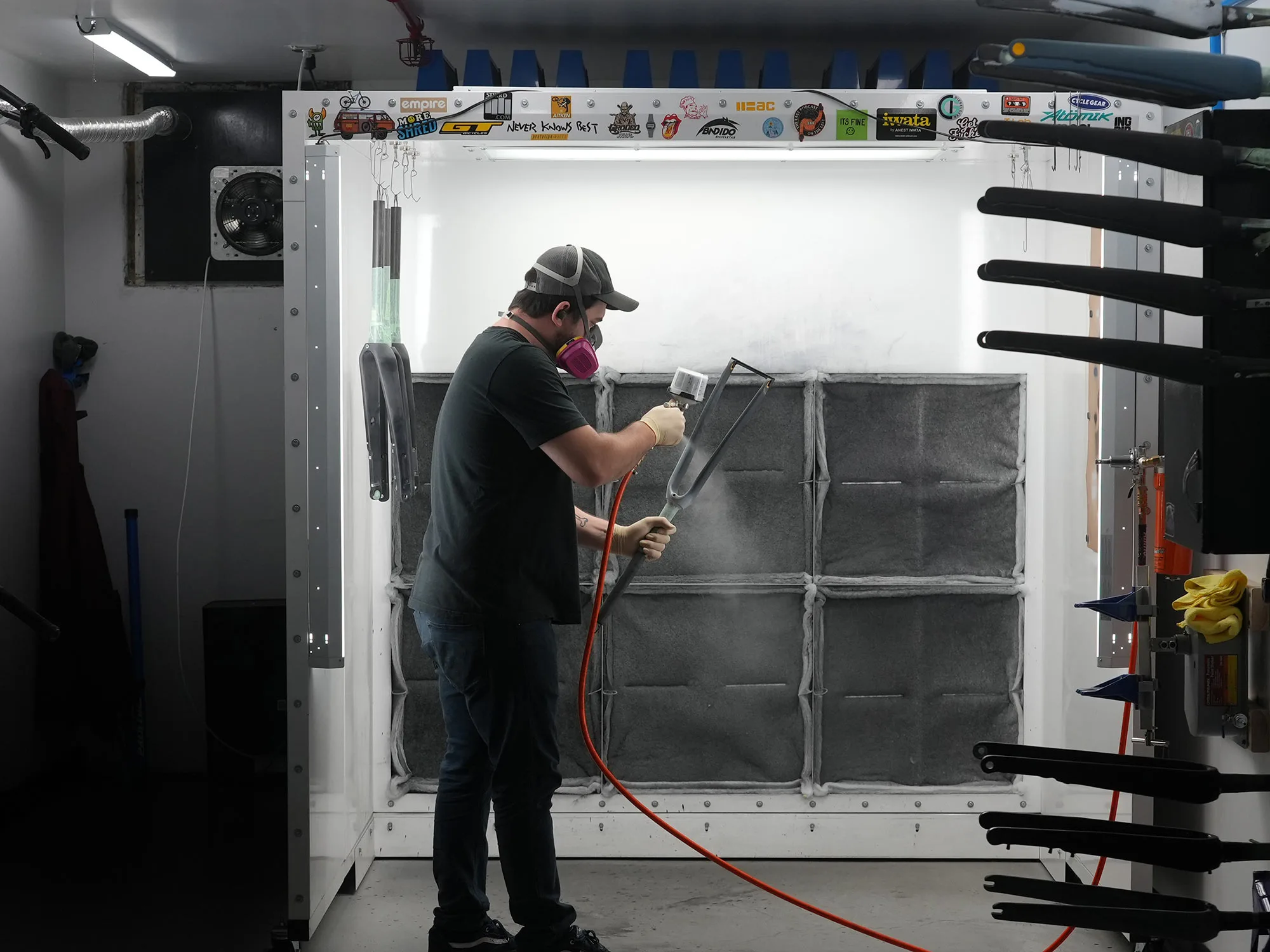
They stopped doing moist paint, as a result of Cerakote is healthier, lighter, extra sturdy, and cleaner to make use of. It’s additionally instantly shippable (whereas moist paint must off-gas for a number of days earlier than it may be bubble wrapped…and oh boy, does No22 like their bubble wrap!).
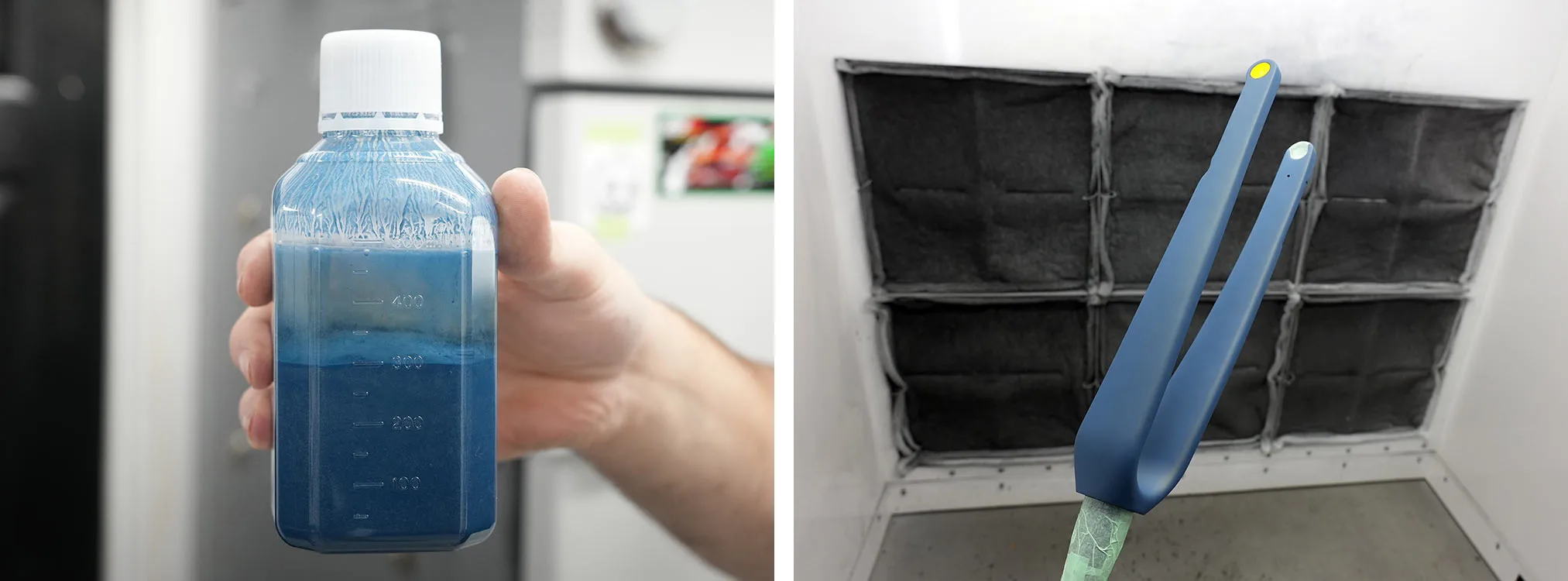
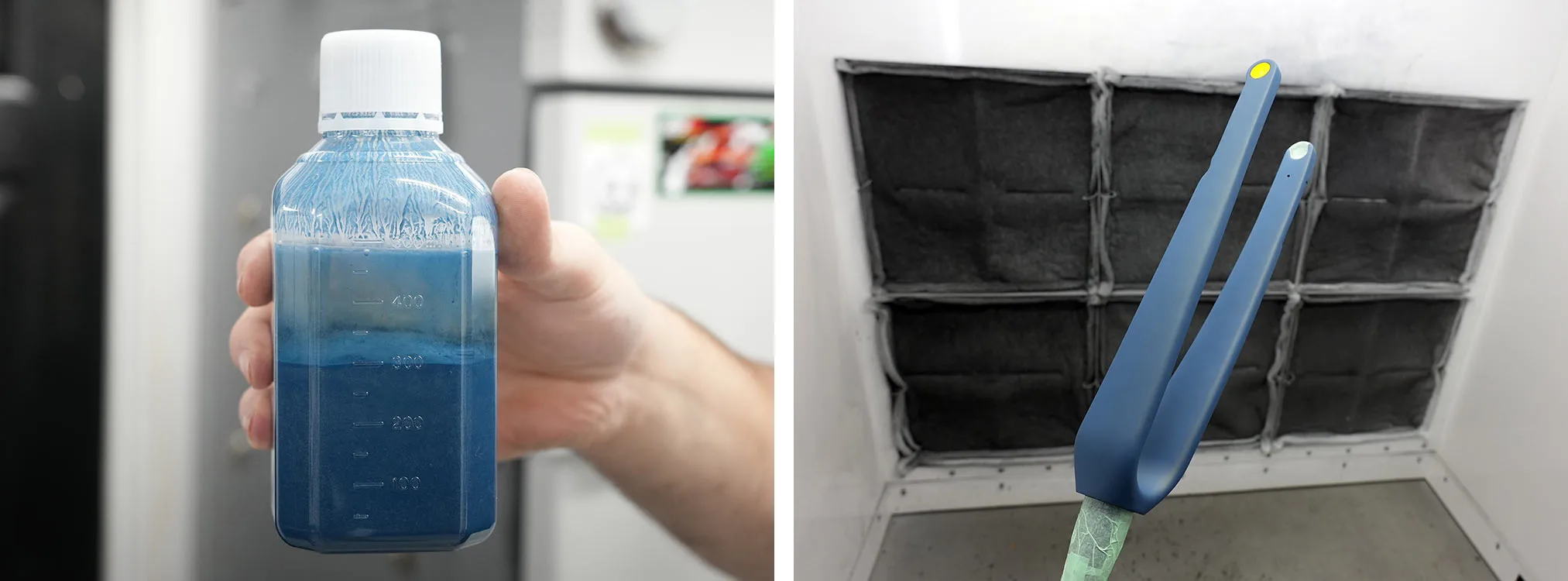
Their paint sales space is immaculate, and technically Cerakote says you don’t even have to put on a masks whereas spraying. They do anyway.
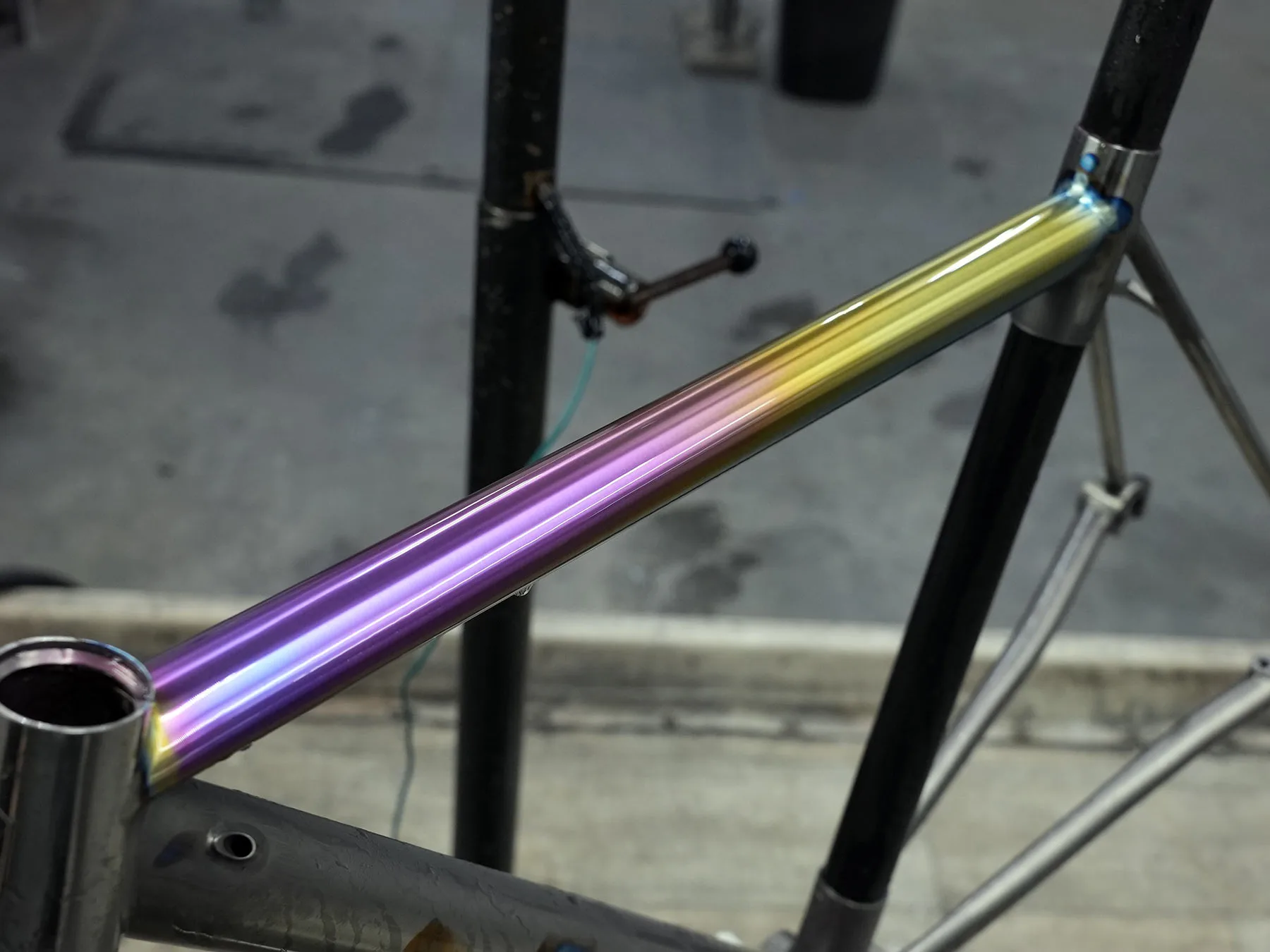
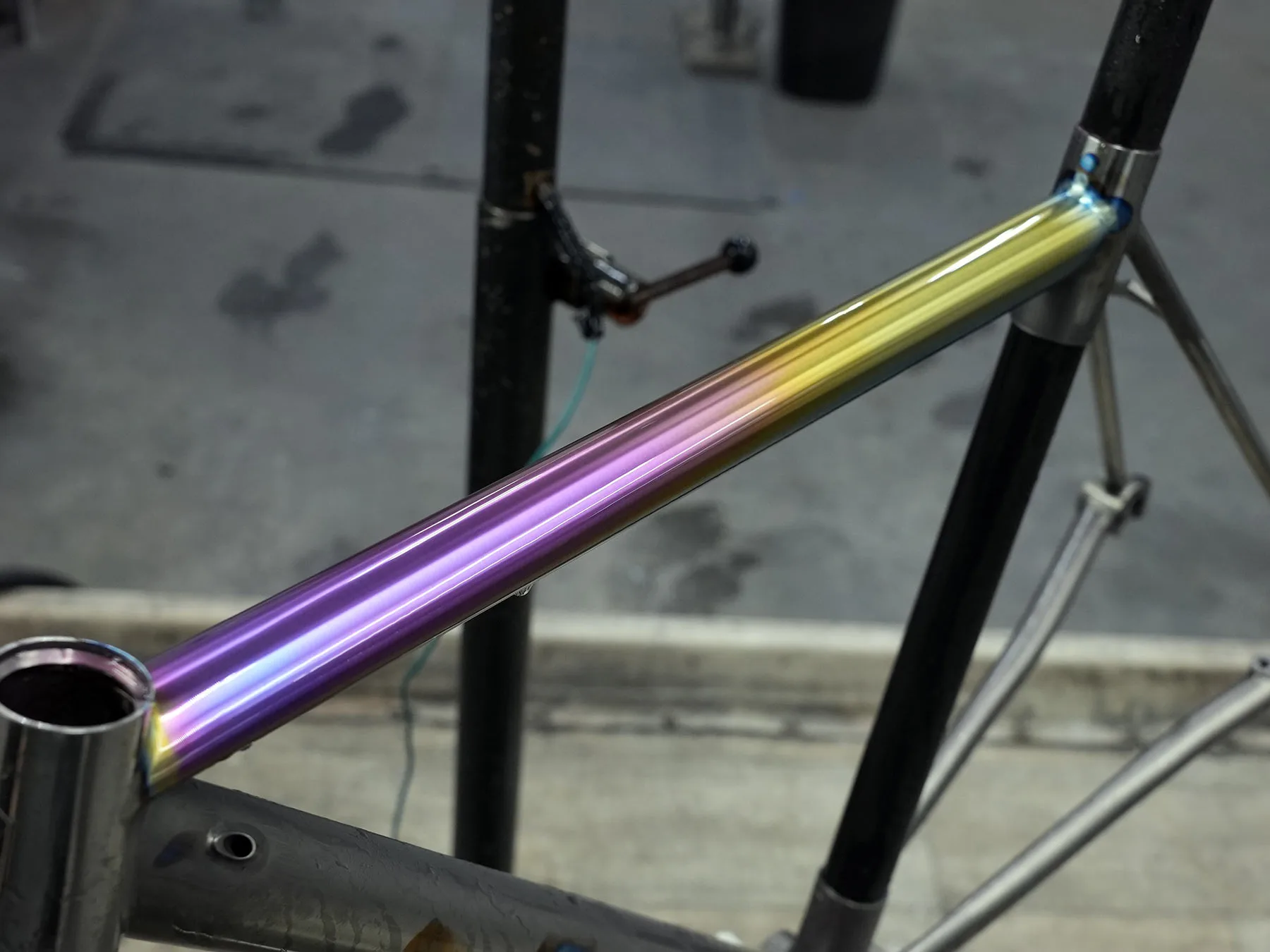
Ano is difficult. The completely different colours are solely coming from completely different voltage. Colours vary from brass to inexperienced, created with voltage starting from about 8 to 100 volts. Getting the fades means various the voltage as they go, but in addition making use of it in layers to get the upper voltage colours.
