With the Bespoked customized bike present returning to Dresden beginning tomorrow, let’s have a look inside Actofive Cycles, who machines lovely mountain bikes within the German metropolis. We’ve been intently following Actofive for a number of years – from the event of their variable journey path to enduro bikes, to their chainrings and modular cranksets. However we additionally had the distinctive probability to get a more in-depth look backstage on one in every of our final visits to Dresden.
Try these machined aluminum gems with us, and a few uncommon up-close seems to be on the inside their machined masterpieces…
Actofive Manufacturing facility Tour: CNC-machining mountain bikes in Dresden, DE
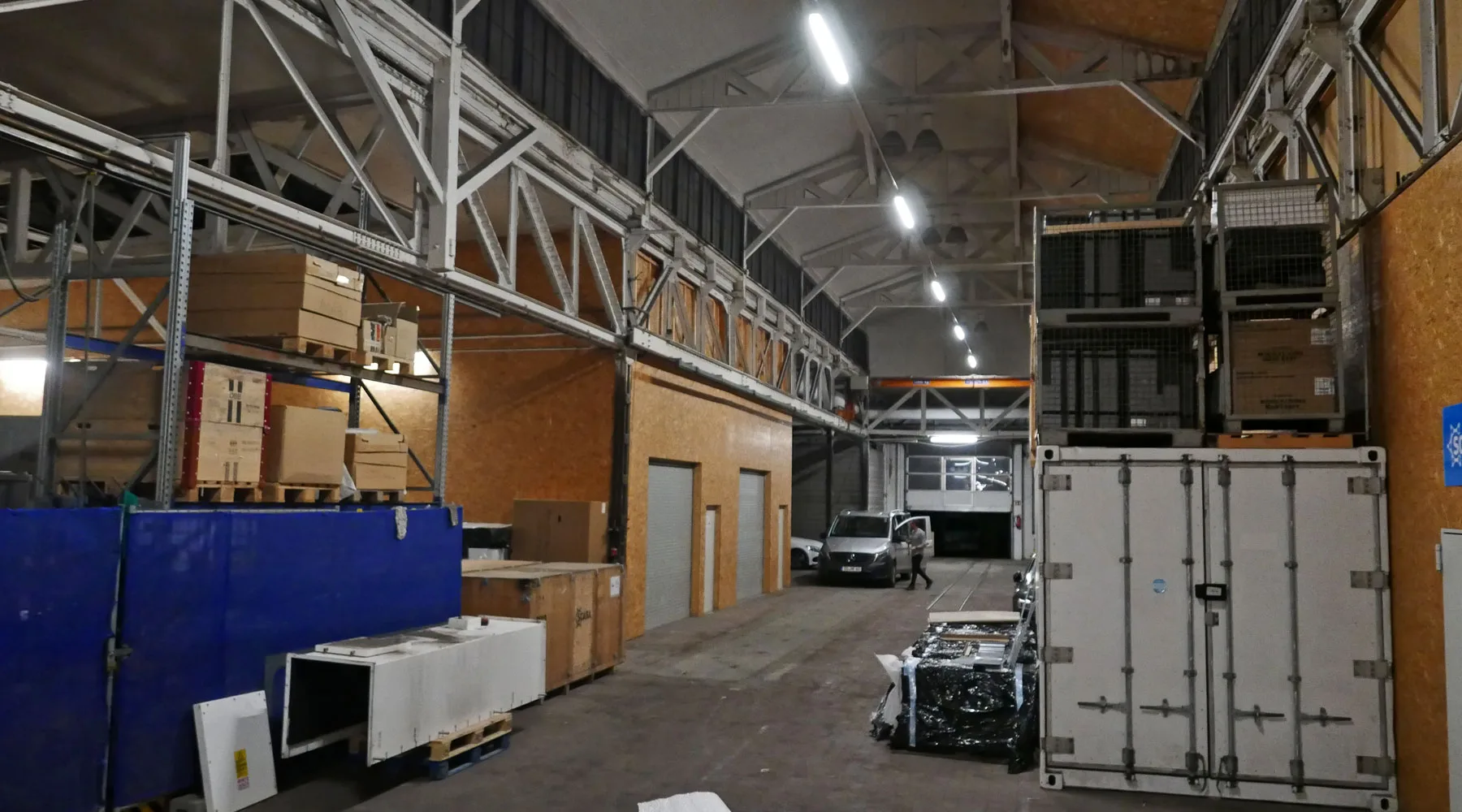
Totally CNC-machined, Actofive produces a number of the most refined mountain bikes one can find anyplace within the biking business. However they’re really fairly a small specialist producer, sitting inside an previous industrial constructing on the sting of Dresden, Germany.
Beneath, these old-school riveted metal trusses and tucked in with a number of different forms of small producers is a extra modern field hiding the fashionable capabilities of Metzner Engineering and the house of Actofive Cycles.
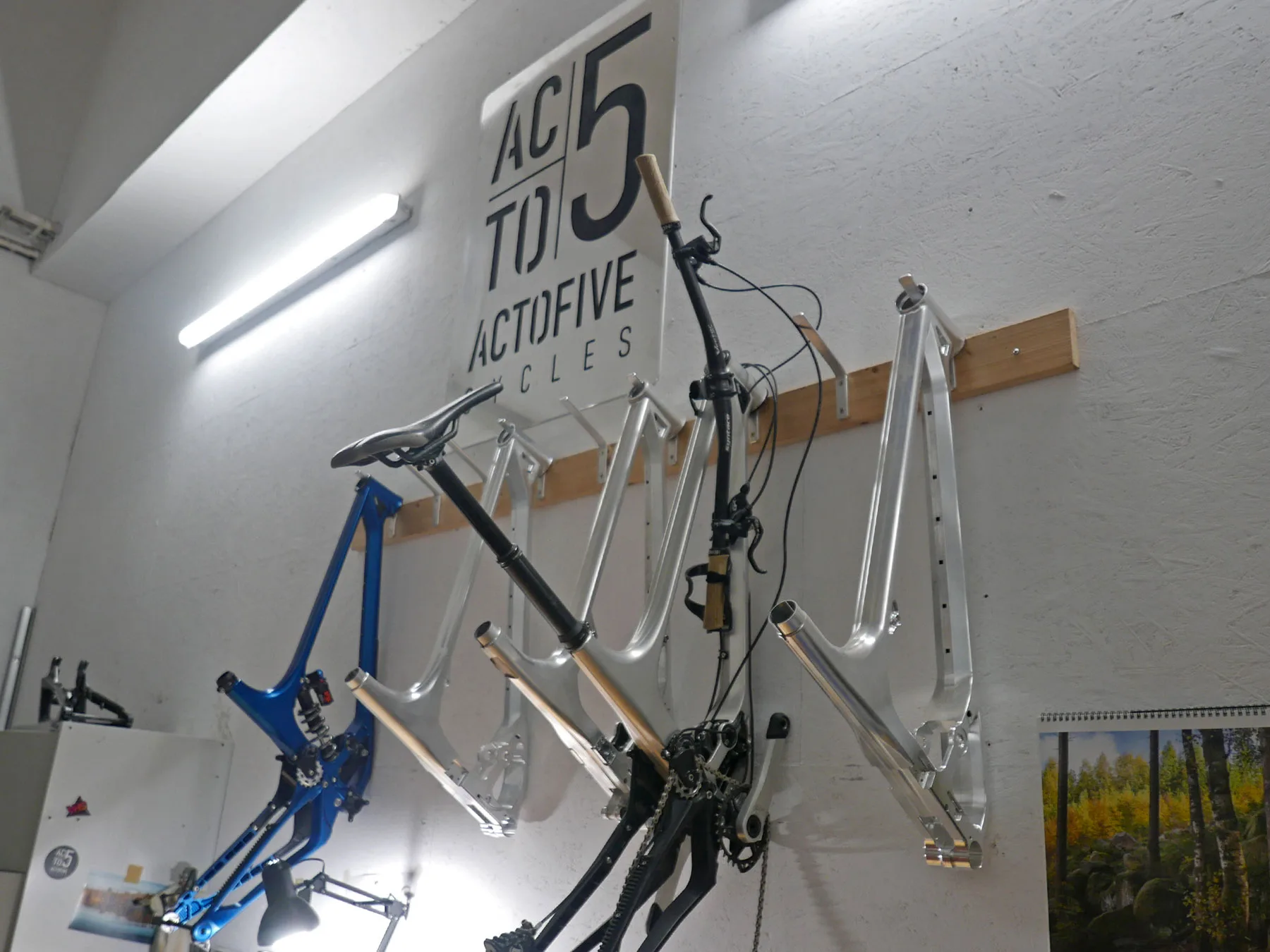
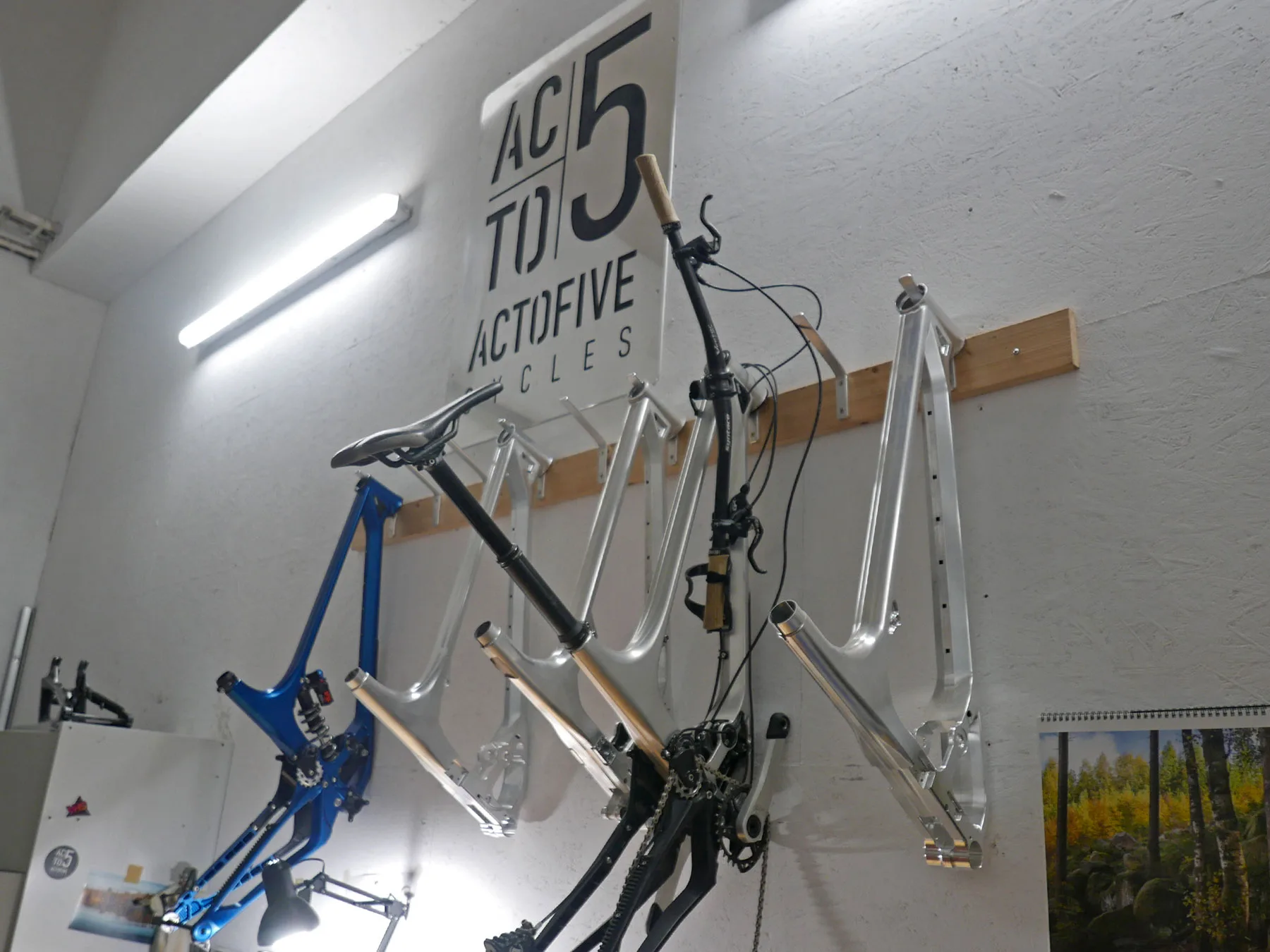
As soon as contained in the interior sanctum, a lot of Actofive fashions and improvement prototypes hold on the wall of the unassuming workshop.
Metzner Engineering: The person behind the machine
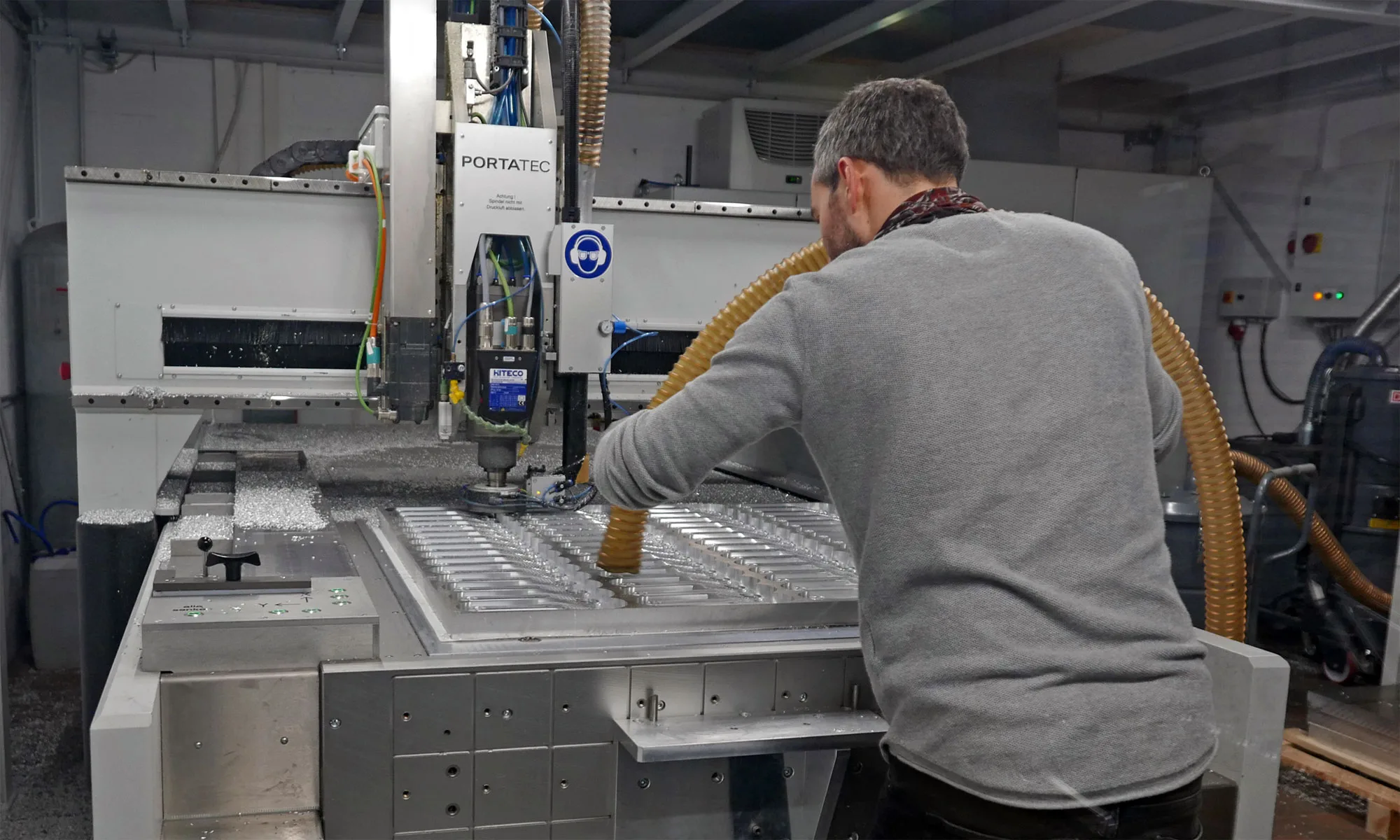
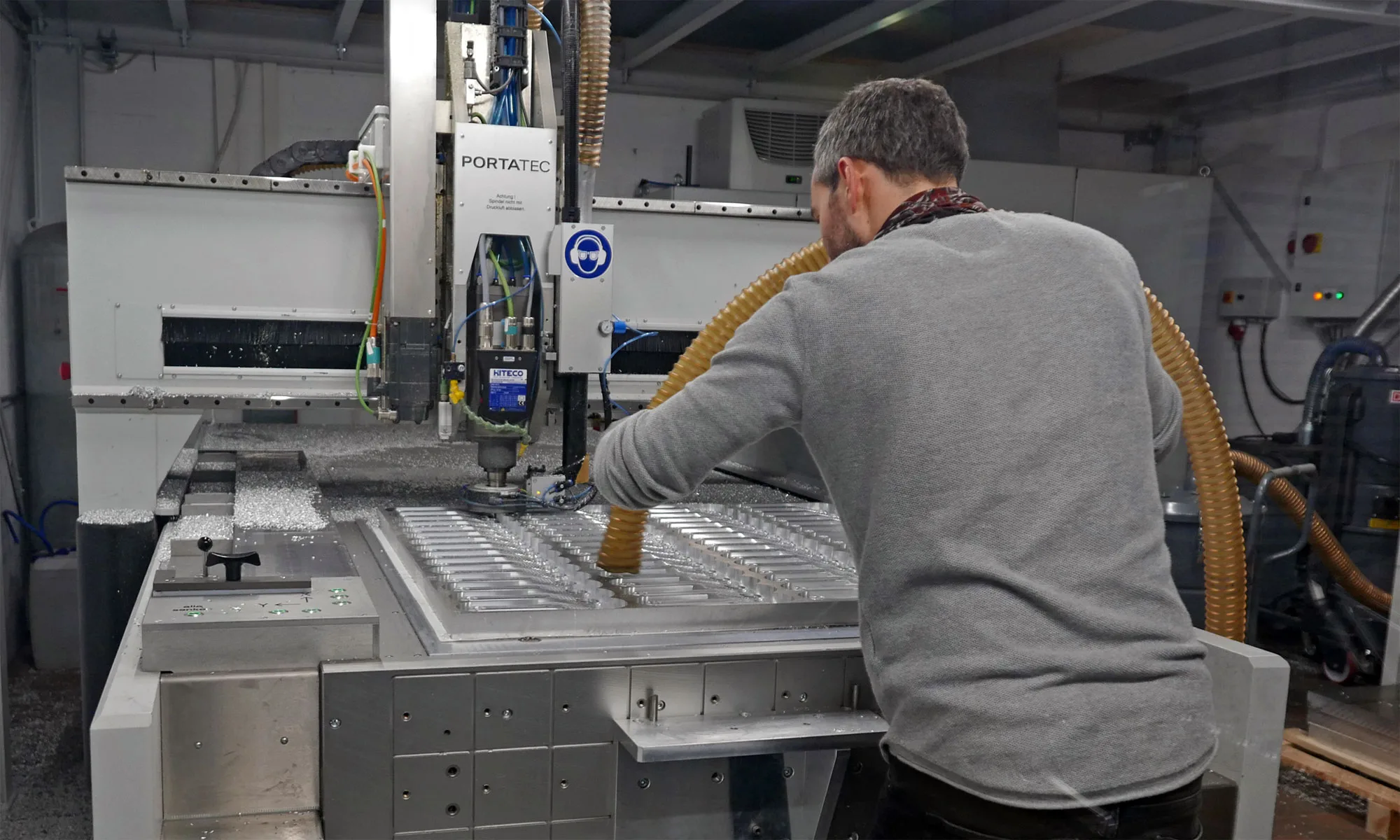
Actually, there are 2 secrets and techniques that make Actofive.
One is the person behind the model, Simon Metzner. And the opposite, the exact Portatec CNC milling machine. Working collectively, these two create each Actofive mountain bike and part.
The CNC-machine and several other of its distinctive options are produced by the corporate of Simon’s father, primarily for the aerospace business. However as an alternative of taking on the enterprise, Simon at all times had different concepts of find out how to use these machines. And with mountain biking being his ardour, Simon Metzner went out on his personal to start out up Metzner Engineering, a contract CNC-manufacturing firm created to permit him to additionally additional his MTB part and bike improvement.