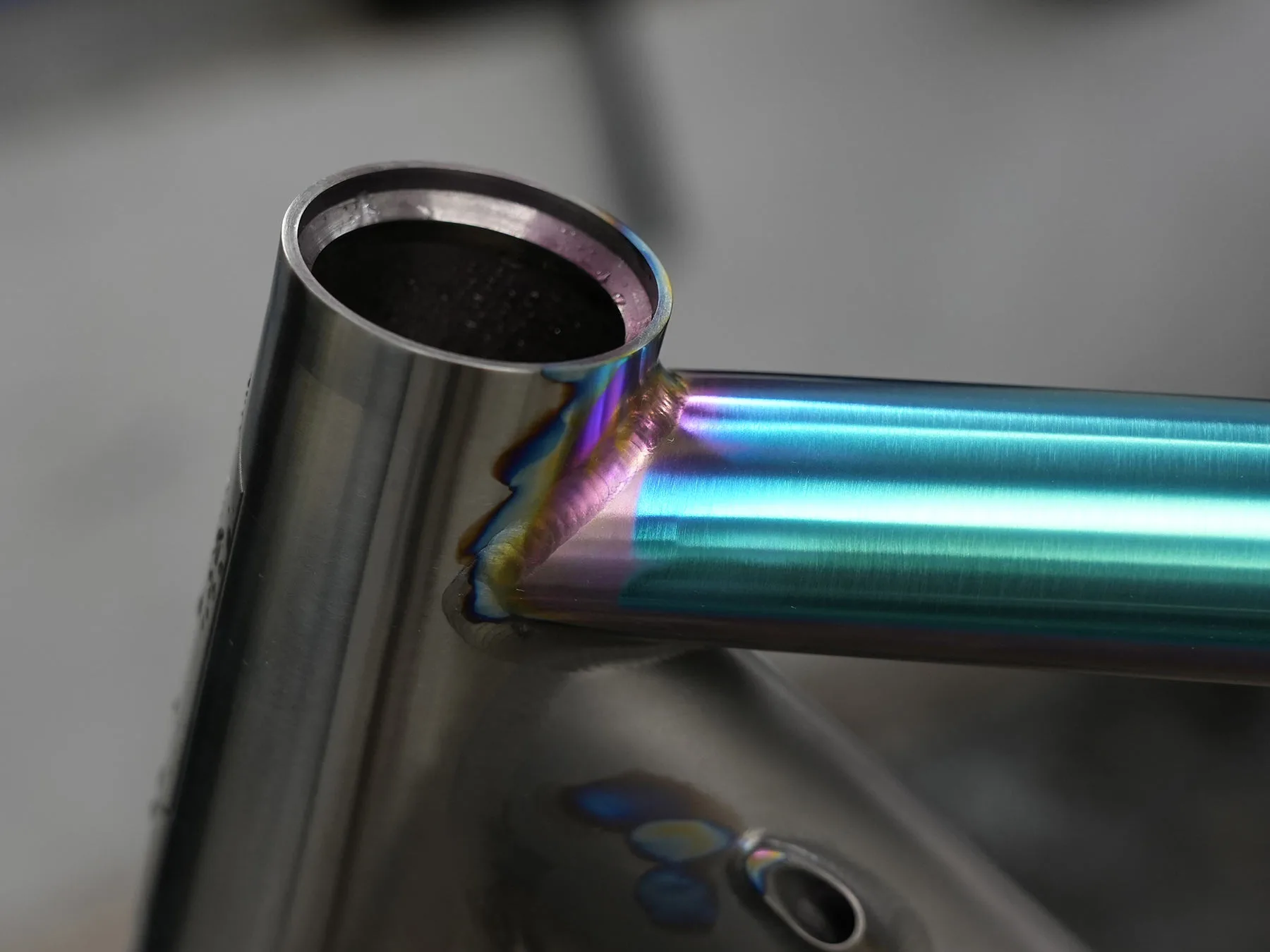
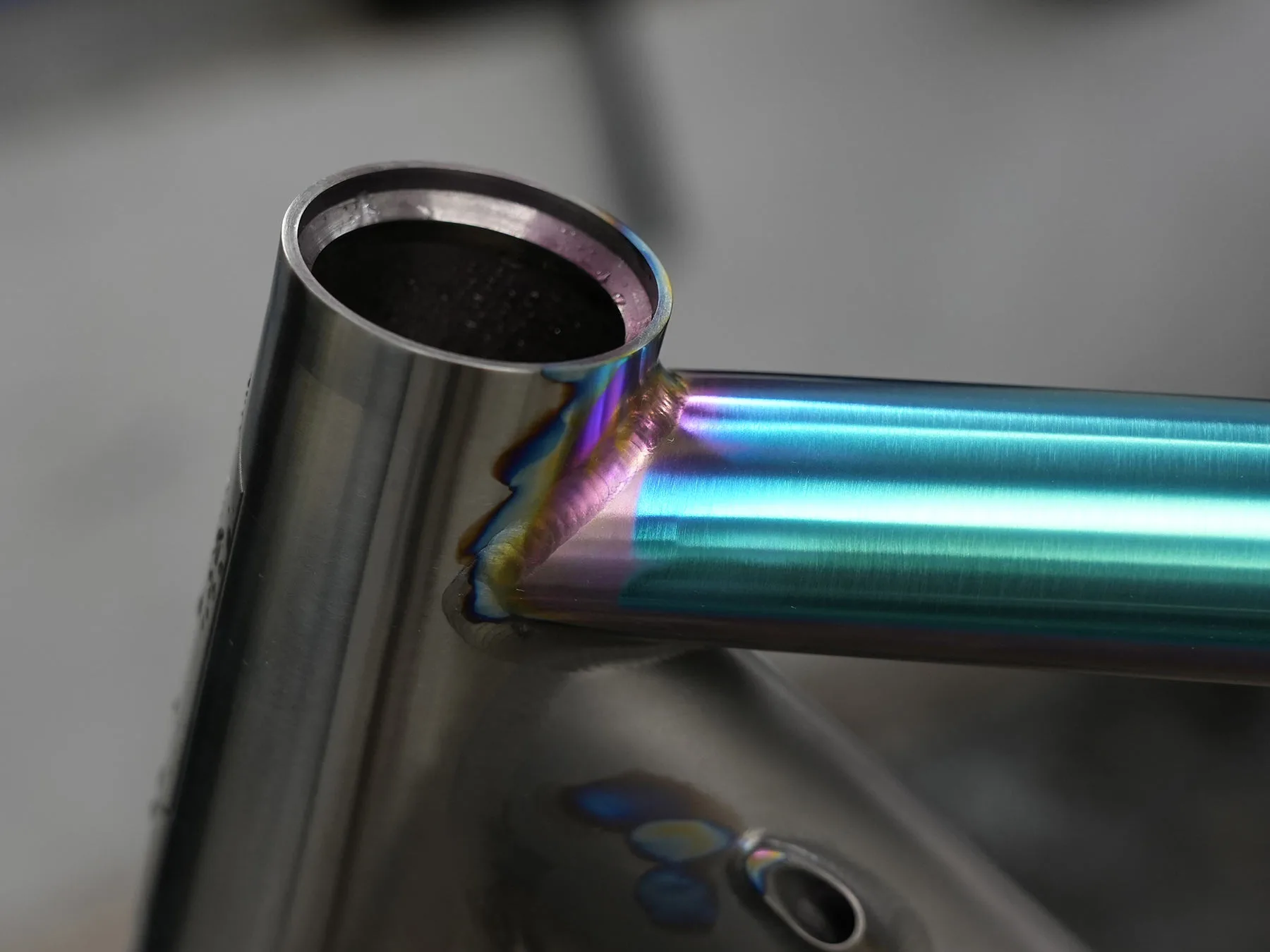
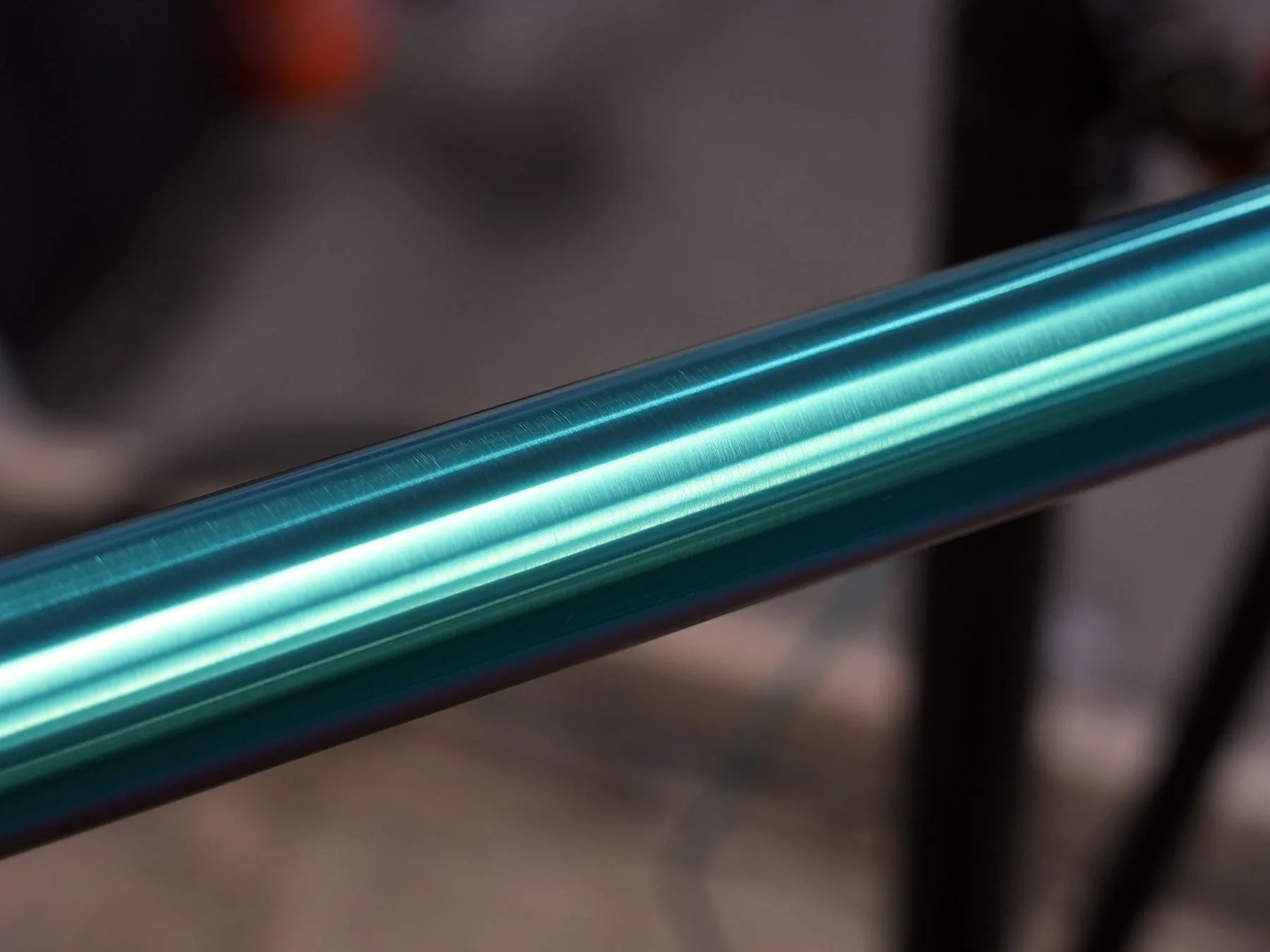
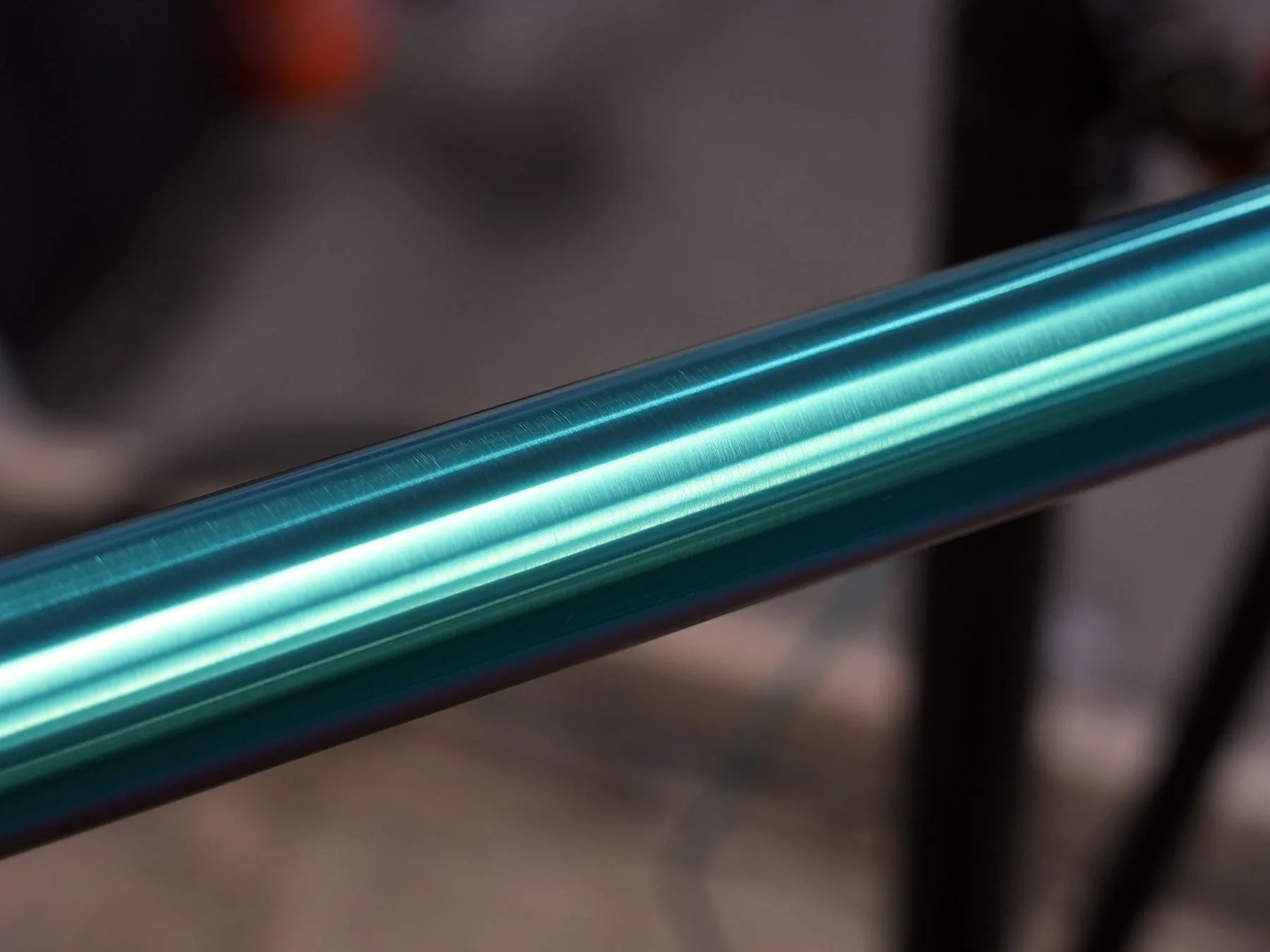
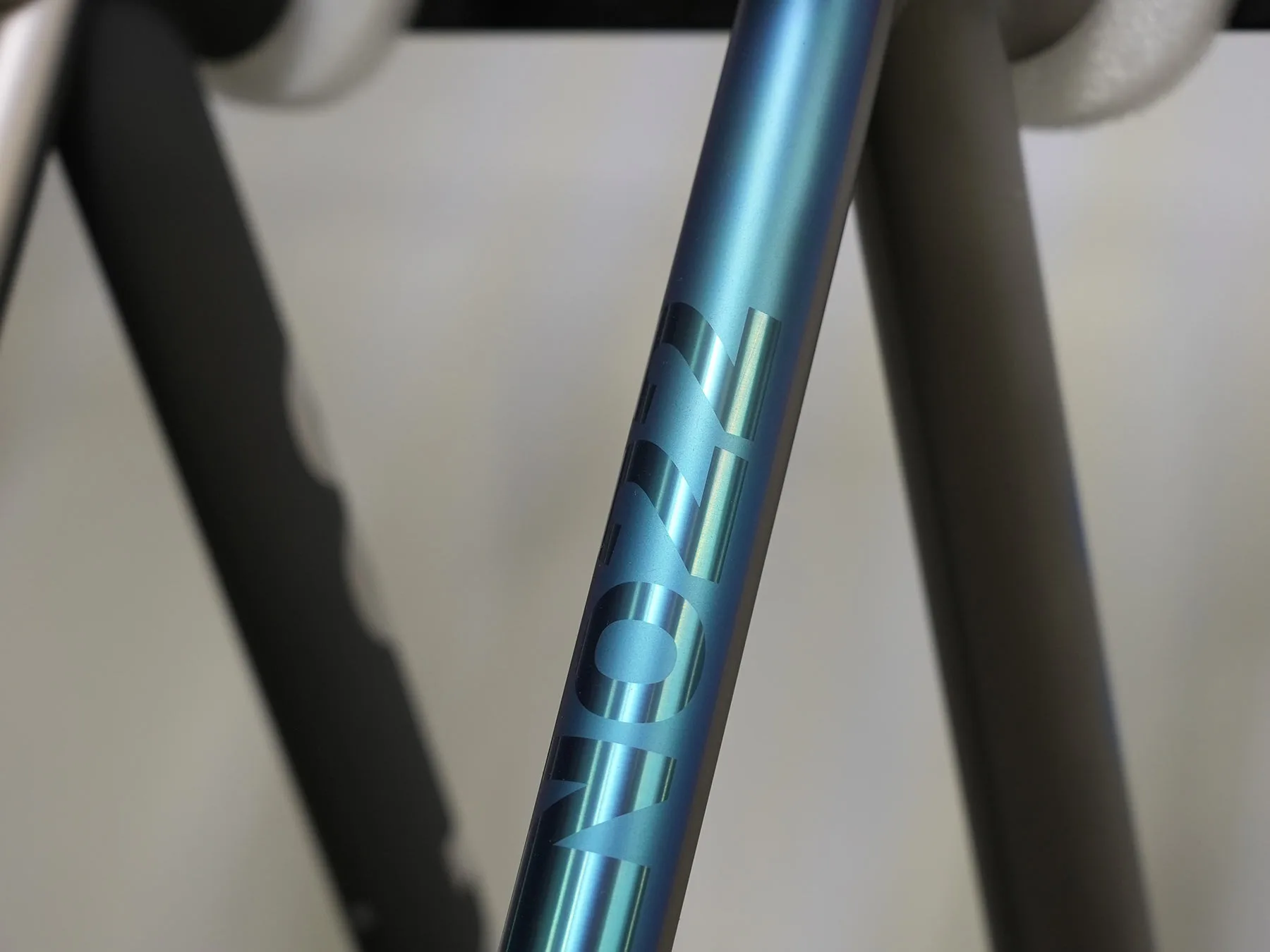
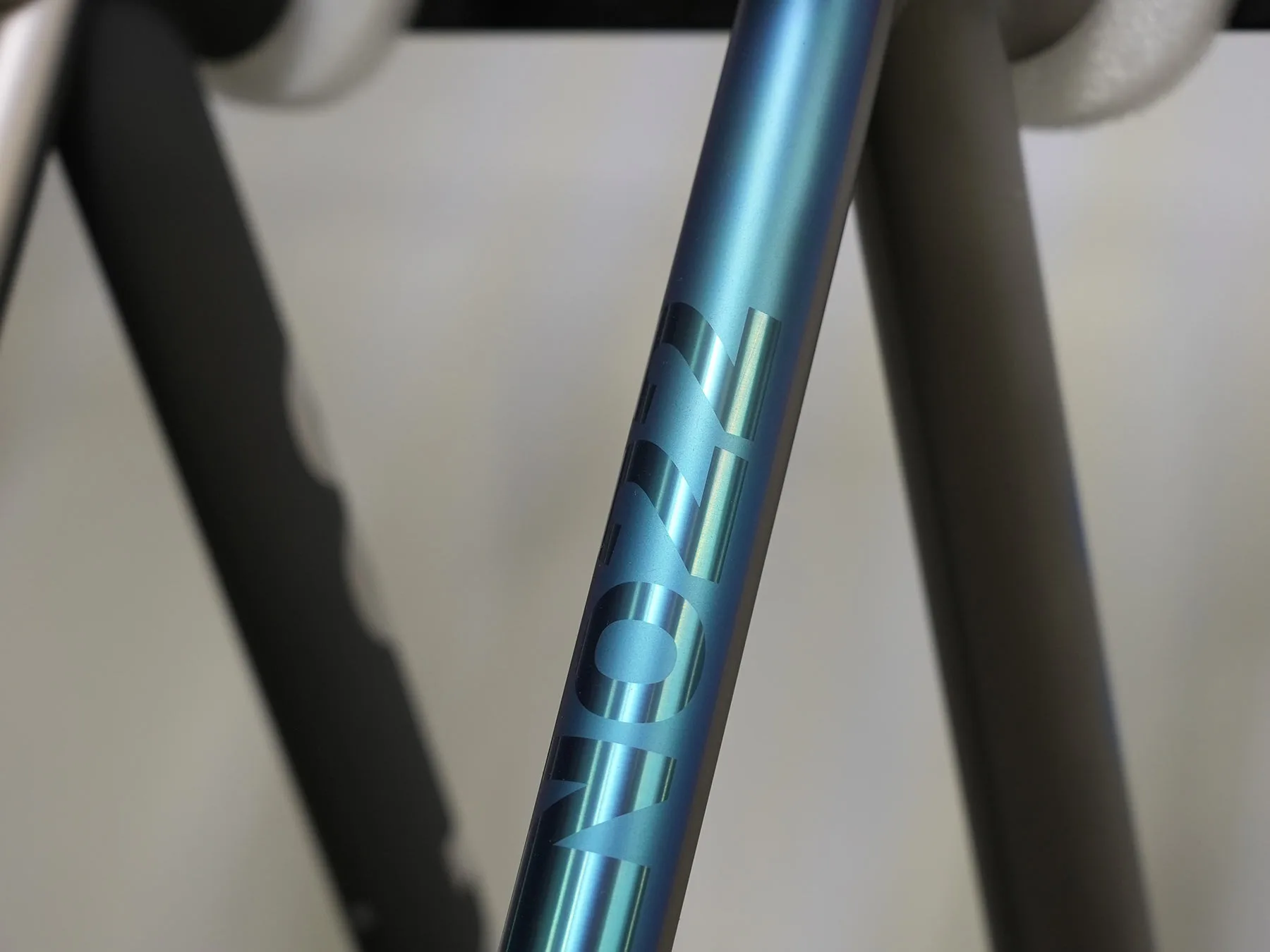
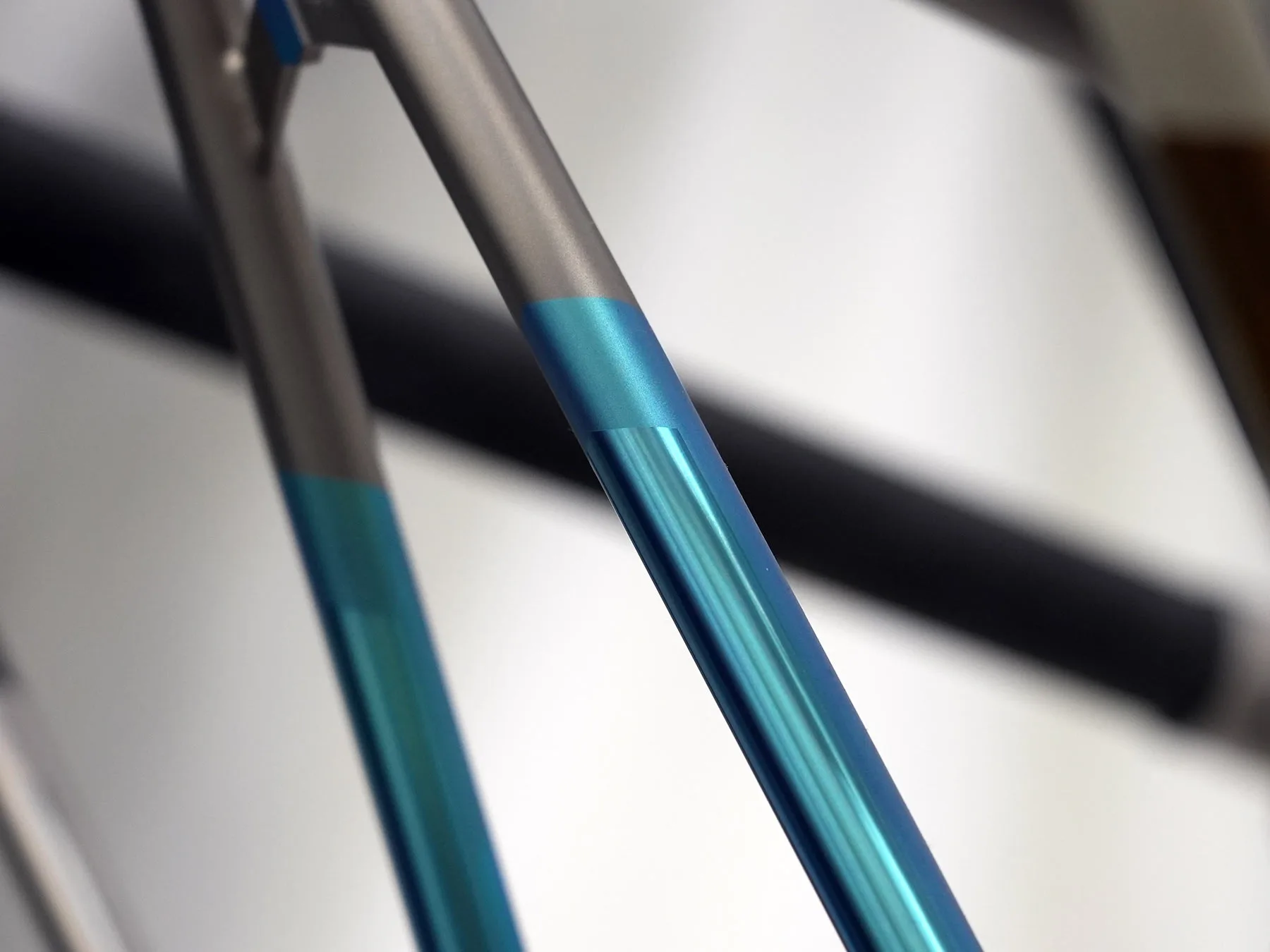
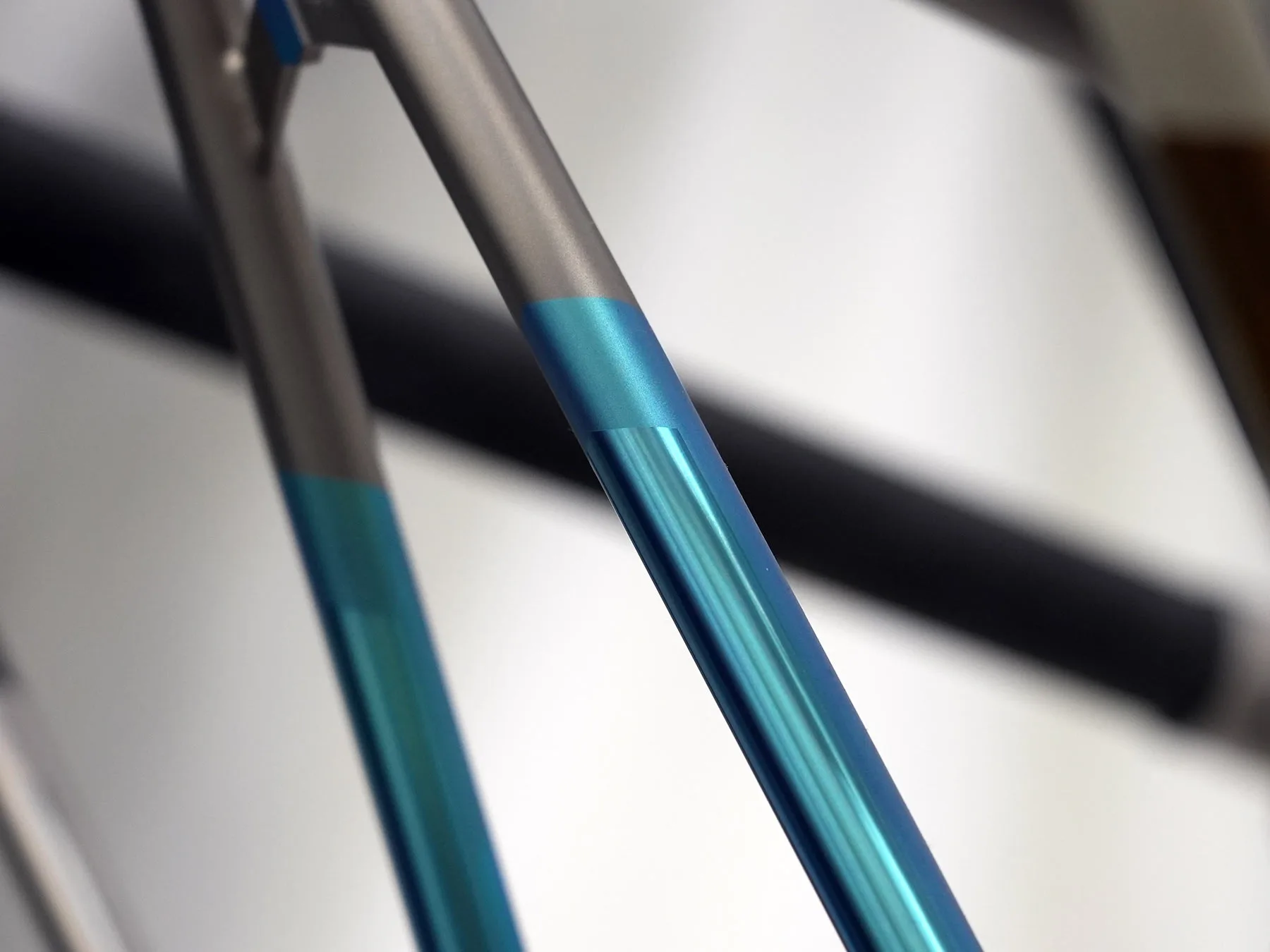
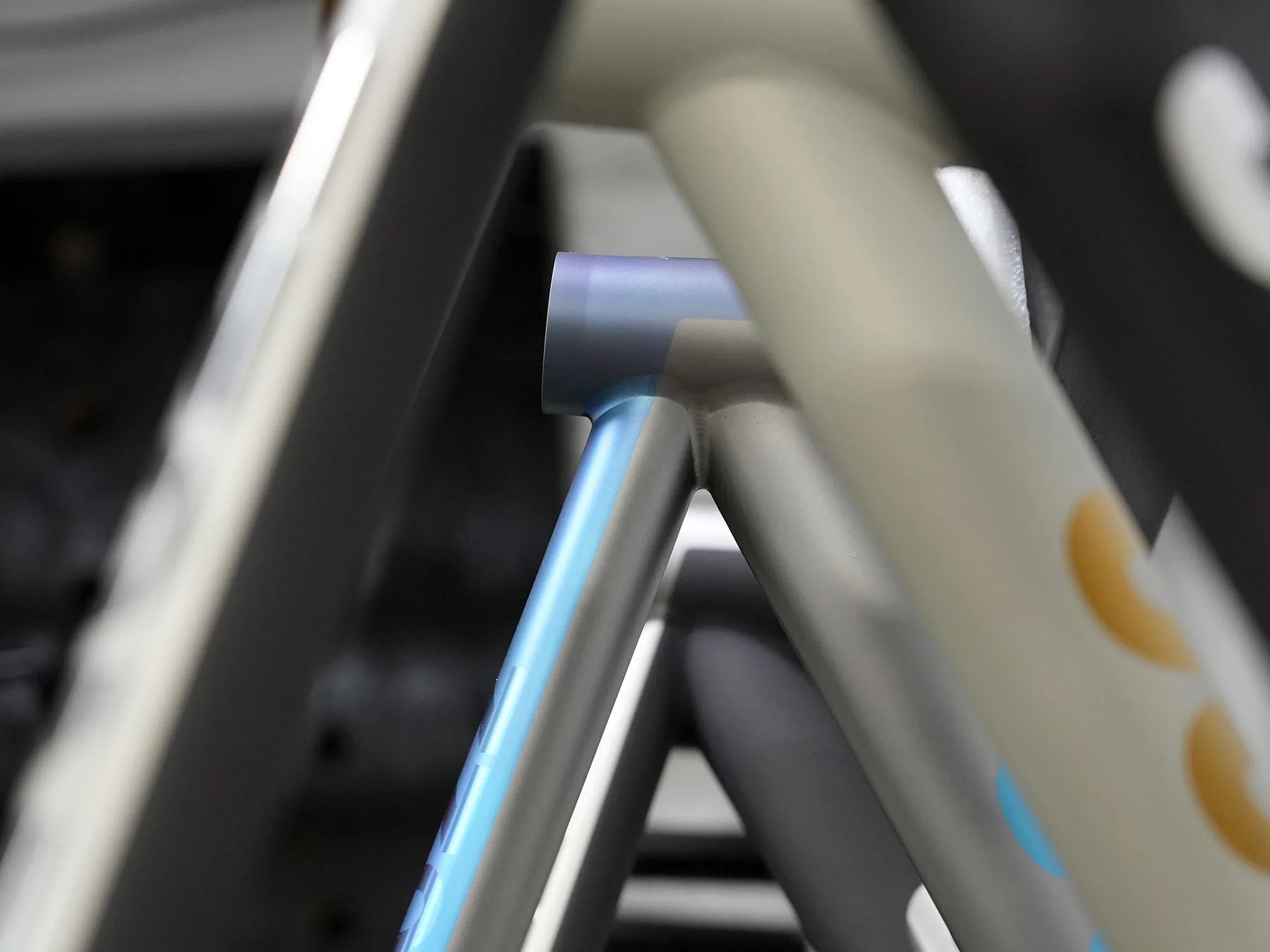
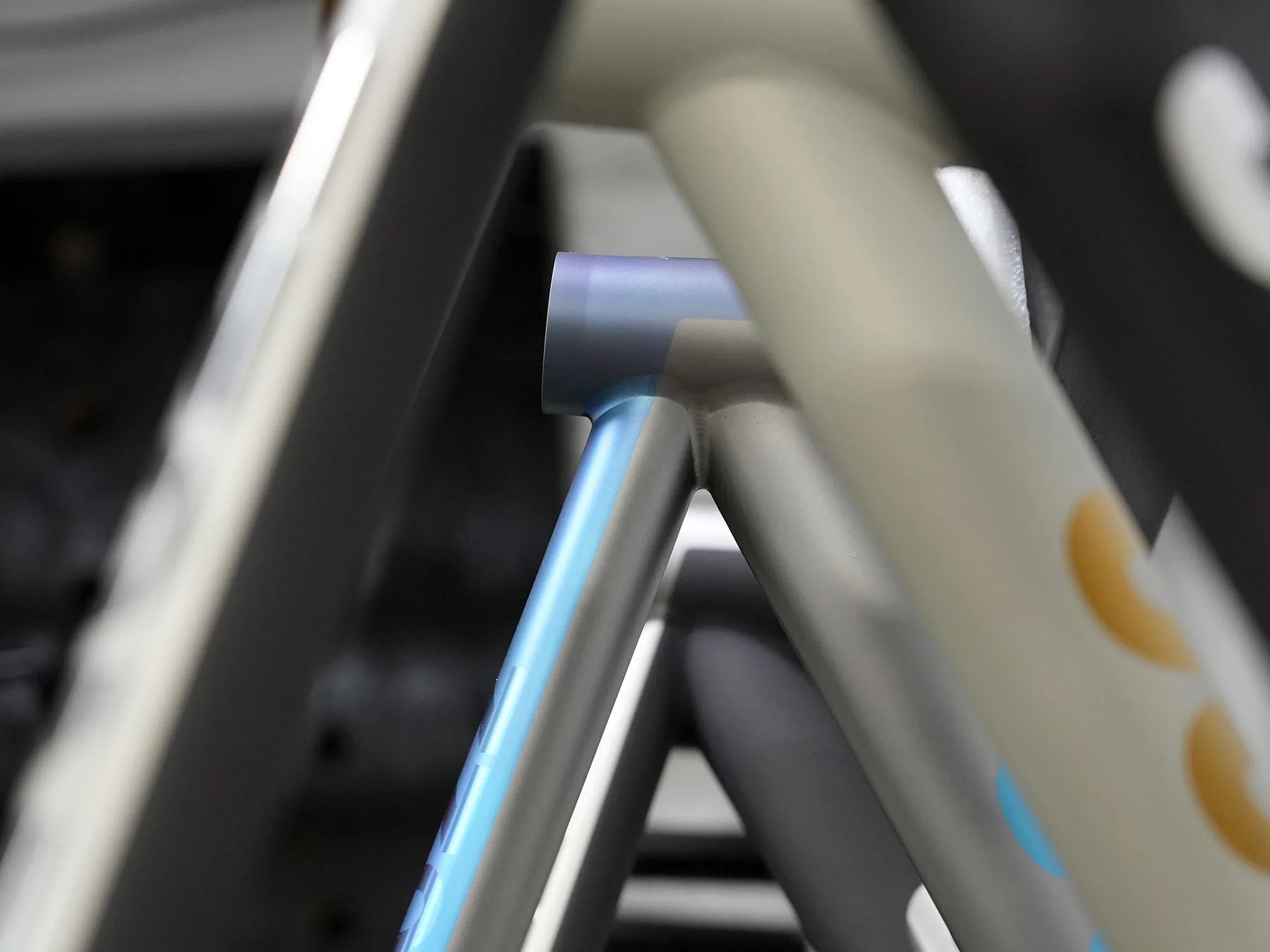
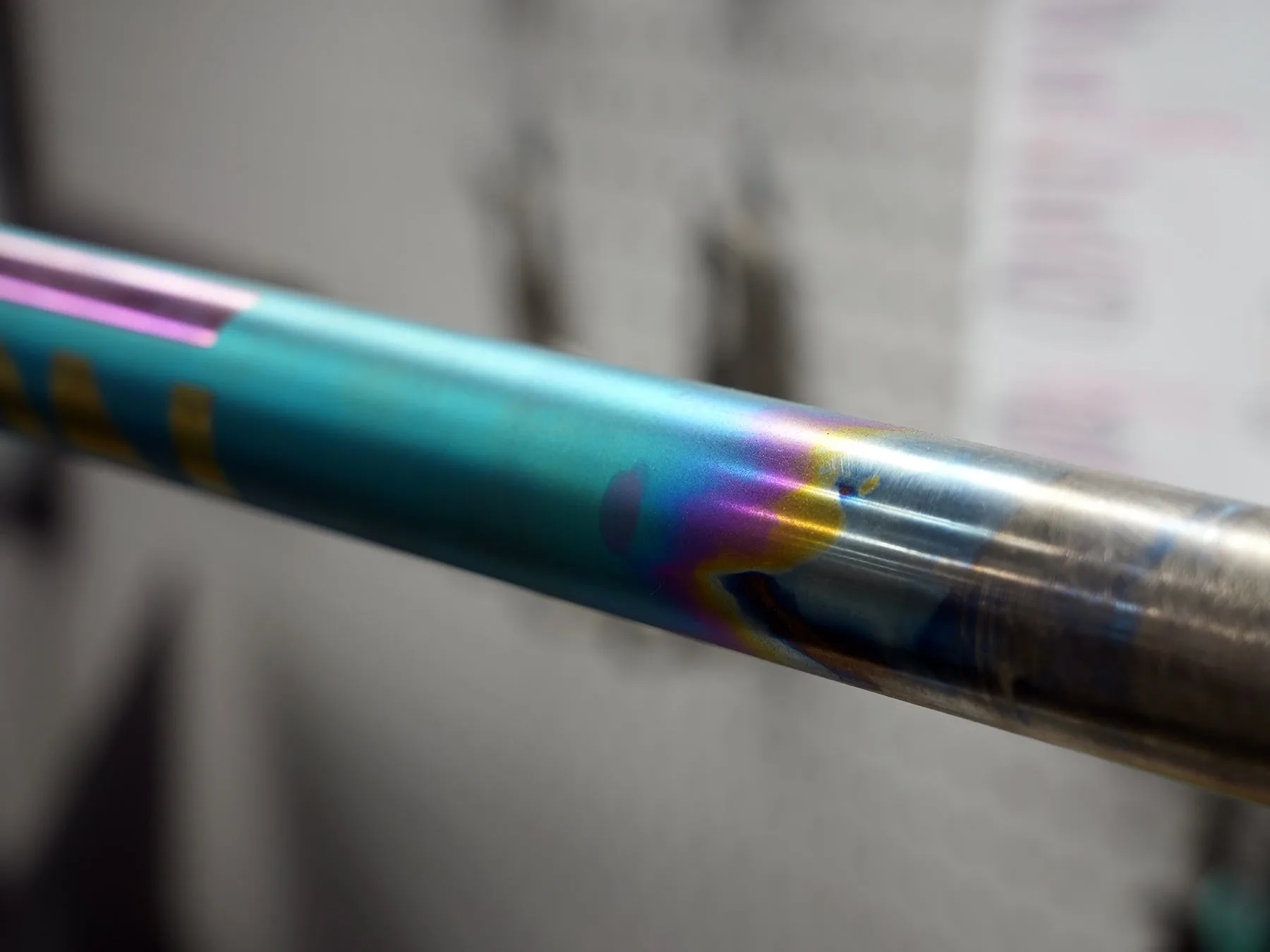
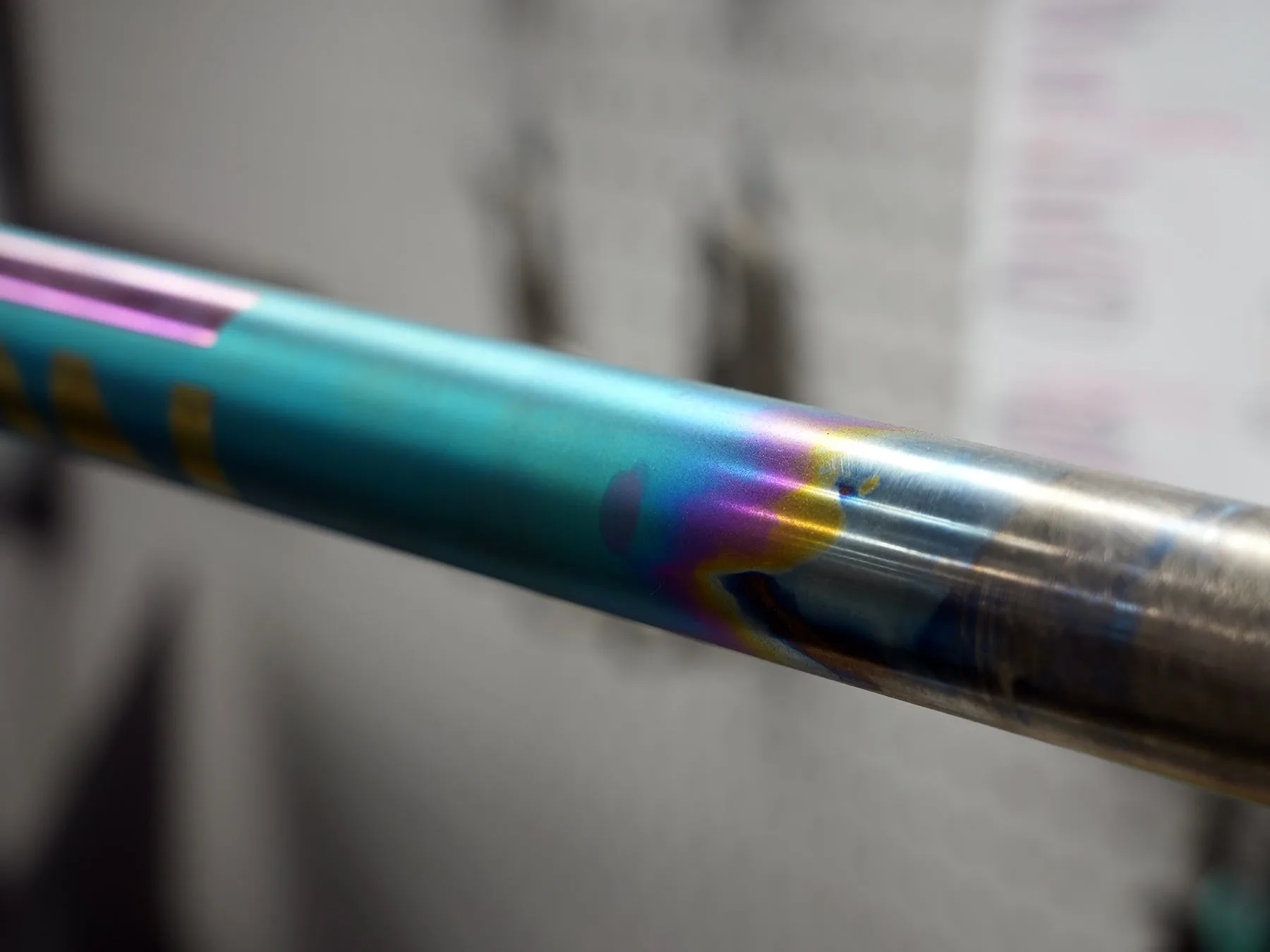
Including to the complexity is that the colour could be a little completely different between 6/4 and three/2.5 titanium, and any fluctuations within the energy provide may have an effect on the end result. So, what you see on their frames may be 6-8 hours of anodizing on prime of the prep work!
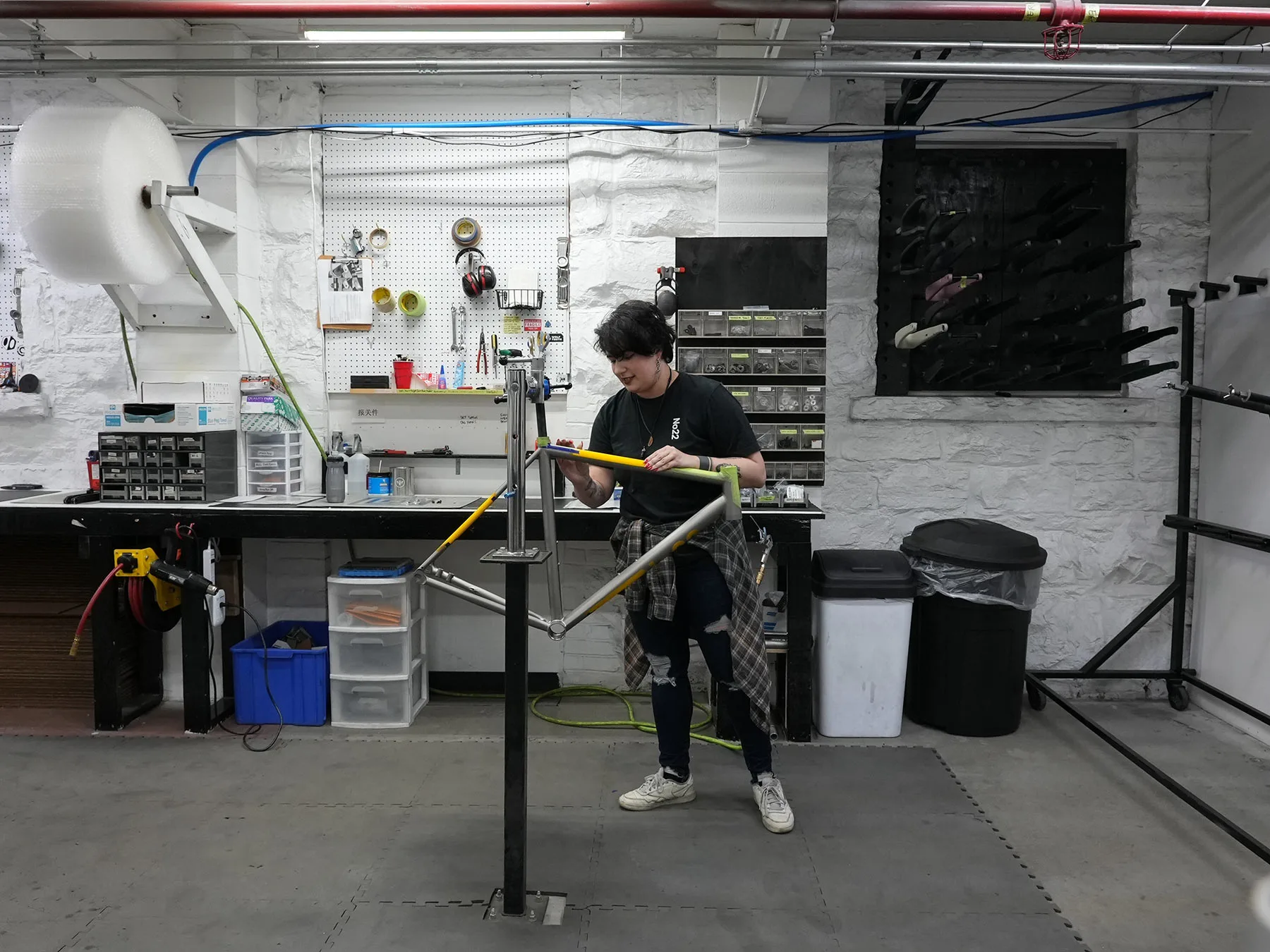
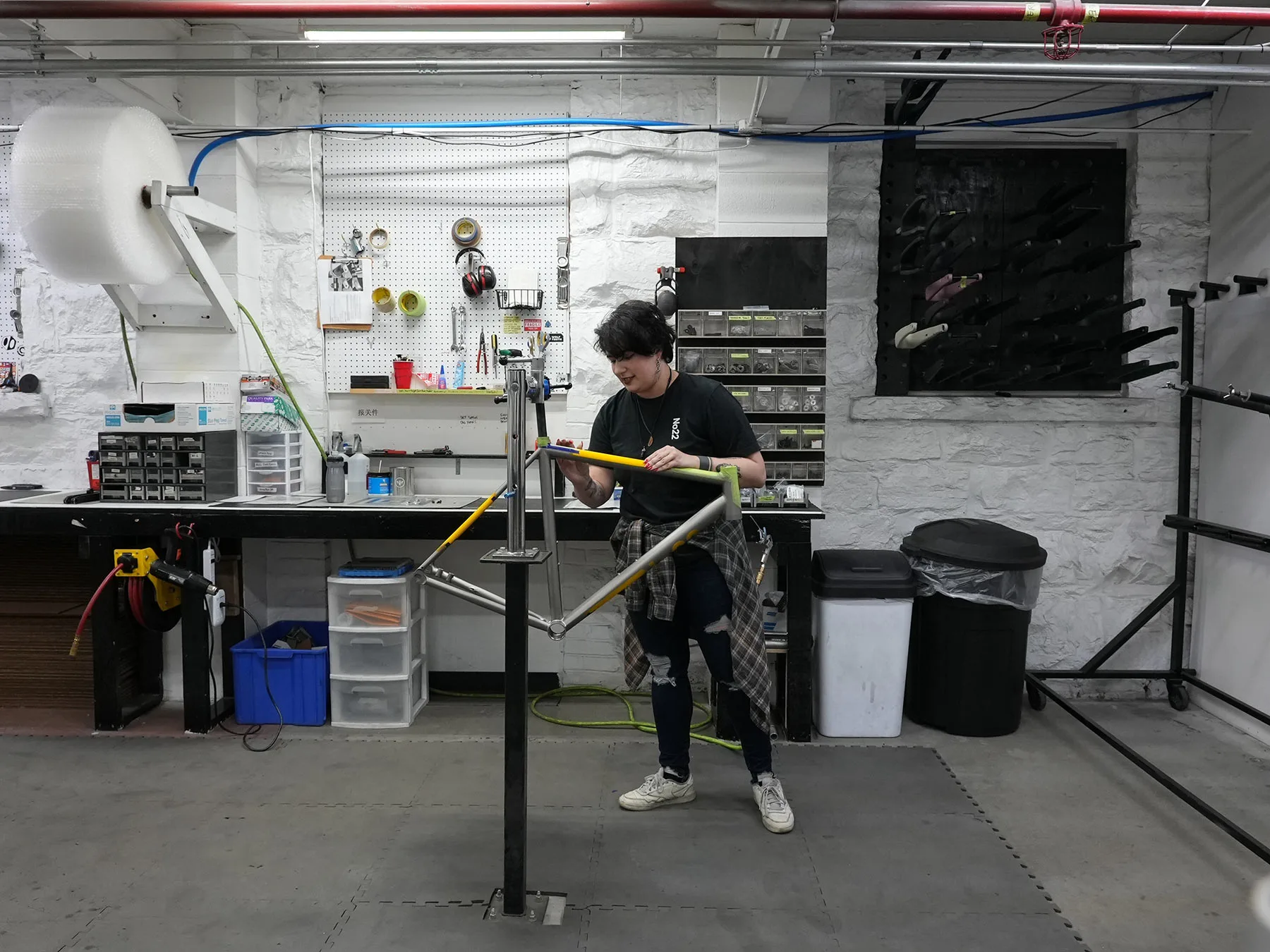
Masking, sharpening, and blasting lets them get combos of uncooked, gloss, and matte colours.
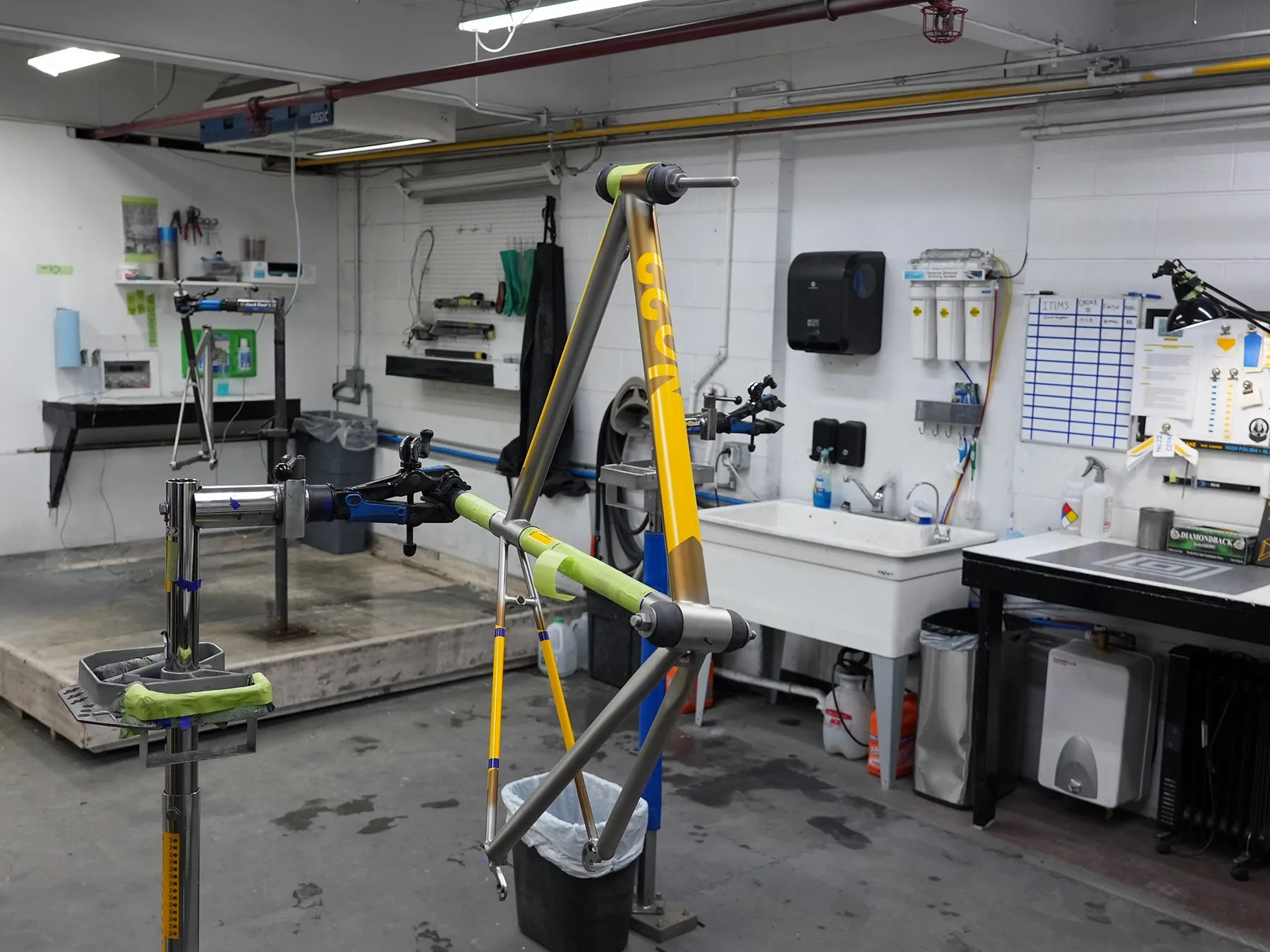
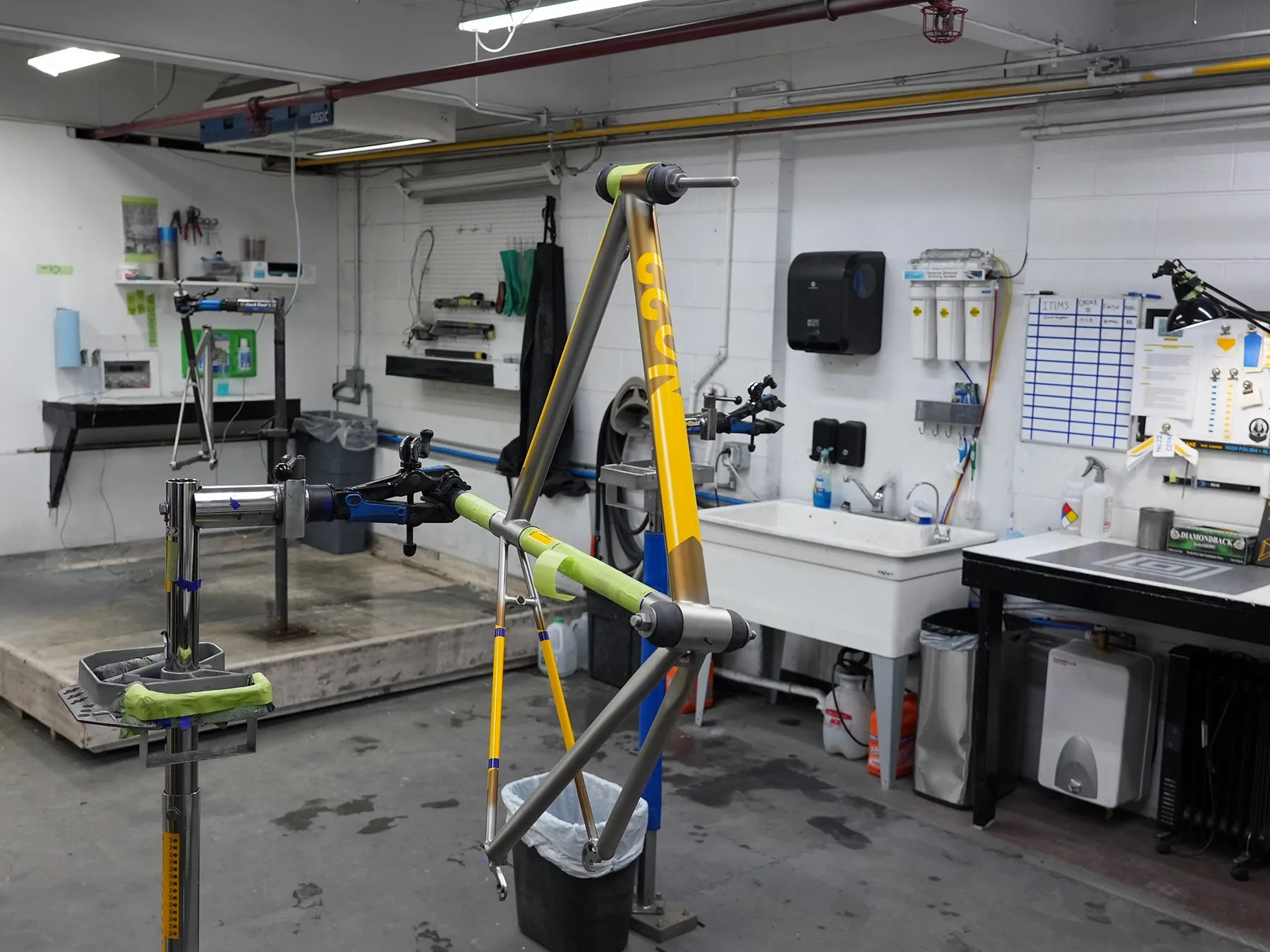
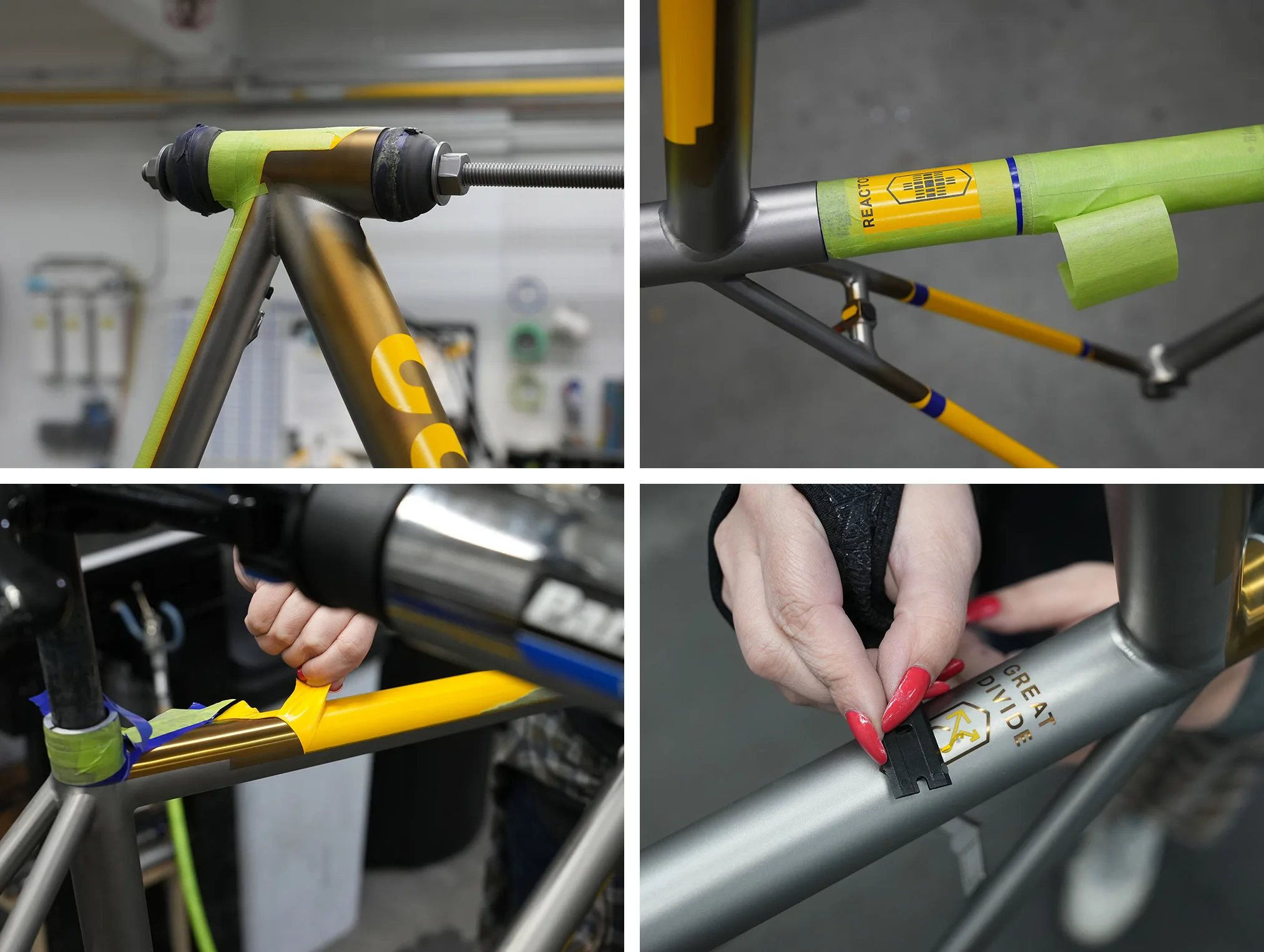
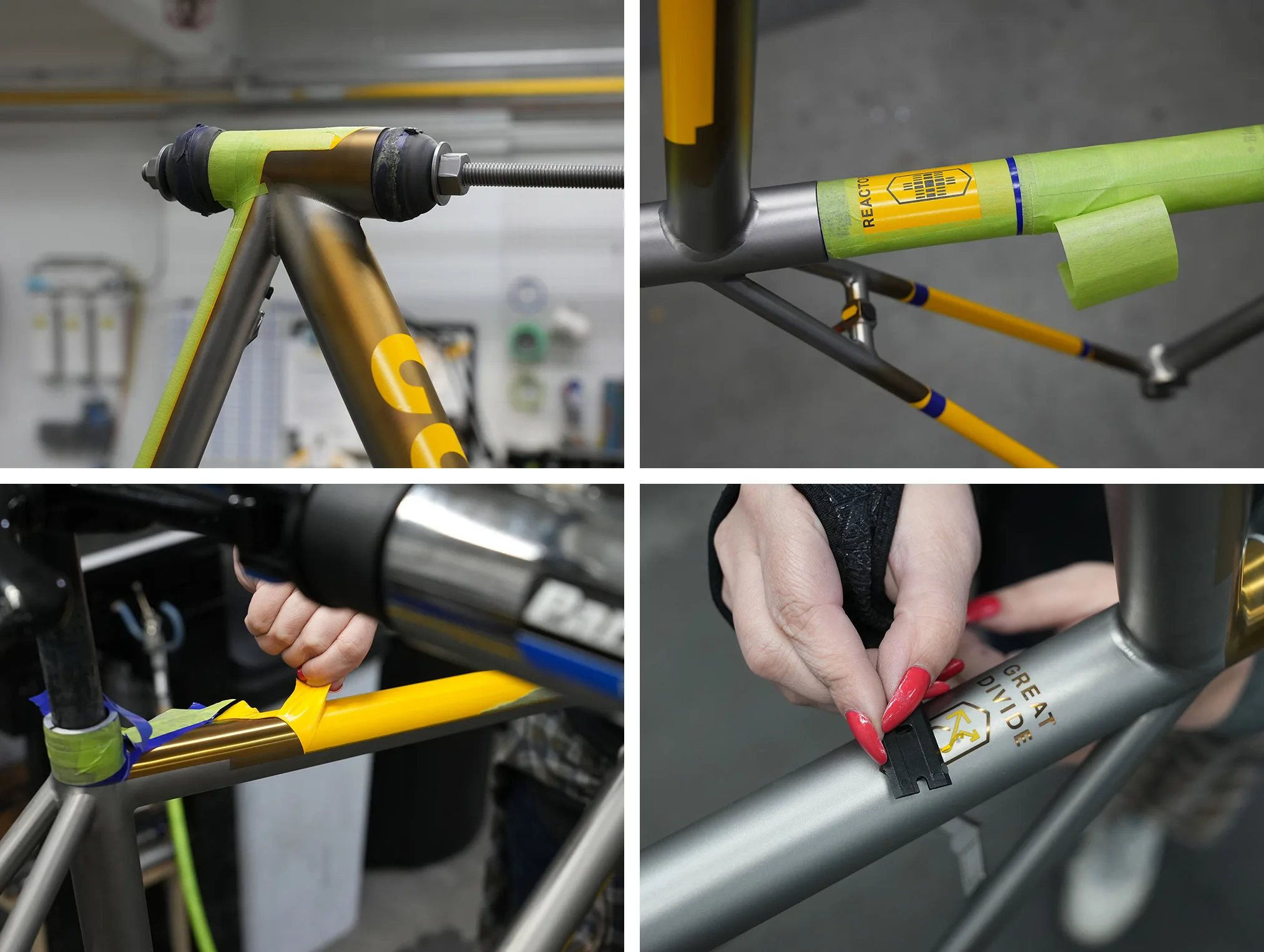
Vinyl decals are minimize on a plotter to create the designs. They’re mixed with the entire Cerakoting, anodizing, sharpening, and blasting to attain the specified final result.
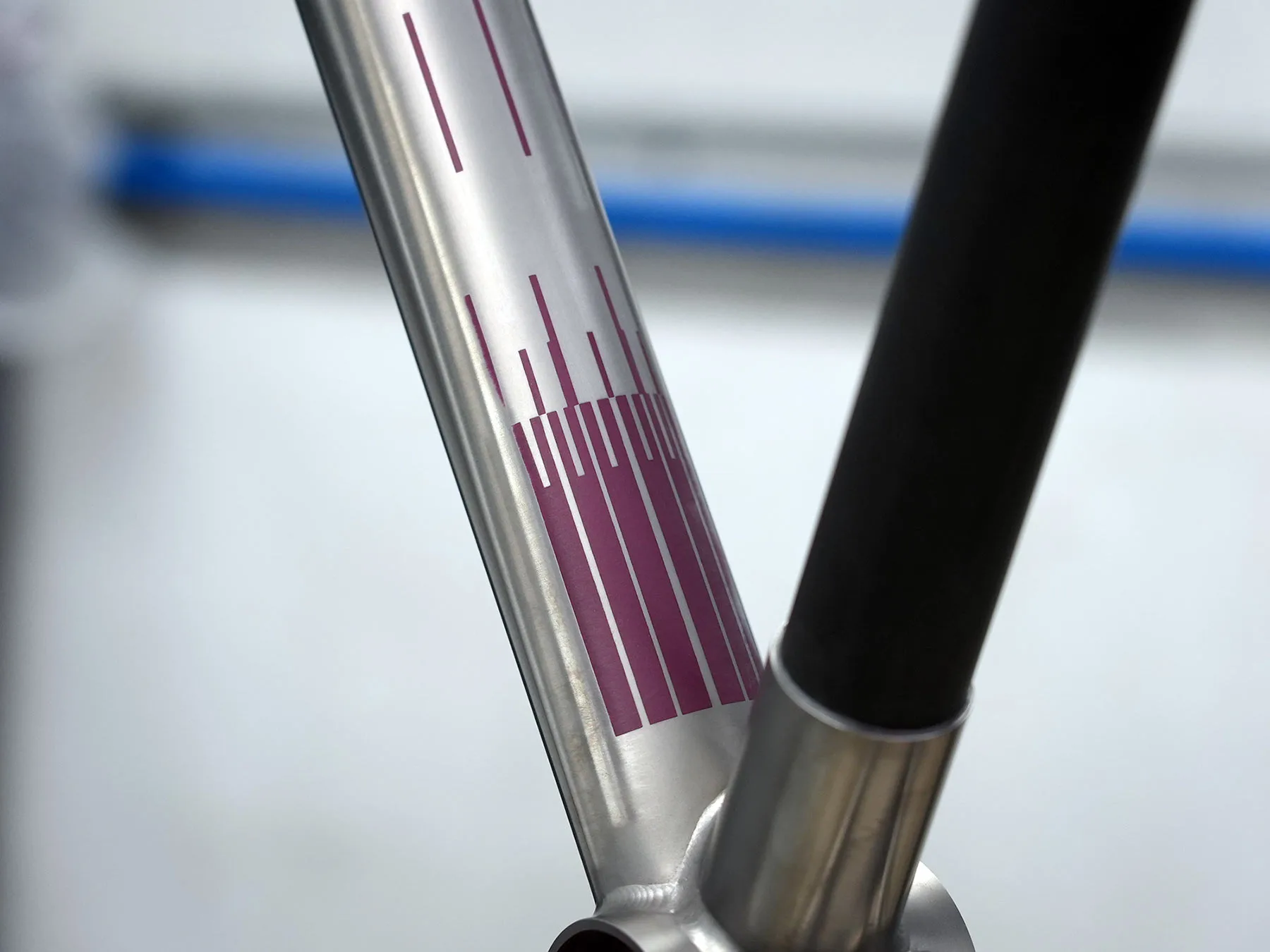
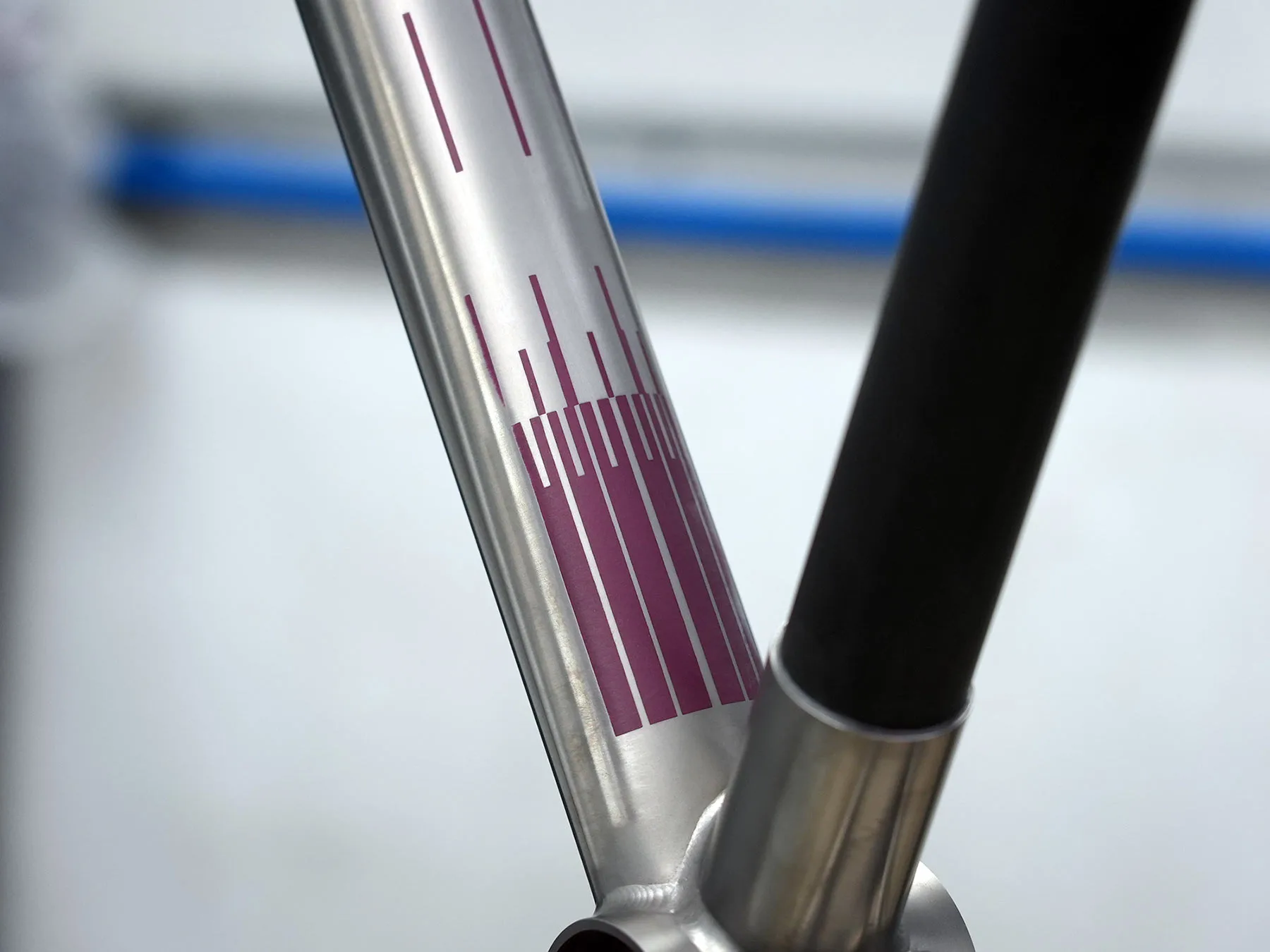
That lets them get very small particulars and logos throughout the whole body.
How No.22 Bikes are Made
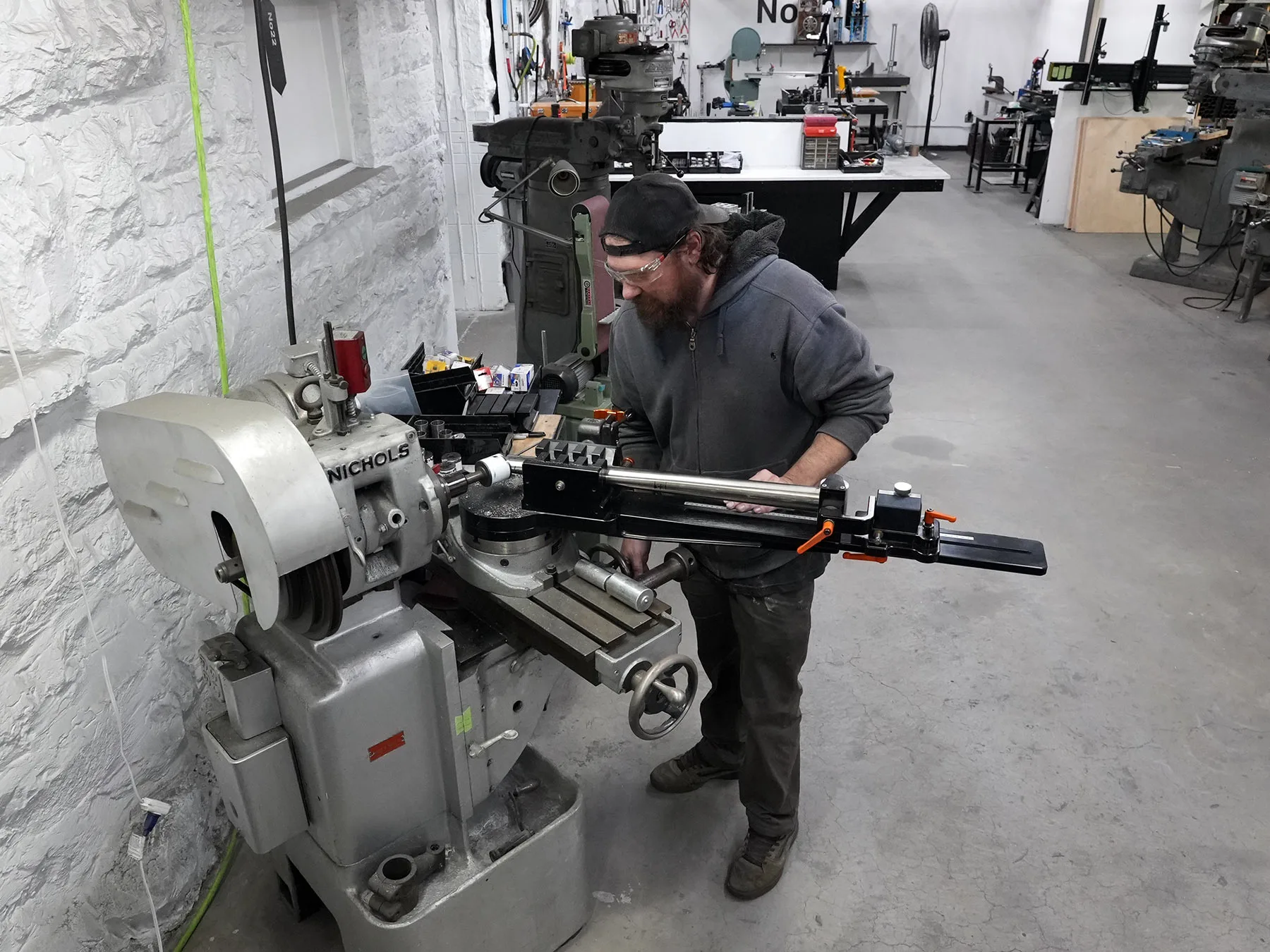
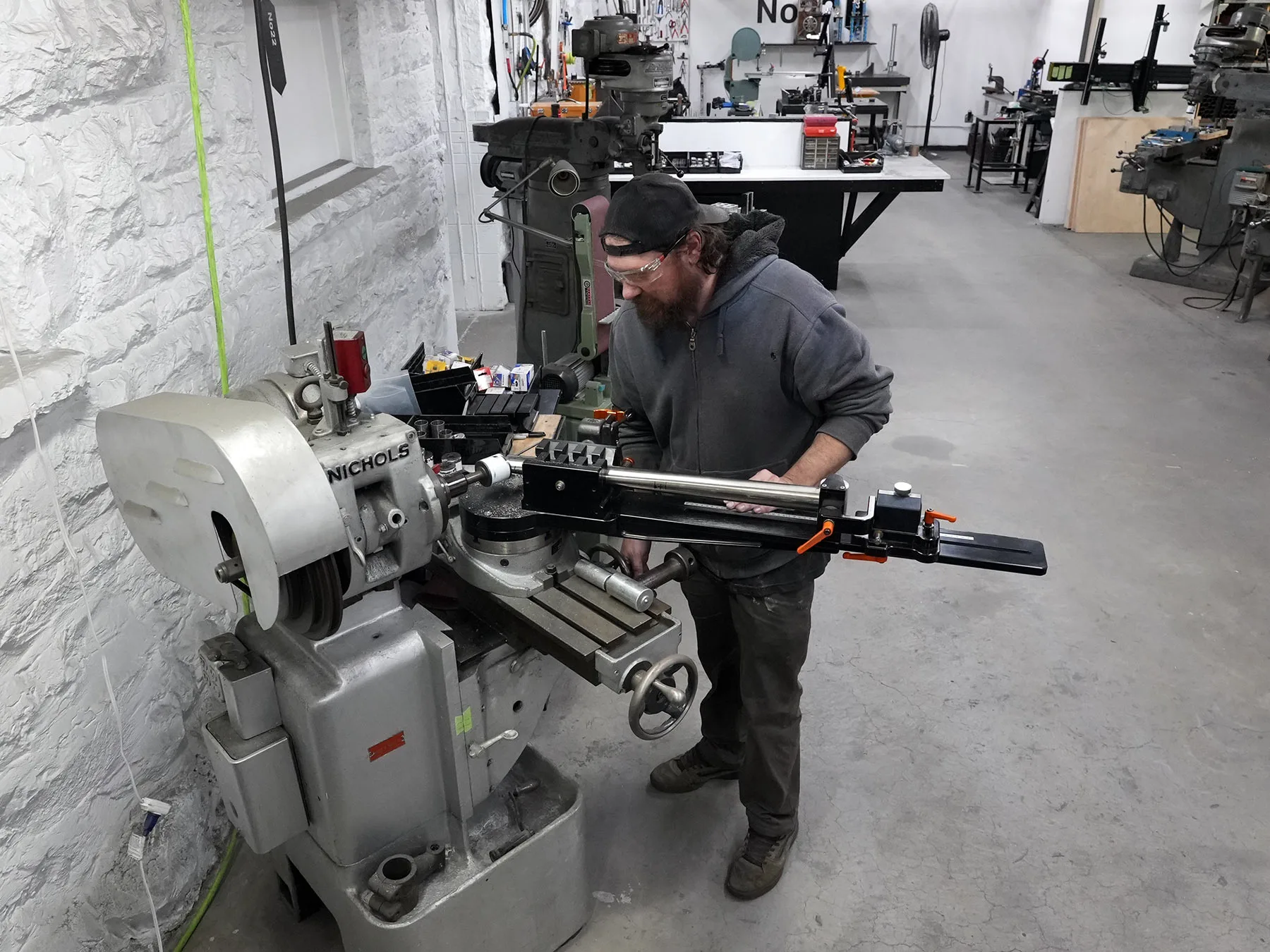
Mike or Bryce are the primary level of contact. They take the order after which they or Scott do the design primarily based on the match numbers. Scott evaluations each one, and he’s received years of expertise coming from match coaching and design at Serotta.
Their prime tubes are largely stage, however they’ll make small tweaks to the highest tube’s slope to get a seatpost brand a number of mm above the collar. It’s a purely aesthetic effort, however particulars matter.
Buyer order sheets have all of the numbers, then it goes to manufacturing. They don’t do body drawings anymore, it’s all carried out by quantity, and it’s colour coded by fixture so it’s simple to effectively run it by means of the system. They’ve machines and fixtures for many steps in order that it may well transfer by means of shortly with out requiring quite a lot of additional setup steps between completely different tubes.
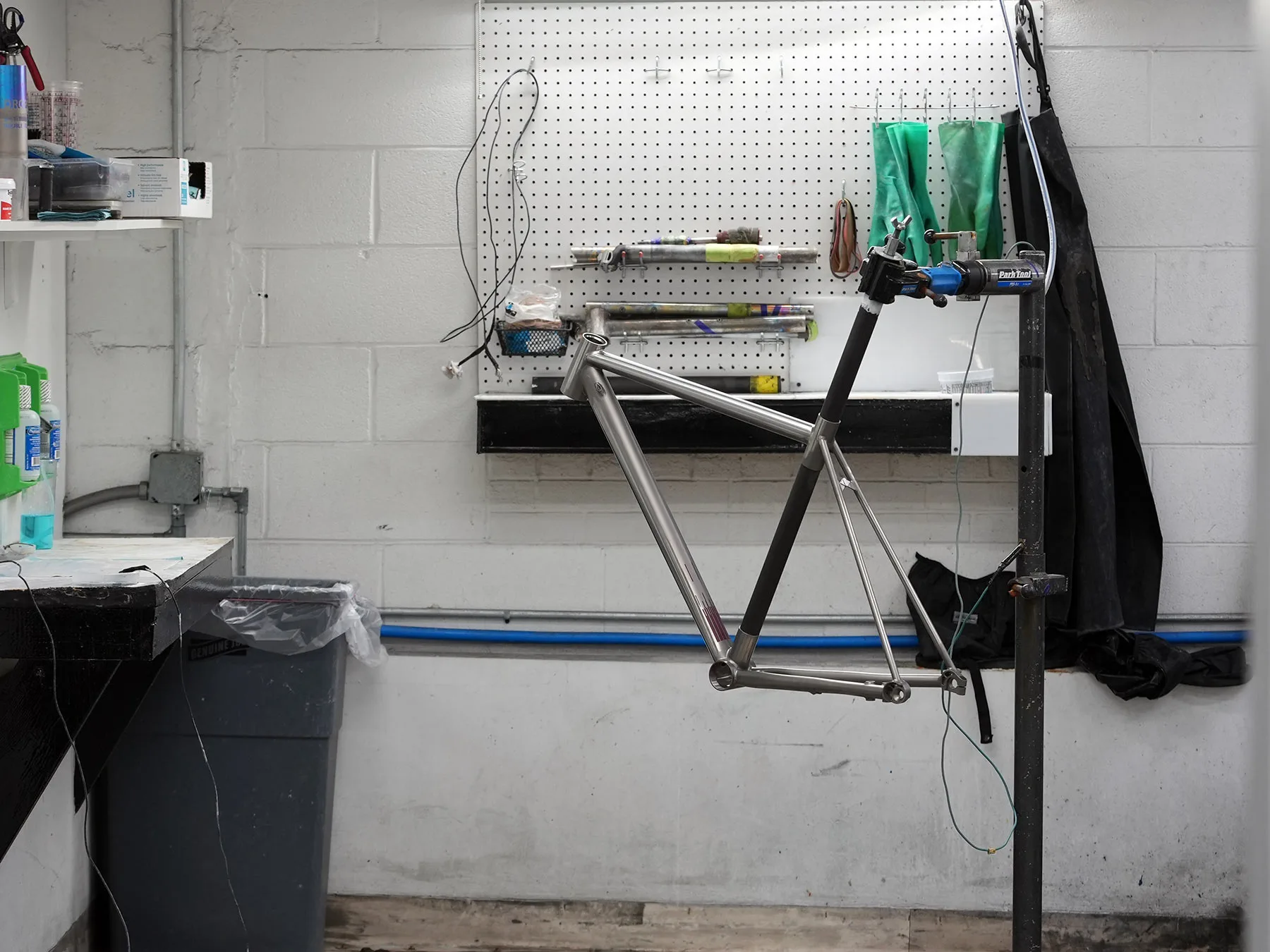
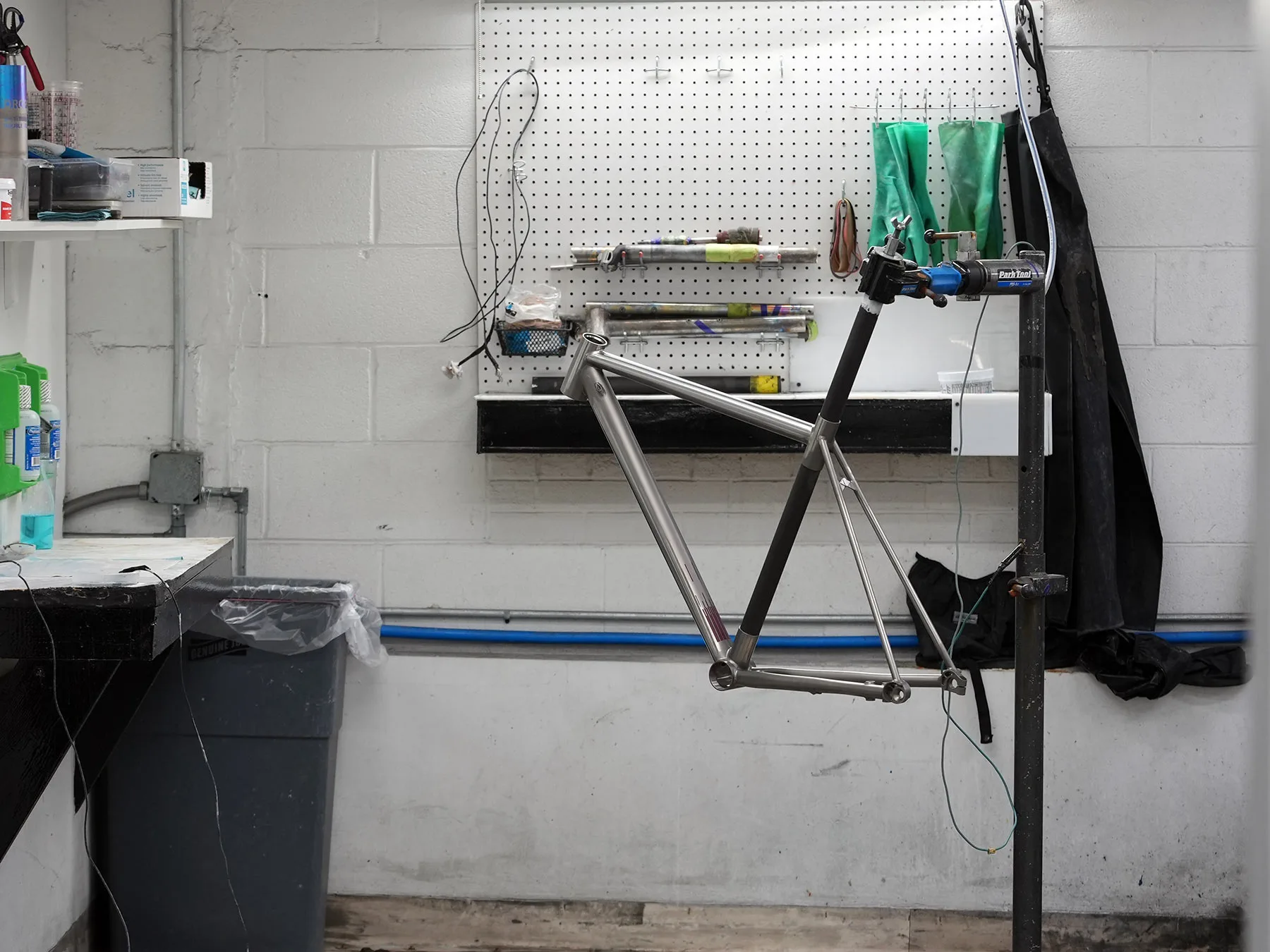
The Aurora and Reactor have a carbon seat tube and mast, and so they make that with an adjustable insert somewhat than make the bike with a full seat tube then minimize it out, saving tubing.