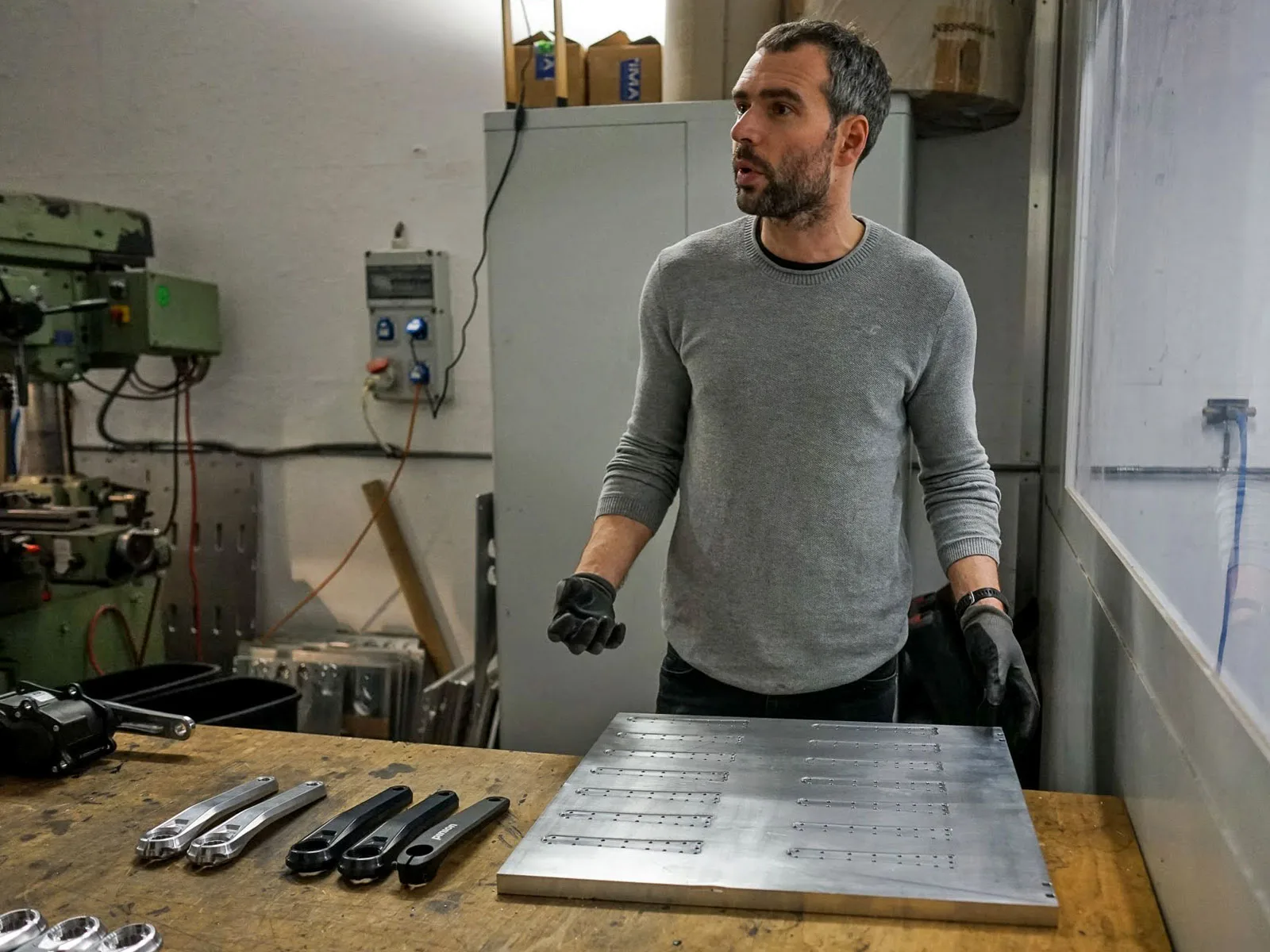
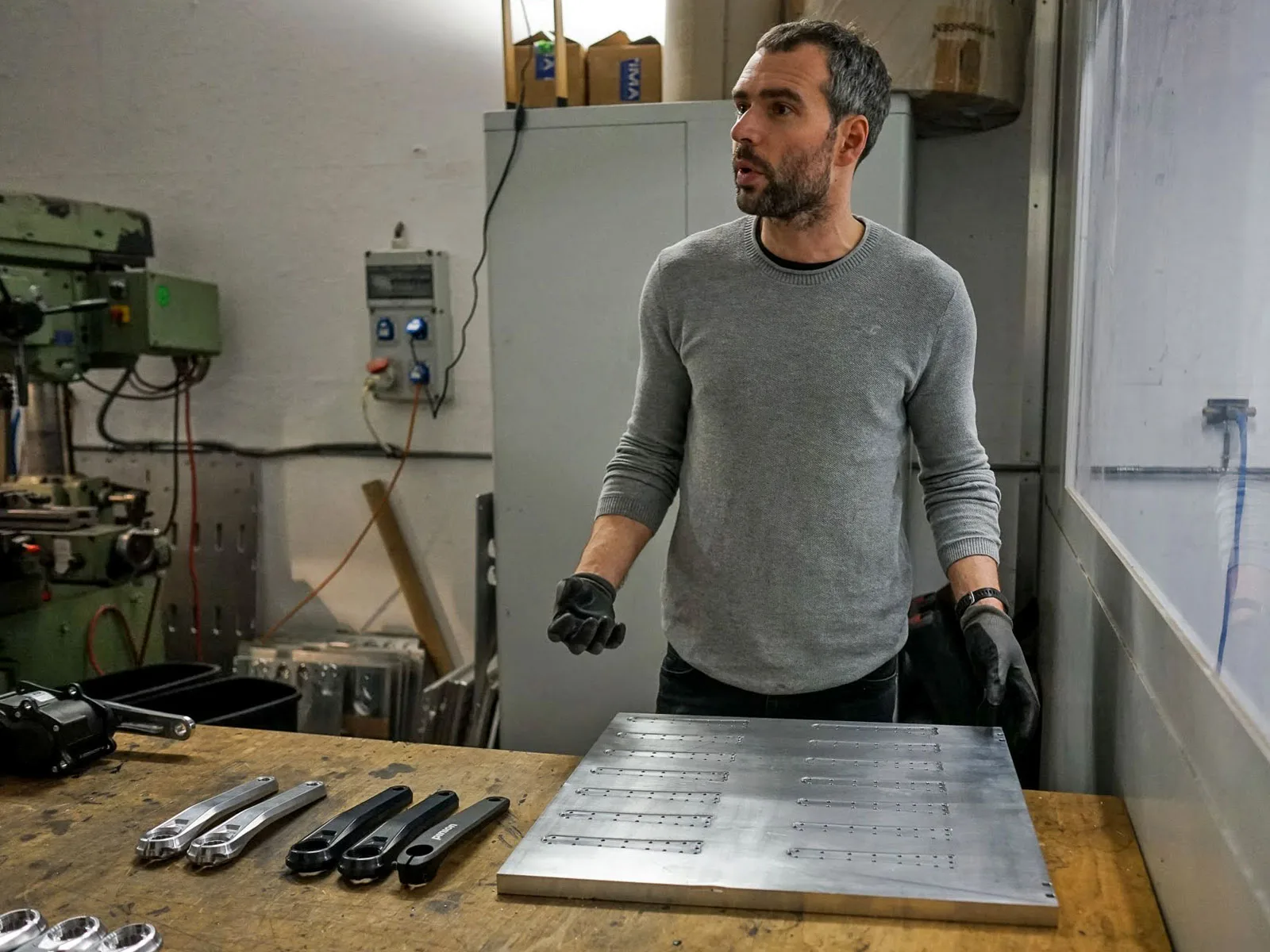
So by mixing his experience in manufacturing course of optimization, the CNC capabilities of his small workshop, and deep mountain bike design data, Simon has developed Actofive right into a sought-after small German mountain bike producer creating true CNC-machined MTB gems.
From prototype to manufacturing
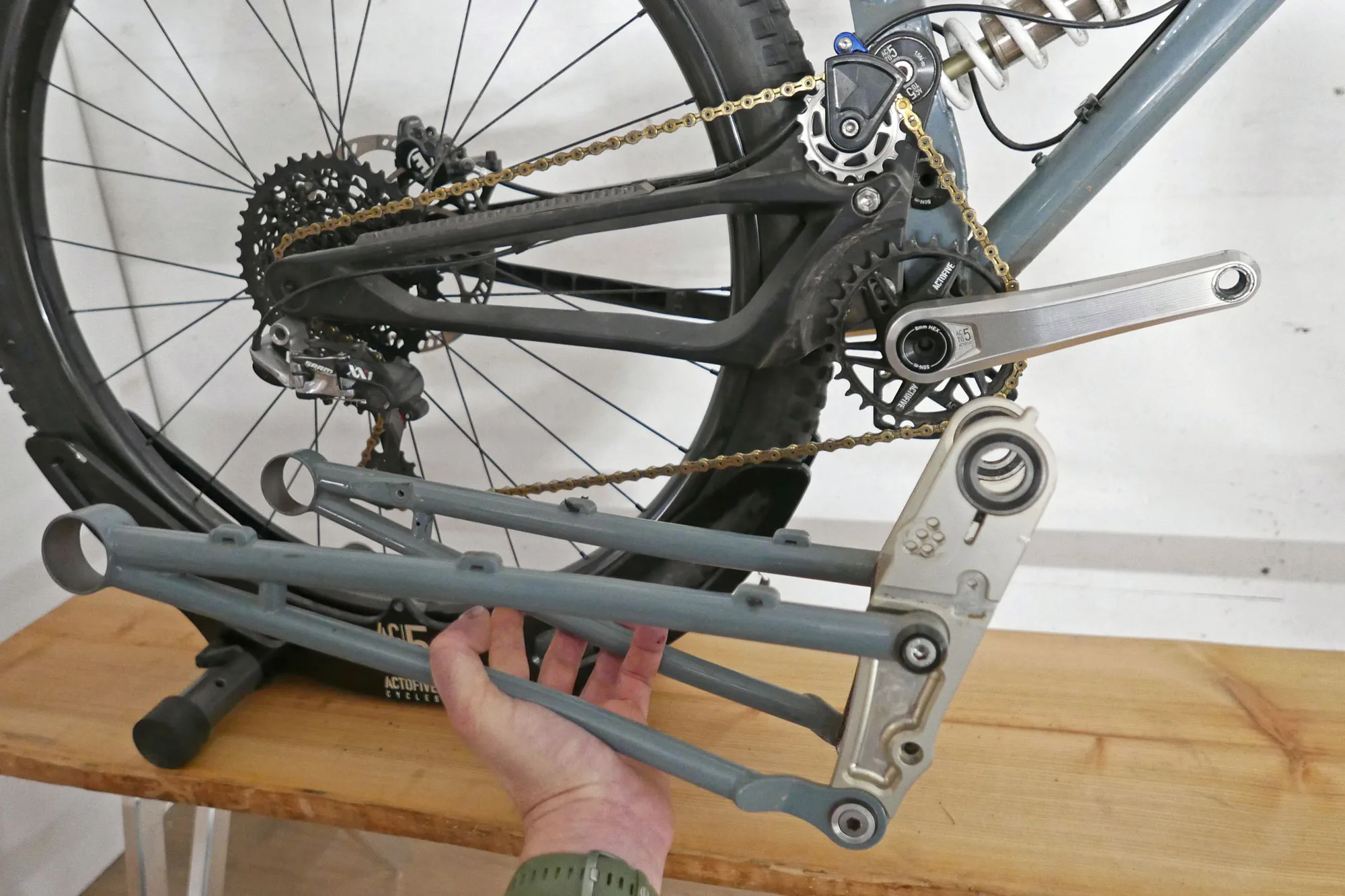
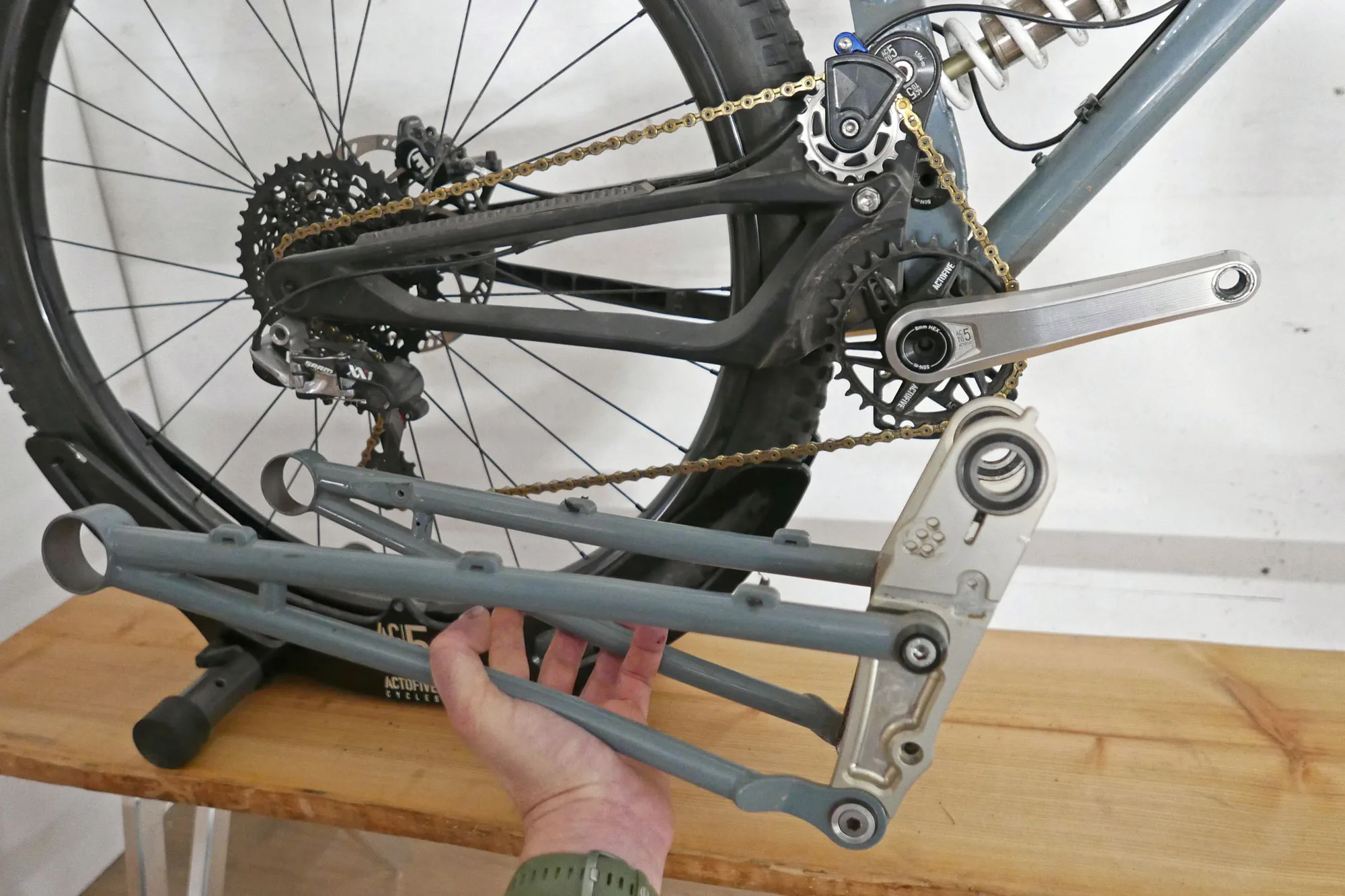
We had been first actually launched to Actofive’s high-pivot alloy P-Prepare about 3 years in the past. However Simon has been engaged on that first adaptable-travel enduro bike for at the very least a number of years longer, since 2018. That’s when he frolicked his personal shingle as Metzner Engineering, after leaving the household CNC machine manufacturing enterprise.
In its first iteration, the bike began with a welded metal entrance & rear triangle joined along with CNC-machined alloy hyperlinks. And it has continued to evolve in lots of iterations alongside the way in which. That authentic metal bike now sits in Simon’s workplace with a machined rear finish fairly just like as we speak’s manufacturing P-Prepare.
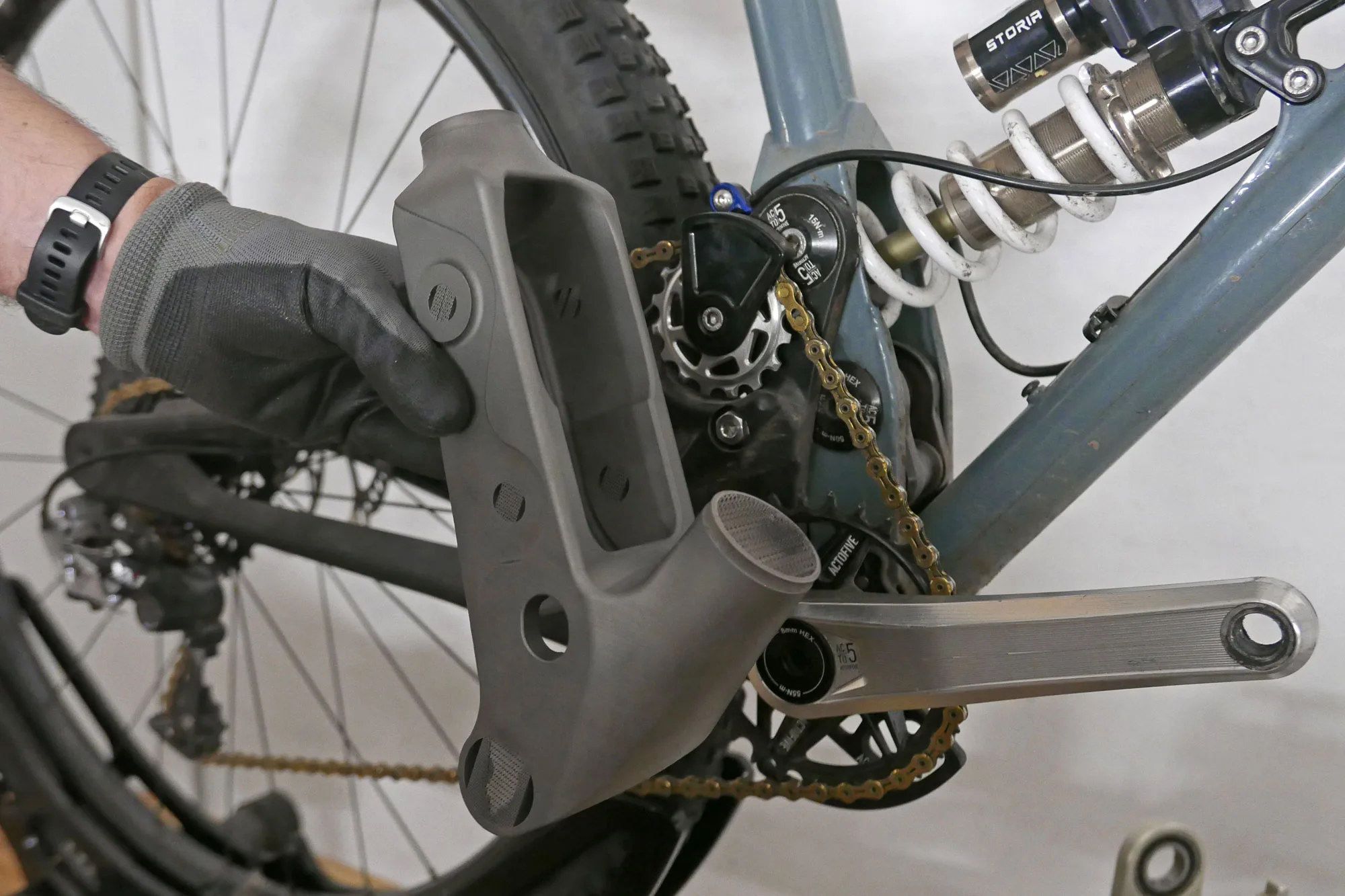
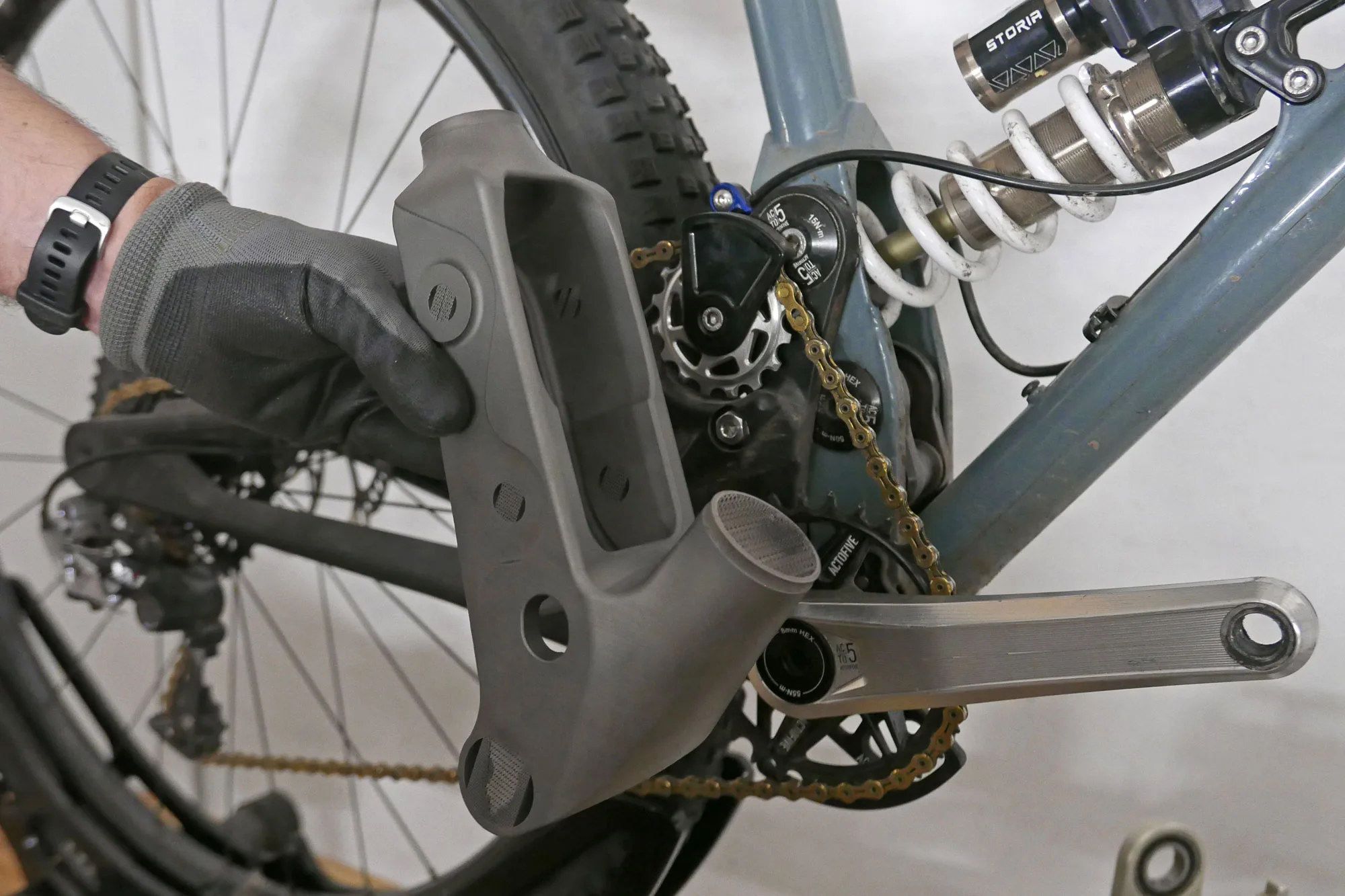
And whereas CNC-machining aluminum has at all times been sort of in Simon’s blood, he isn’t solely beholden to 1 materials, and even the subtractive machining course of. He’s toyed with different supplies – like titanium – and likewise with the potential of recent 3D-printing capabilities.