Each tube is checked for the “excessive aspect”, as a result of they’re not straight, in order that they have the excessive aspect pointing straight into the within of the entrance triangle, which retains the tubes aligned. With out this, it might make the body “lean” left or proper and almost unattainable to make excellent. All that mentioned, we’re speaking about ~0.3mm variance, so it’s only a good instance of the eye to element.
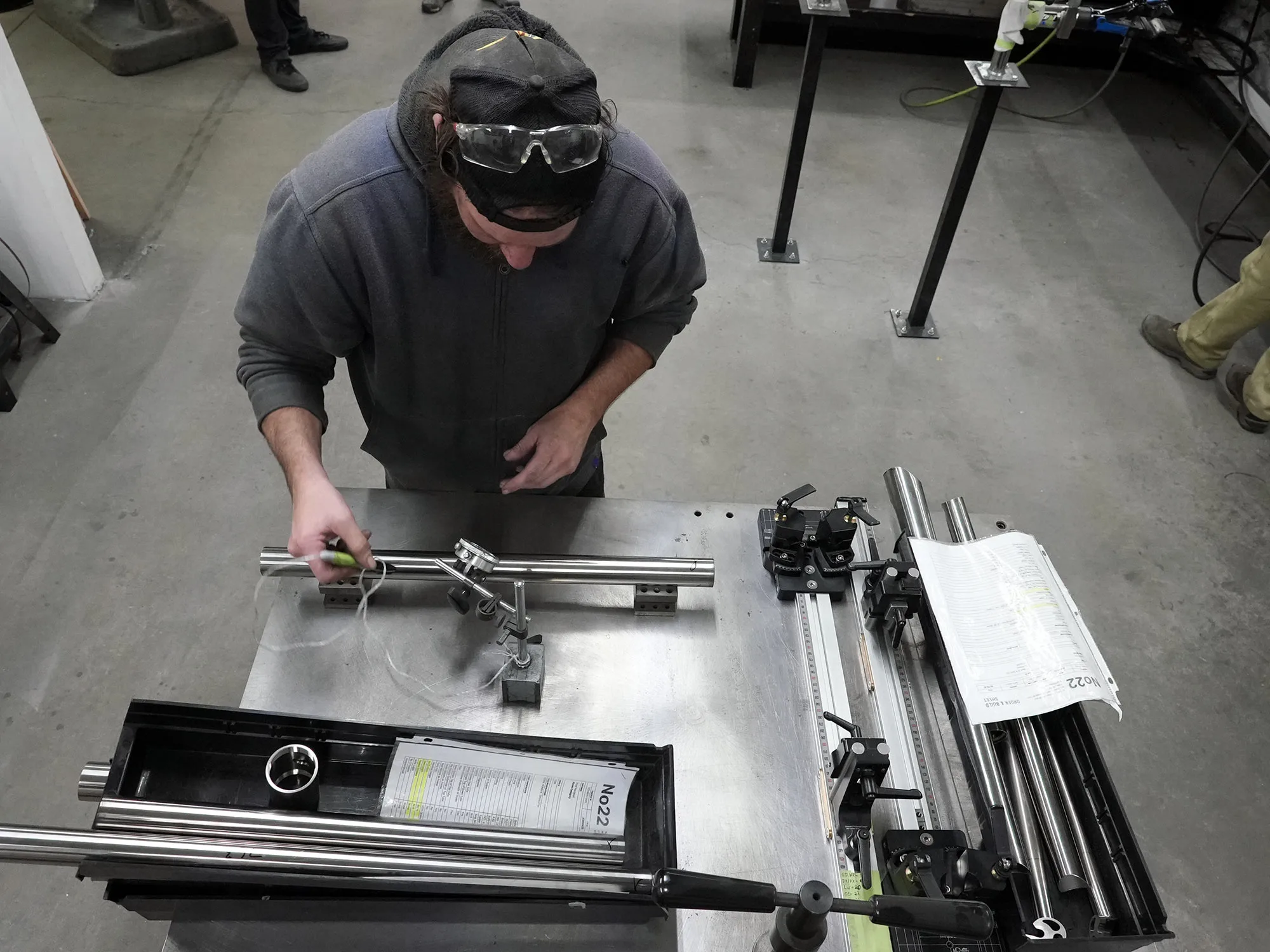
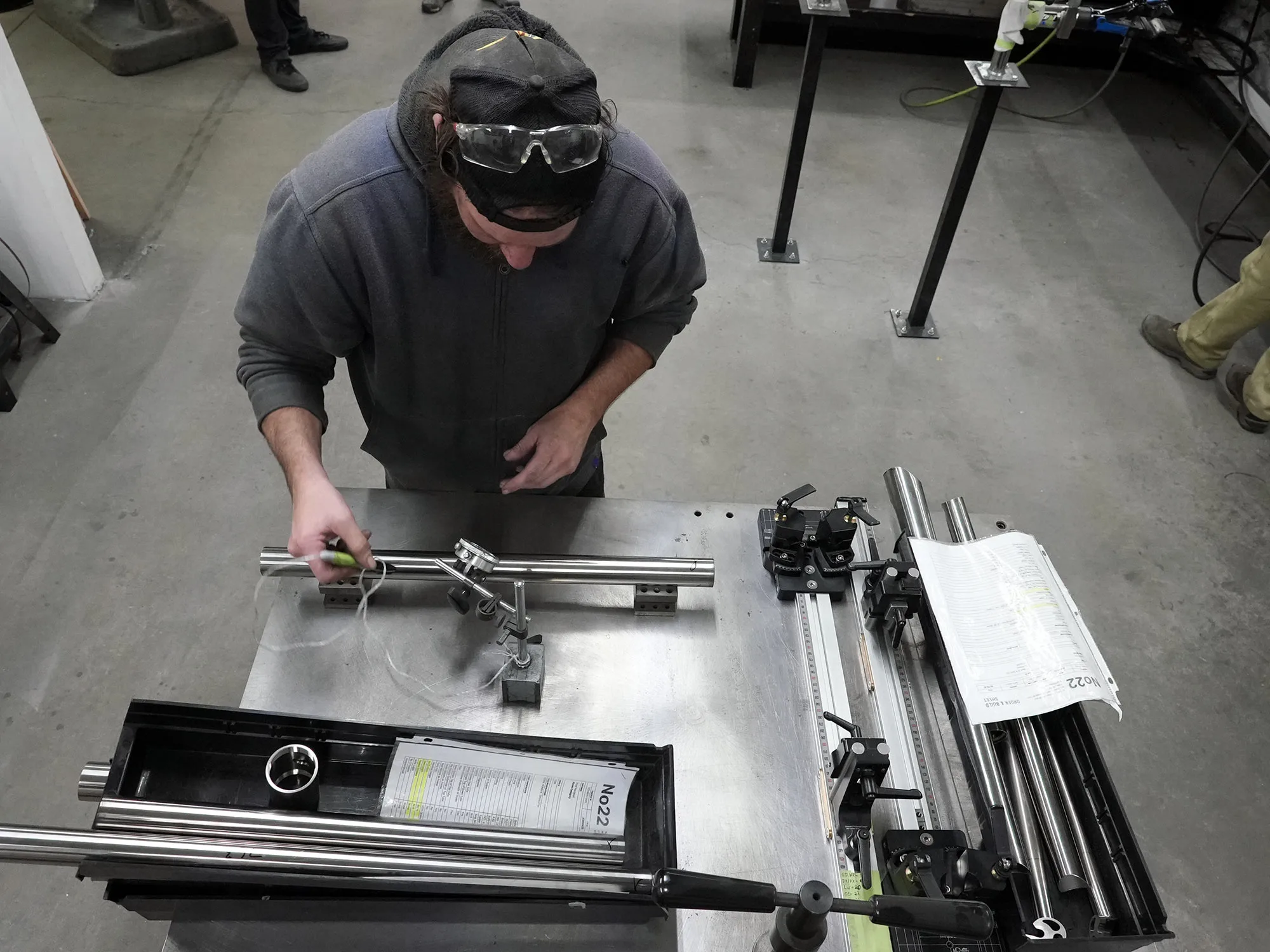
Butting the principle tubes saves as much as 75g per tube, and likewise offers it a springier trip high quality, and permits them to get a constant trip high quality throughout the dimensions vary.
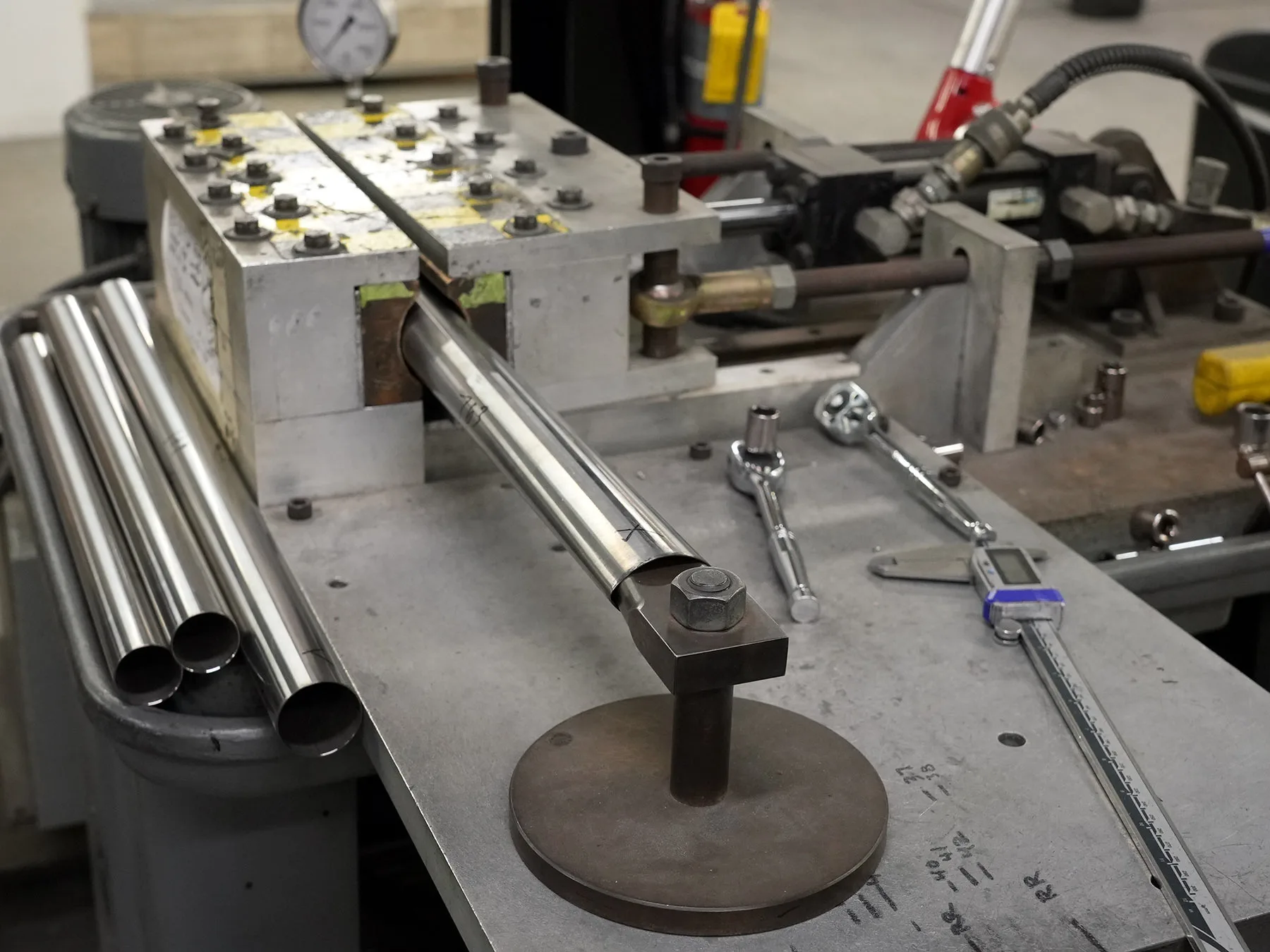
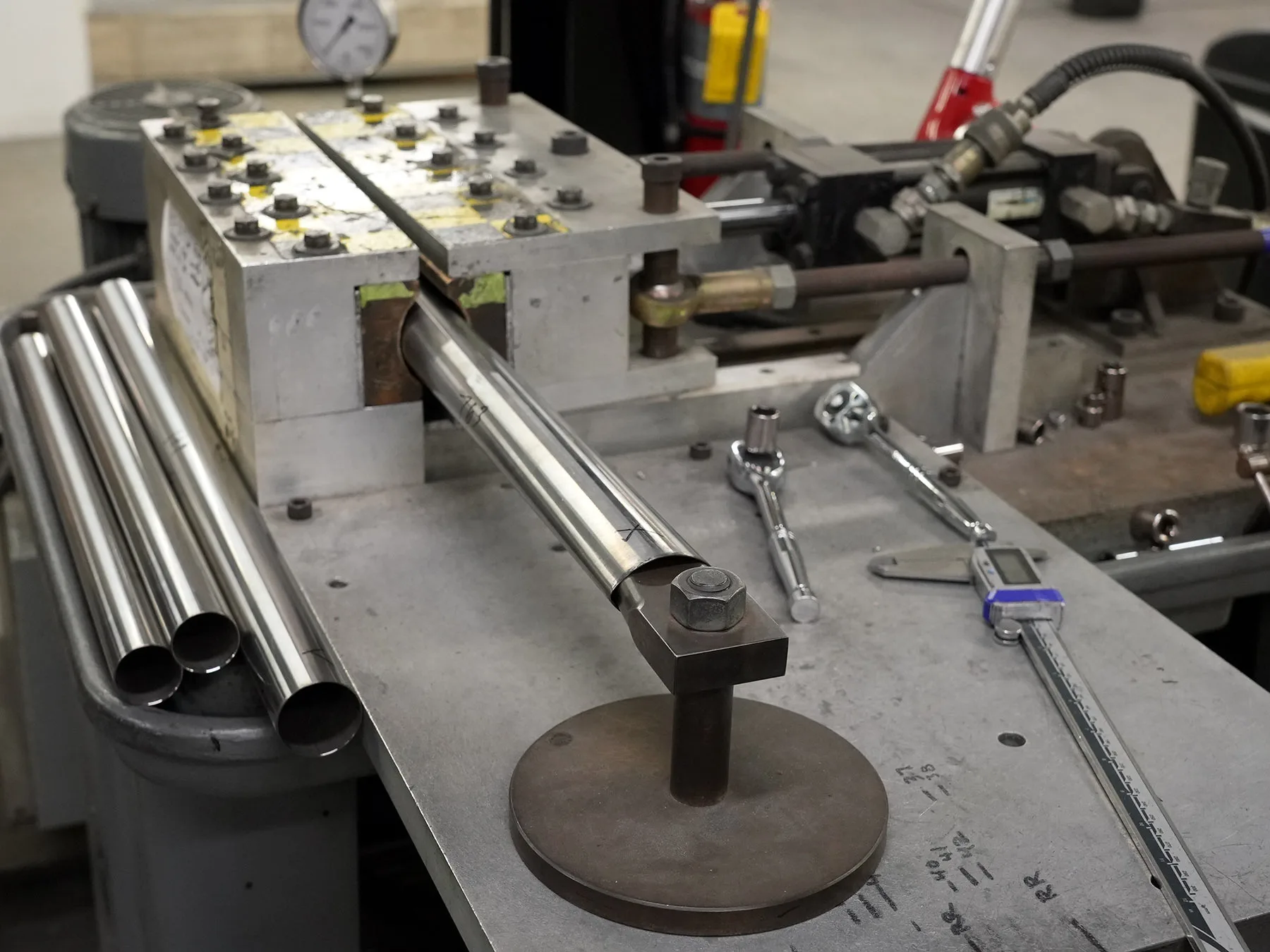
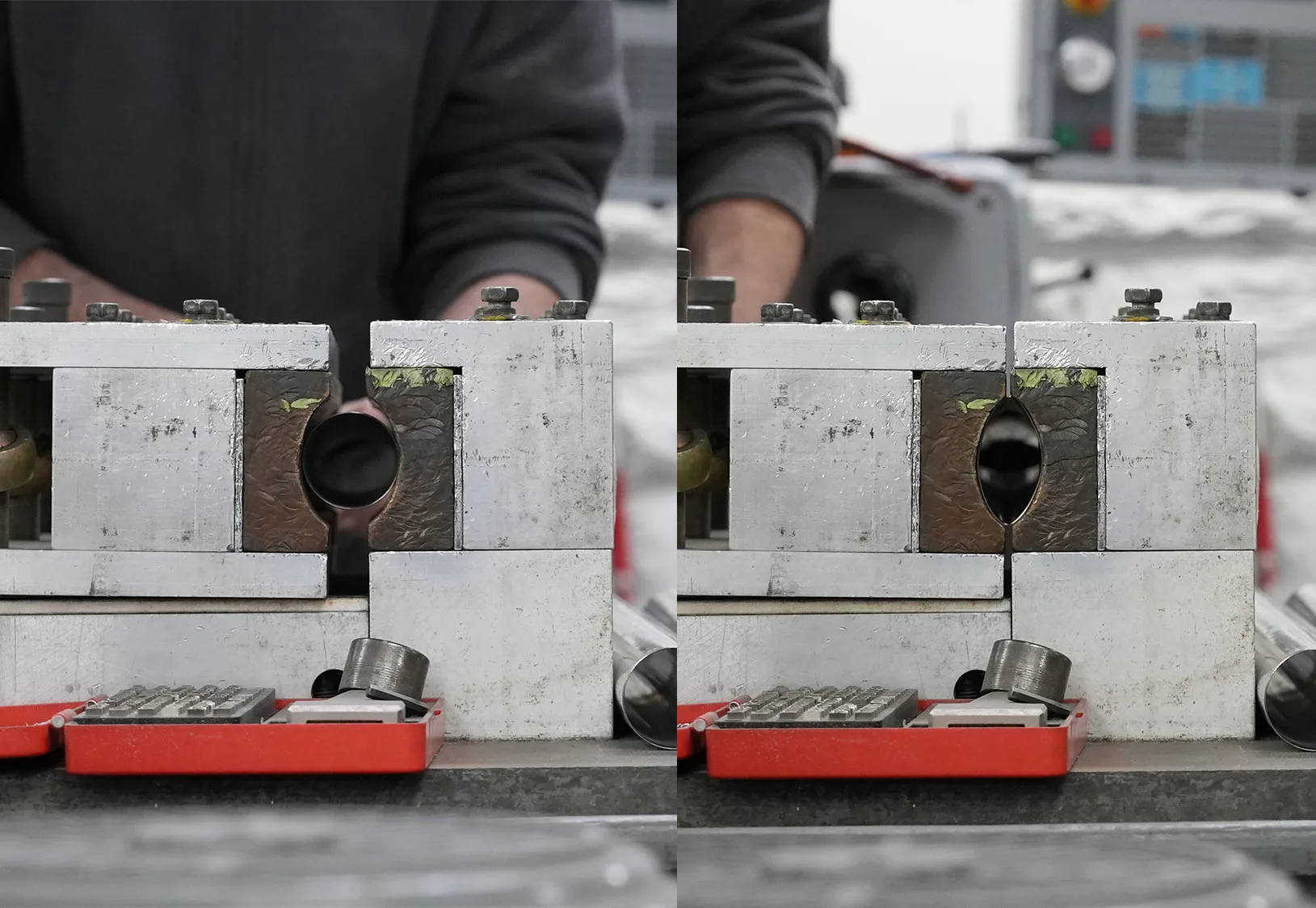
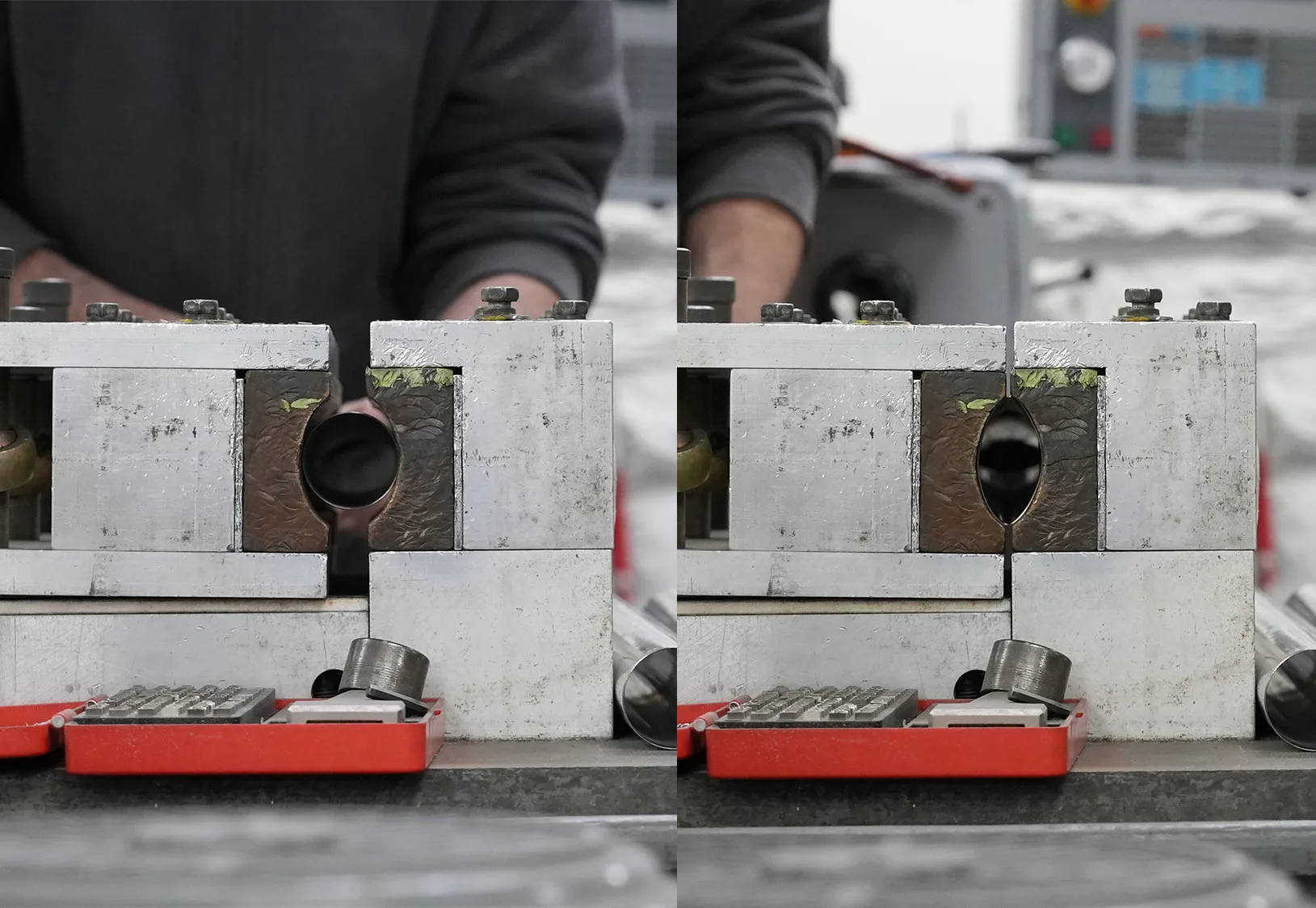
Downtubes are bi-ovalized giving them a wider stance on the backside for a stiffer BB space, and taller on the headtube for a extra streamlined look. The jigs above compress the tube whereas the opposite is held in place at 90º.
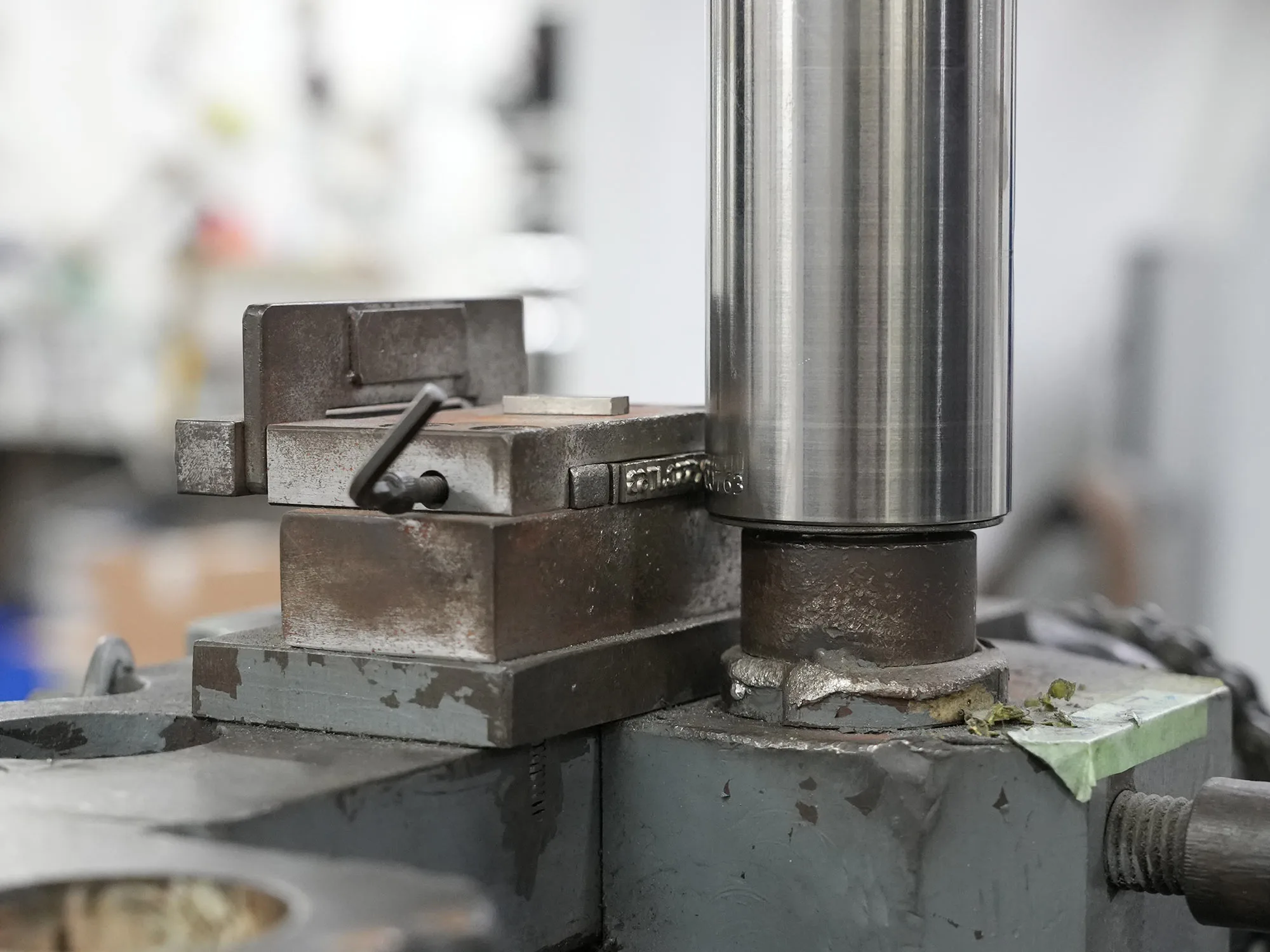
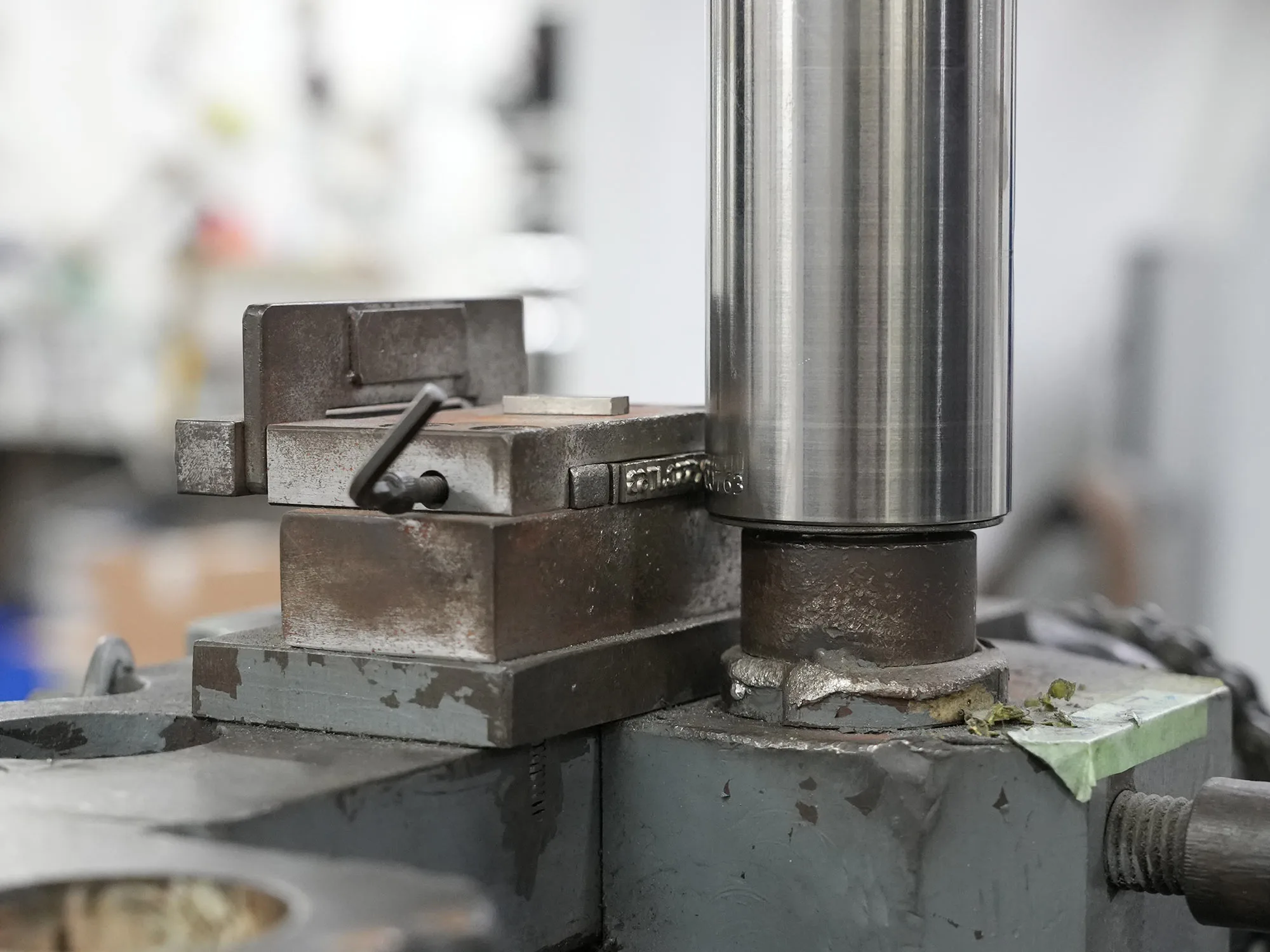
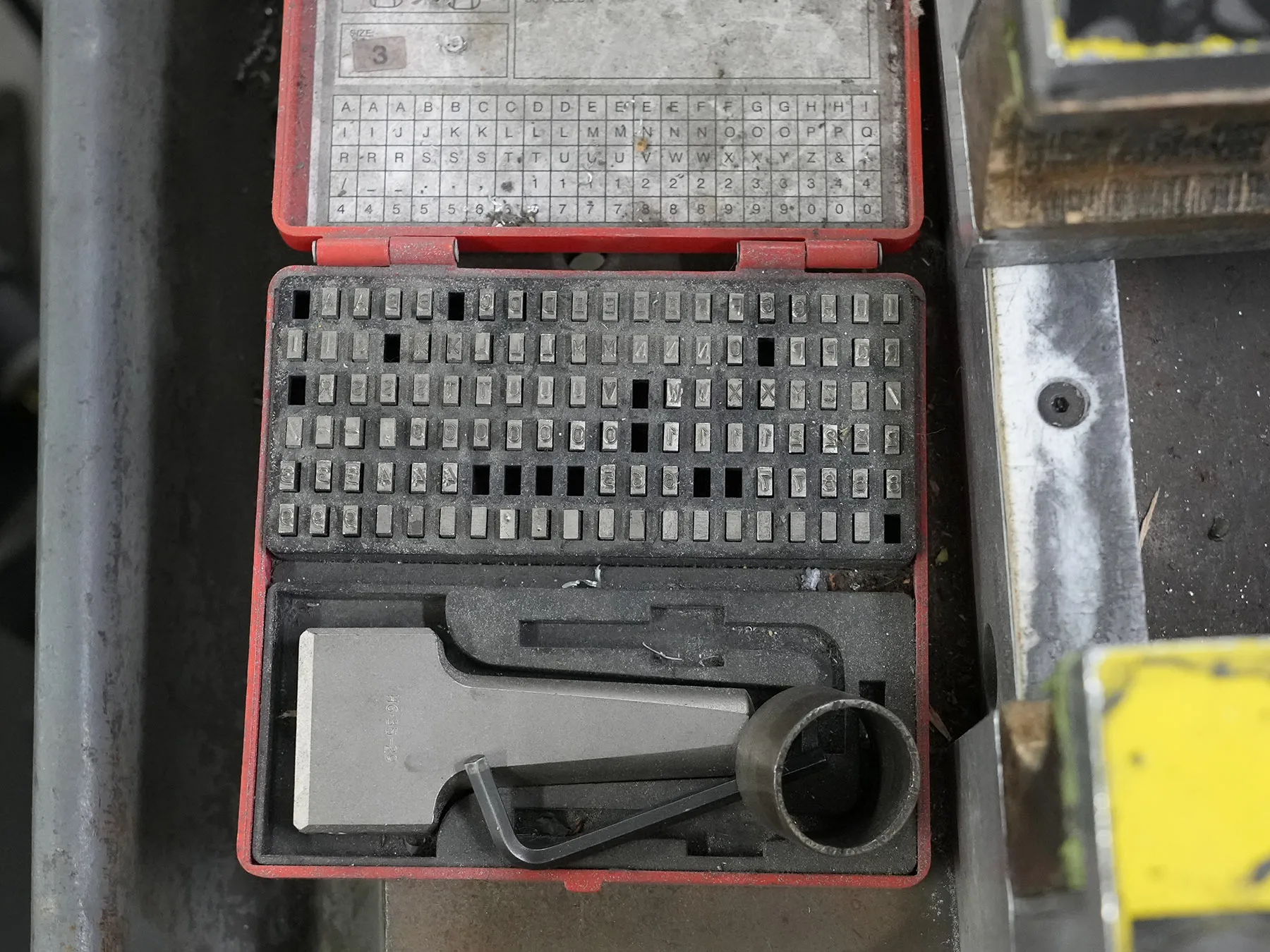
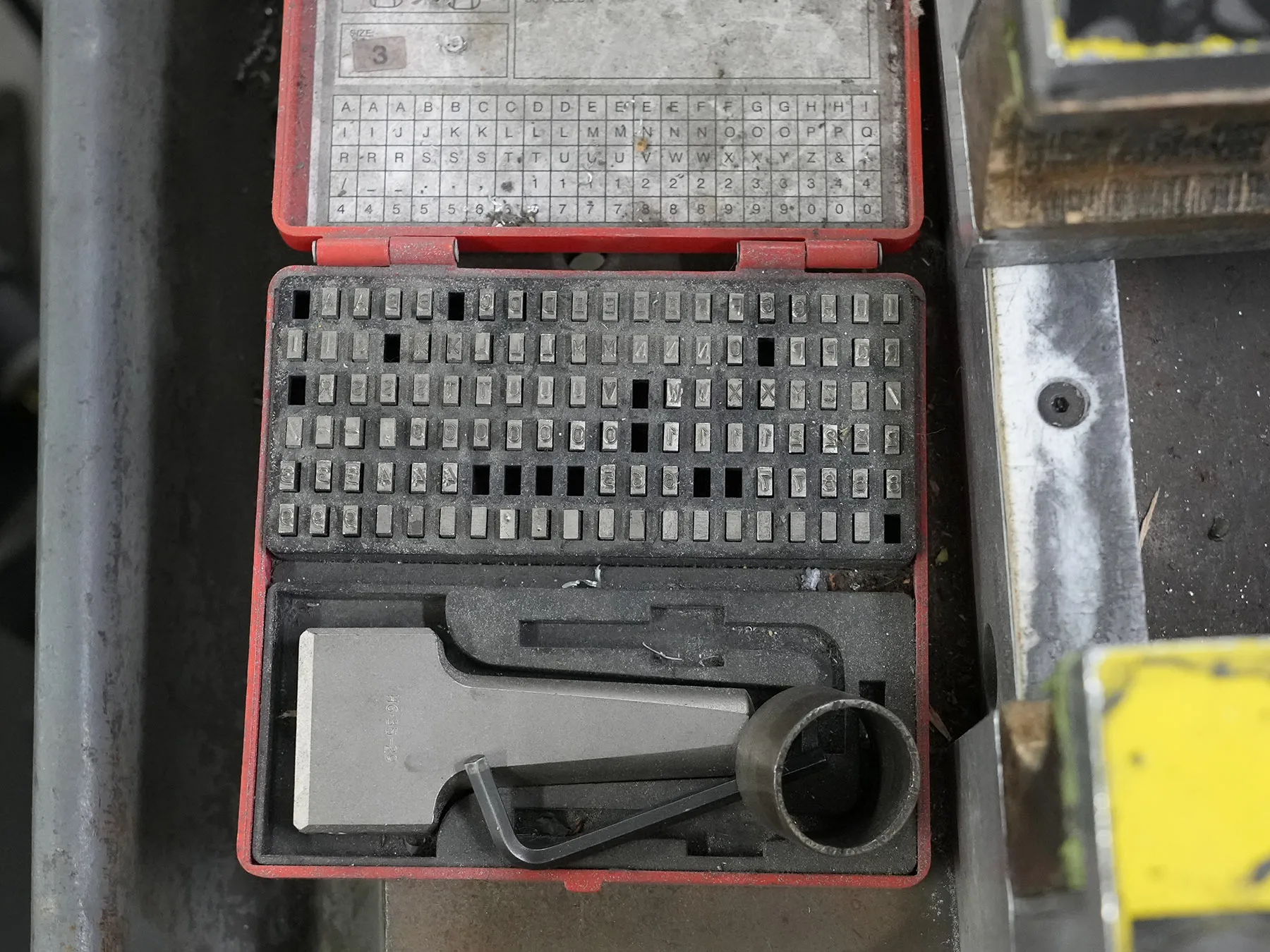
Serial numbers are stamped into the body by inserting particular person characters right into a plate, then rolling the BB shell throughout it below stress. Very guide, and really cool.
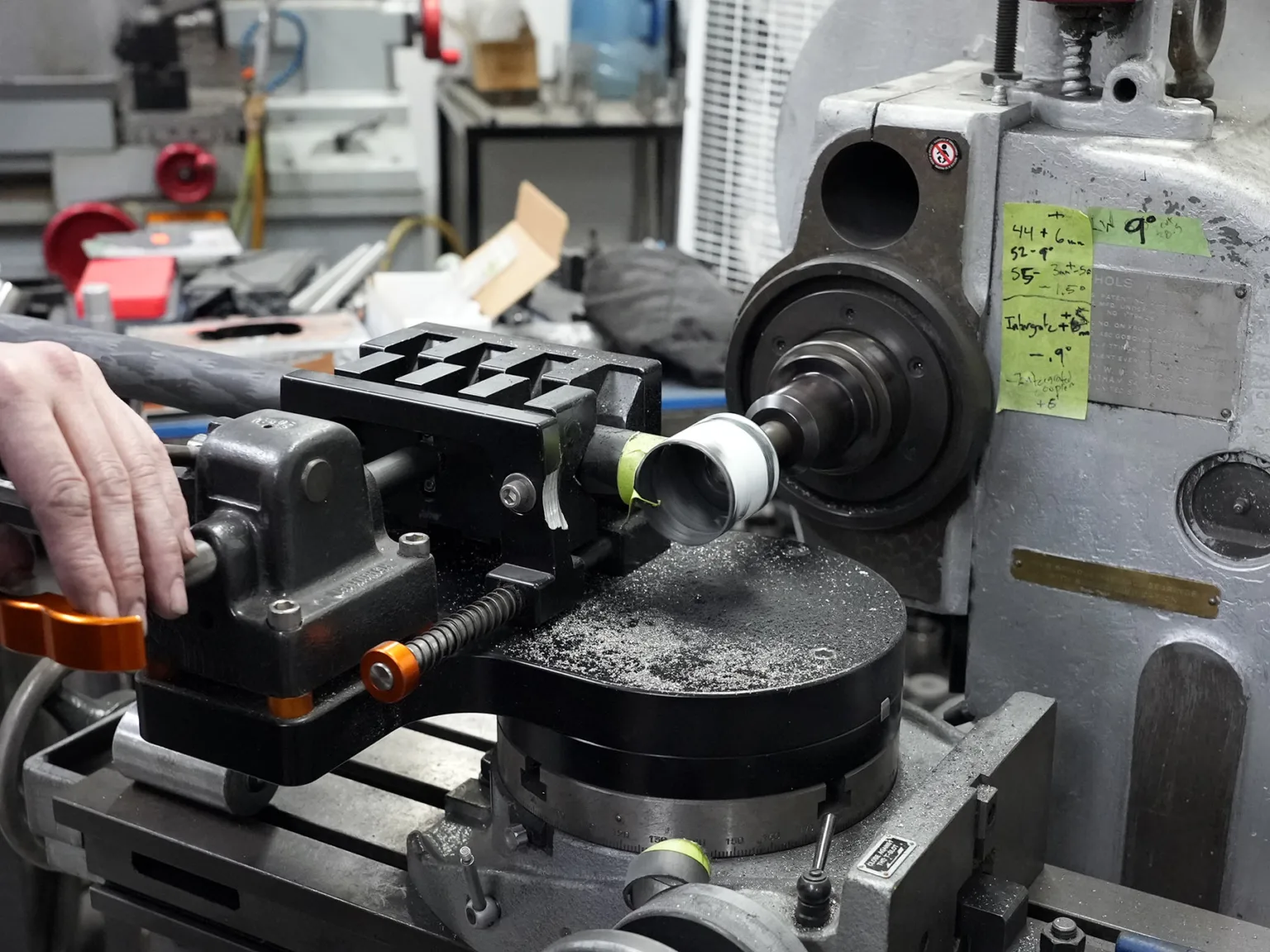
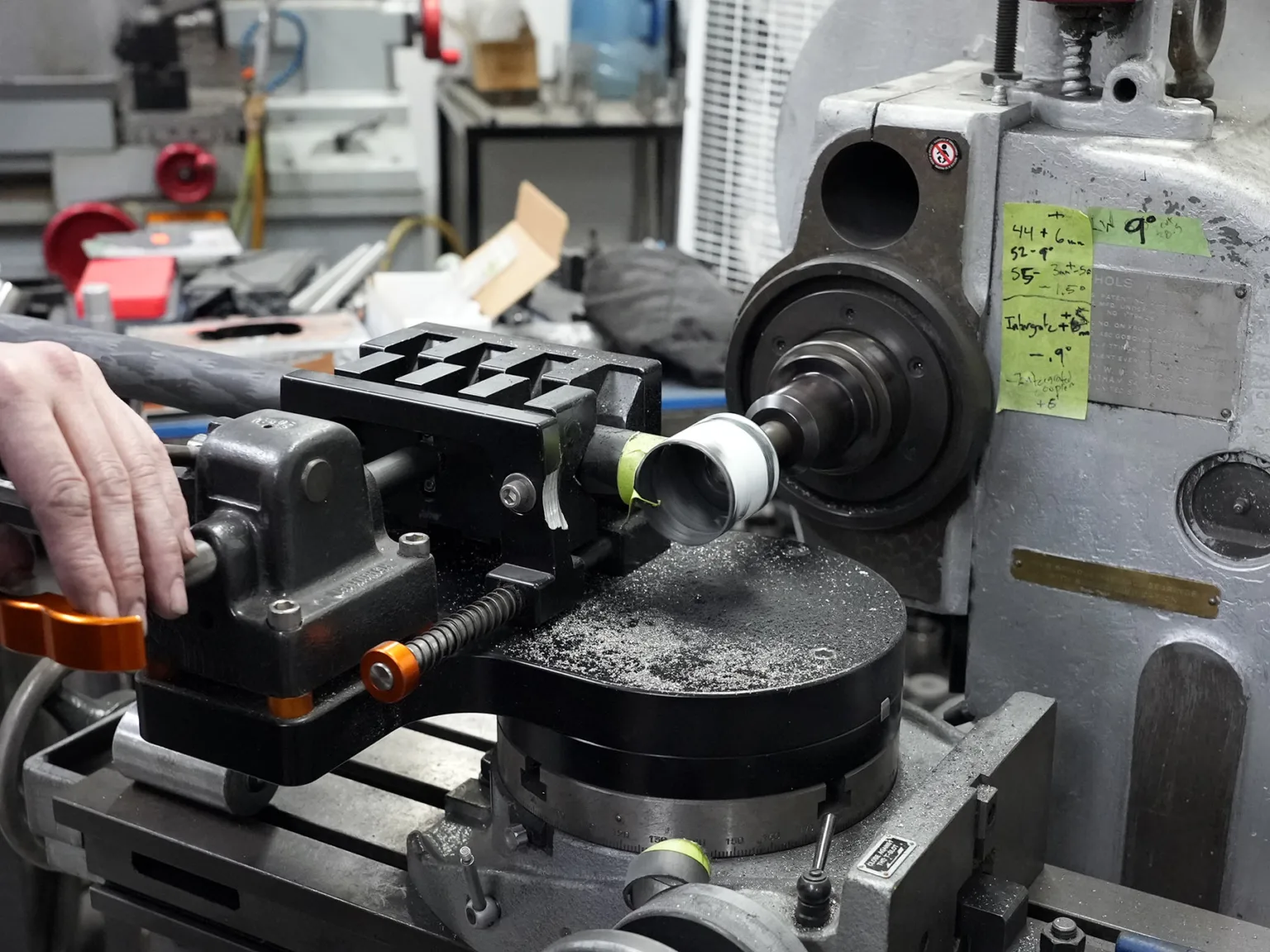
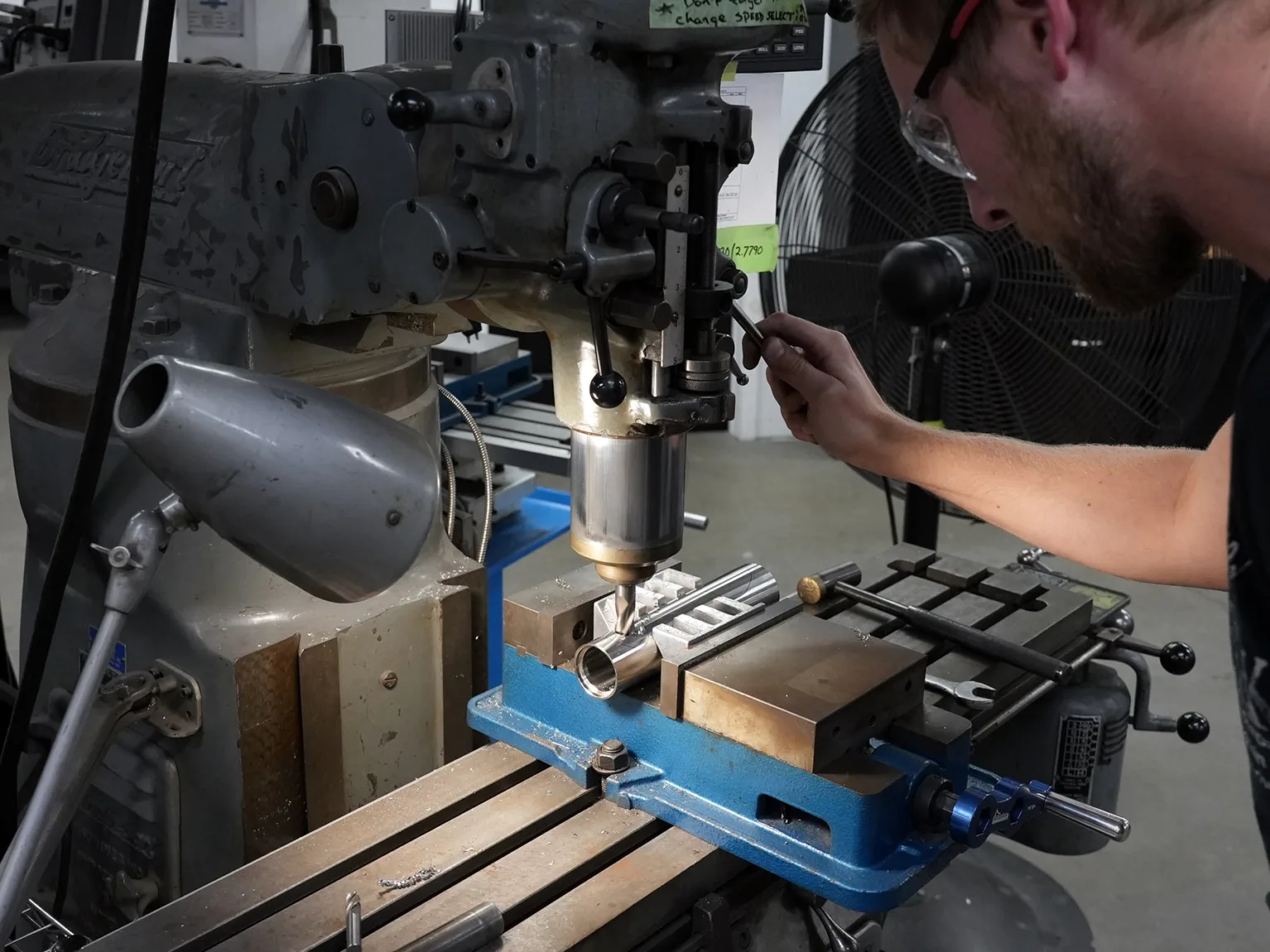
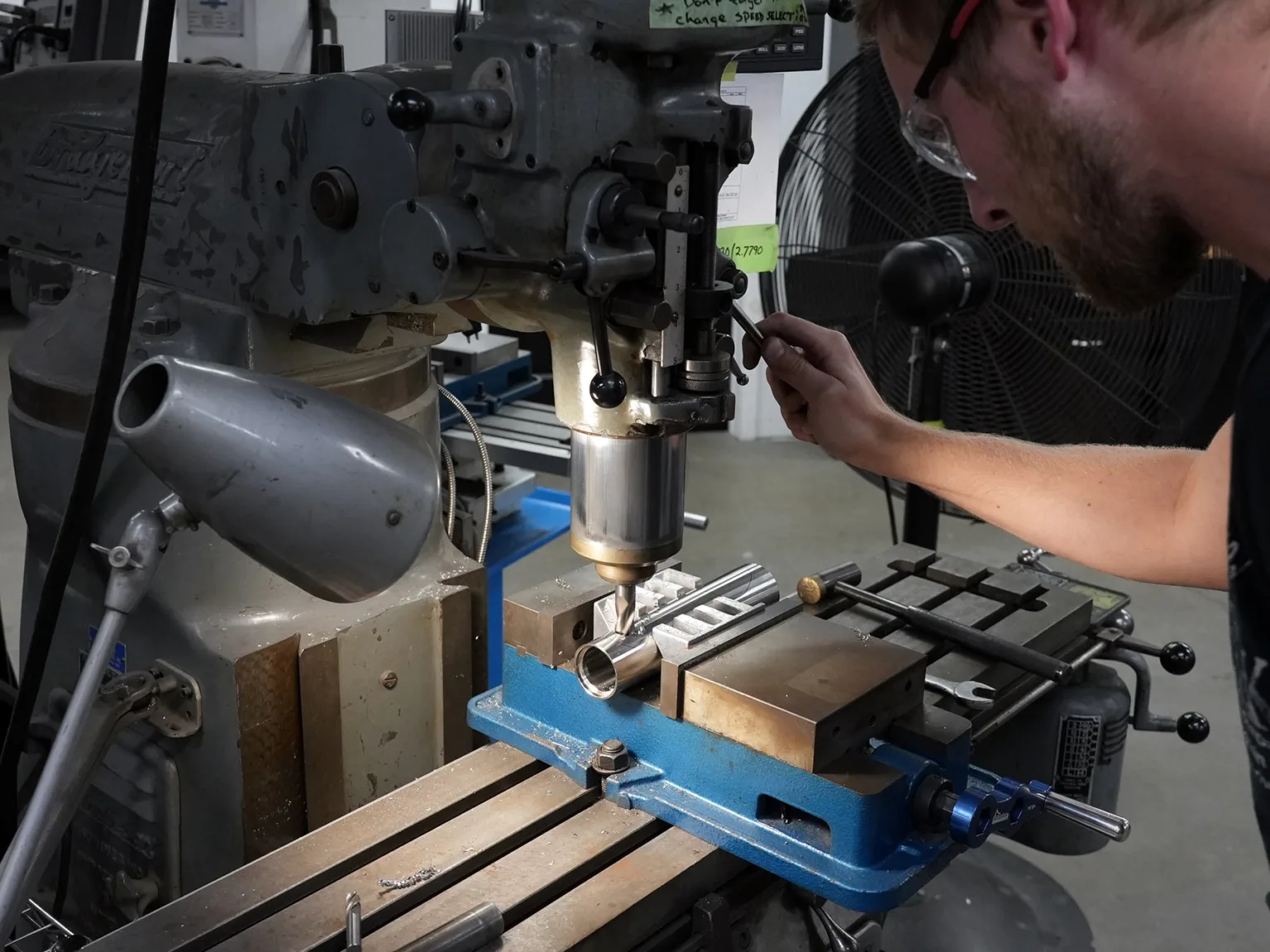
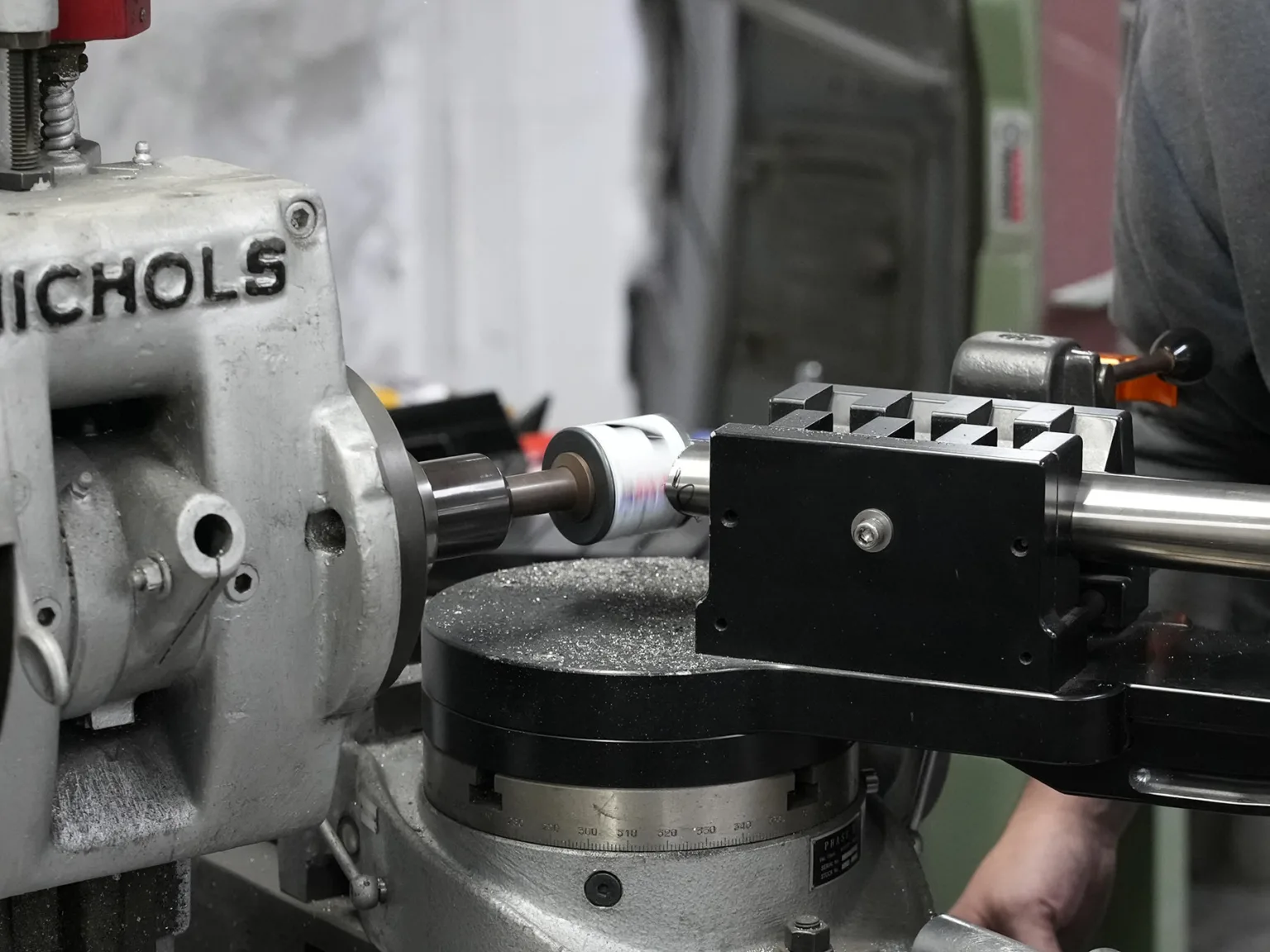
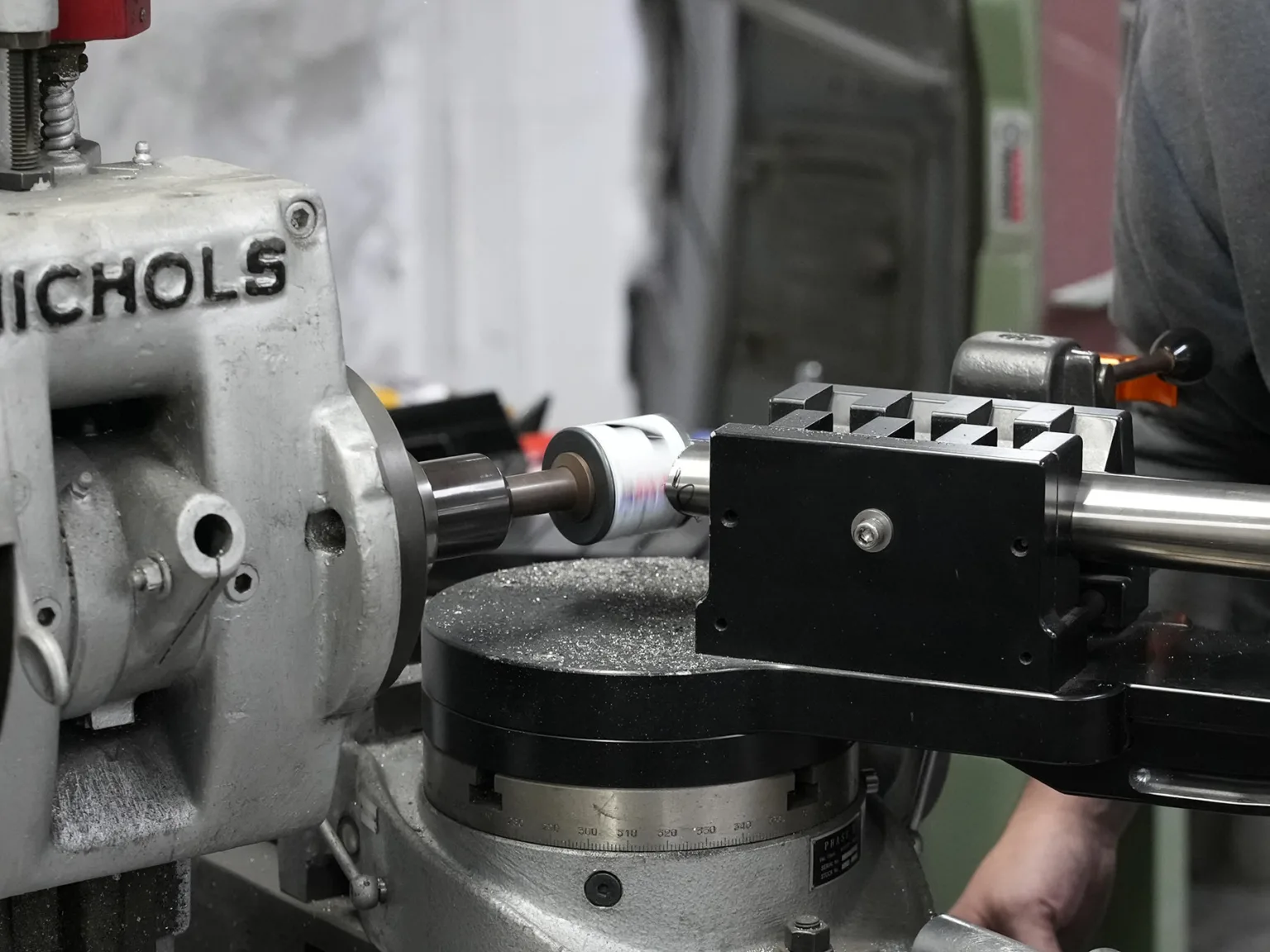
As soon as minimize to size, tubes are mitered, drilled, and in any other case prepped for his or her construct.
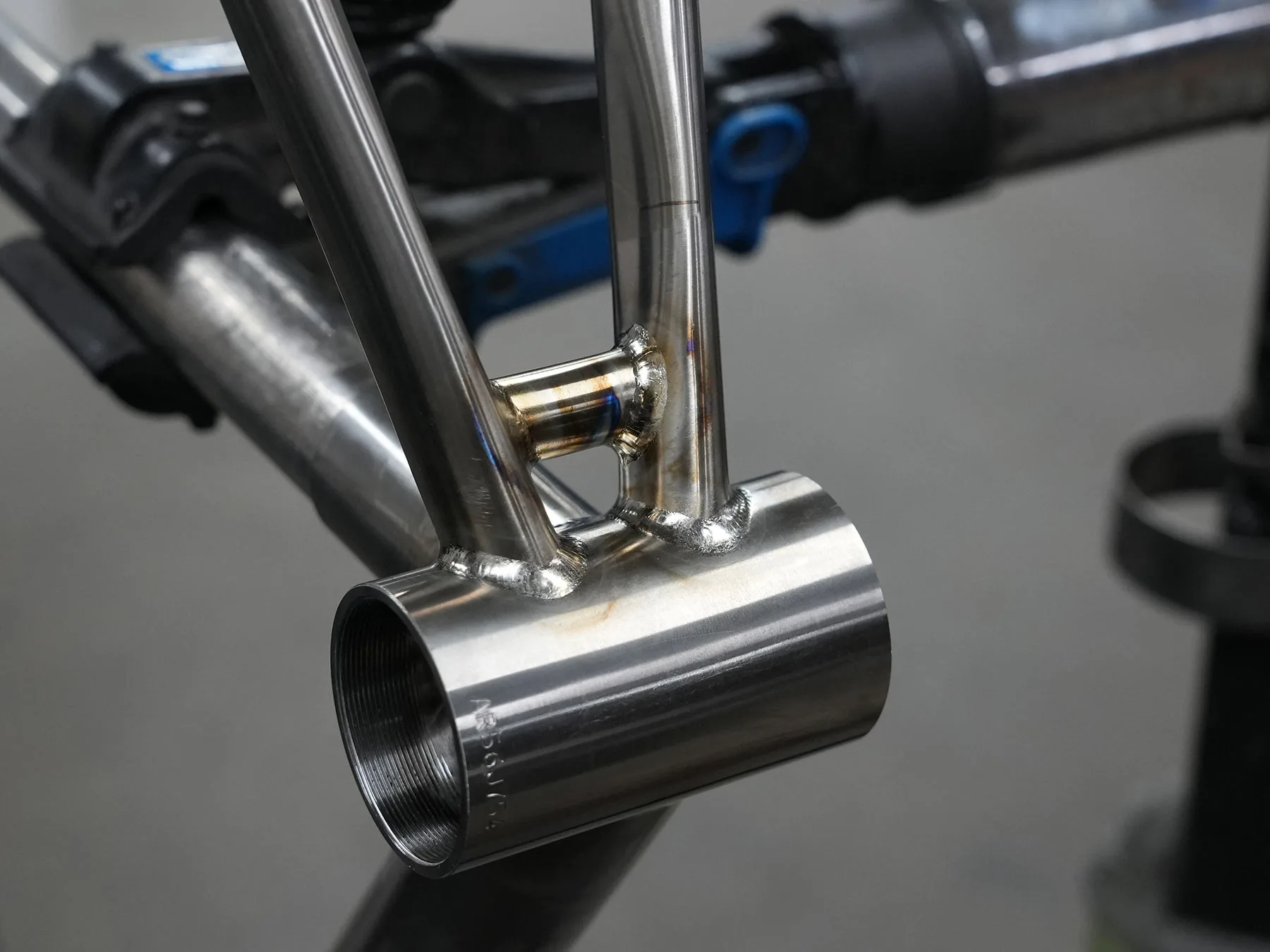
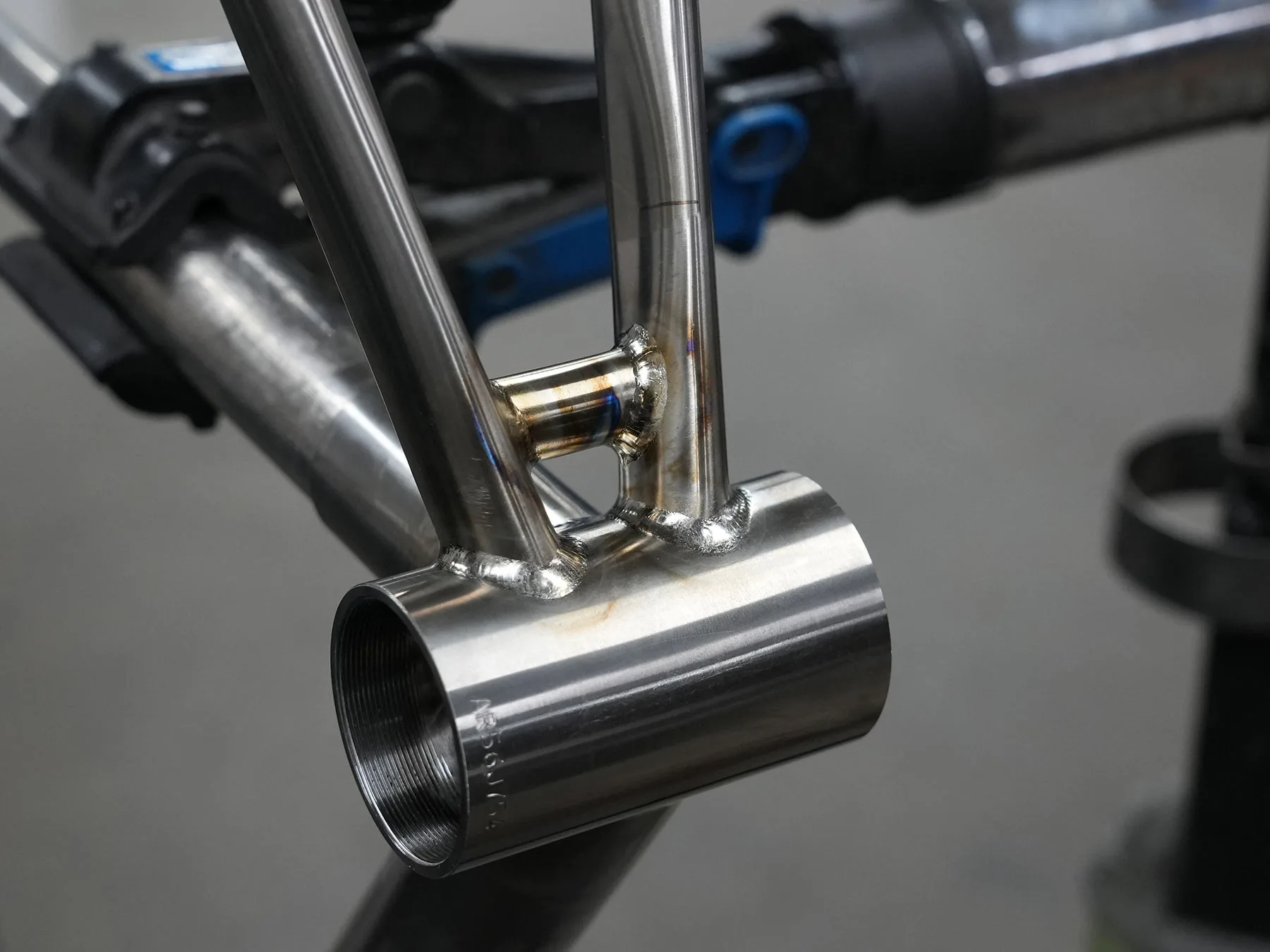
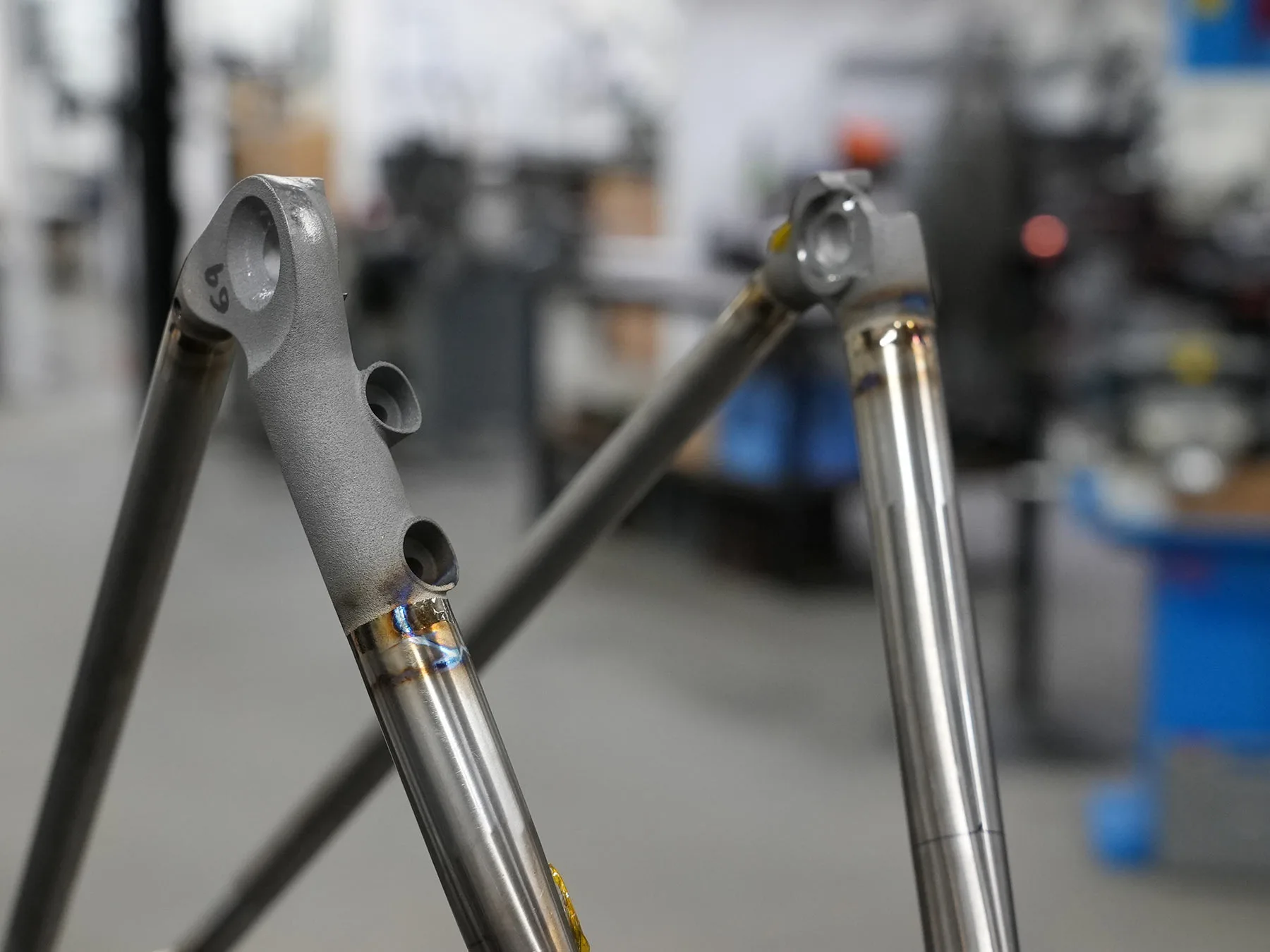
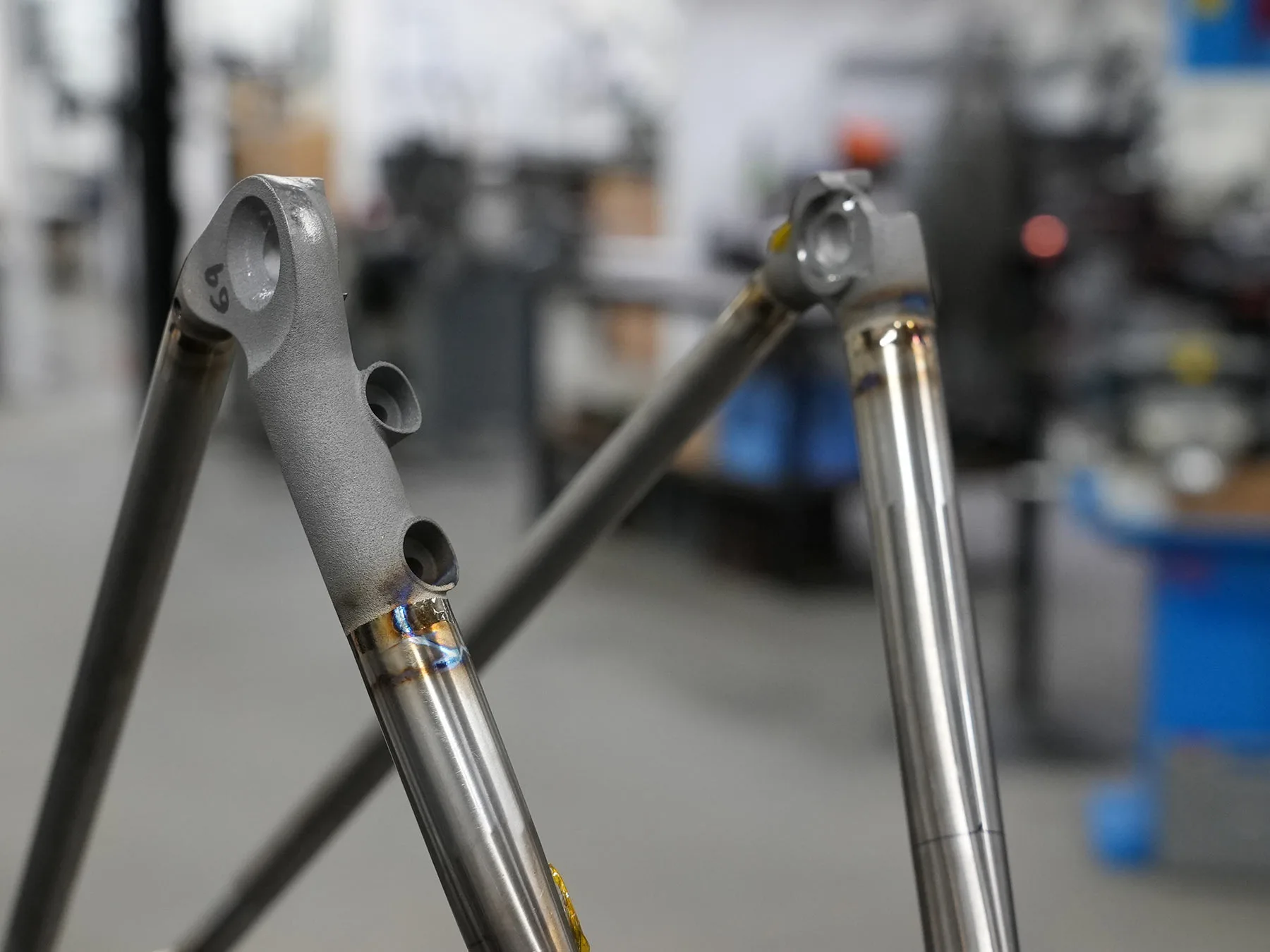
Chainstays are welded on with a wider axle spacer, as a result of they pull inward as they’re heated, in order that they weld them into spec somewhat than having to bend them into alignment after the actual fact.