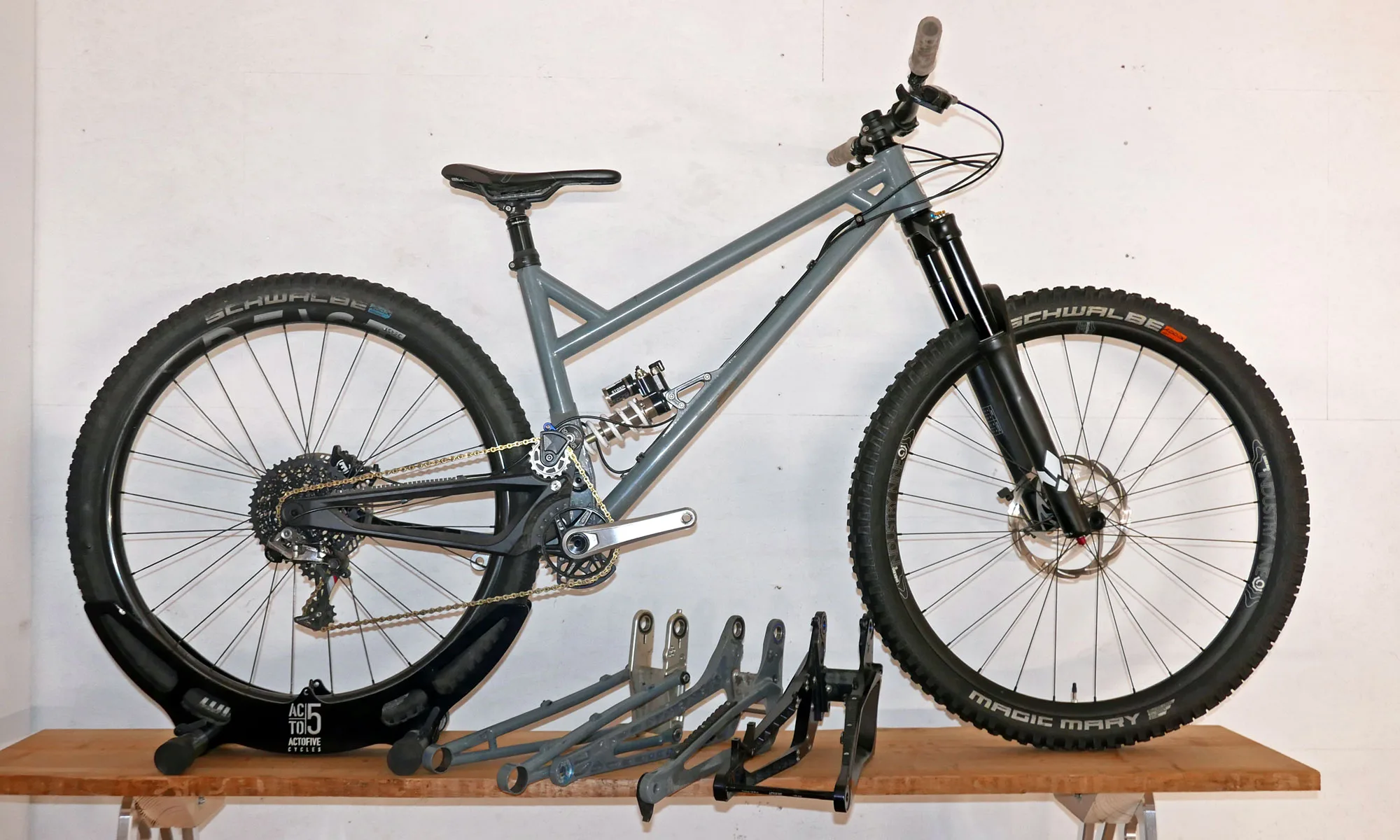
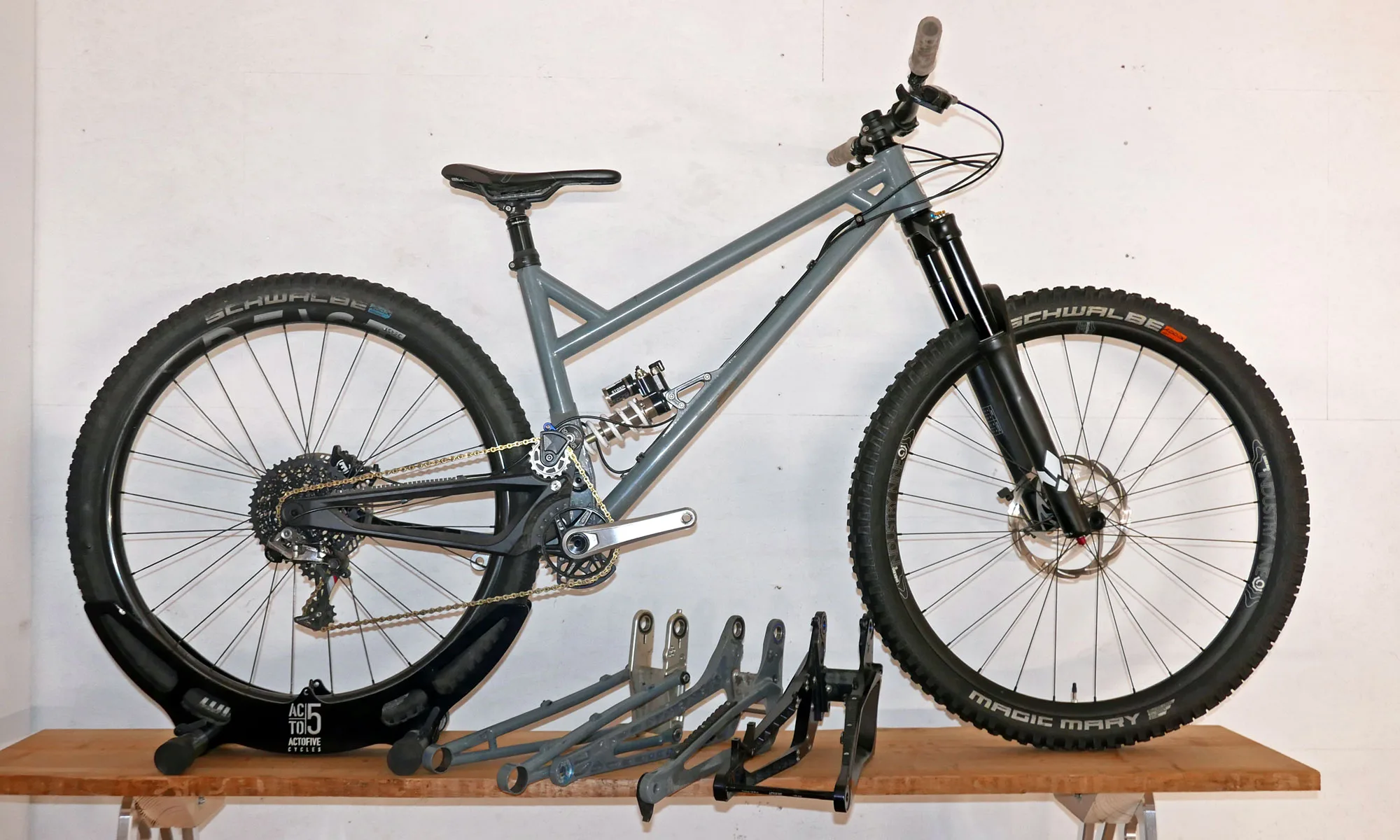
However machining aluminum has outlined the event of Actofive’s bikes and elements these final 6 years, particularly the usage of intricate and well-thought-out milling designs. And it varieties the premise for Actofive’s distinctive clamshell, or sandwich development.
And Simon continues to indicate that he has extra concepts on find out how to refine each his designs and their manufacturing. So there’s a lot evolution left to do in CNC-machined aluminum.
Inside Actofive’s manufacturing unit tour: MTB components in-process
Wanting across the Actofive workshop throughout our manufacturing unit tour confirmed a fairly good pattern of their full providing, in numerous phases of completion.
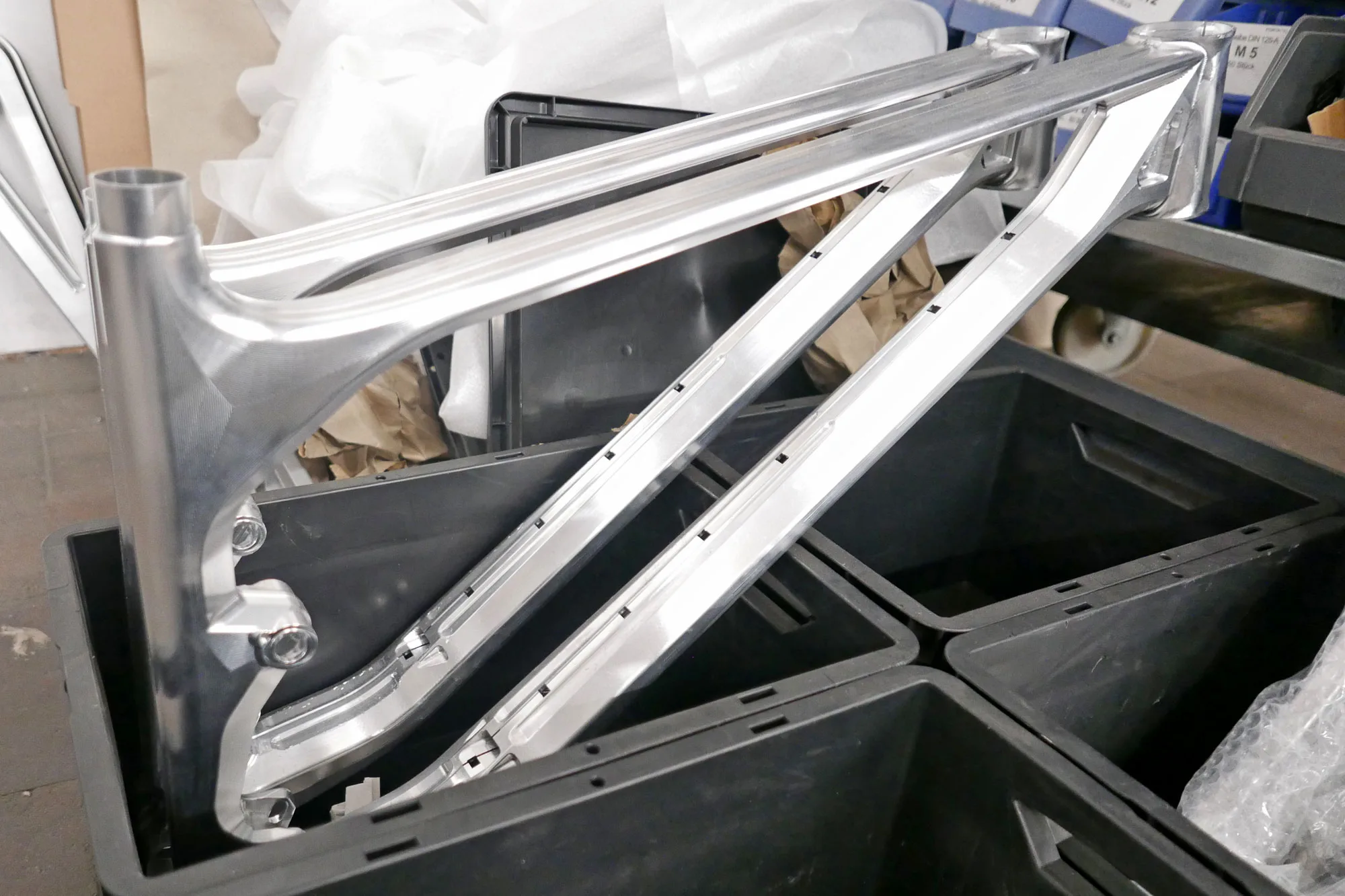
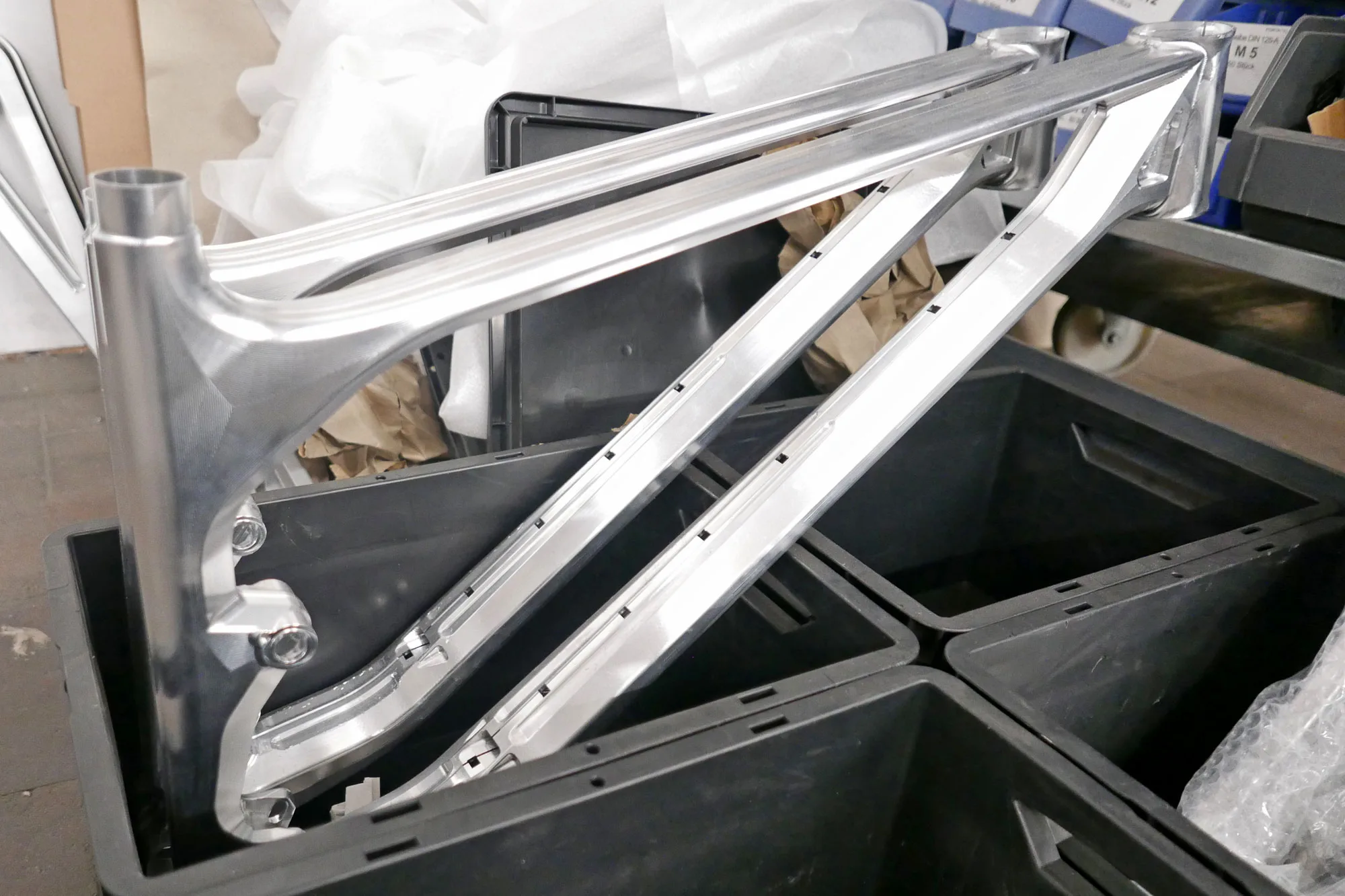
Listed here are a few I-Prepare path bike entrance triangles. The 2 halves have every been machined from each side – the skin that we are able to see, plus the intricate inside webbed truss construction that Actofive doesn’t let anybody else see.
We had a peek, and it’s much more spectacular that the high quality software marks you see on the skin. The design of the interior construction permits Actofive the power to fine-tune power and stiffness at numerous places throughout the mountain bike body, whereas protecting it light-weight.
However Actofive is cautious of making a gift of the secrets and techniques of how they obtain their stability of lightweight-to-strength. And particularly resistant to present away the design of their interlocking system that’s used to bond the 2 halves of a body collectively to create the entire bike.
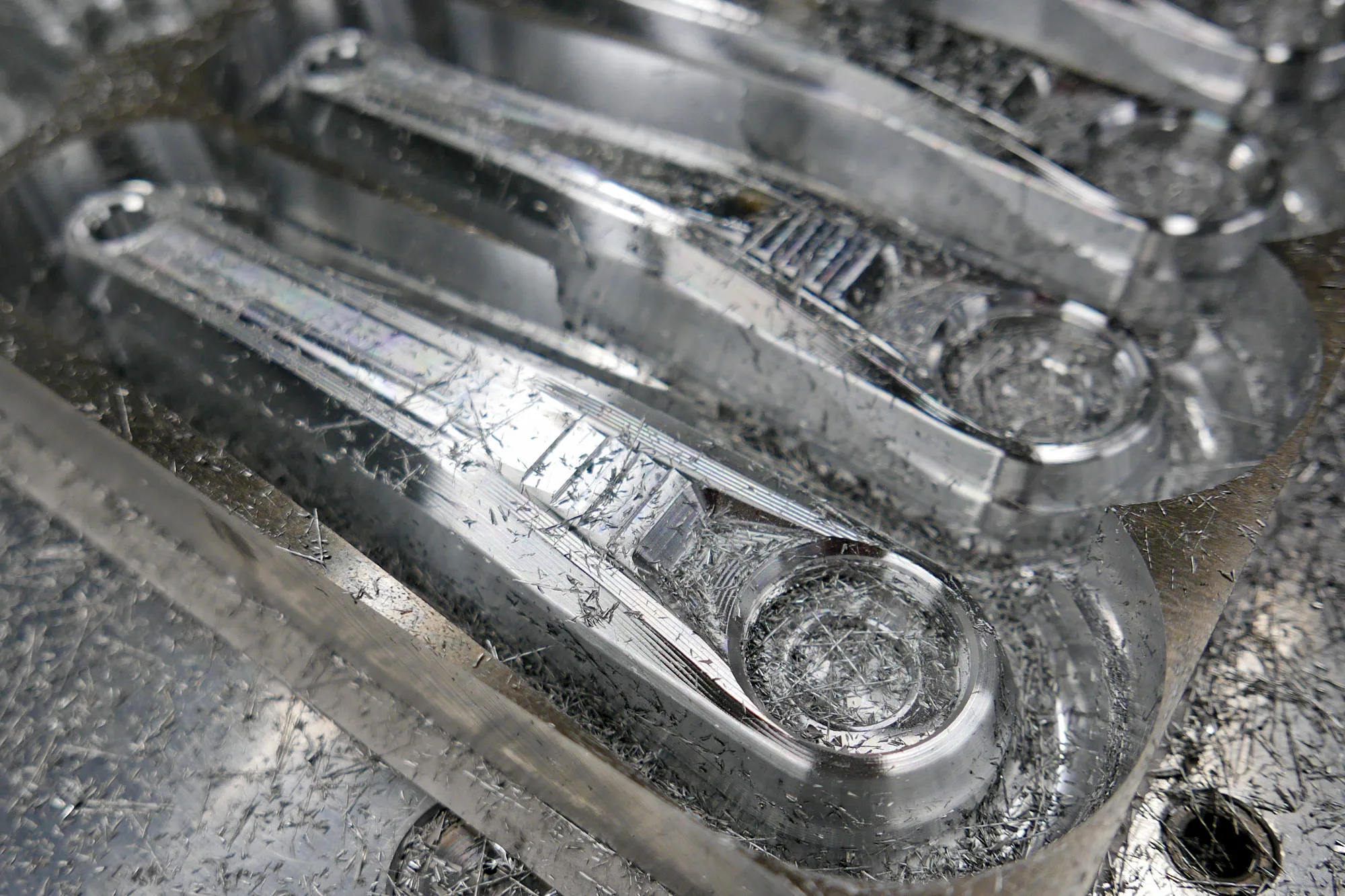
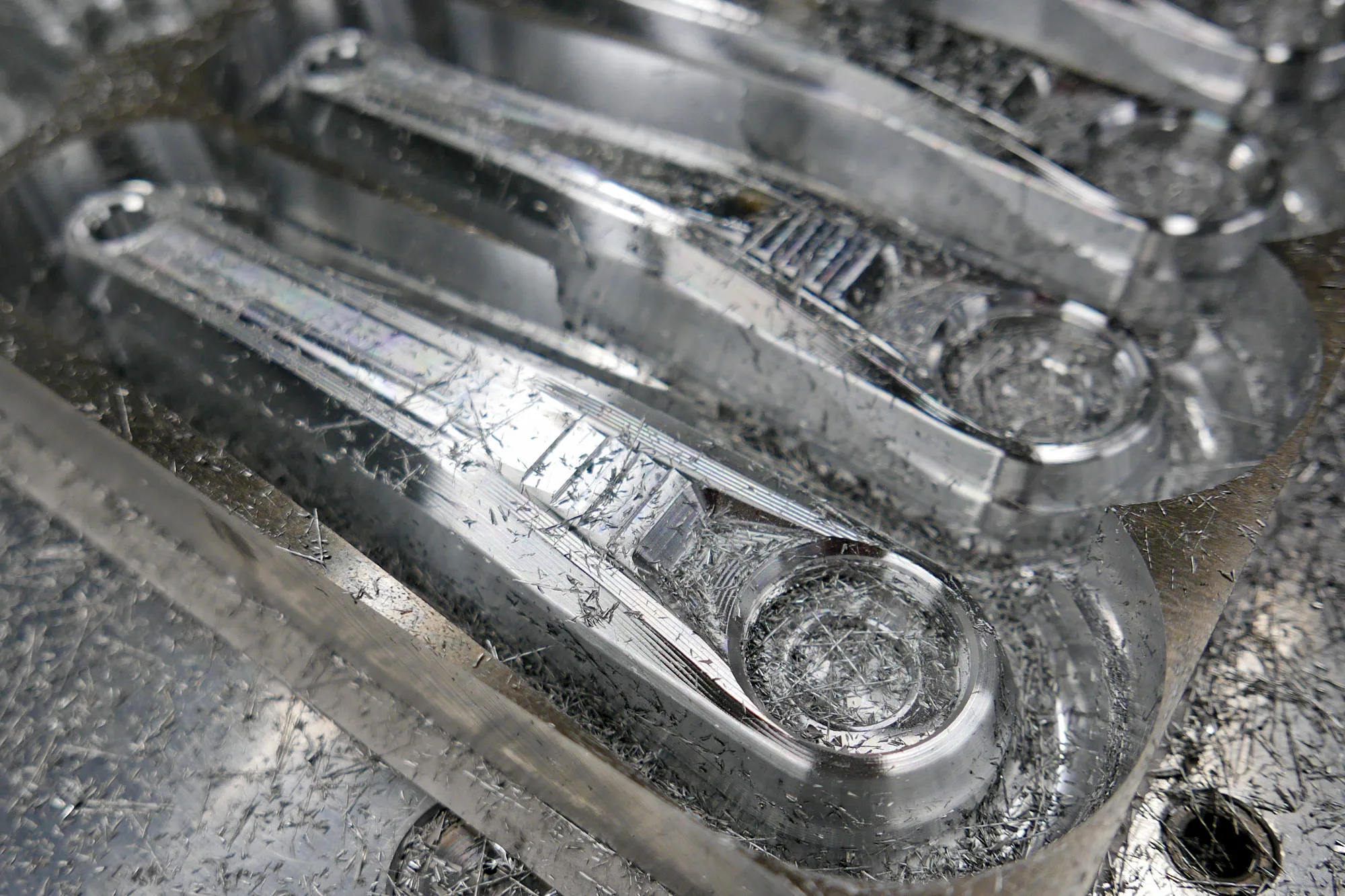
We additionally had an opportunity to observe some Actofive crankarms be machined of their first step throughout our manufacturing unit tour.
From alloy slabs to machined gems
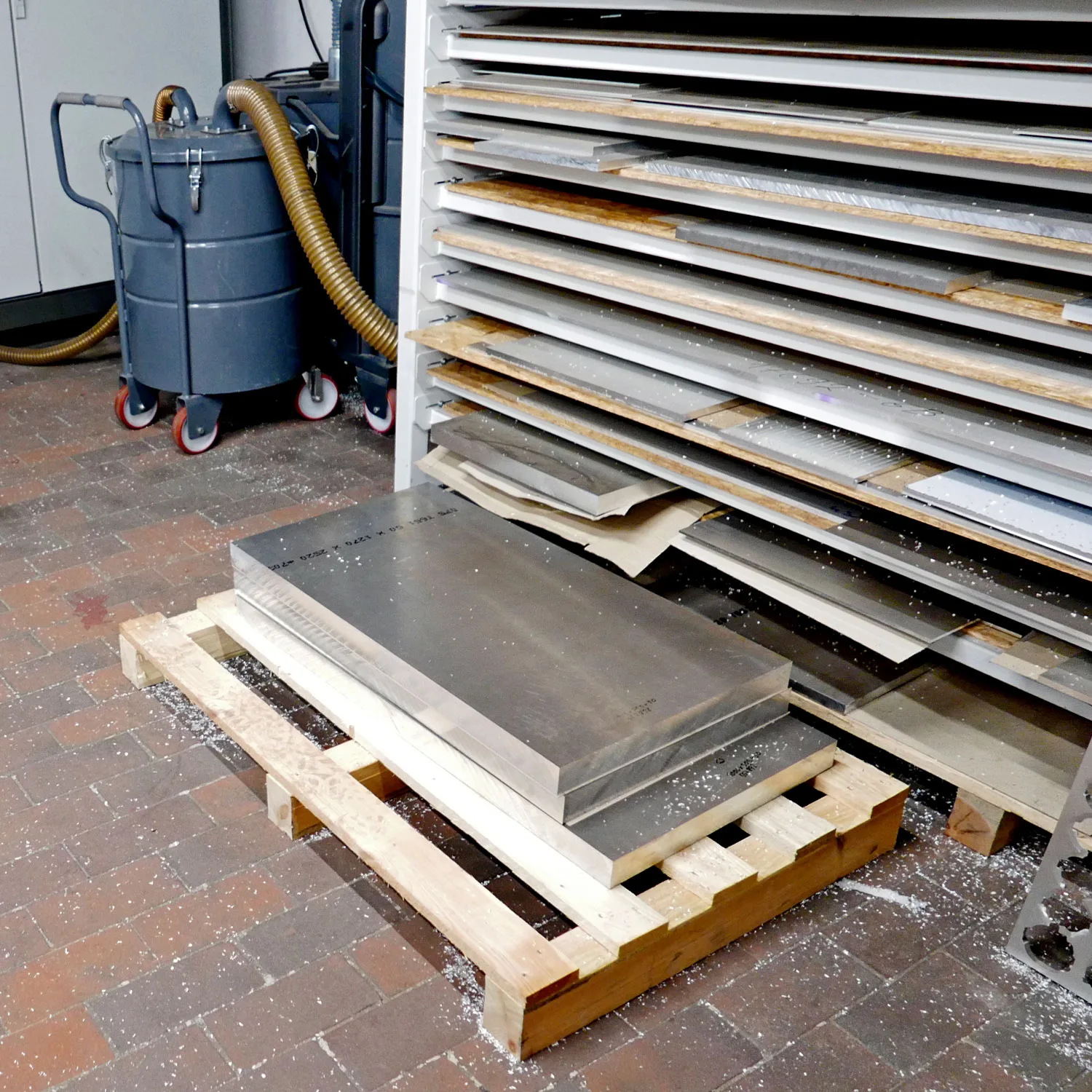
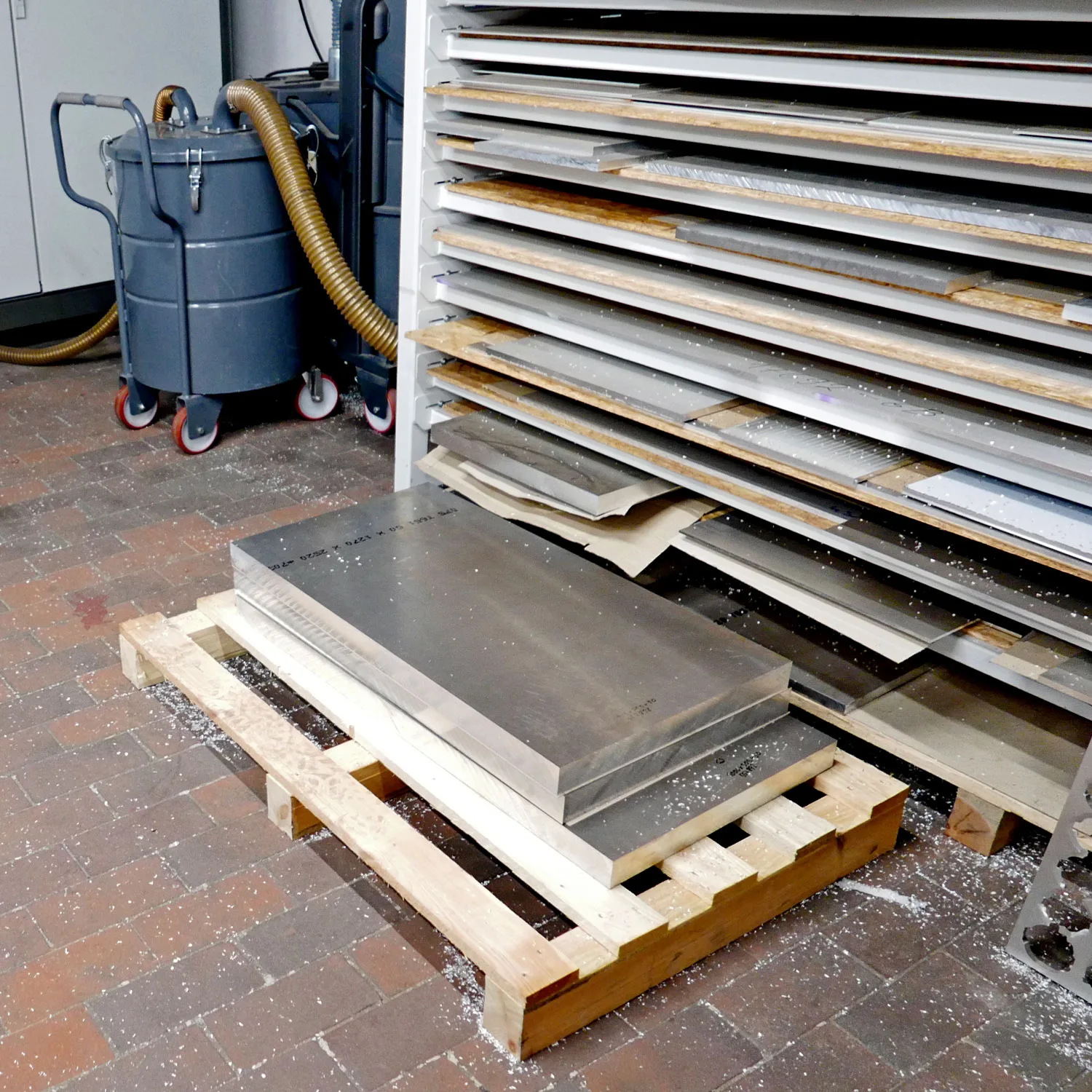
The guts of every little thing that Actofive produces begins out as easy slab of aluminum billet.
And actually, most of Actofive’s elements come right down to machining one facet to get the ultimate outdoors form. Then, flipping it over (and securing it to a unfavourable fixture on the milling machine) to hole out the second facet.
The best components like their extra inexpensive Signature X crankset, the P-train rear finish, and the I-Prepare seatstays depart it at that, the place you possibly can see each side which were machined. However extra complicated hole components just like the mountain bike entrance triangles & Signature cranks, get 2-sided machining for every body half which might be then bonded collectively to create the extra complicated hole construction.
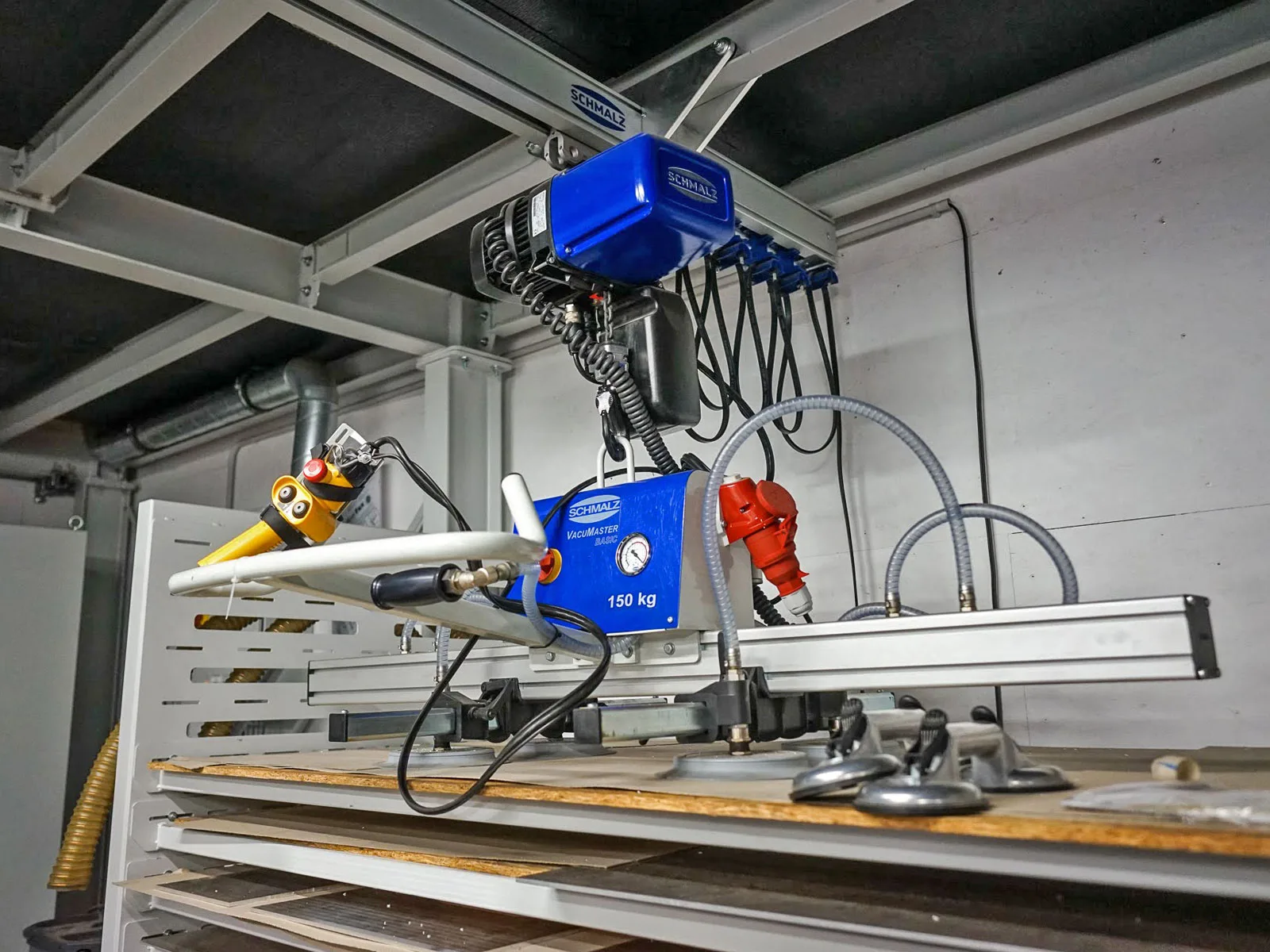
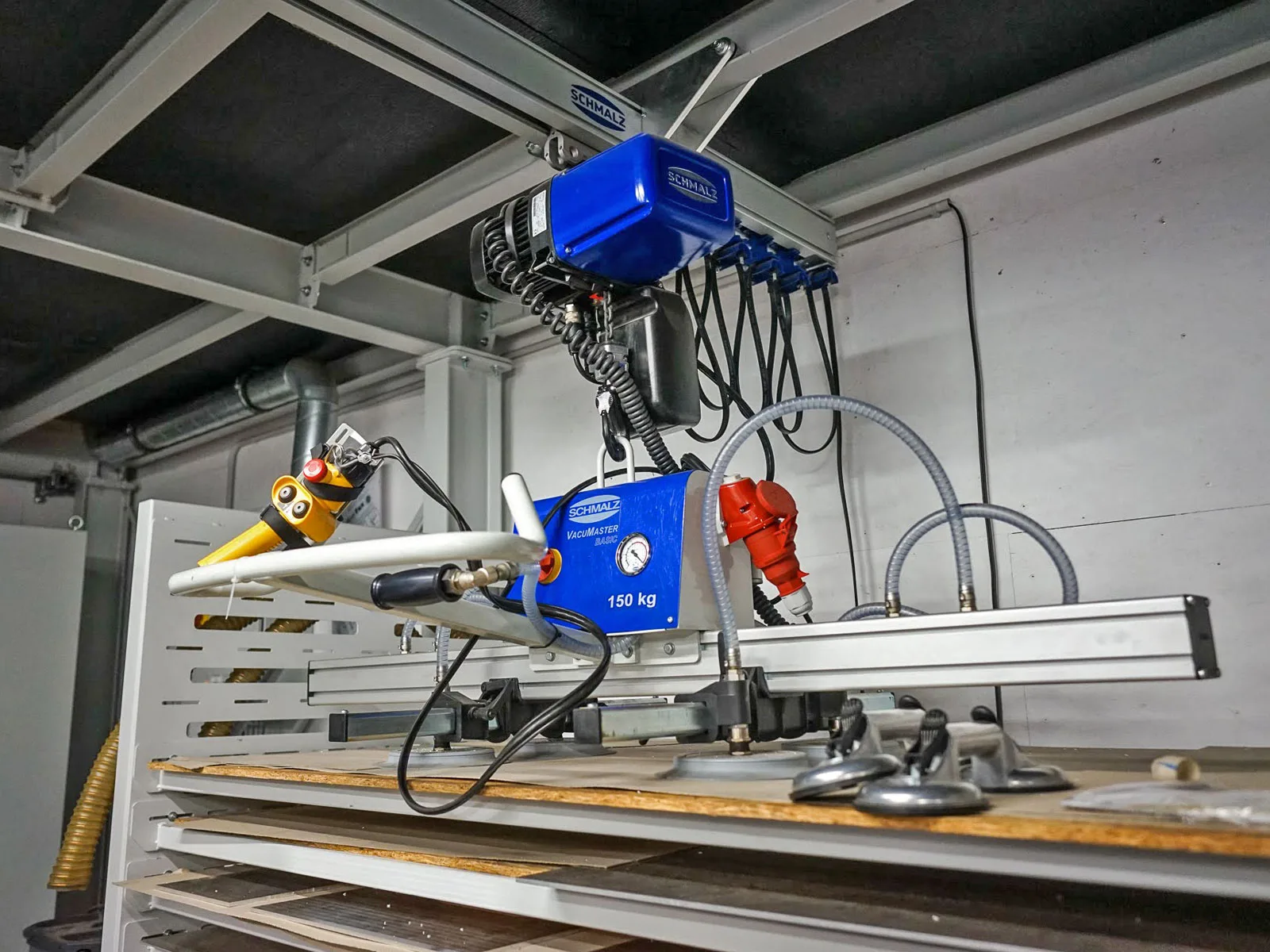
However after all, shifting huge heavy chunks of aluminum round is sort of troublesome earlier than all that further materials is machined away (and picked up for recycling). So Actofive has this good little crane of their machining room, which permits Simon the power to simply maneuver every little thing on his personal.