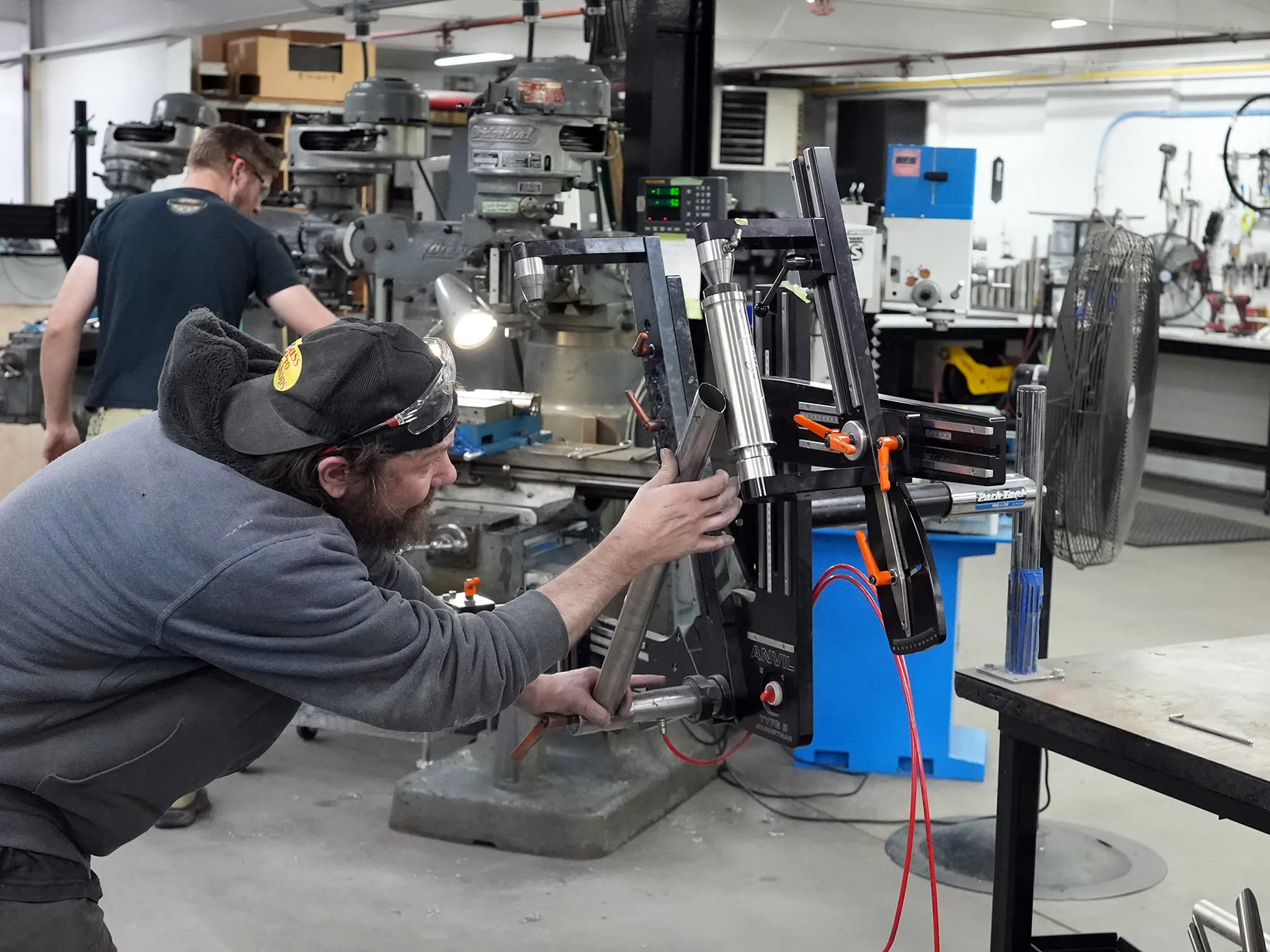
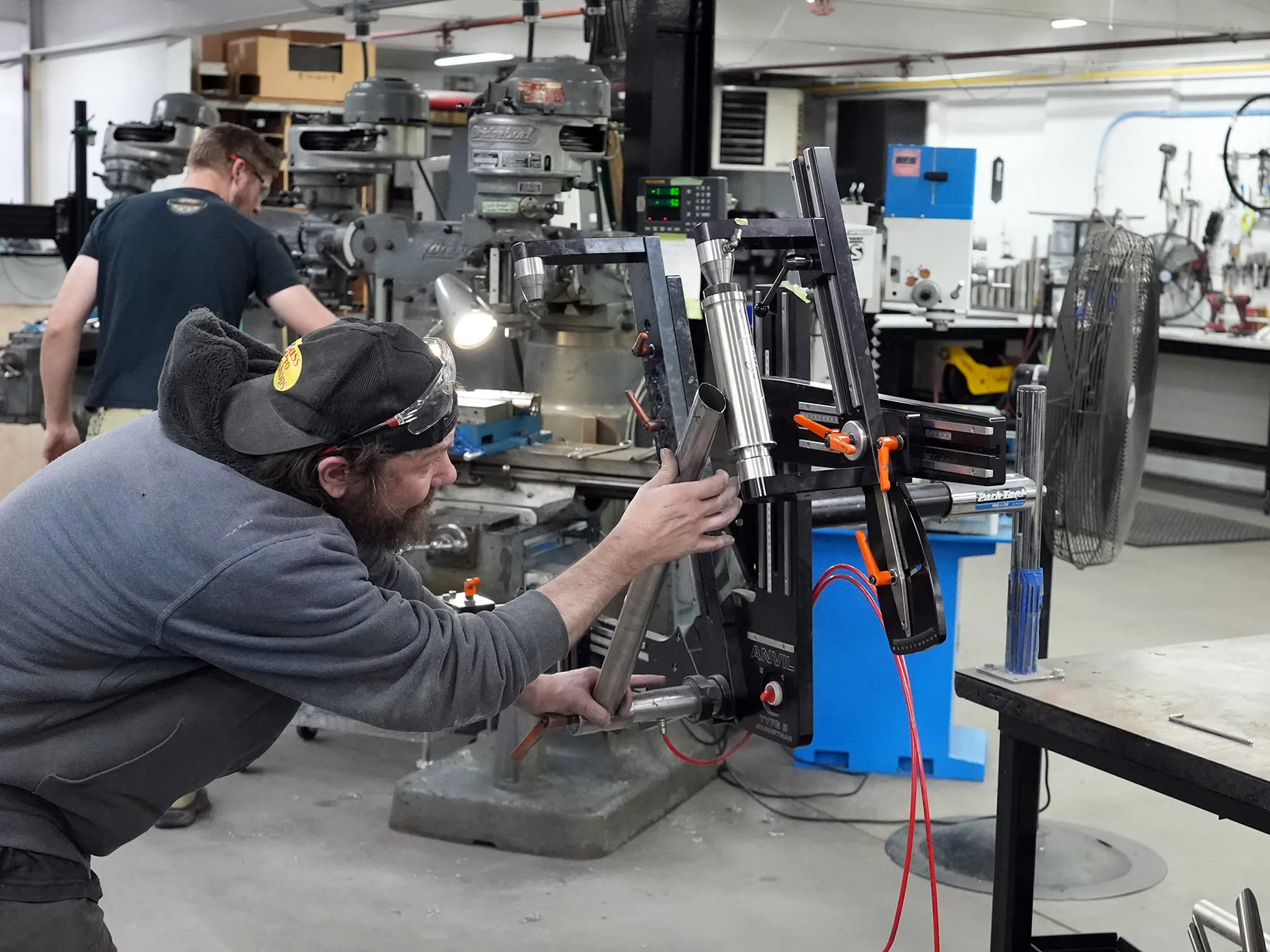
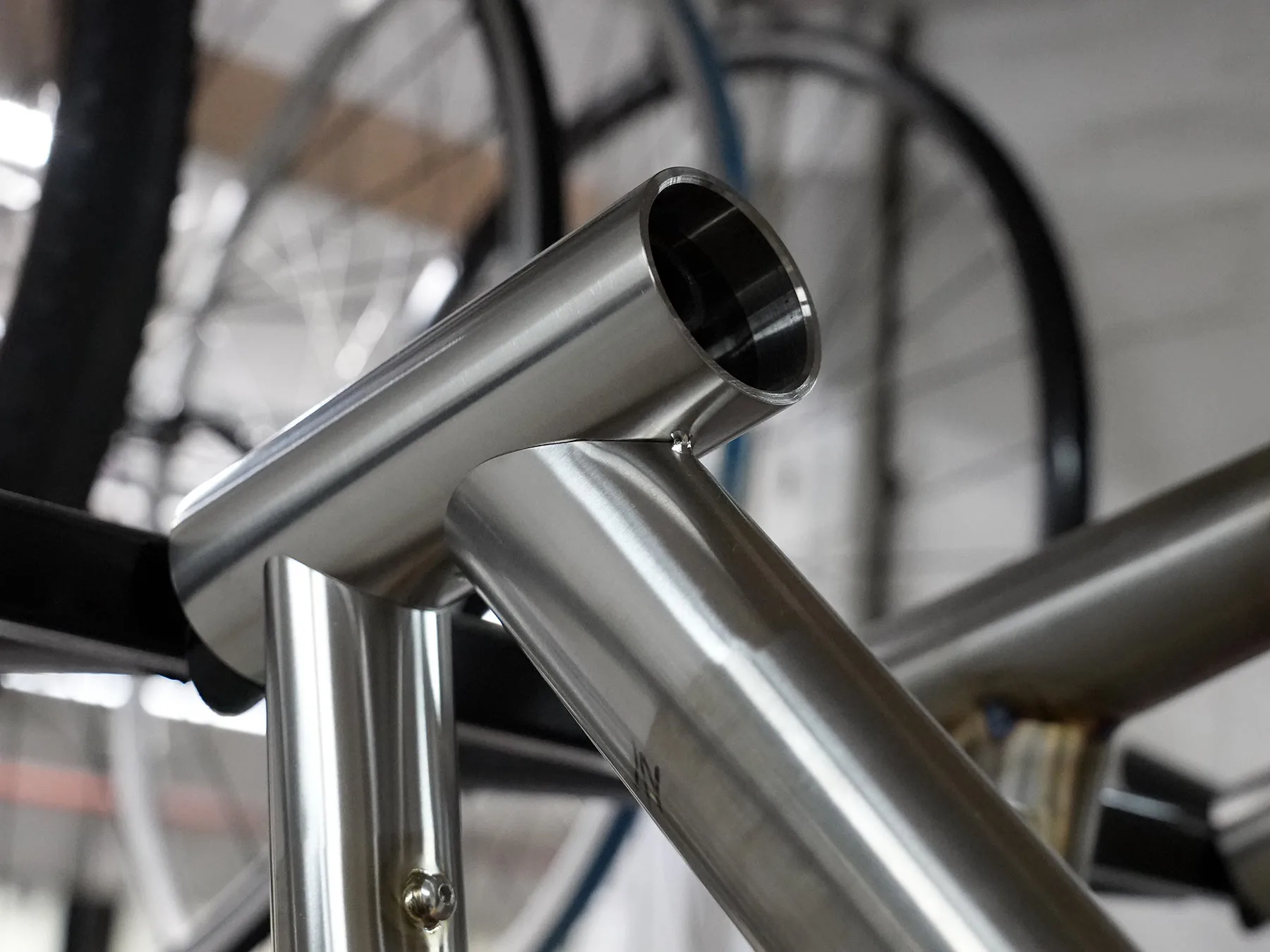
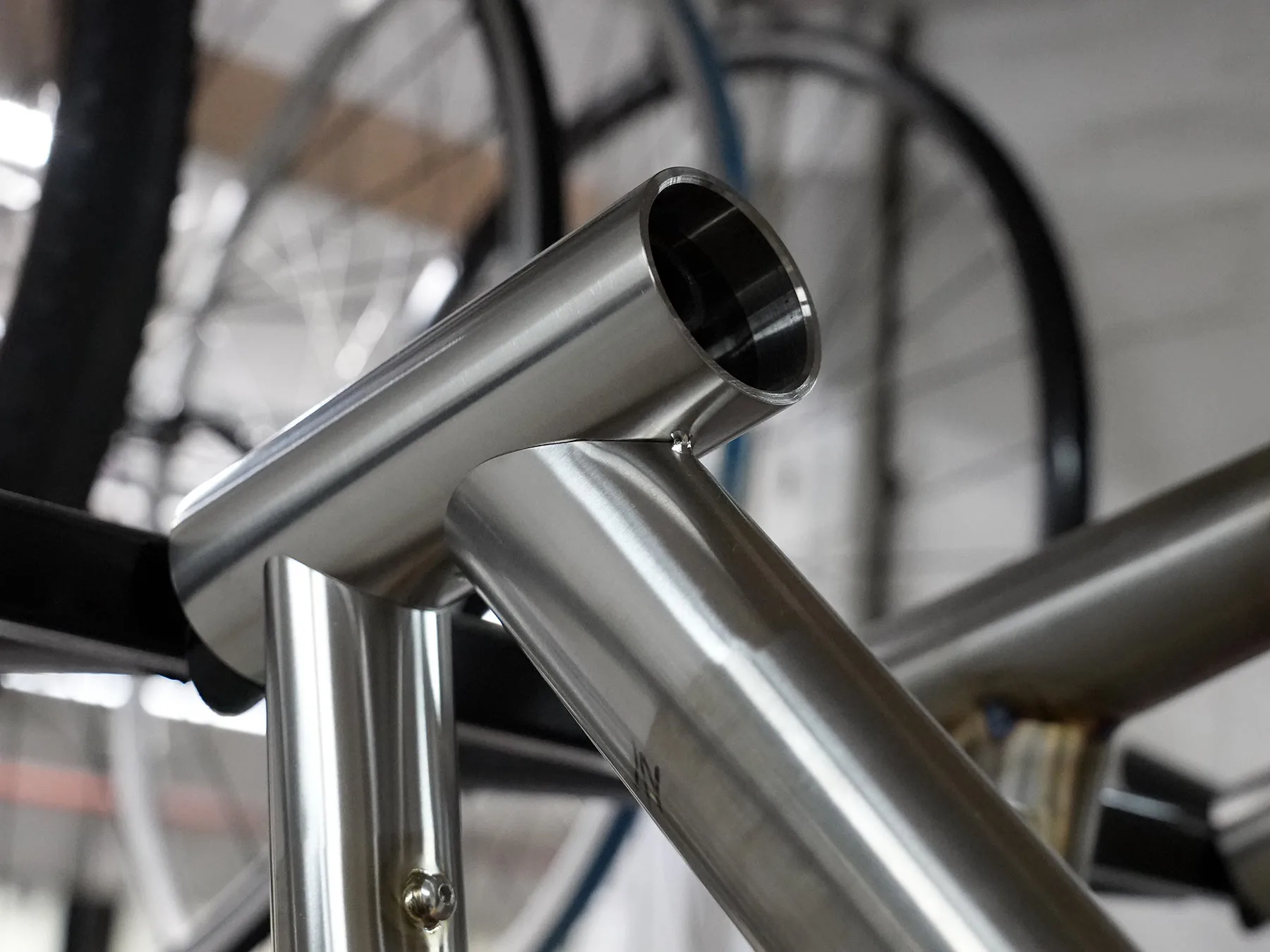
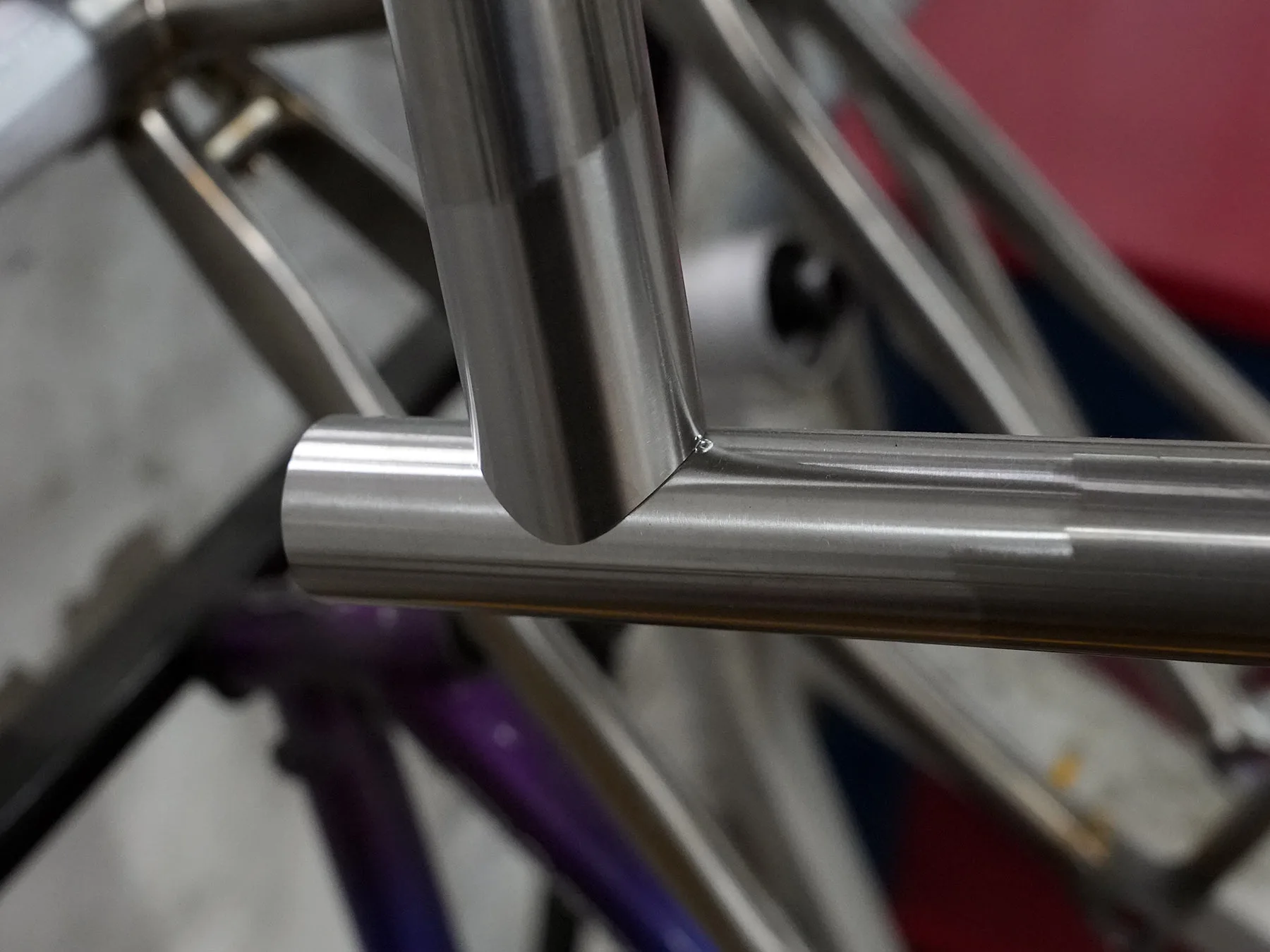
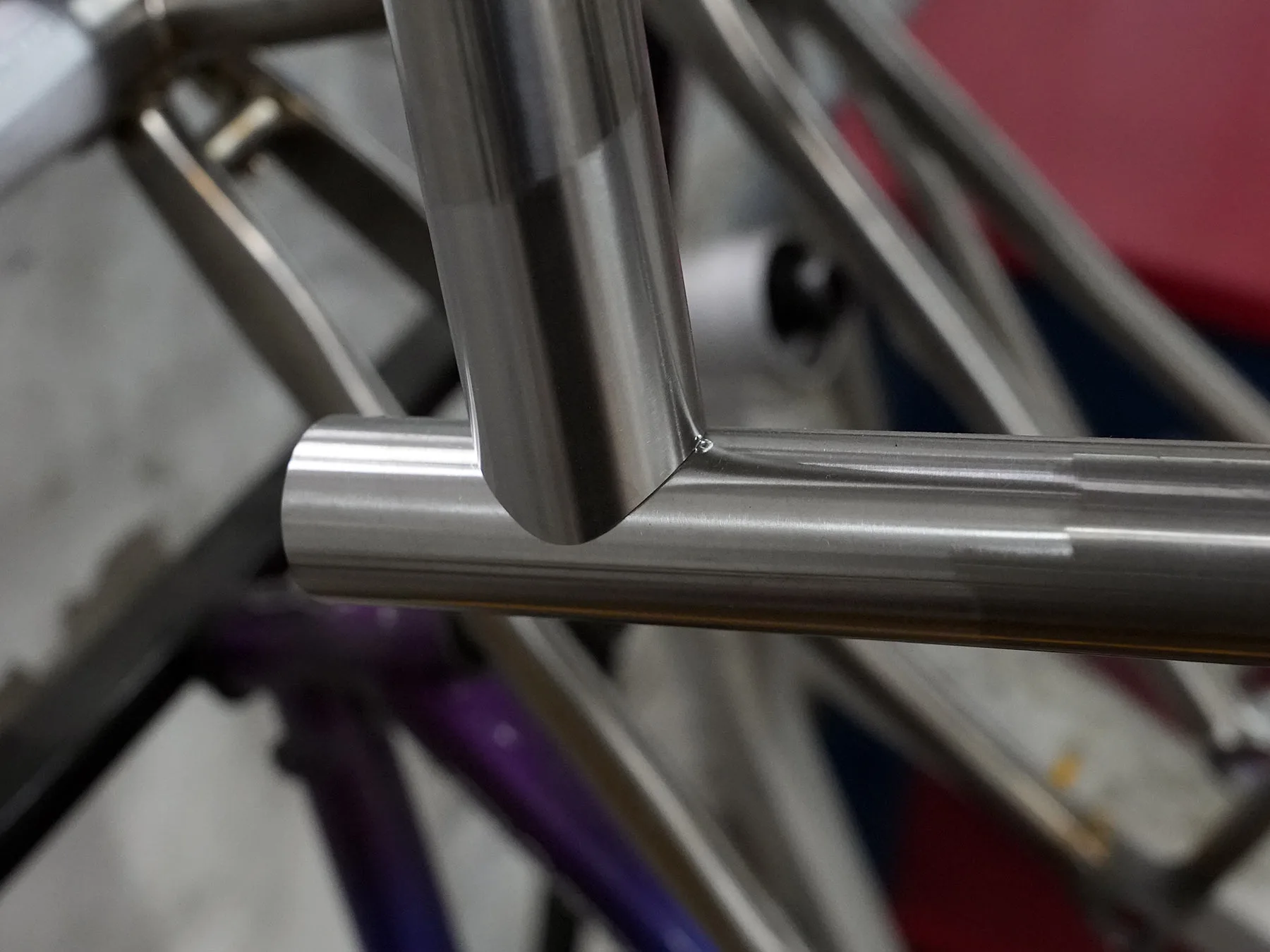
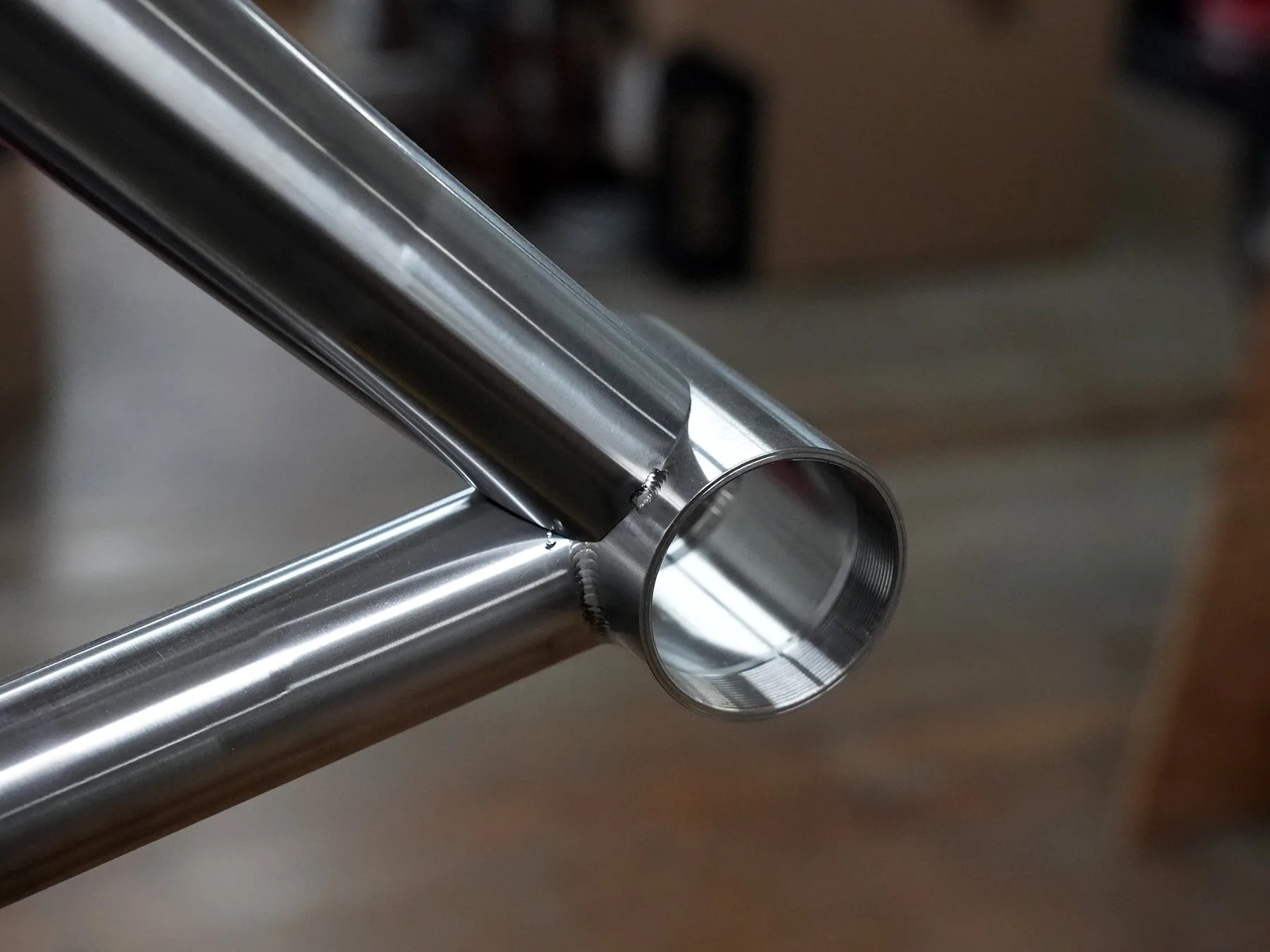
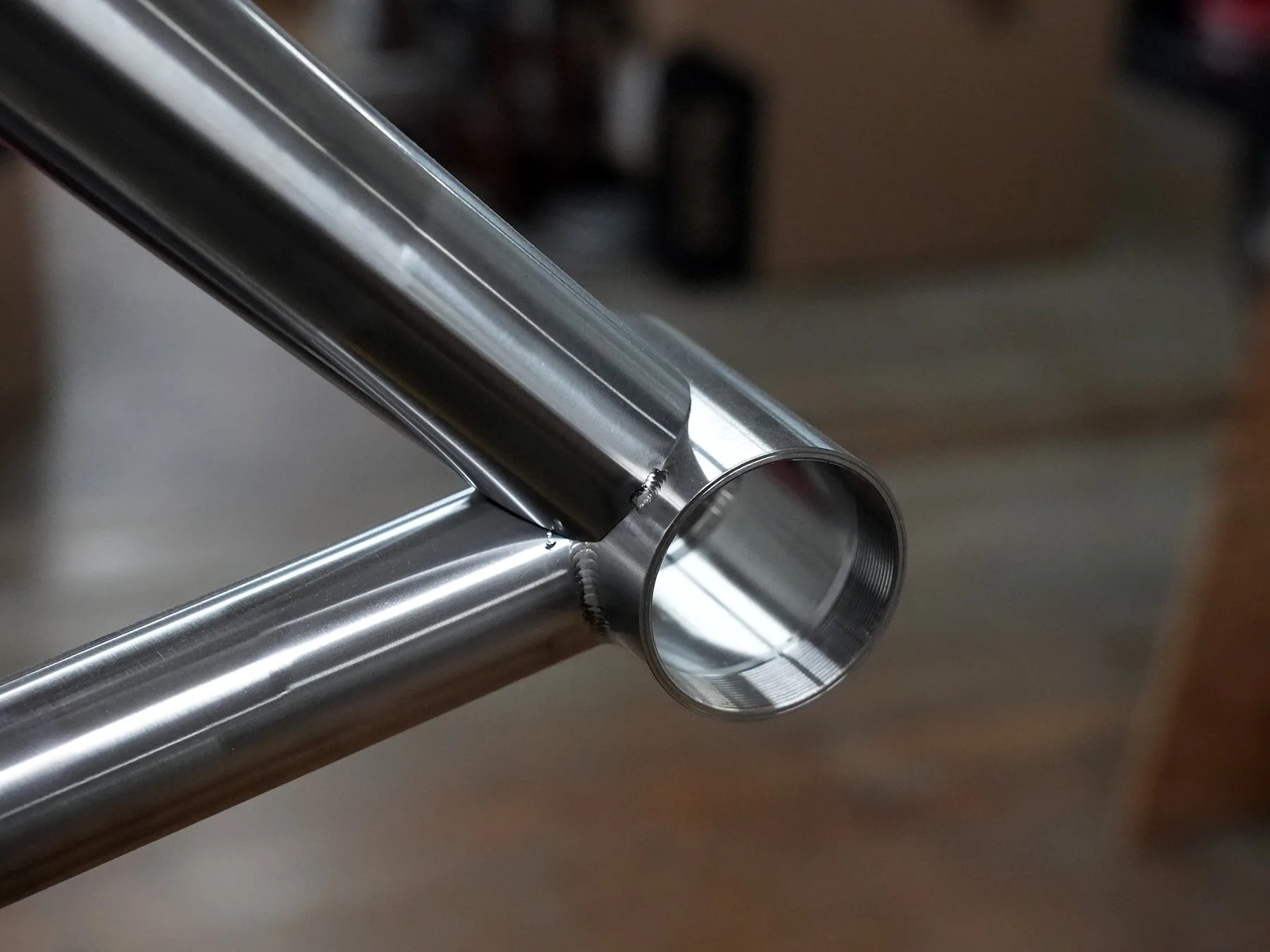
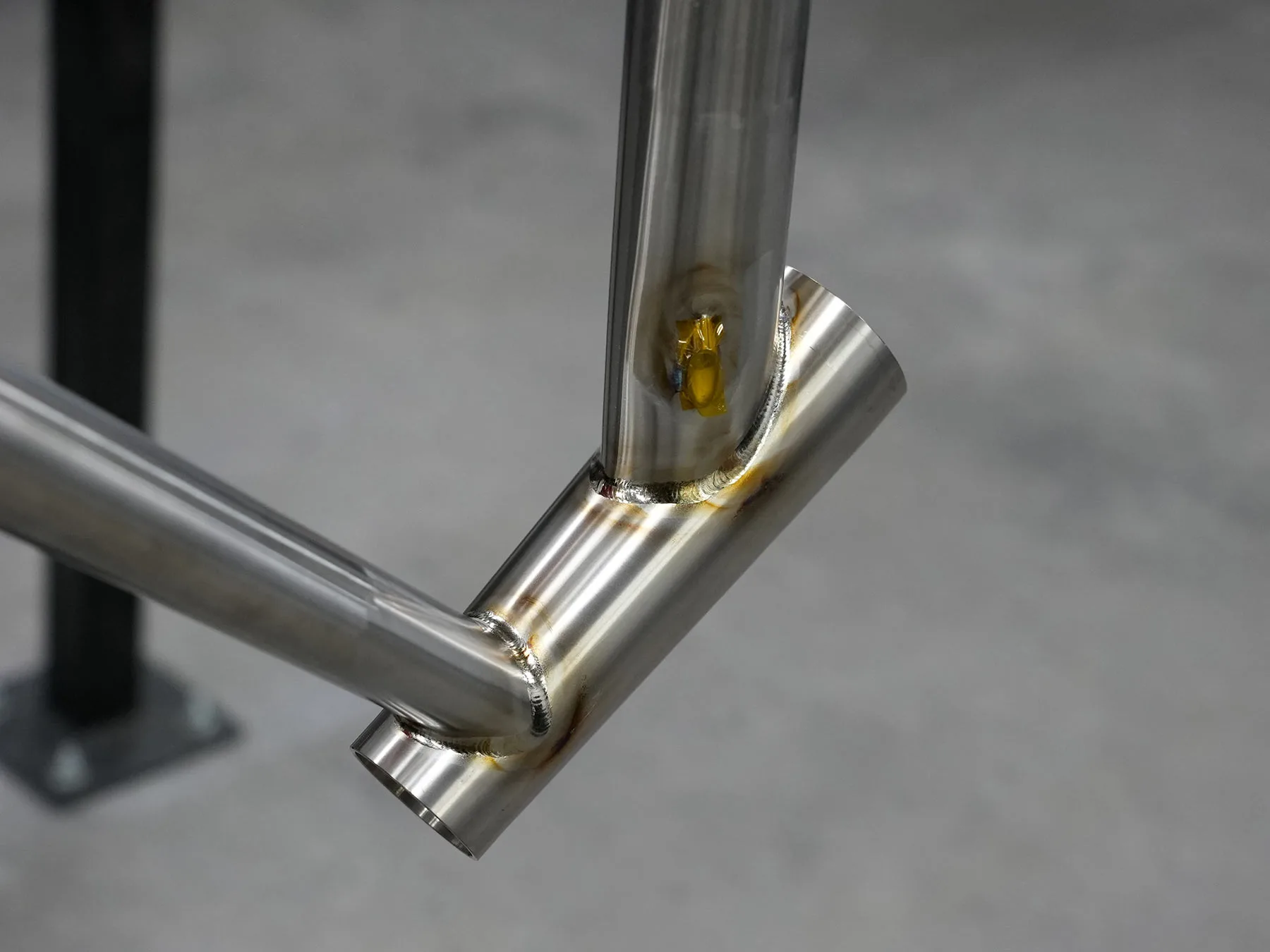
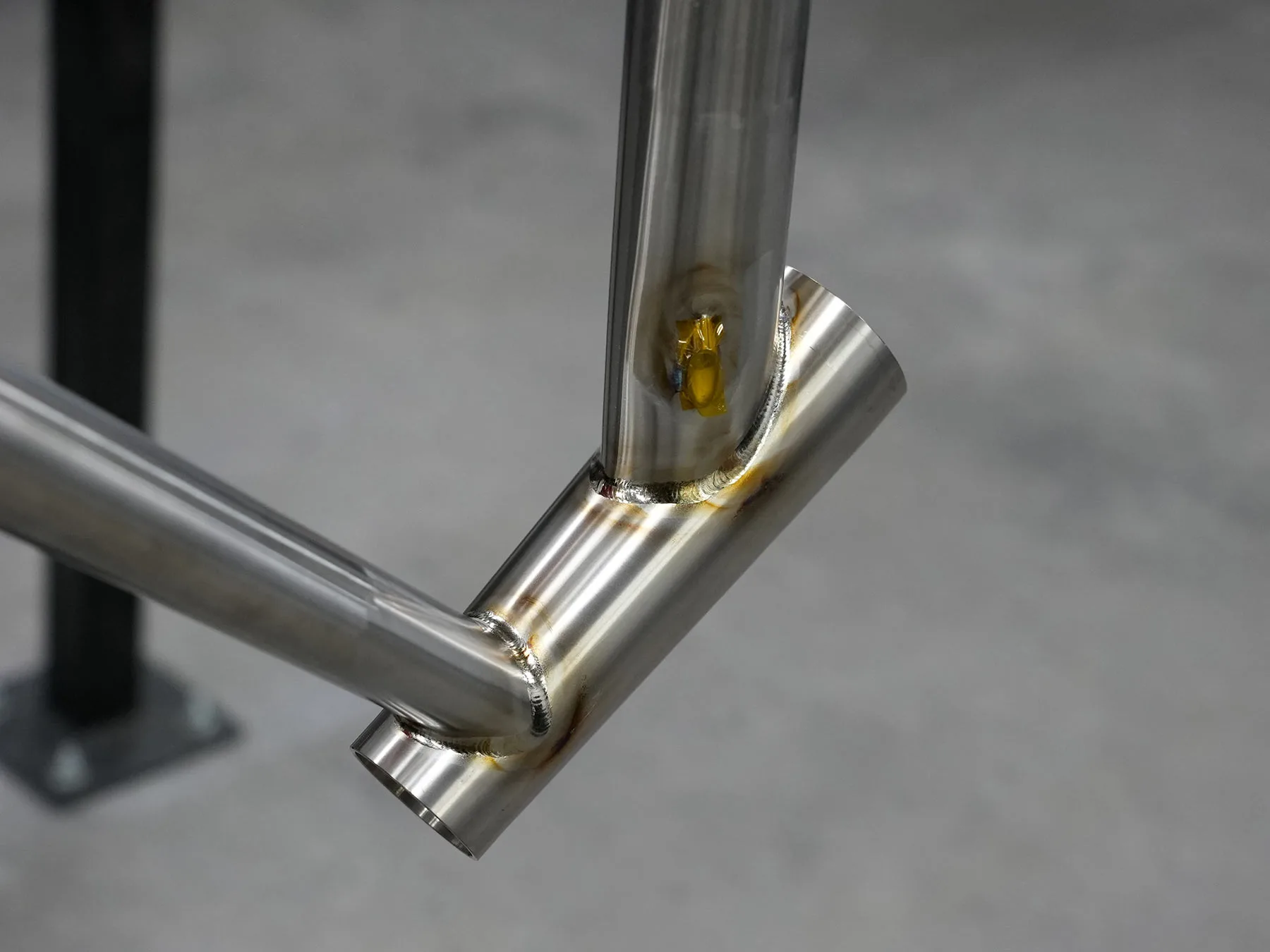
Principal tubes are tacked, then checked for alignment between every step.