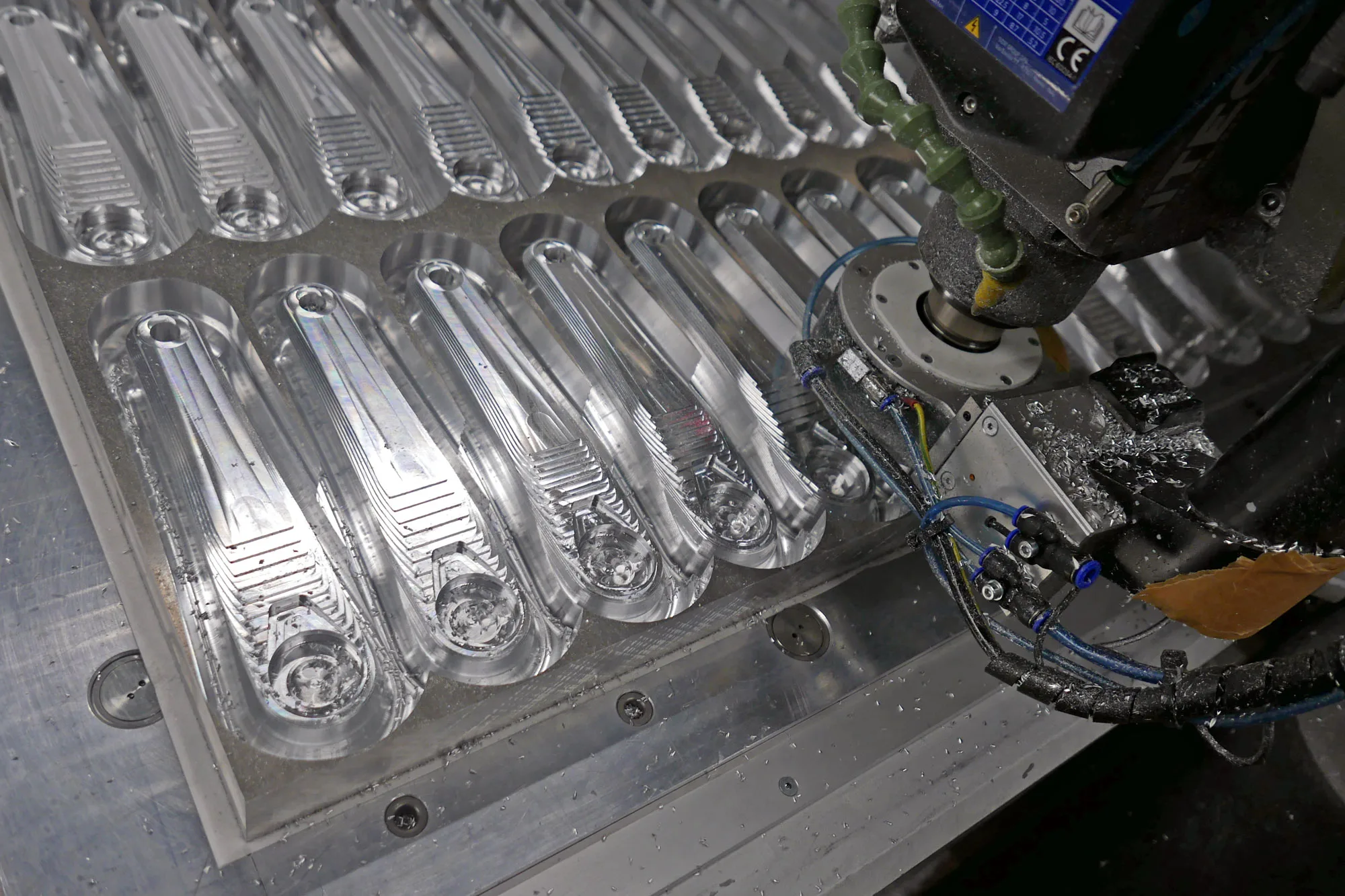
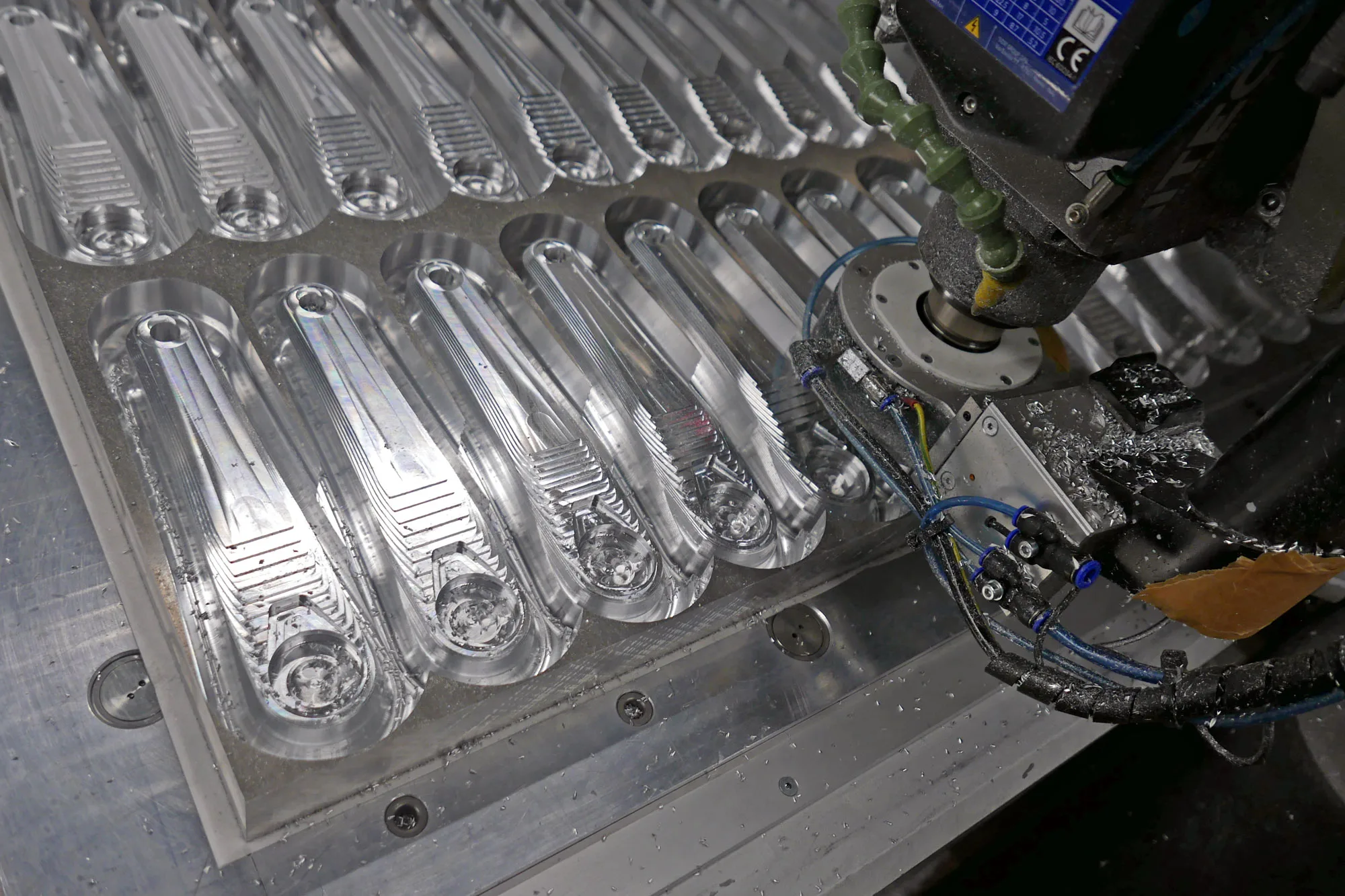
After which, as soon as held down on the milling machine’s worktable with a robust vacuum stress, the intricate designs will be carved out of the uncooked billets of aluminum. Most frequently in densely packed, nested layouts to optimize essentially the most quantity of elements out of a single piece of uncooked aluminum materials.
CAD upstairs + CAM downstairs
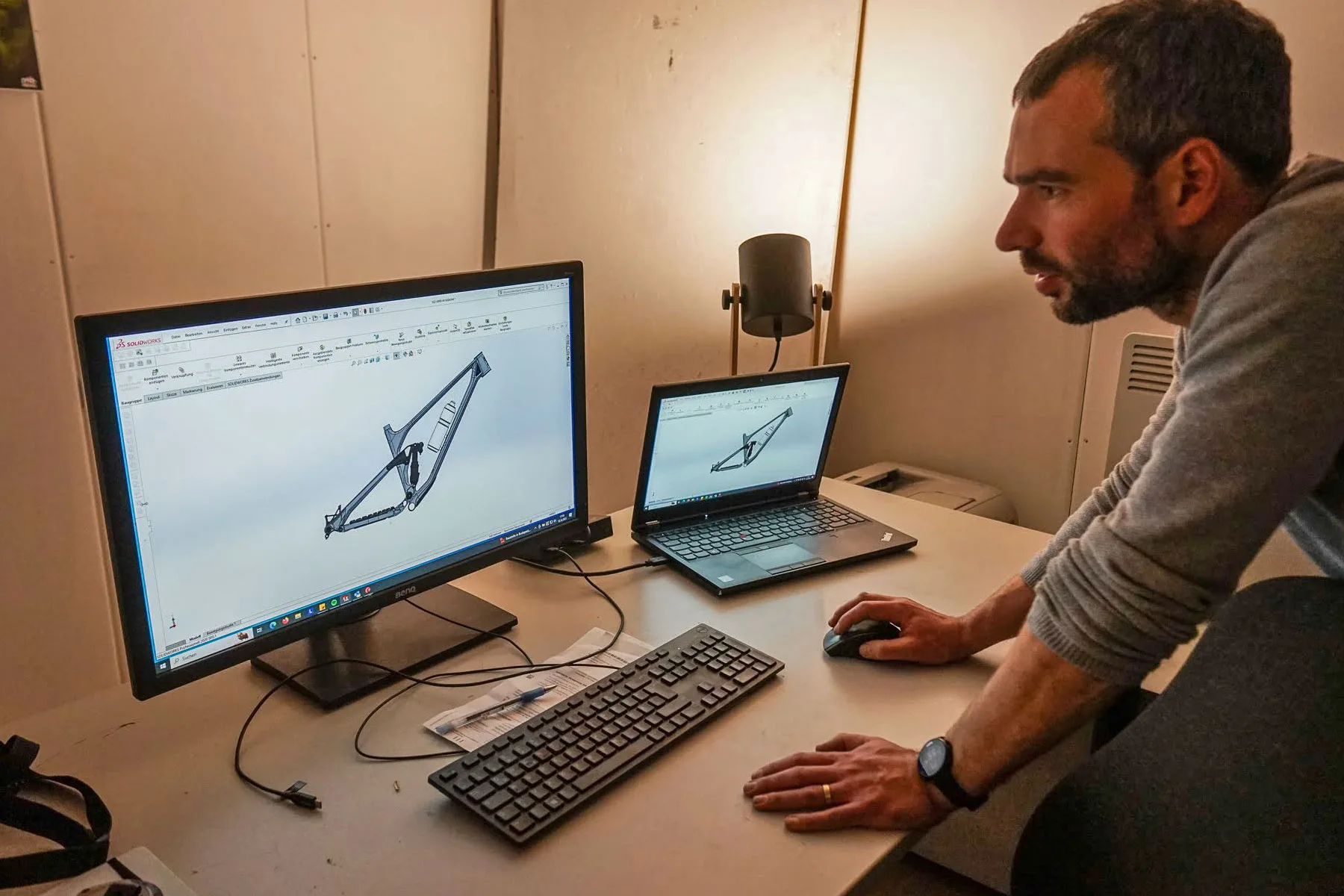
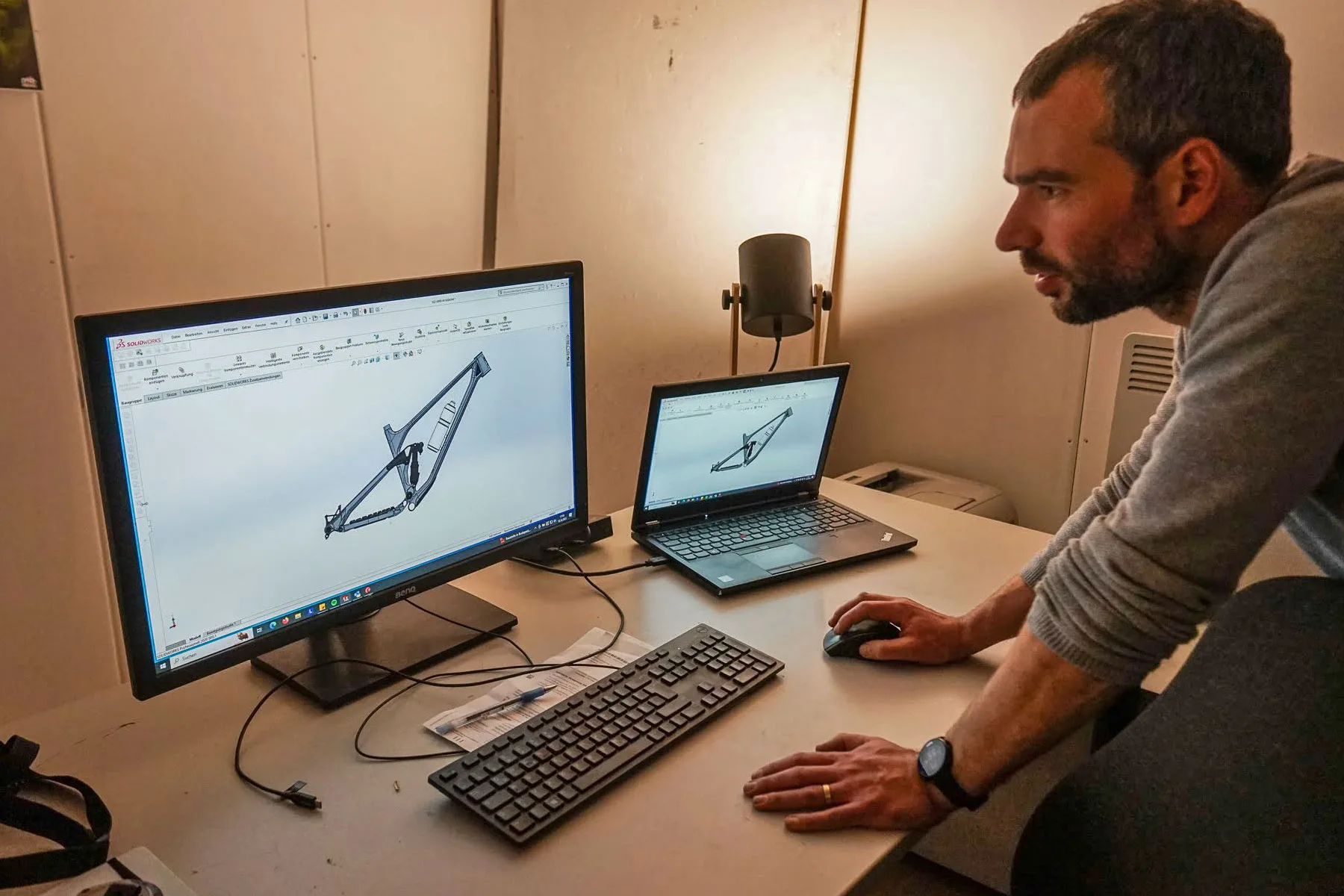
Every little thing that Actofive produces in made in-house within the manufacturing unit that we toured.
Simon has a design workplace upstairs instantly over his machining room.
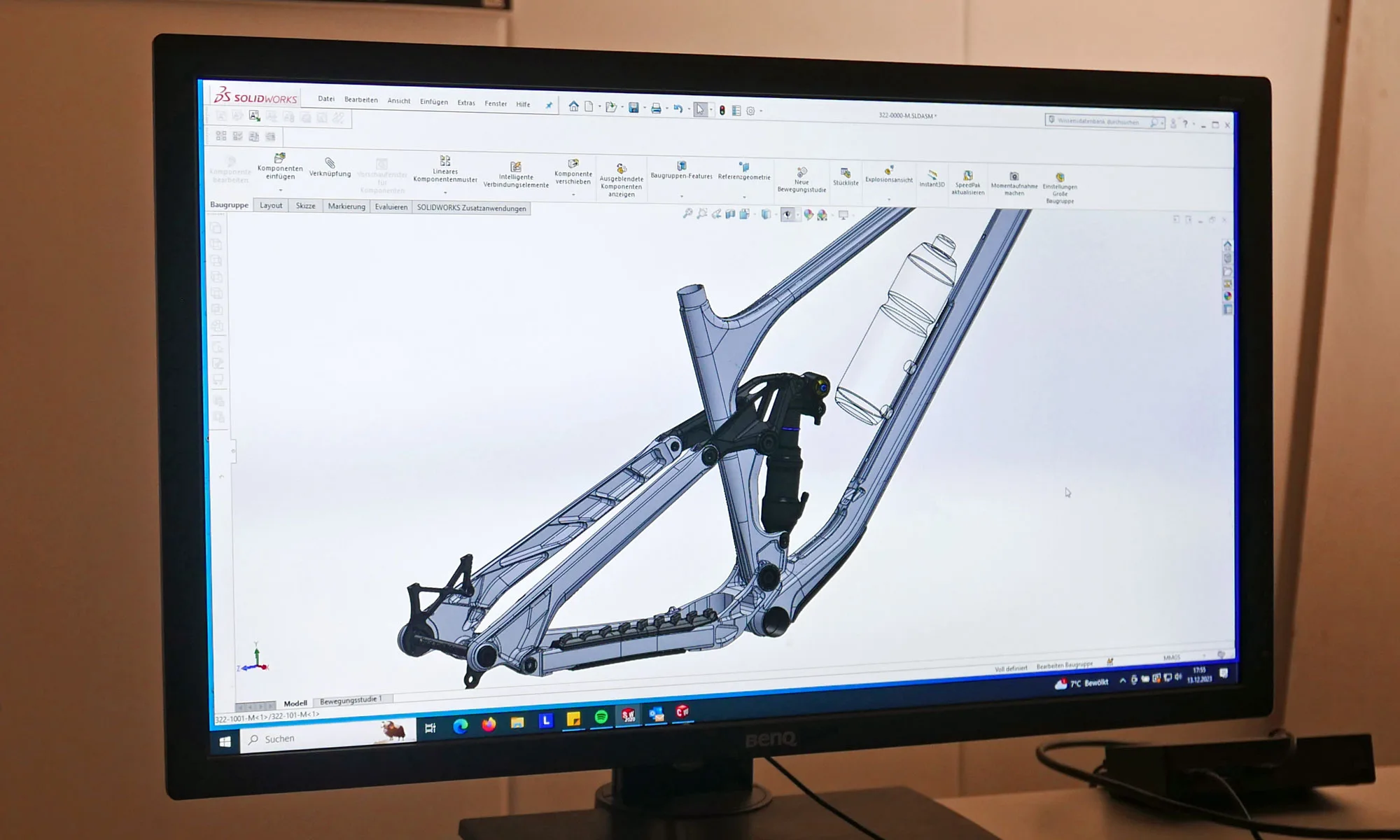
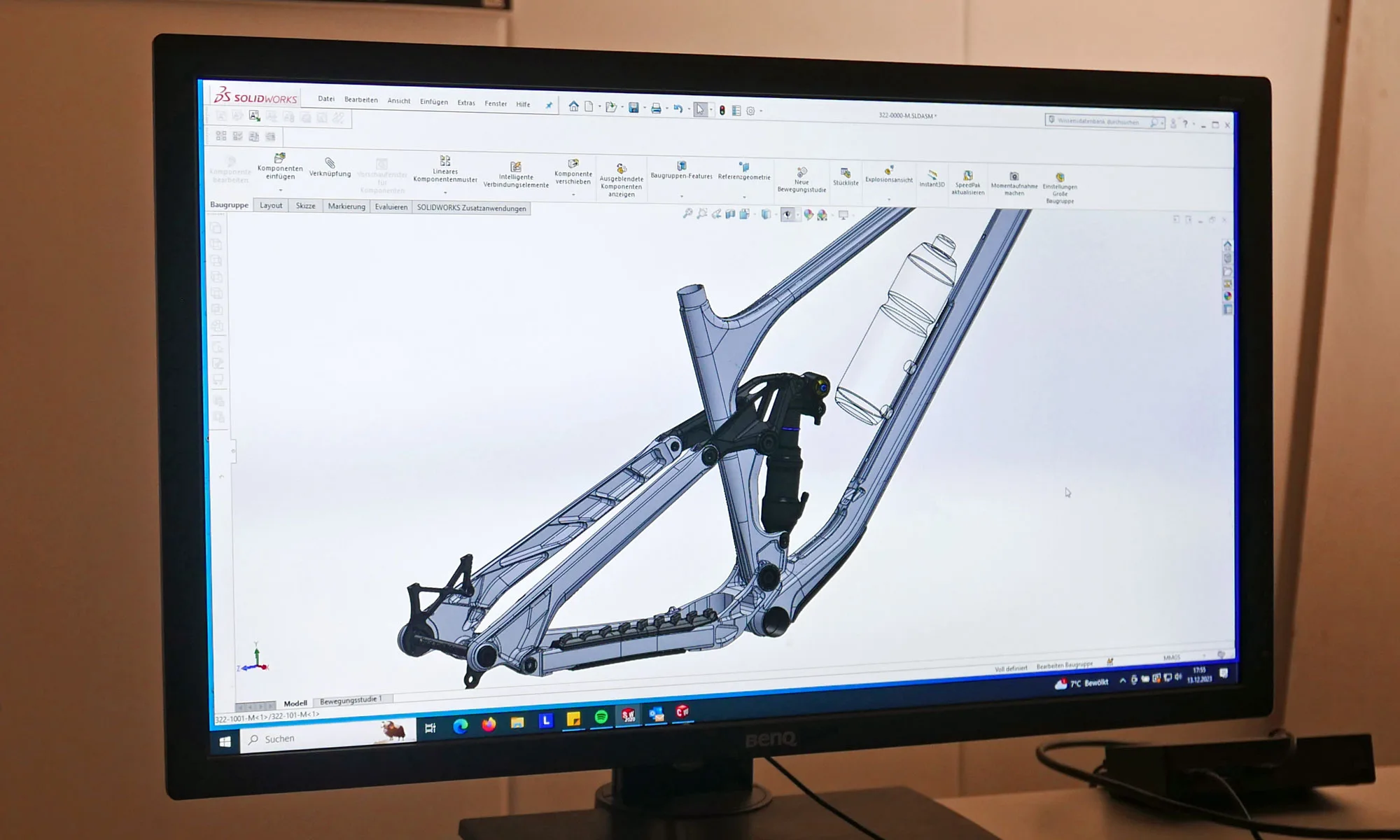
There every little thing is designed and refined in SolidWorks, creating the computer-aided design (CAD) knowledge to drive the computer-aided manufacturing (CAM) processes one ground under.
ActoFive’s key manufacturing outputs…
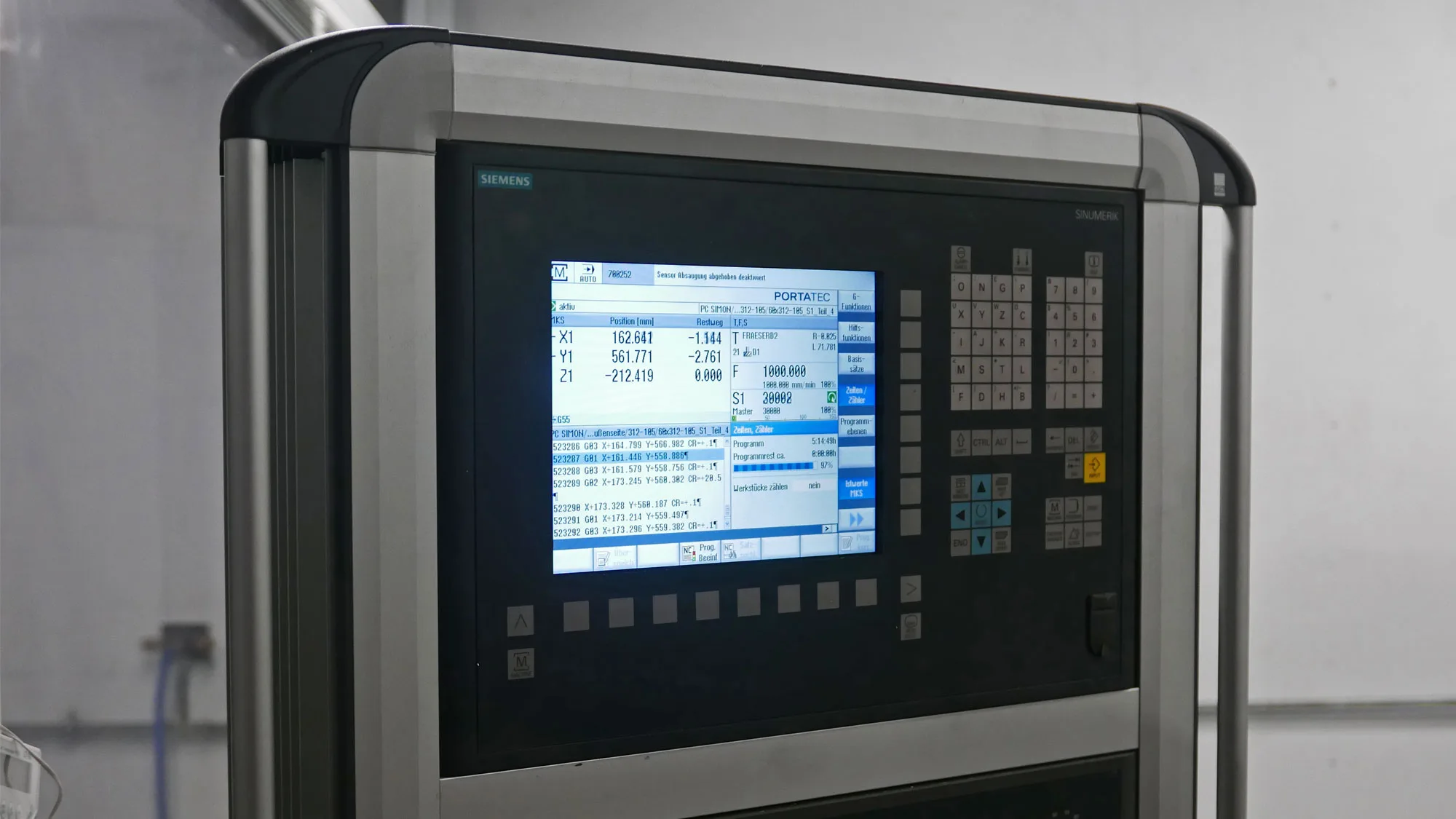
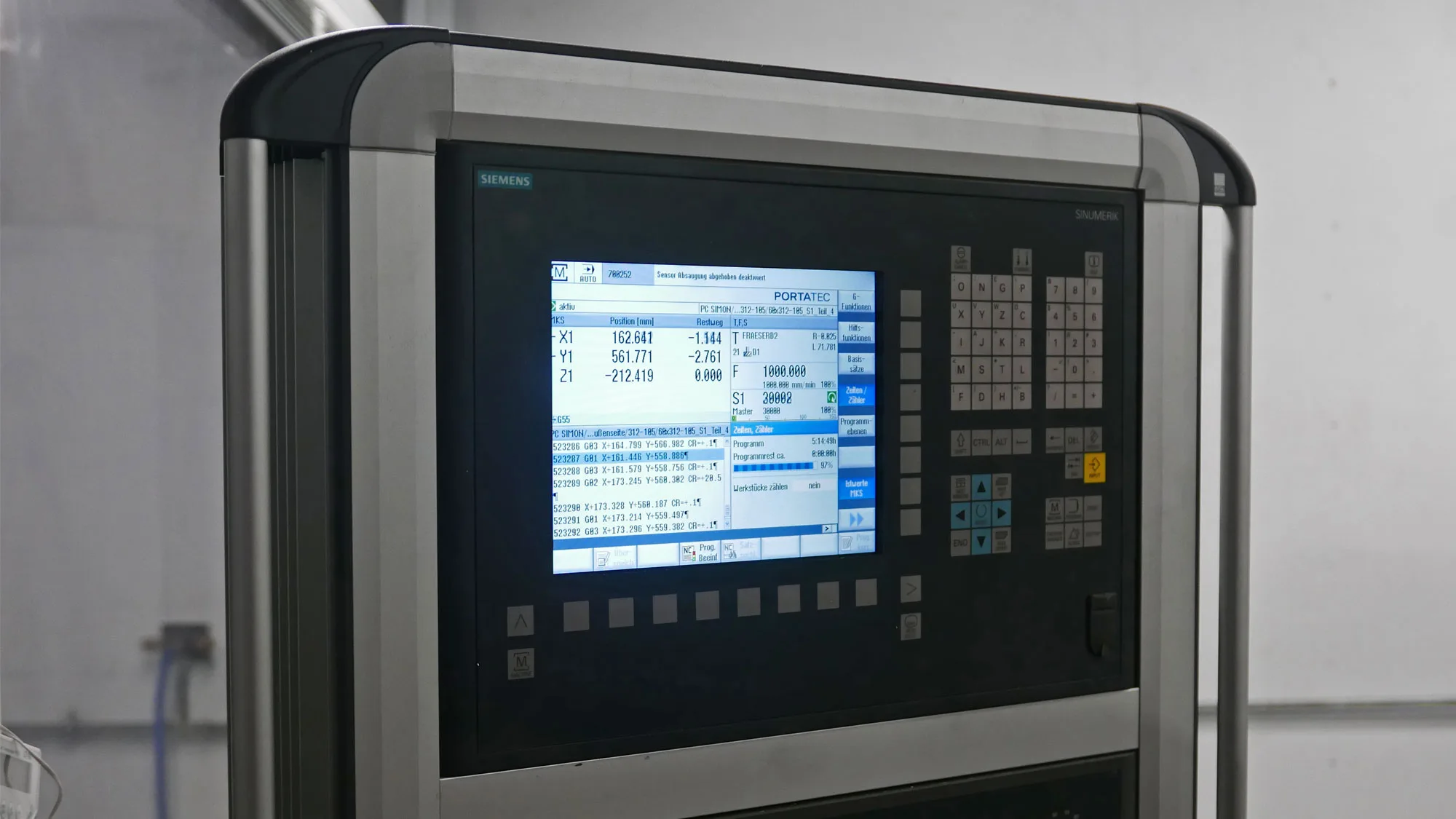
Actofive’s specialty is creating 3 issues. CAD/CAM knowledge, metallic filings, and out of that… precision machined alloy elements.
The Portatec CNC mill is the brawn. However the brains of the Siemens controller manages all of the machining processes, tooling, and the place these software reduce. Whereas Simon can remotely function every little thing from his laptop upstairs, for manufacturing, every little thing is dealt with instantly on the machine. There’s a lot uncooked knowledge governing the machining course of, this ensures that any potential minor breakdown in communication couldn’t negatively have an effect on the ultimate work.
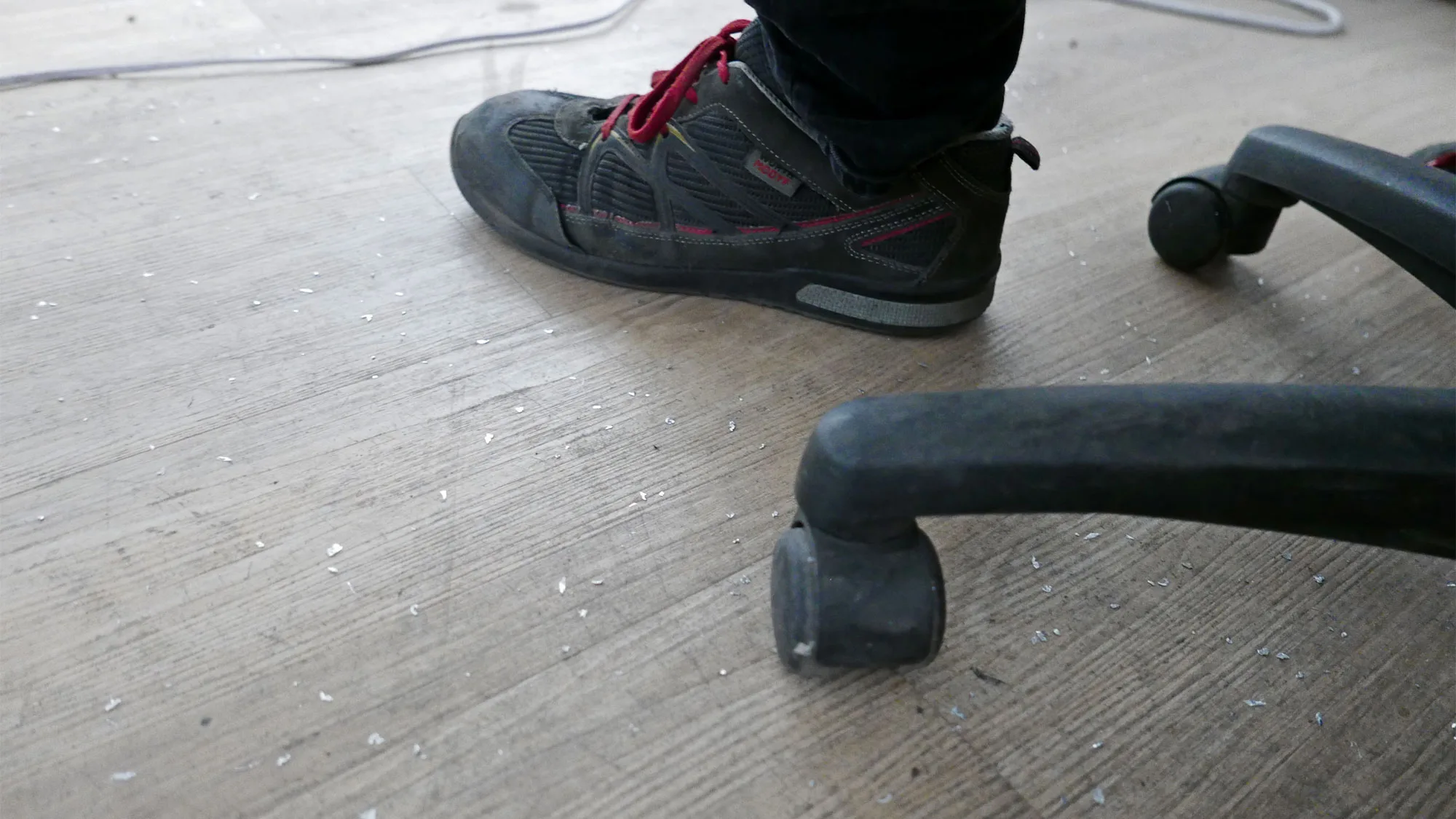
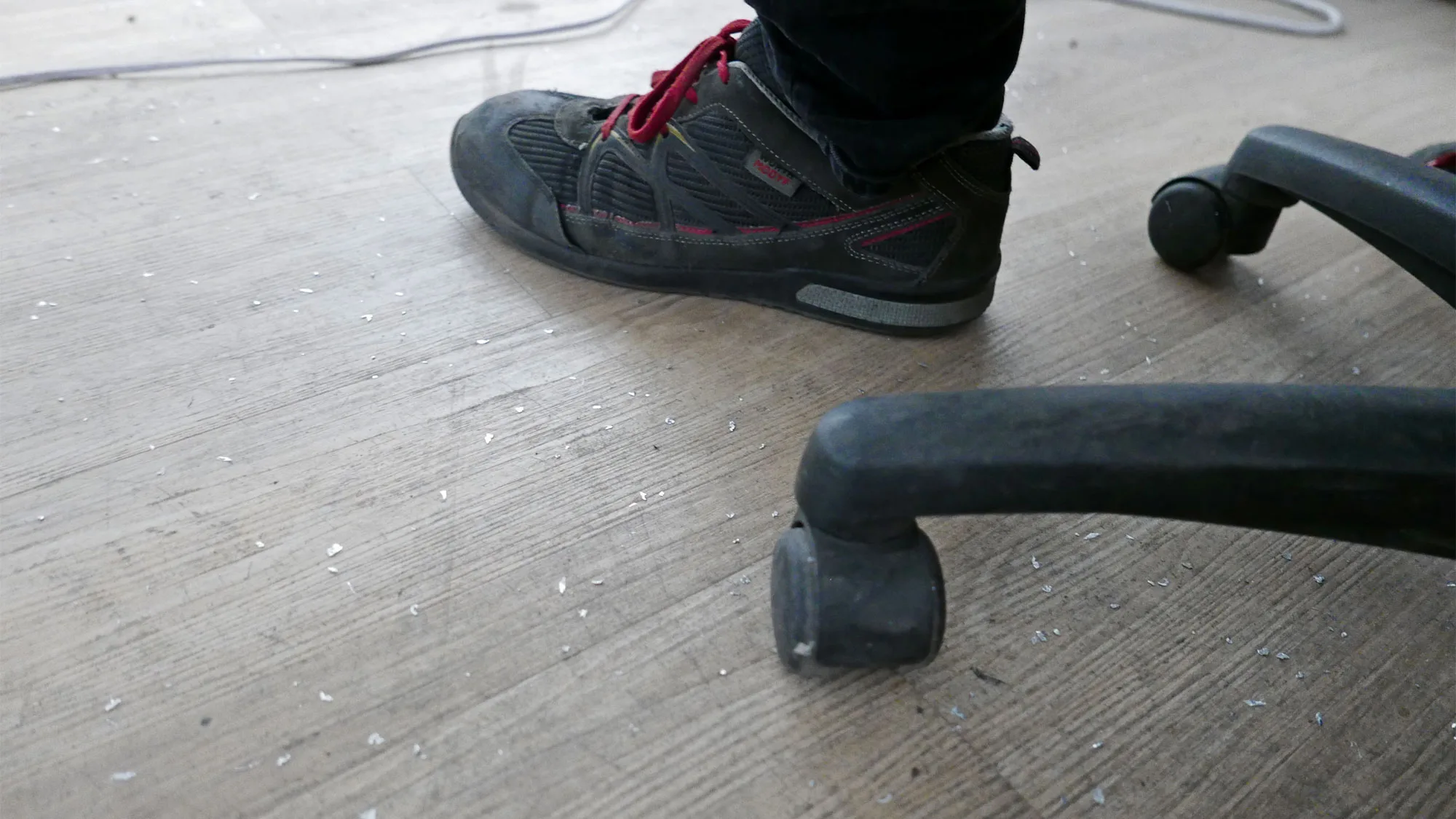
Moreover knowledge, Actofive’s manufacturing unit is roofed with these small aluminum filings we noticed in our tour.
Positive, the majority of fabric will get effectively collected for recycling, however loads of chips fly round. That’s why machining occurs in its personal fully enclosed room. However each time Simon strikes round to manage the method, filings keep on with his garments & footwear. And since they’re not magnetic, it’s a chore to completely maintain beneath management.
So he has separate garments and footwear for engaged on bikes & elements within the store. And simply resigns himself to common cleansing and swapping to separate clothes earlier than leaving the workshop.
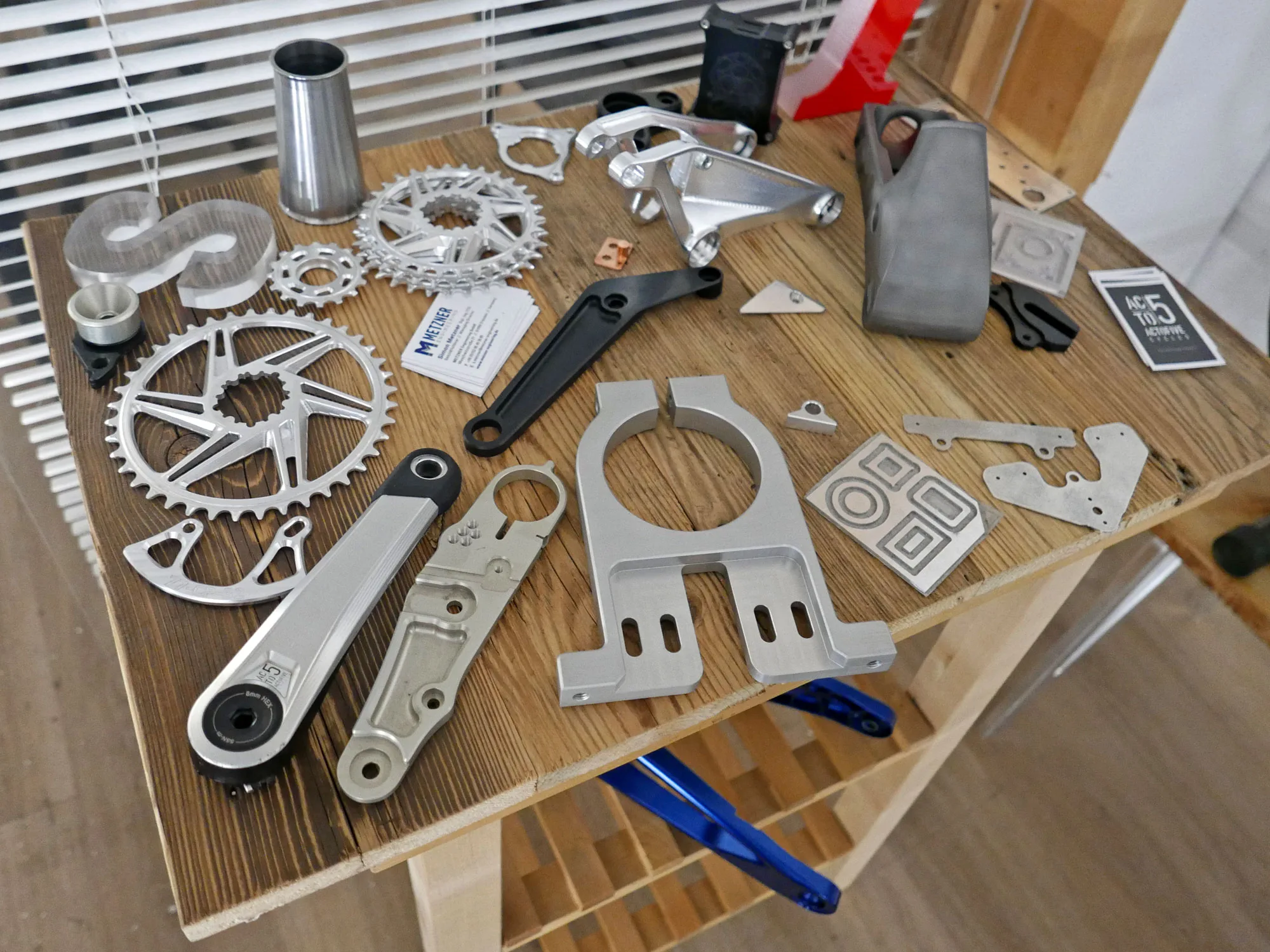
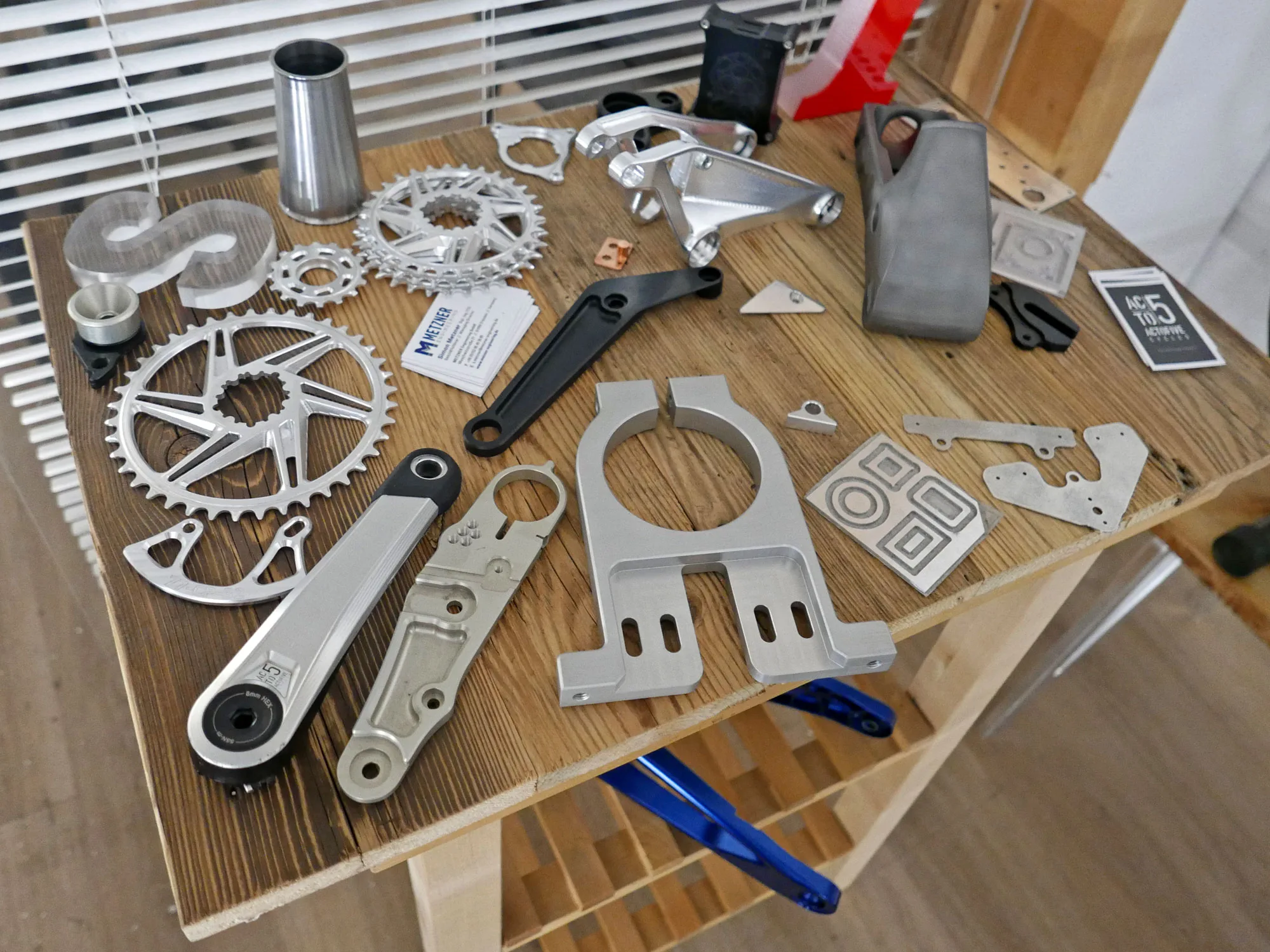
Lastly, specialised machined alloy elements. Actofive is the bike model that drives Simon Metzner’s ardour. And from that we get full-suspension Actofive mountain bike frames, cranksets & chainrings.