They tack within the jig, however don’t weld in it, as a result of as soon as it’s tacked, it’ll need to pull in a single path or one other. So that they’ll mark the place they need to begin and end the weld in order that they’ll actually weld it into alignment. The result’s a greater ultimate product that doesn’t require guide manipulation after it’s completed.
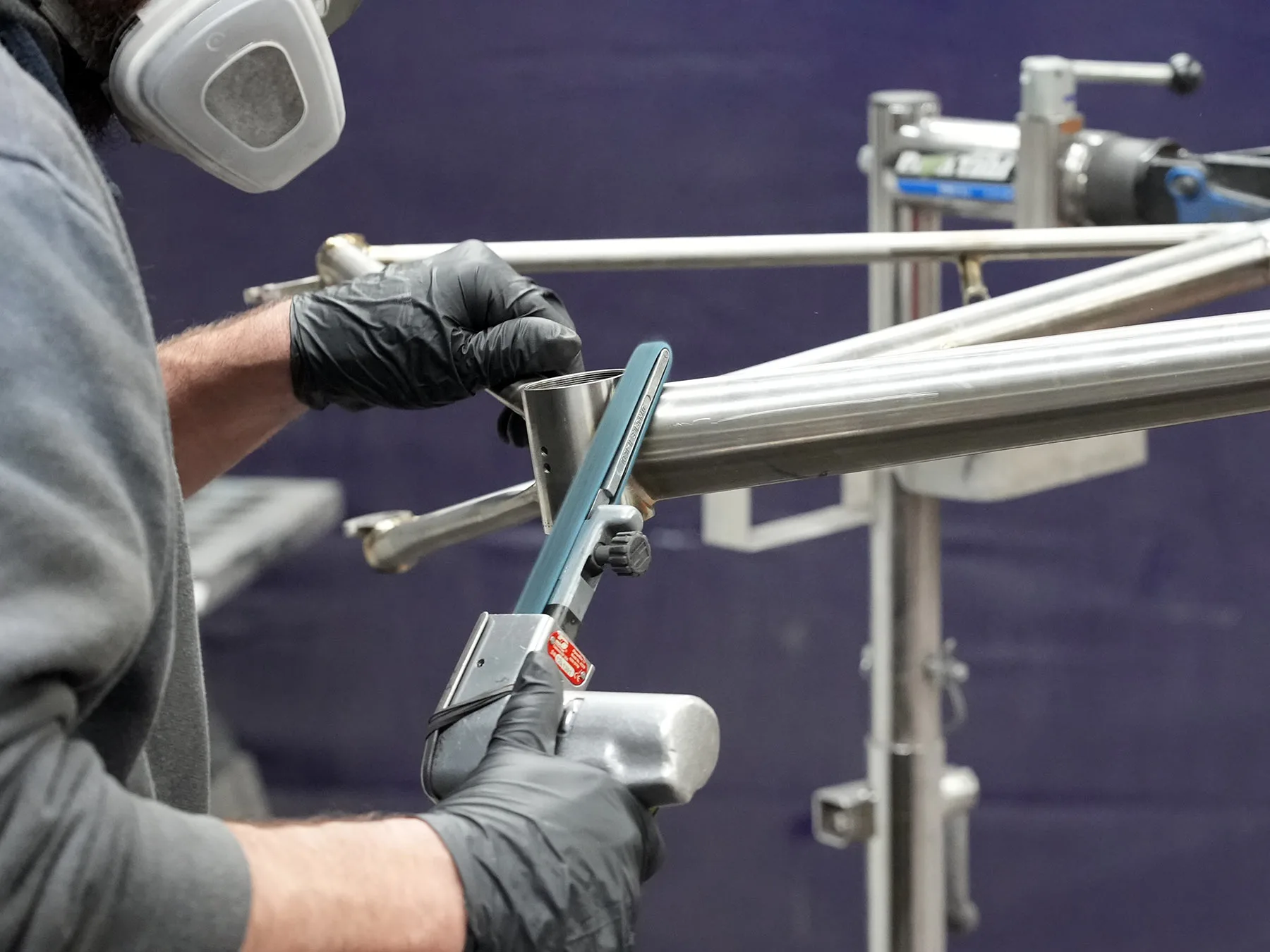
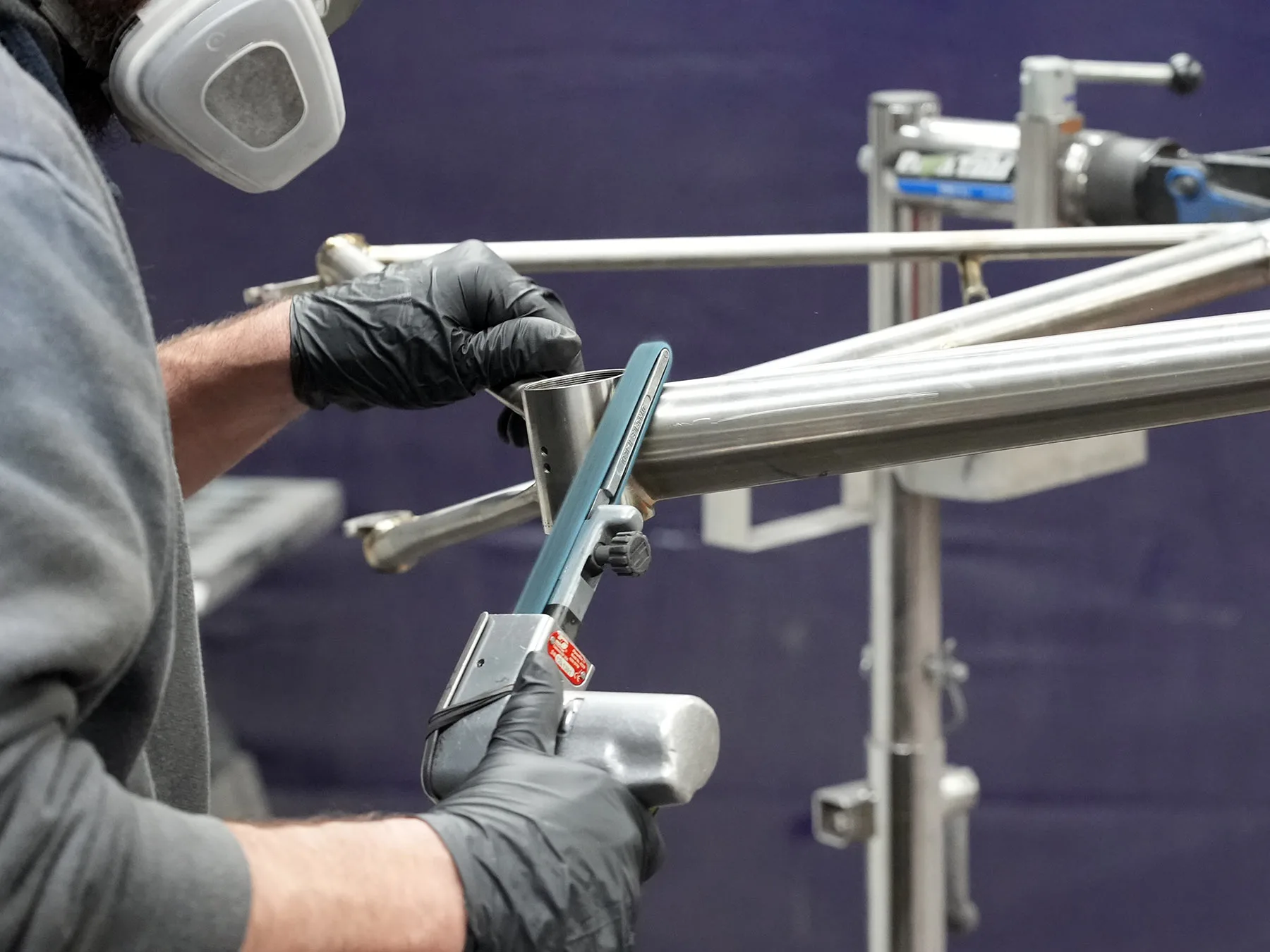
All submitting is completed in a separate room in order that there’s no mud, and it’s cleaned between every step. Every body is QC’d by somebody apart from the welder.
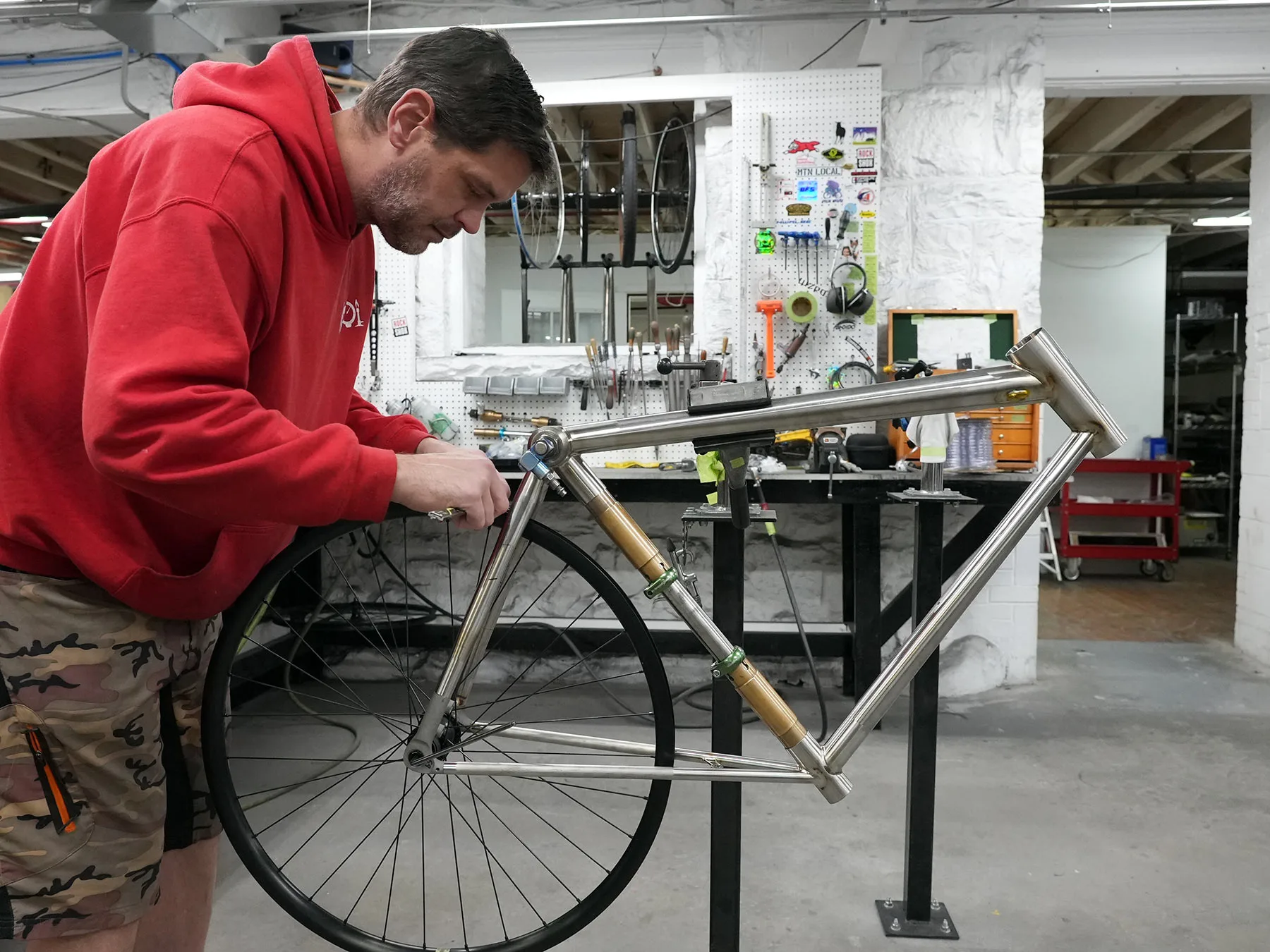
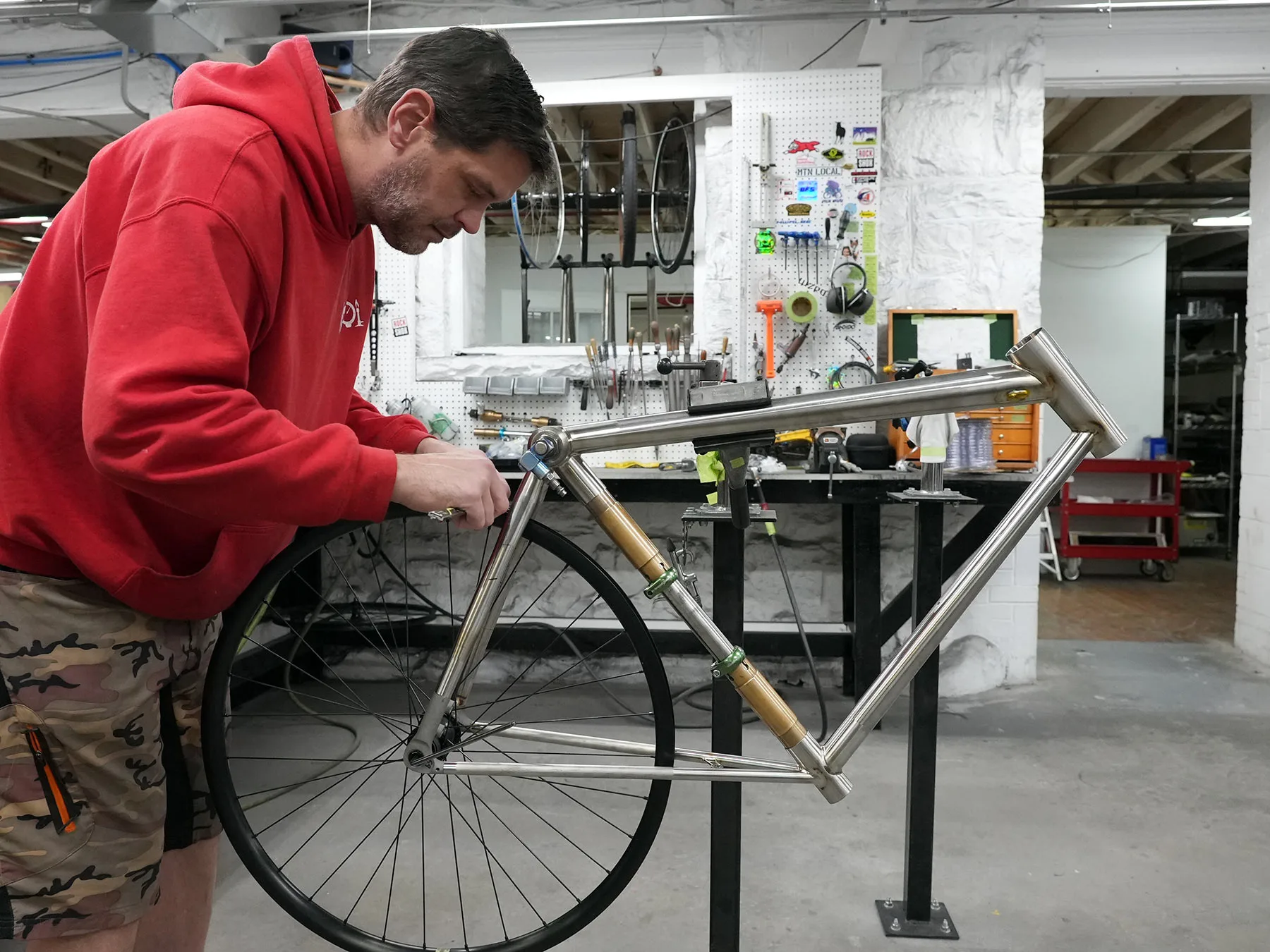
After ultimate alignment examine, it will get reamed, confronted, and the holes bored for cable ports, bottle cages, and so forth. Full bikes are then constructed, and every little thing’s utterly lined in bubble wrap and boxed up for supply.