However he does loads of contract manufacturing too. There’s definitely a little bit of crossover within the bike business – issues like bashguards, prime caps, and even some extra superior components like rocker hyperlinks & seatstays for different bike firms. However there’s loads of different industrial machining, too. Simon defined that he spends the overwhelming majority of his improvement and manufacturing time on the Actofive mountain bike facet of issues, however nonetheless greater than three-quarters of his revenue comes from contract machining.
Actofive Manufacturing facility Tour: MTB cranks, chainrings & frames
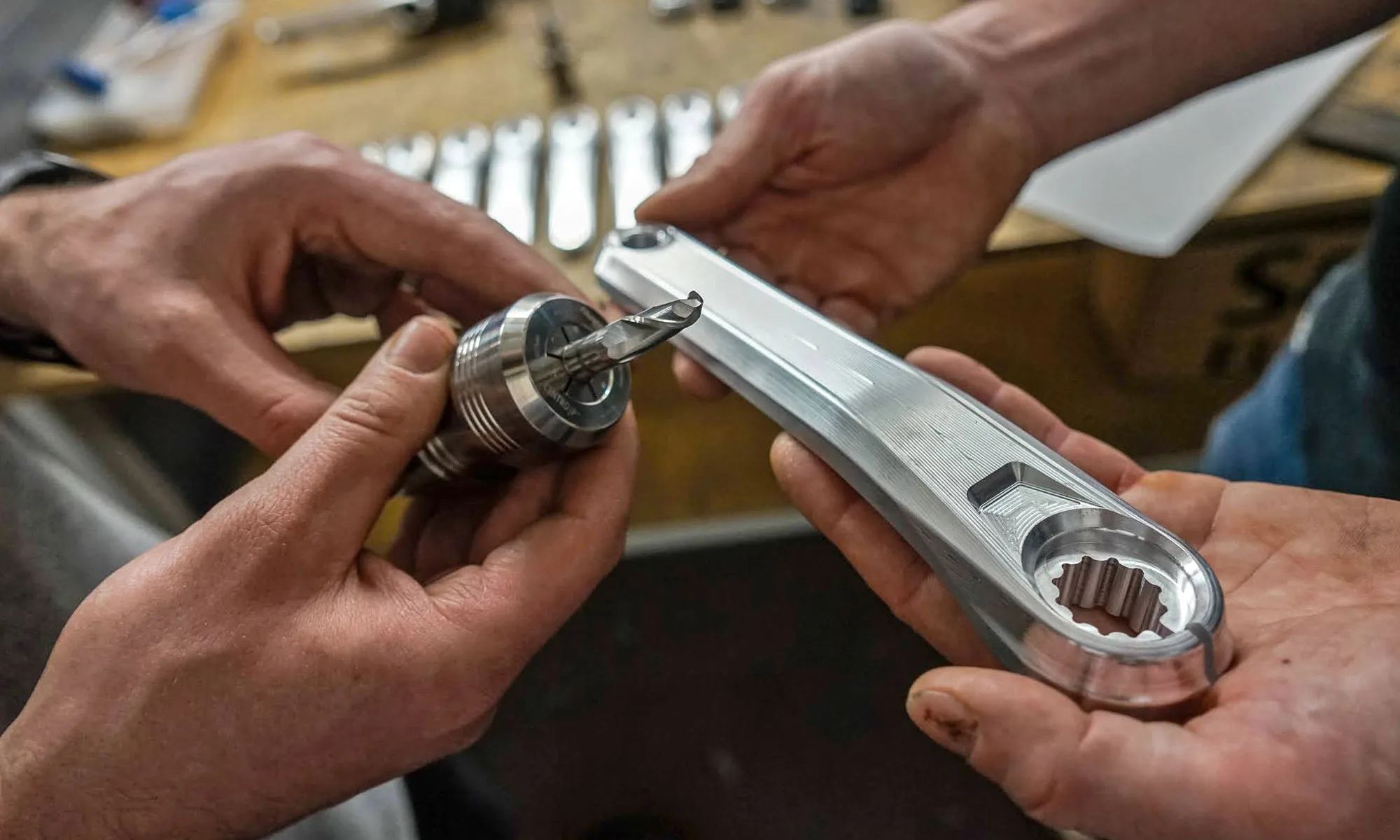
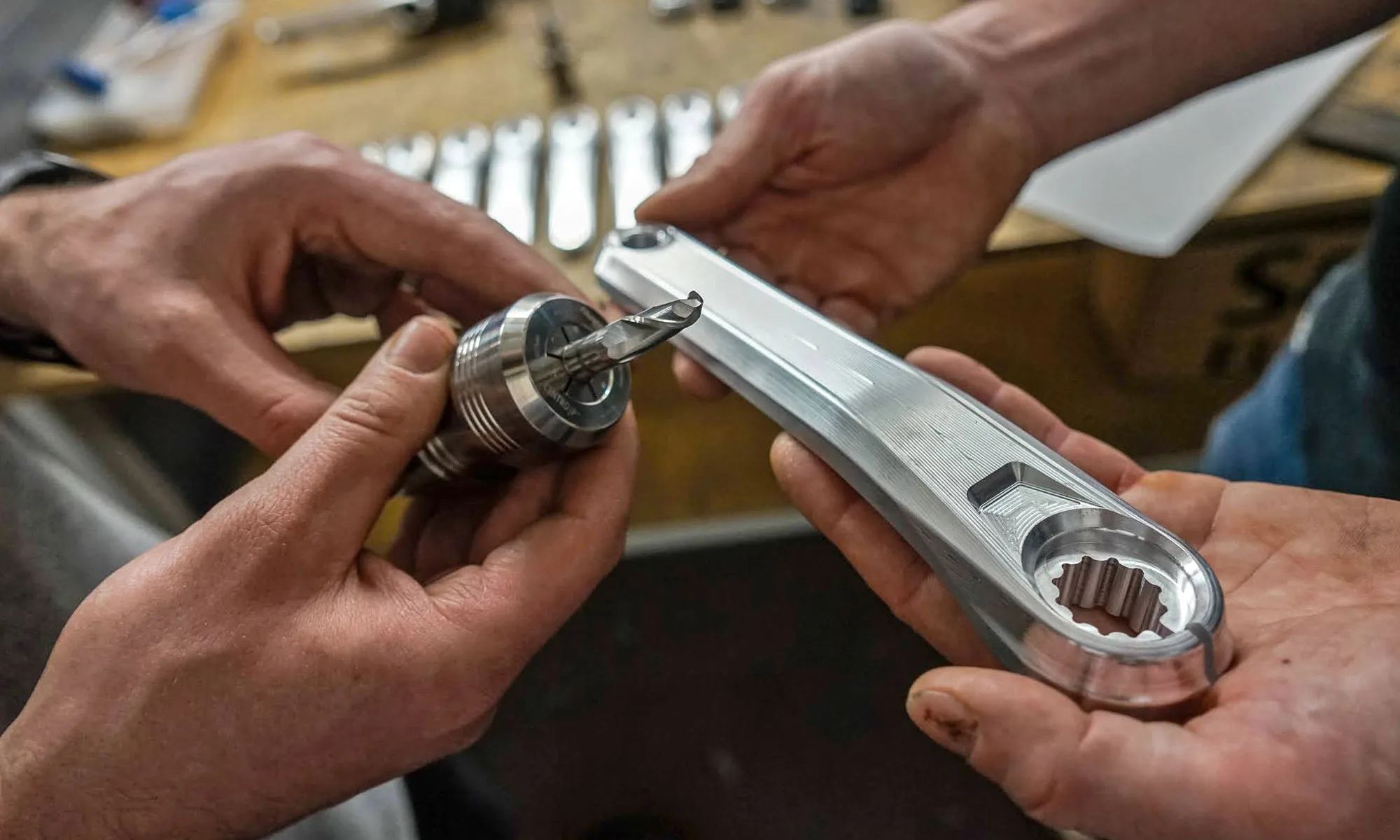
Signature X cranksets had been a giant shift in making Actofive elements extra inexpensive, from slightly below 400€.. or half the price of the unique hole Signature cranks.
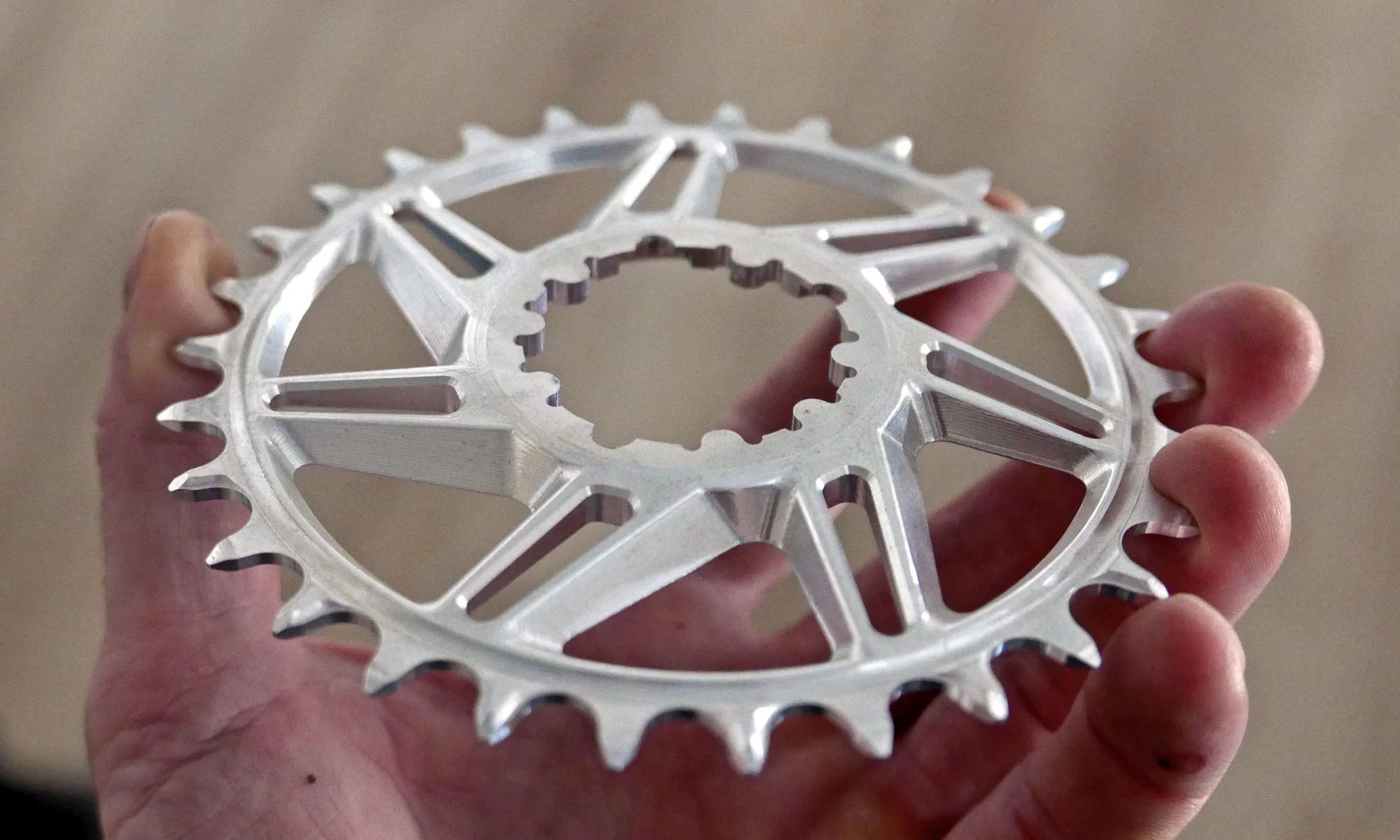
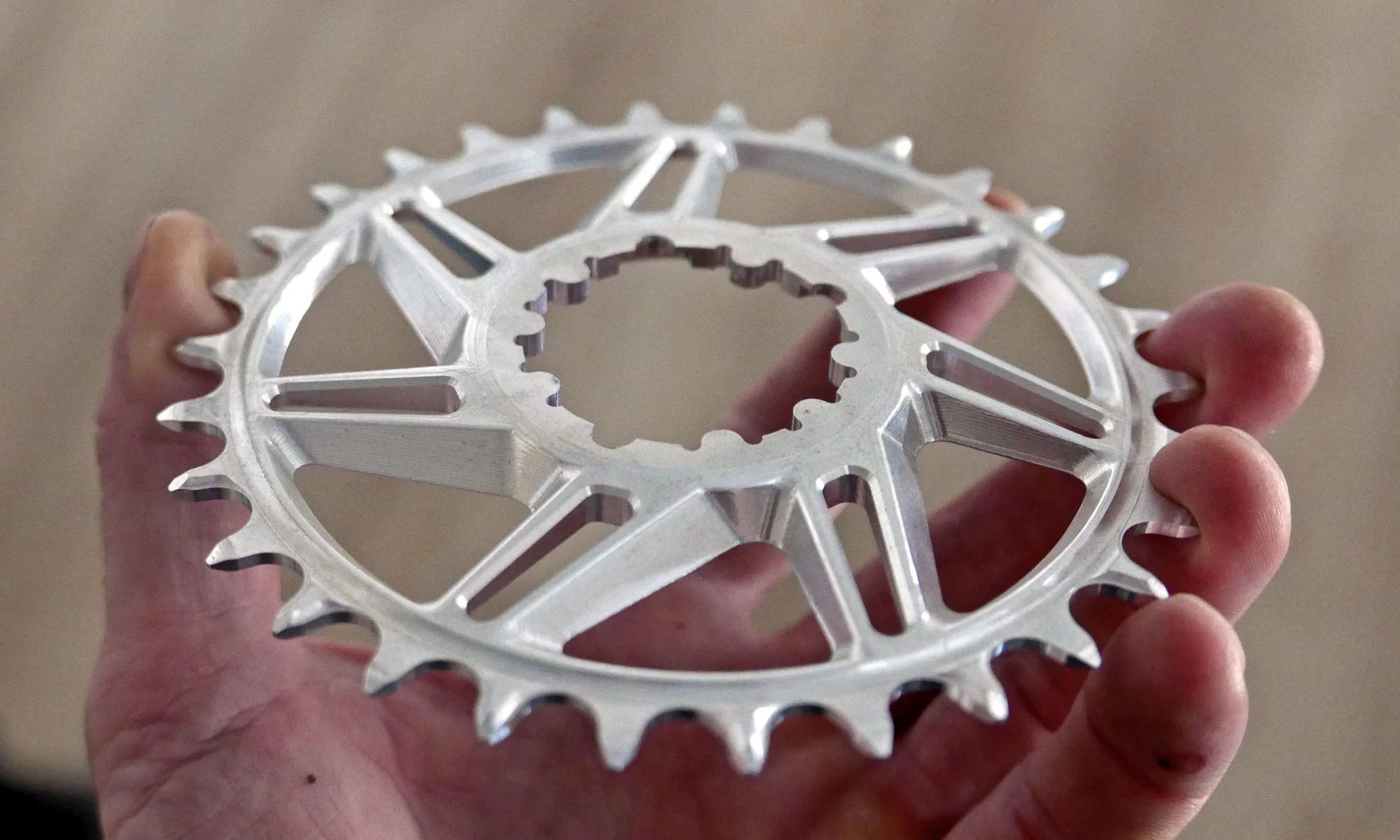
Actofive direct mount chainrings add 120-150€ on prime of that.
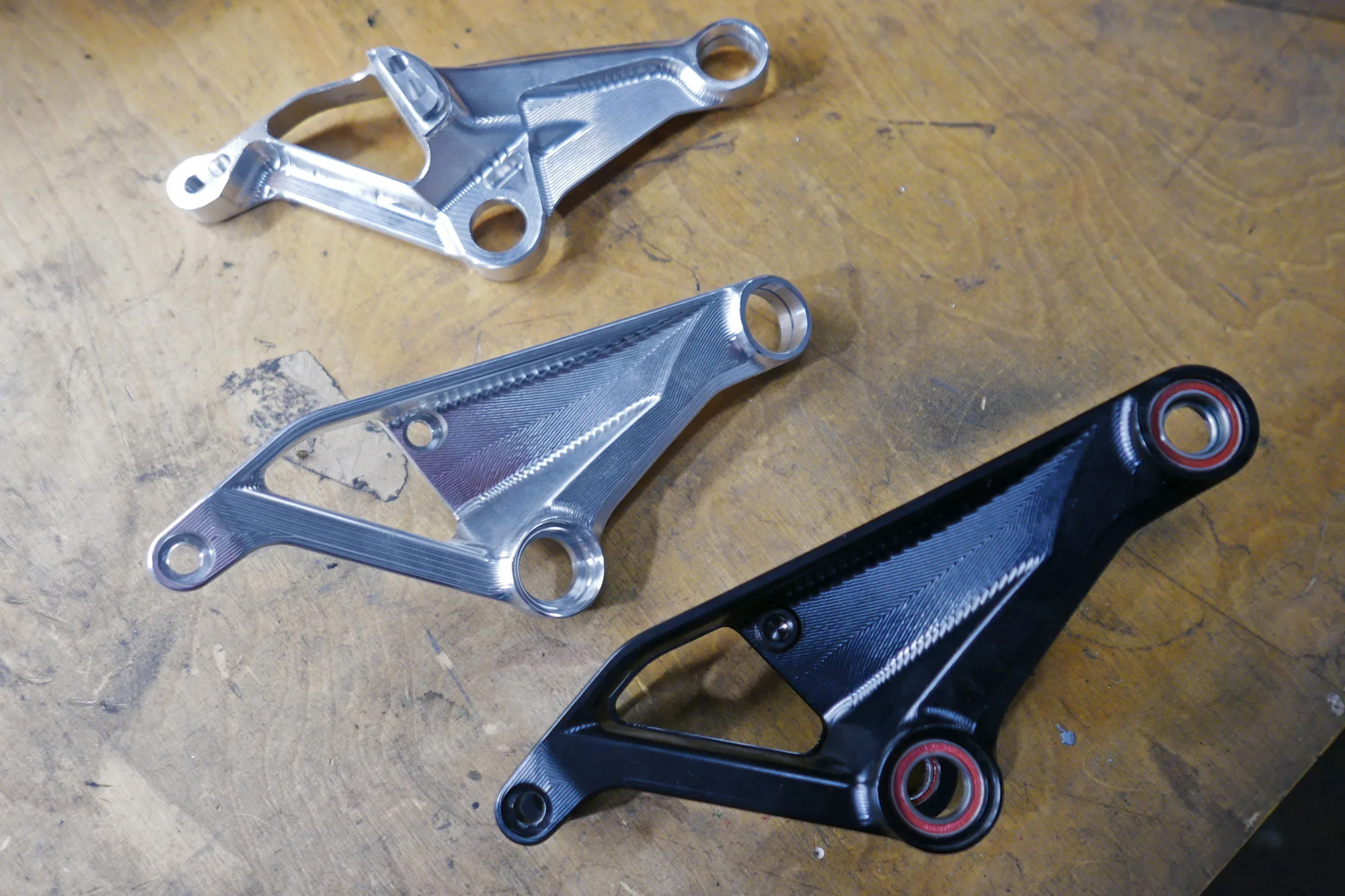
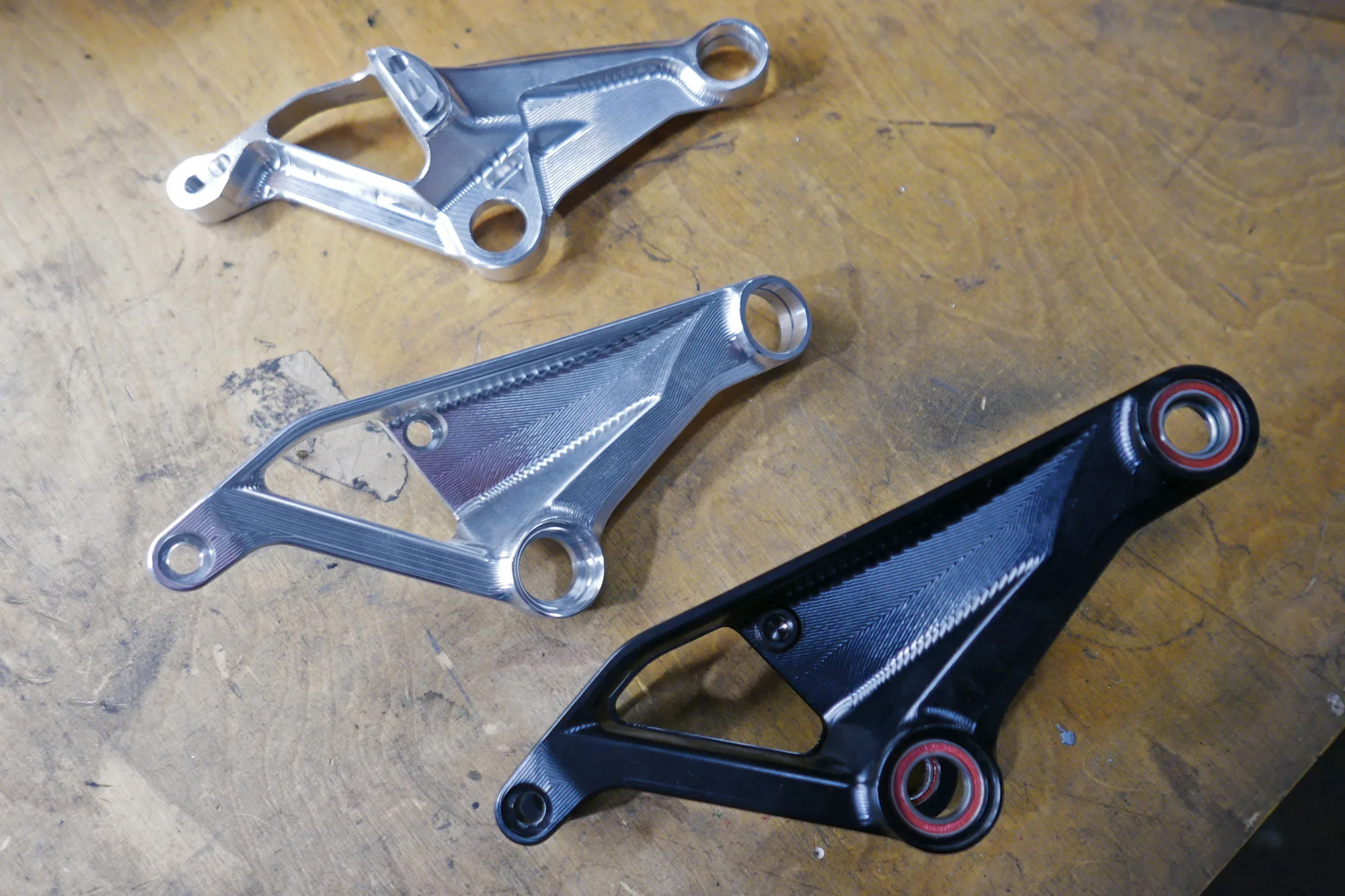
The rocker hyperlink on the I-Prepare is one other nice instance of Actofive’s artistic 2D manufacturing. Like most of their MTB elements, it’s made by merely matching two halves (from each side) which might be then joined along with a easy keyed interface and a single bolt for easy power.