Extra Cool Stuff
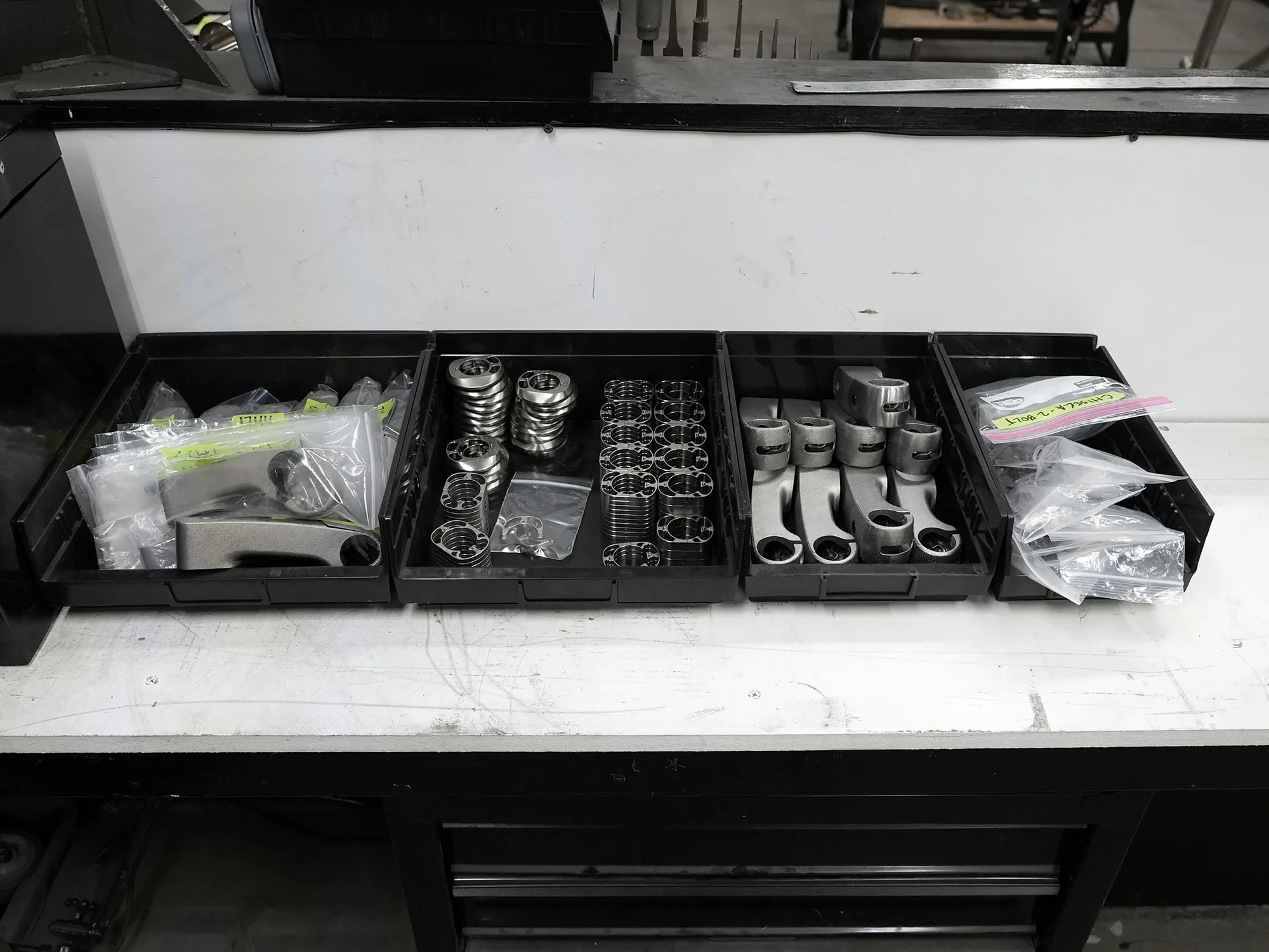
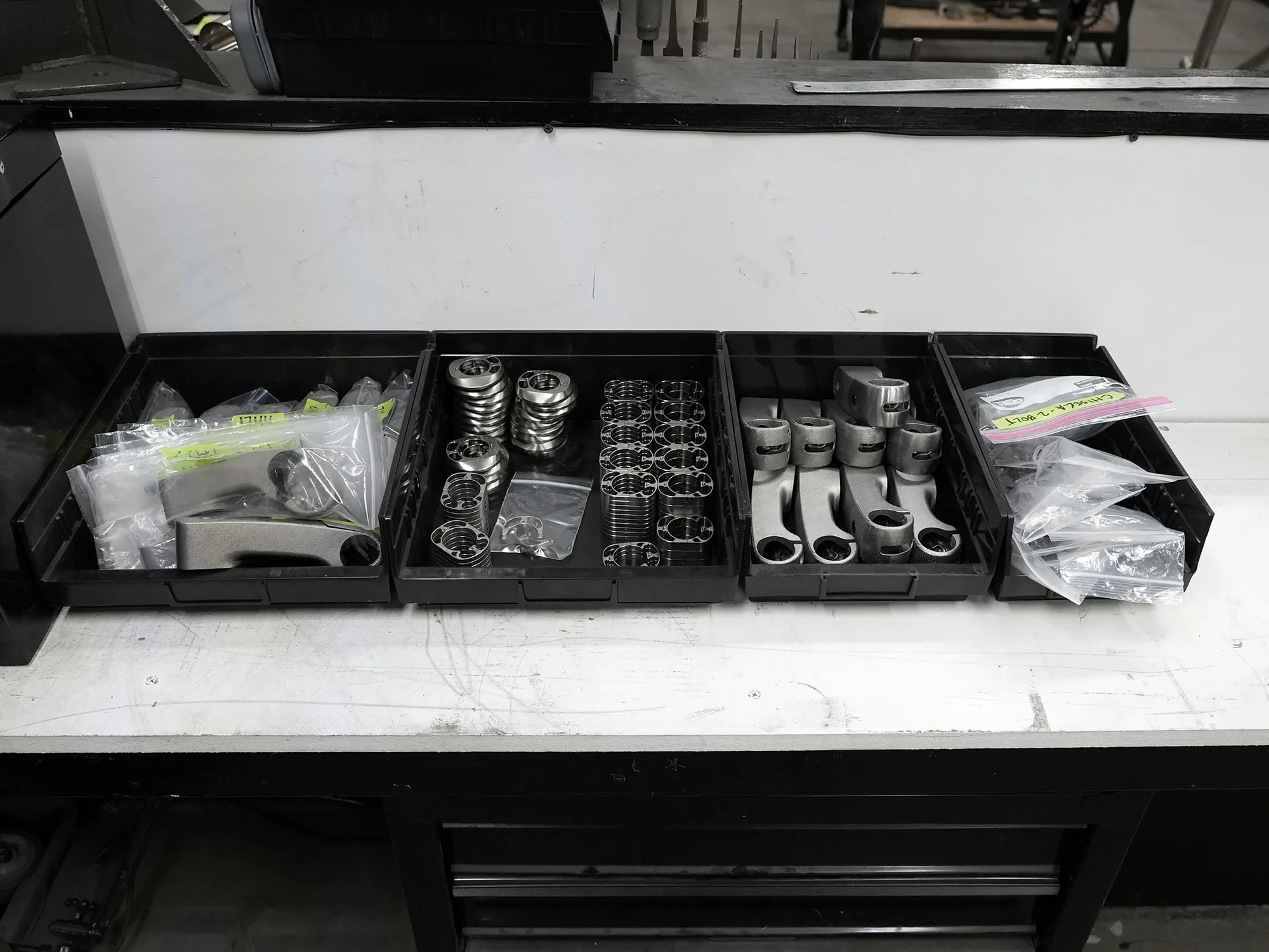
No.22’s 3D-printed stems are paired with shape-matched headset spacers with ports for inner cable routing. These give the entire bike a particularly glossy, built-in look (examine my evaluation of the Nice Divide for plenty of photographs)
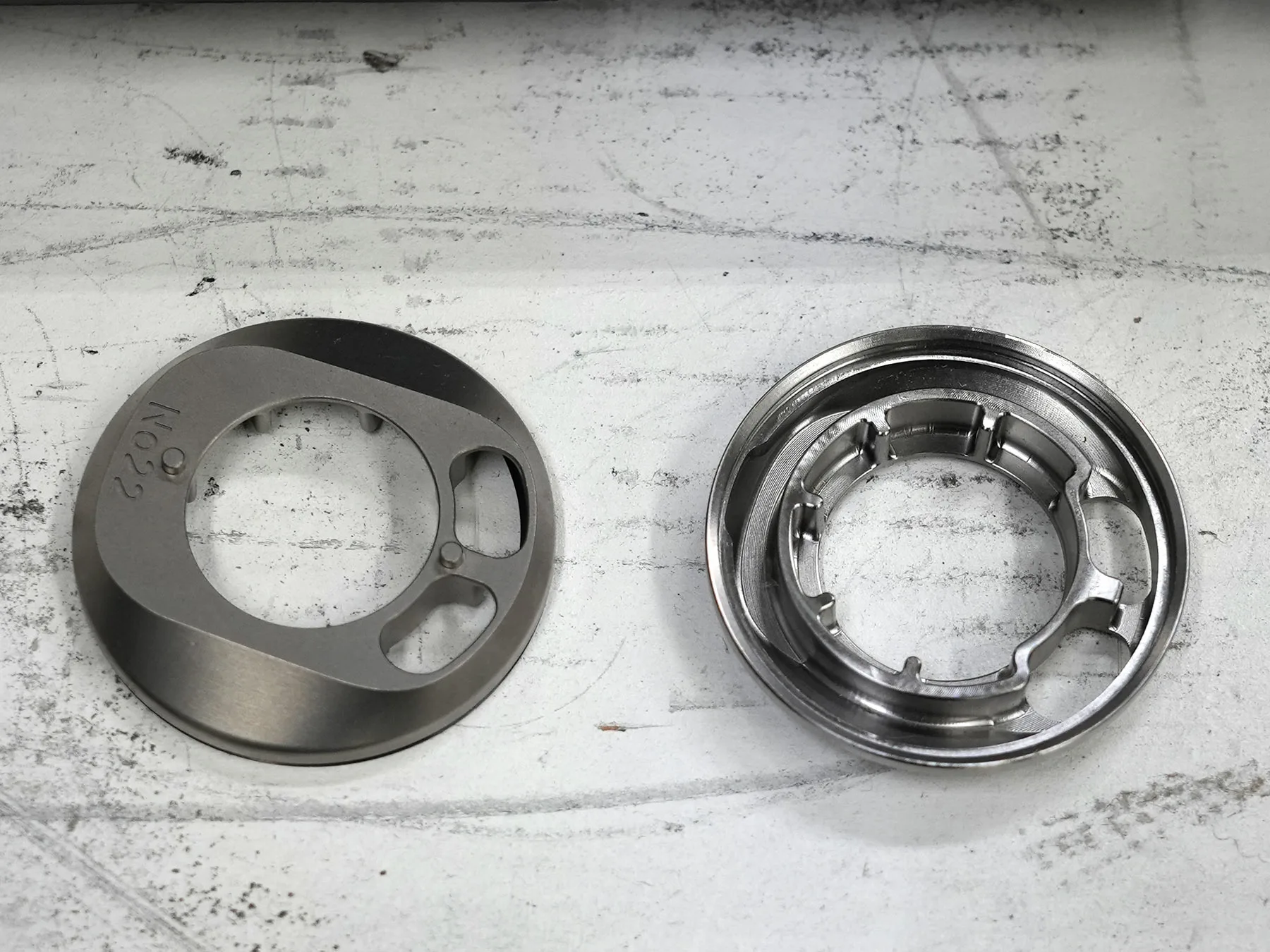
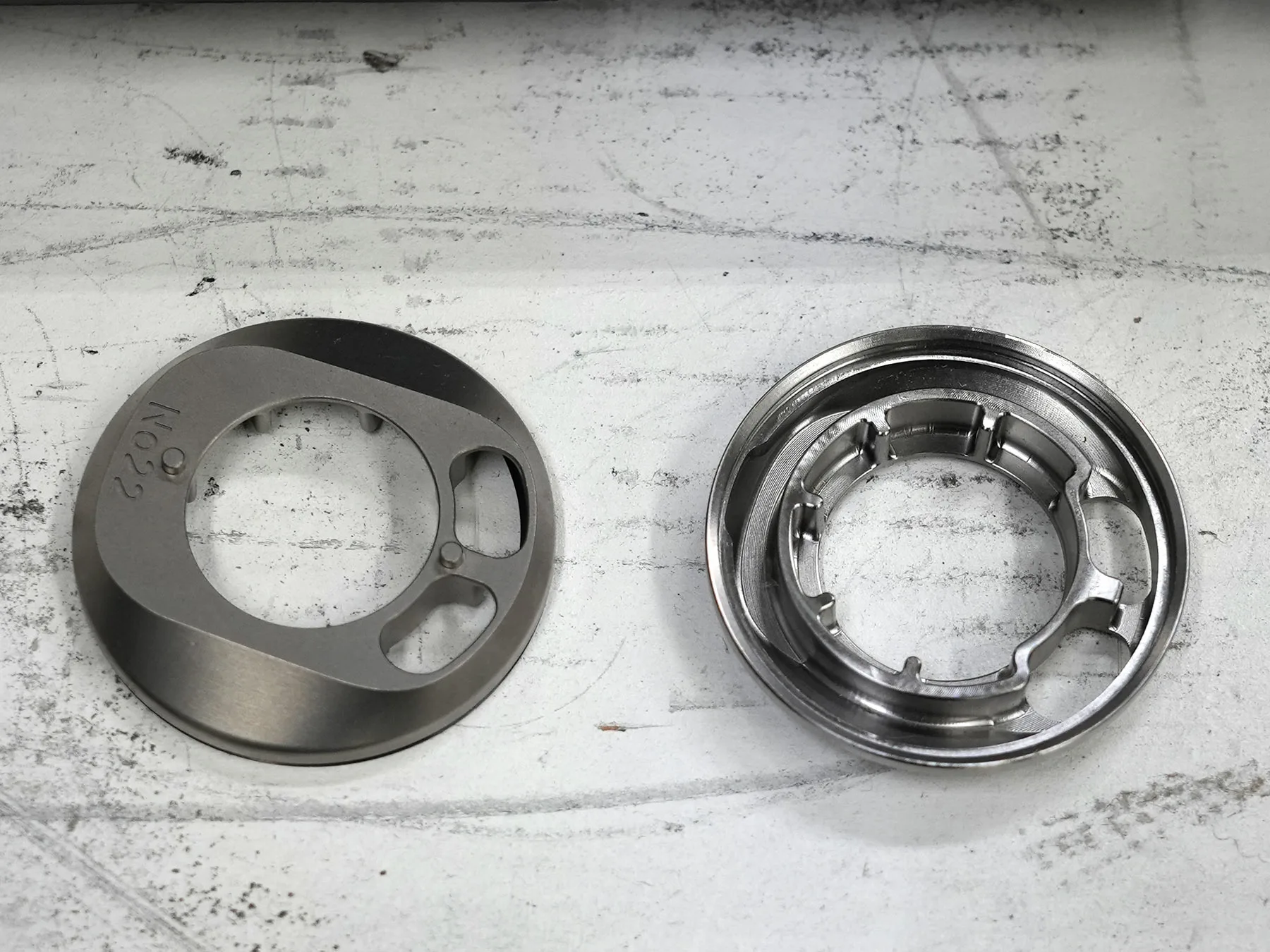
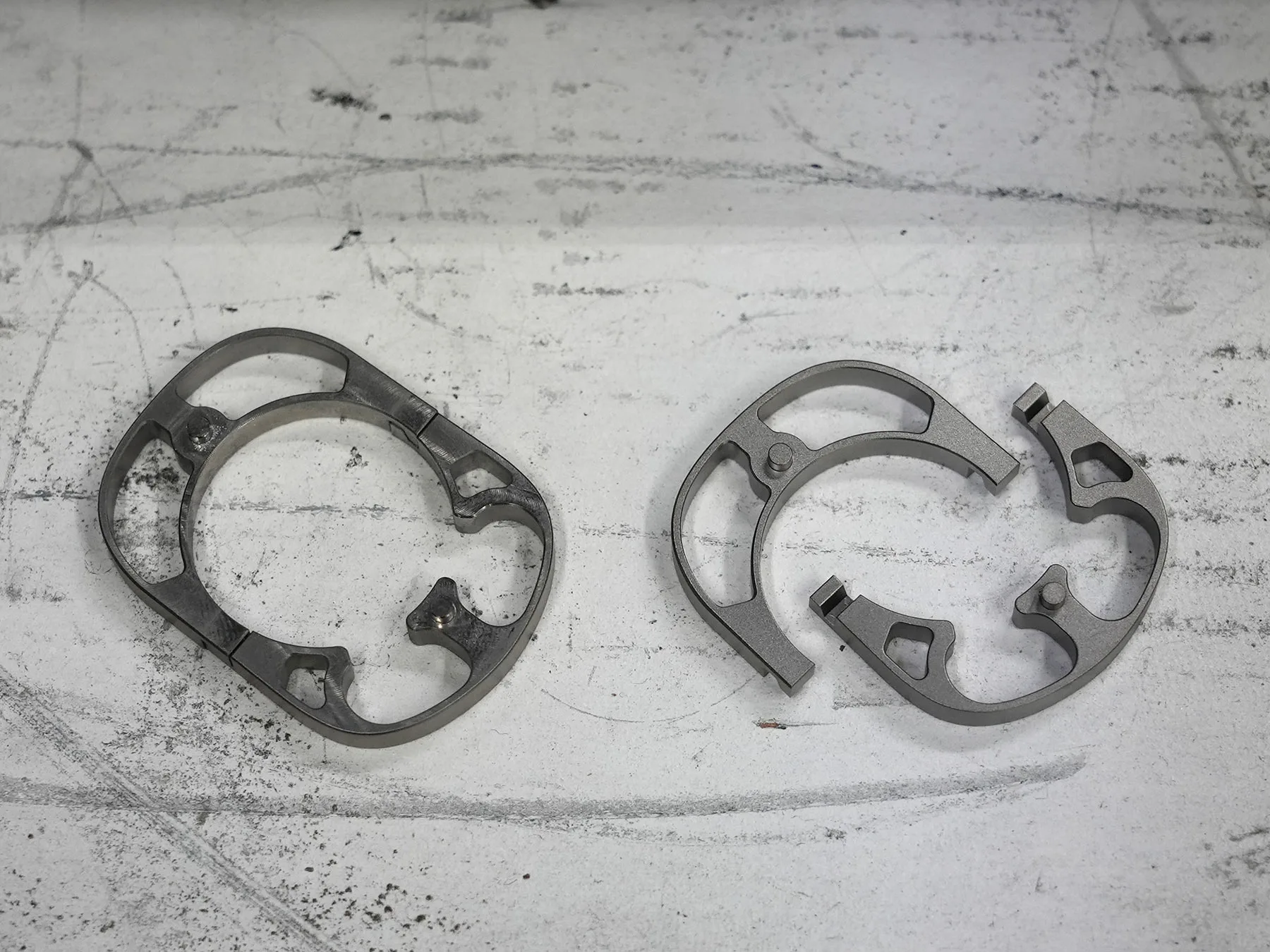
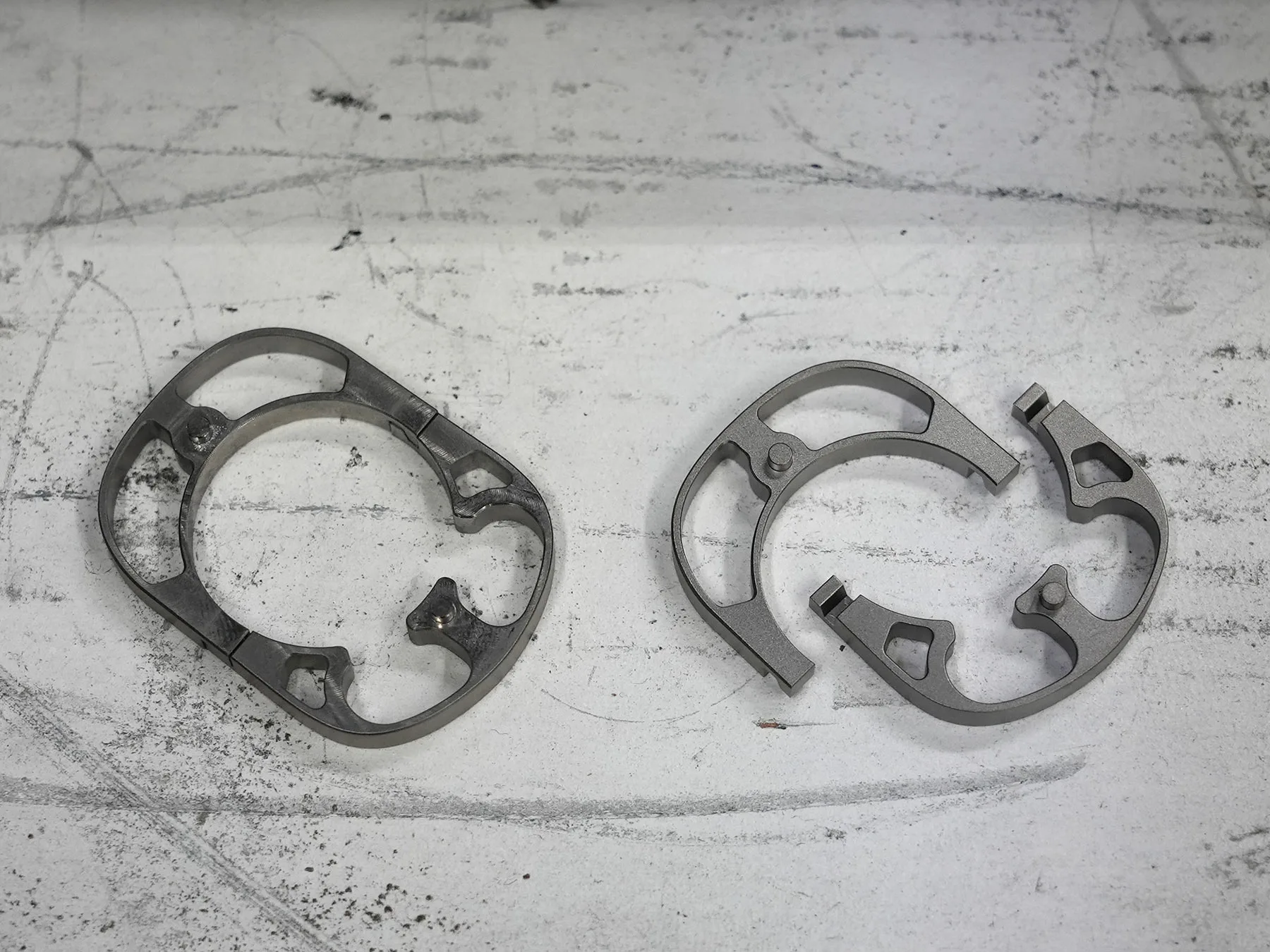
Whereas the headset cap is one piece and would require a brake line removing to alter, the spacers are segmented and keyed so you can also make match changes…so, possibly go for a barely taller fork steerer if you happen to’re undecided the place you need your stack top to finish up. You may all the time minimize it down…
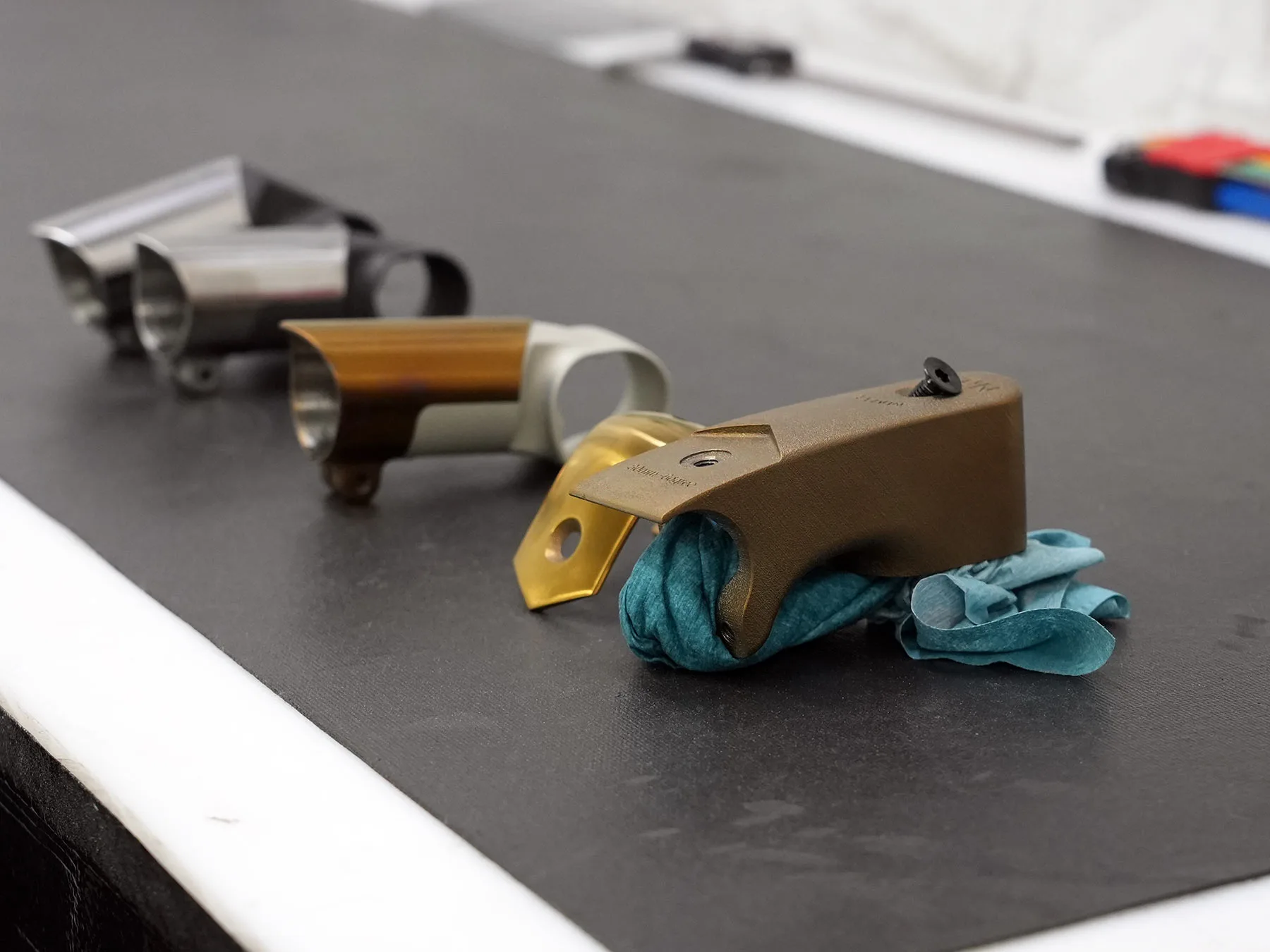
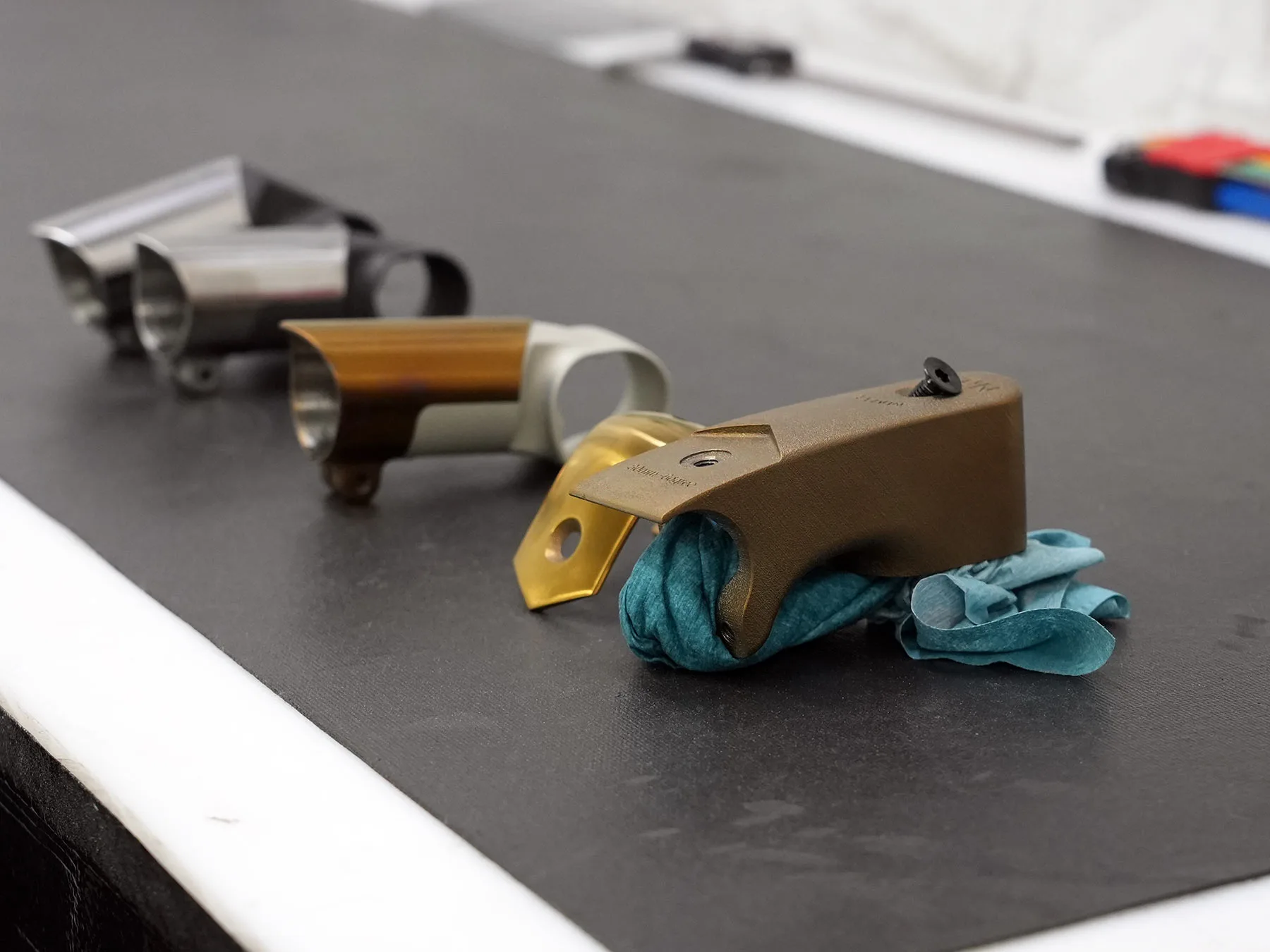


…however you possibly can’t add steerer size again. The No.22 stem has a strong design, performing as prime cap, too. It may be anodized to match the remainder of the bike, too, as can seatmast toppers for his or her bikes with the carbon seat tube.
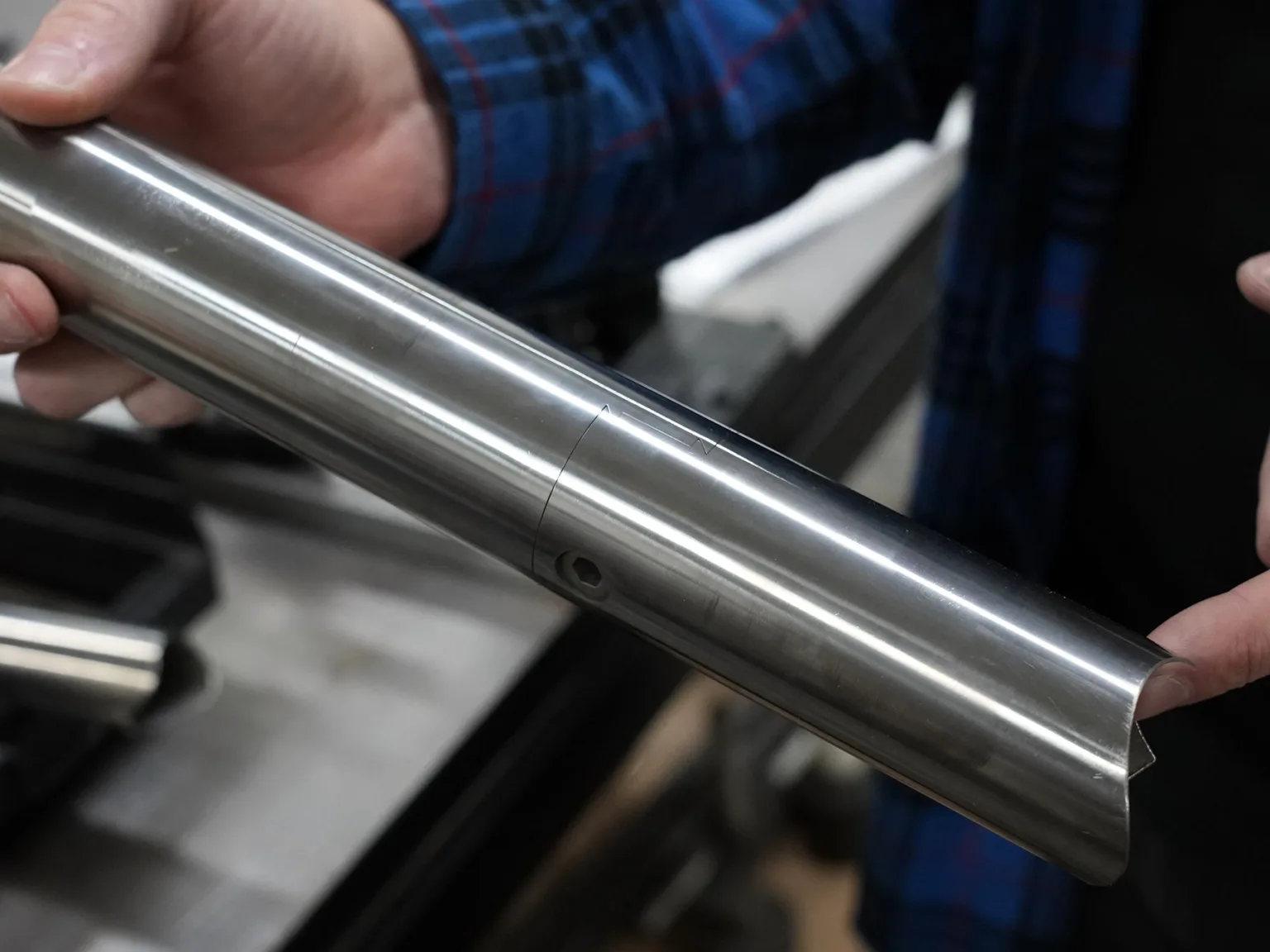
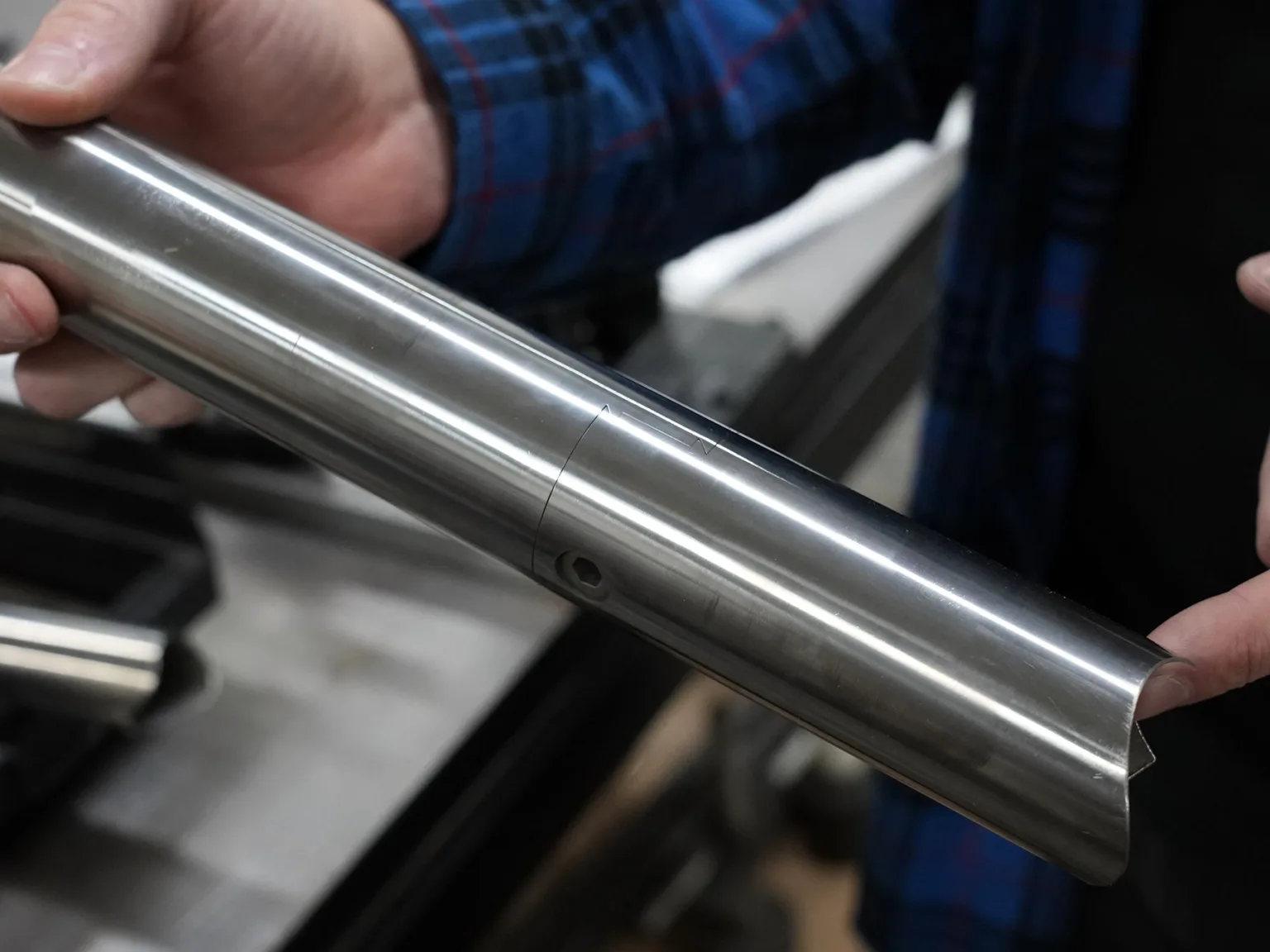
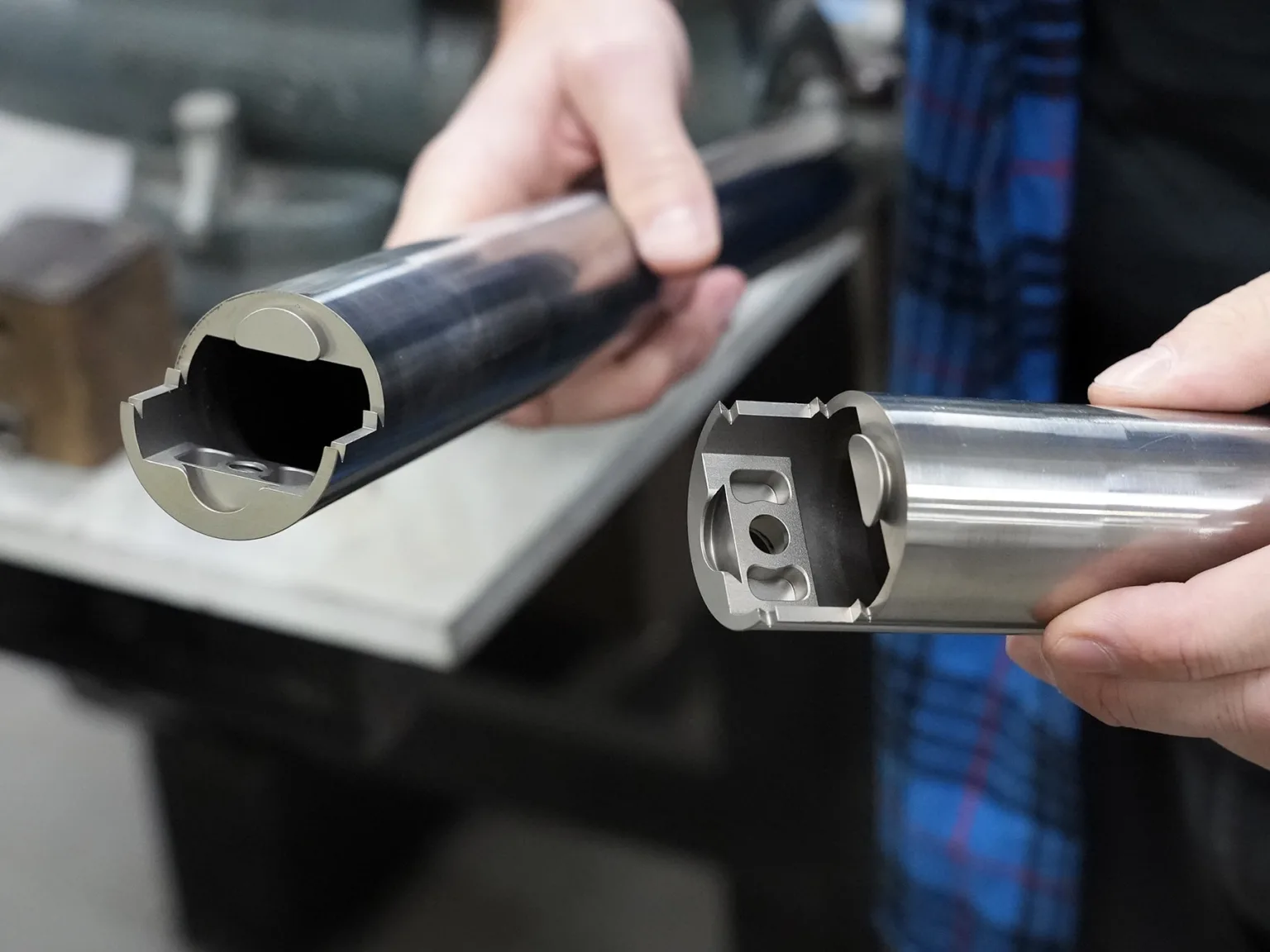
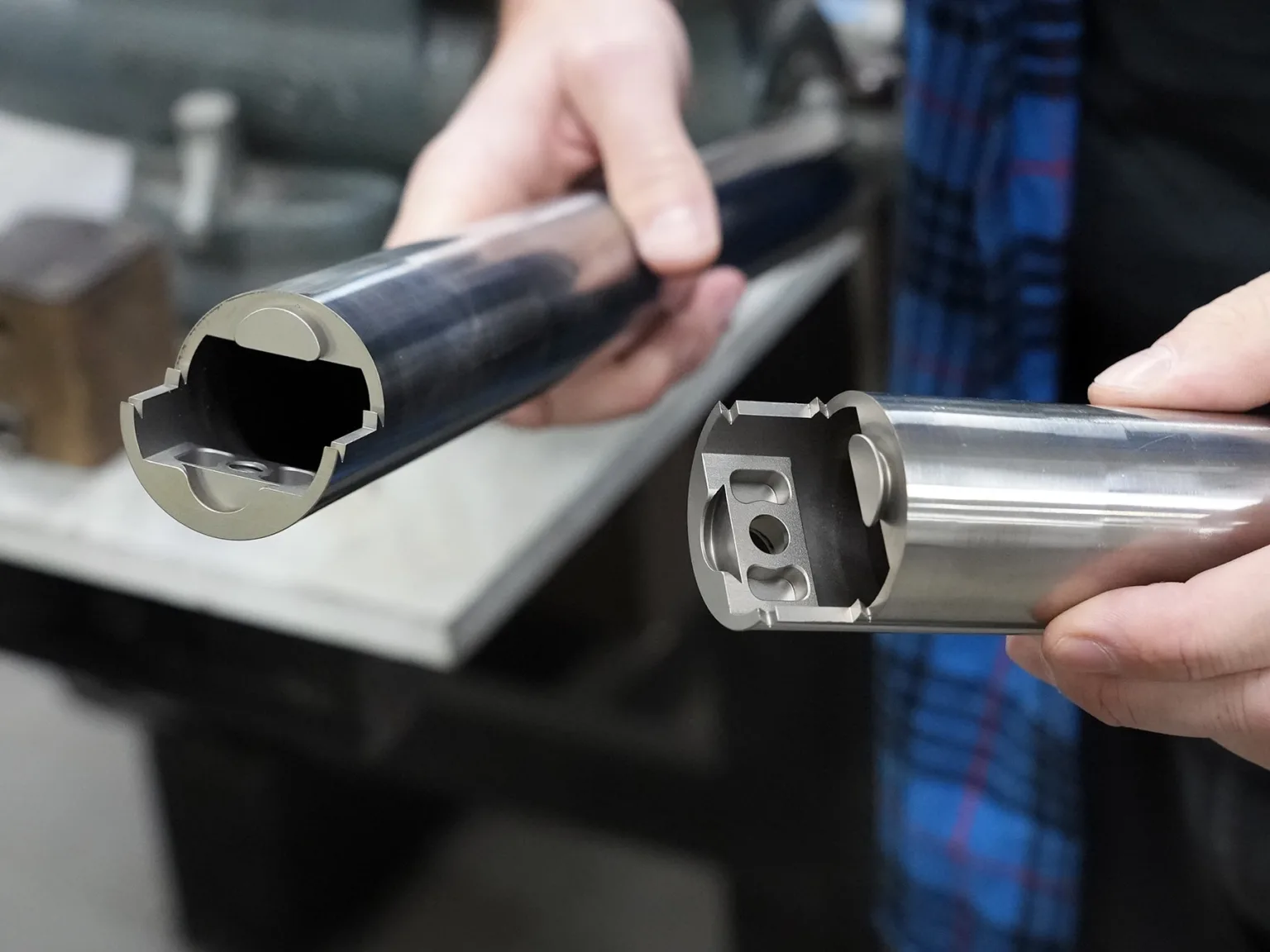
Additionally they supply breakaway tubes with a keyed design that allows you to extra simply journey along with your bike in a smaller case.
Enormous due to No.22 for internet hosting me and displaying us across the manufacturing facility. Their consideration to element and delight of their work actually reveals by means of, and their completed bikes are nothing wanting lovely. They trip very nice, too! It’s good to see a titanium model pushing the cutting-edge ahead, too. Their 3D-printed stems had been a begin, however their future Reactor aero bike takes issues to a different stage.