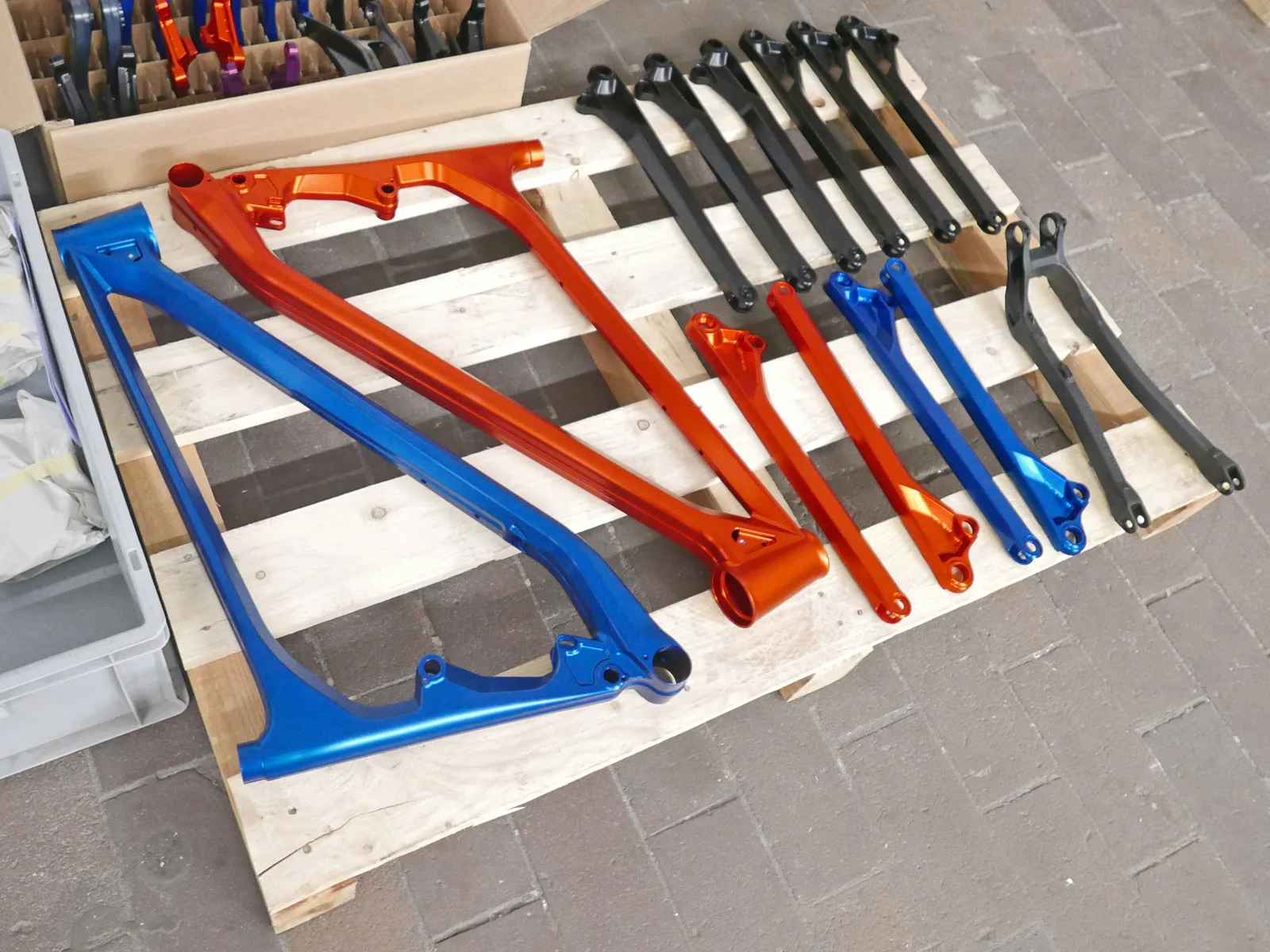
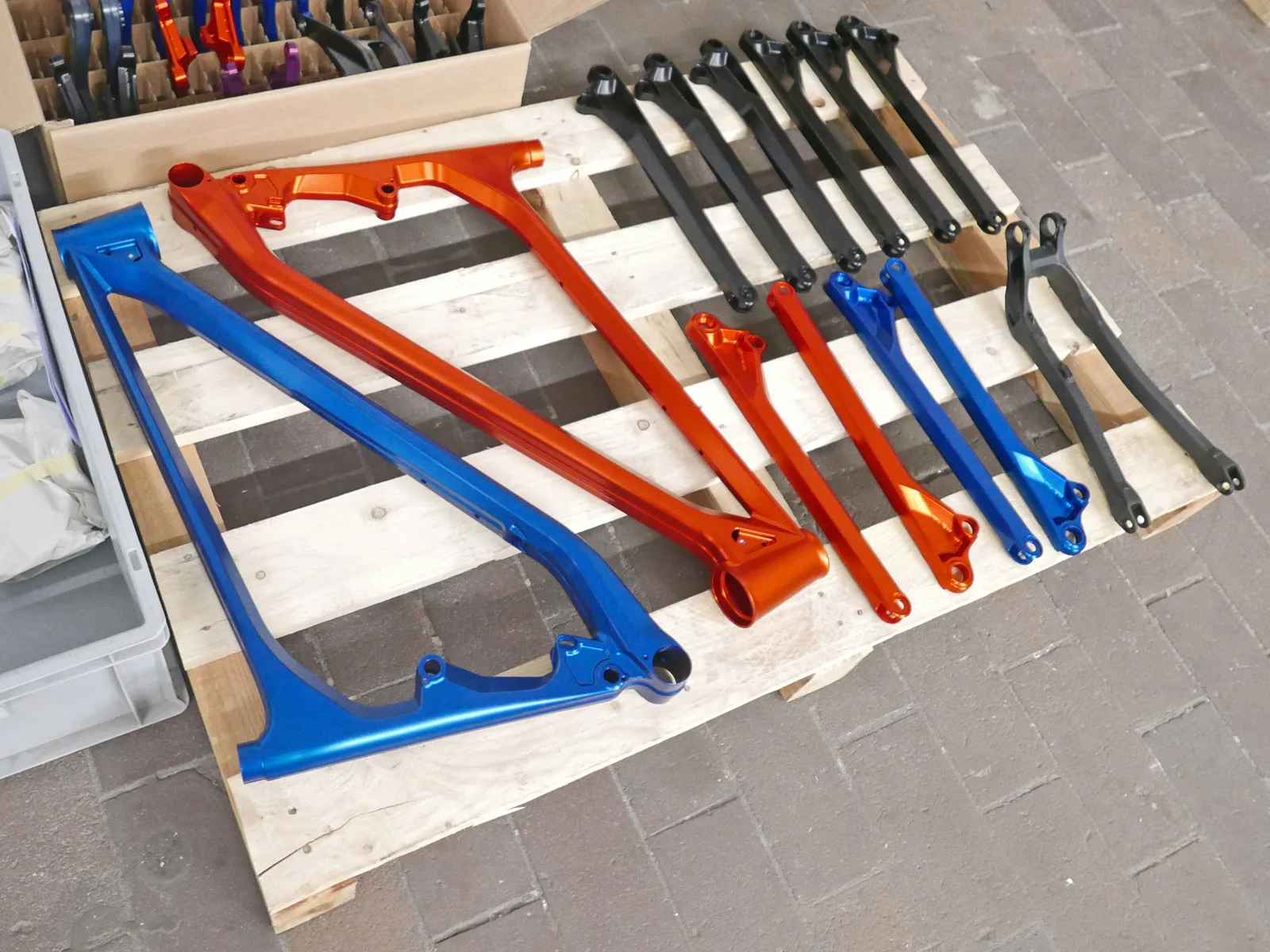
MTB frames begin from 6000€ for the easier I-Prepare body set. A P-Prepare will set you again at the very least 7000€.
Curiously, one technique to come up with an Actofive mountain bike body for a bit cheaper is likely to be to put your palms on a present demo. With Bespoked on the horizon, Actofive is providing offers of their on-line store on earlier variations of the I-Prepare that had been already proven. And they’re even providing the customized mk2 I-Prepare bike prematurely, that might be on show within the Dresden Airport present over the weekend.
Anodized eye sweet colours
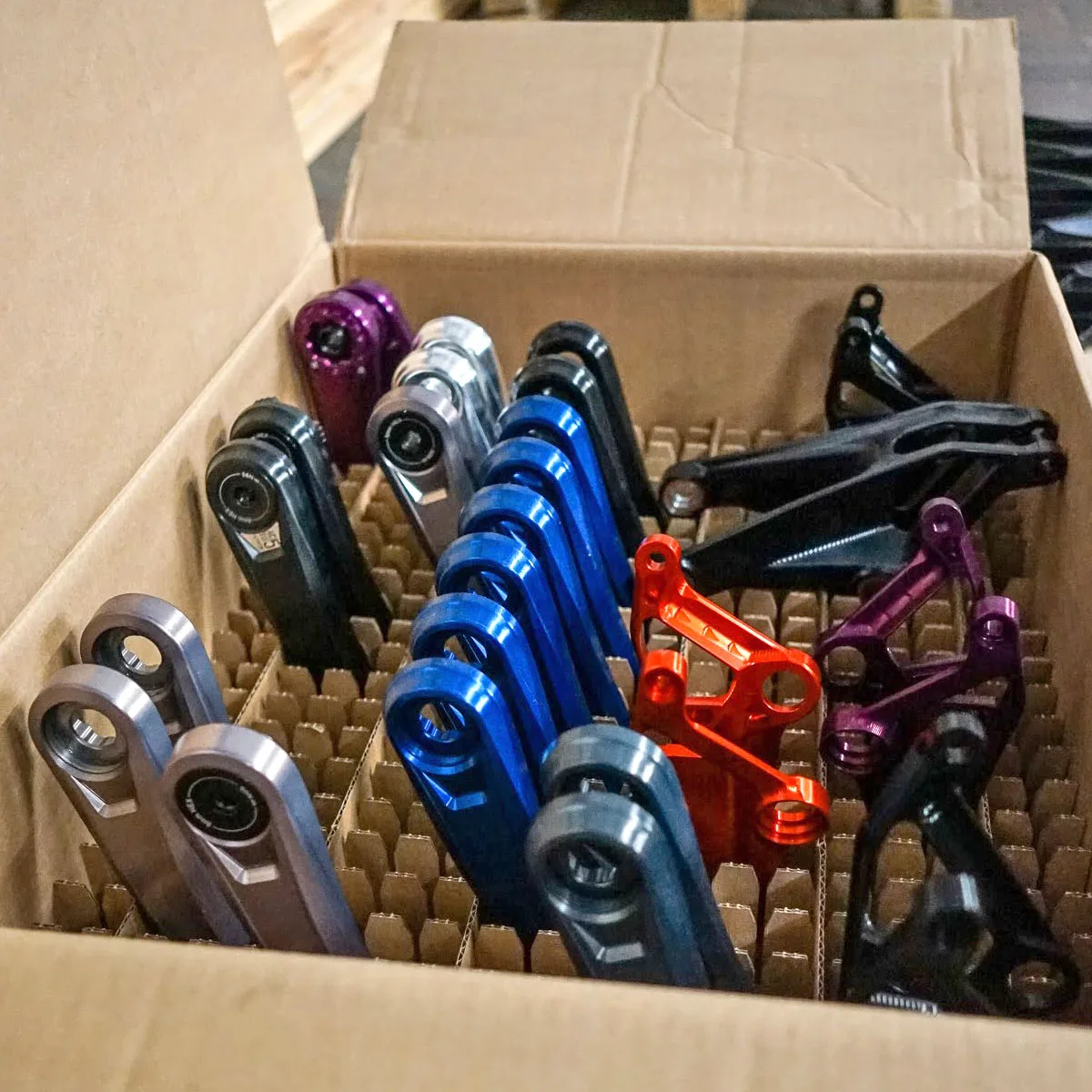
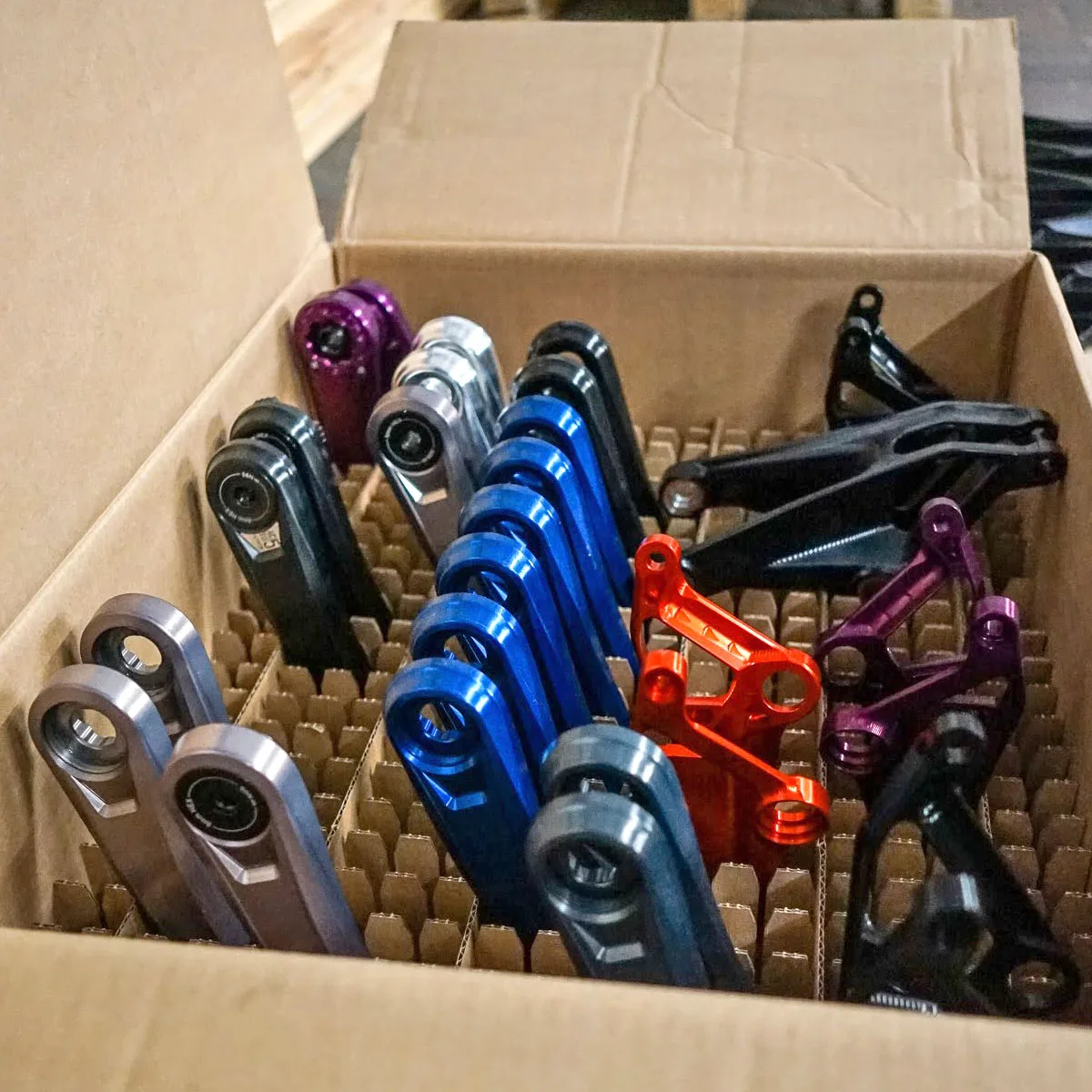
After all, one of many cool advantages of an all-machined-alloy mountain bike (or elements) is the power for some flashy anodized finishes. Actofive has a associate handle their eye-catching colours, however they will even do some enjoyable stuff with two-done finishes one facet to the opposite.
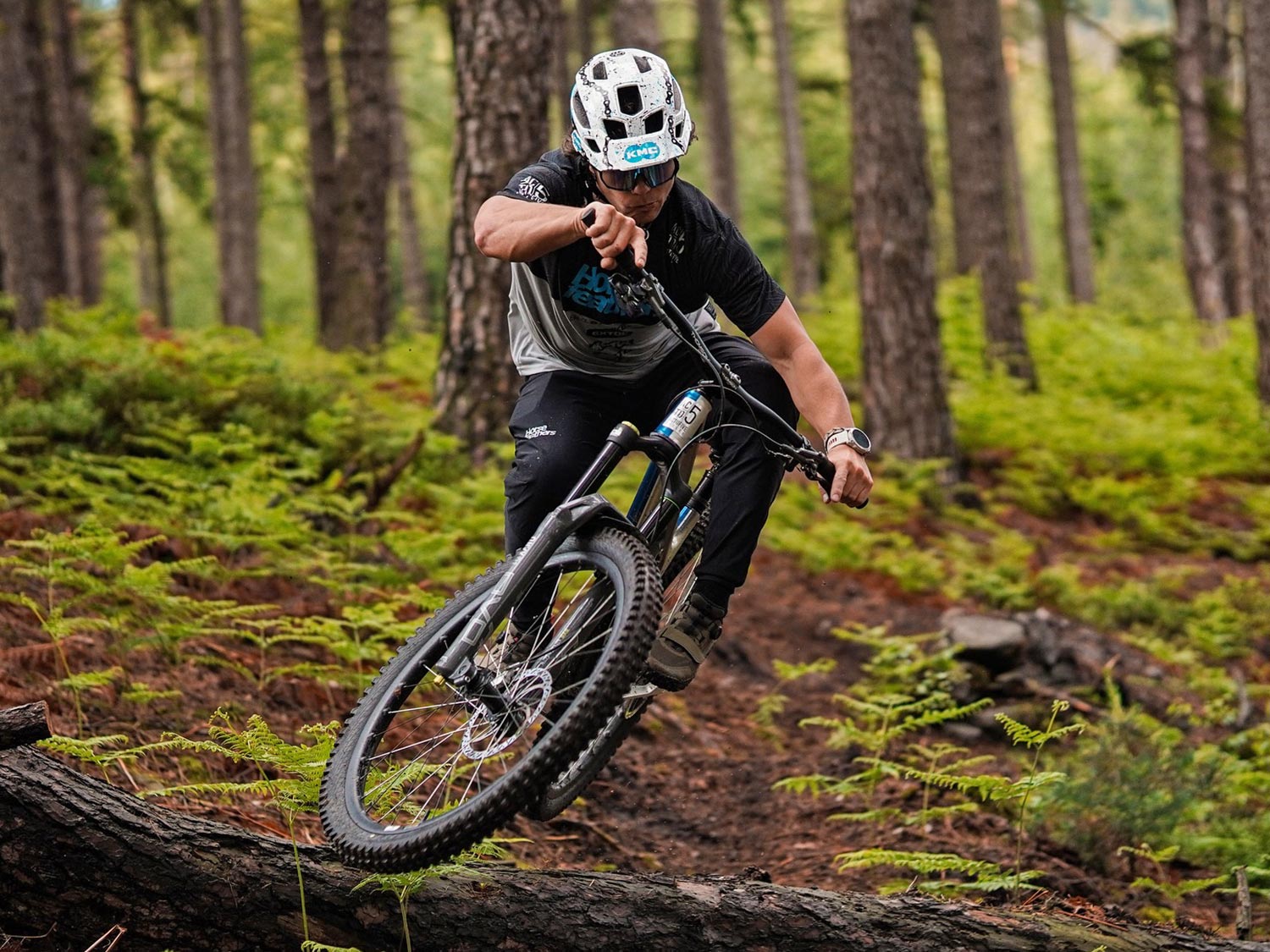
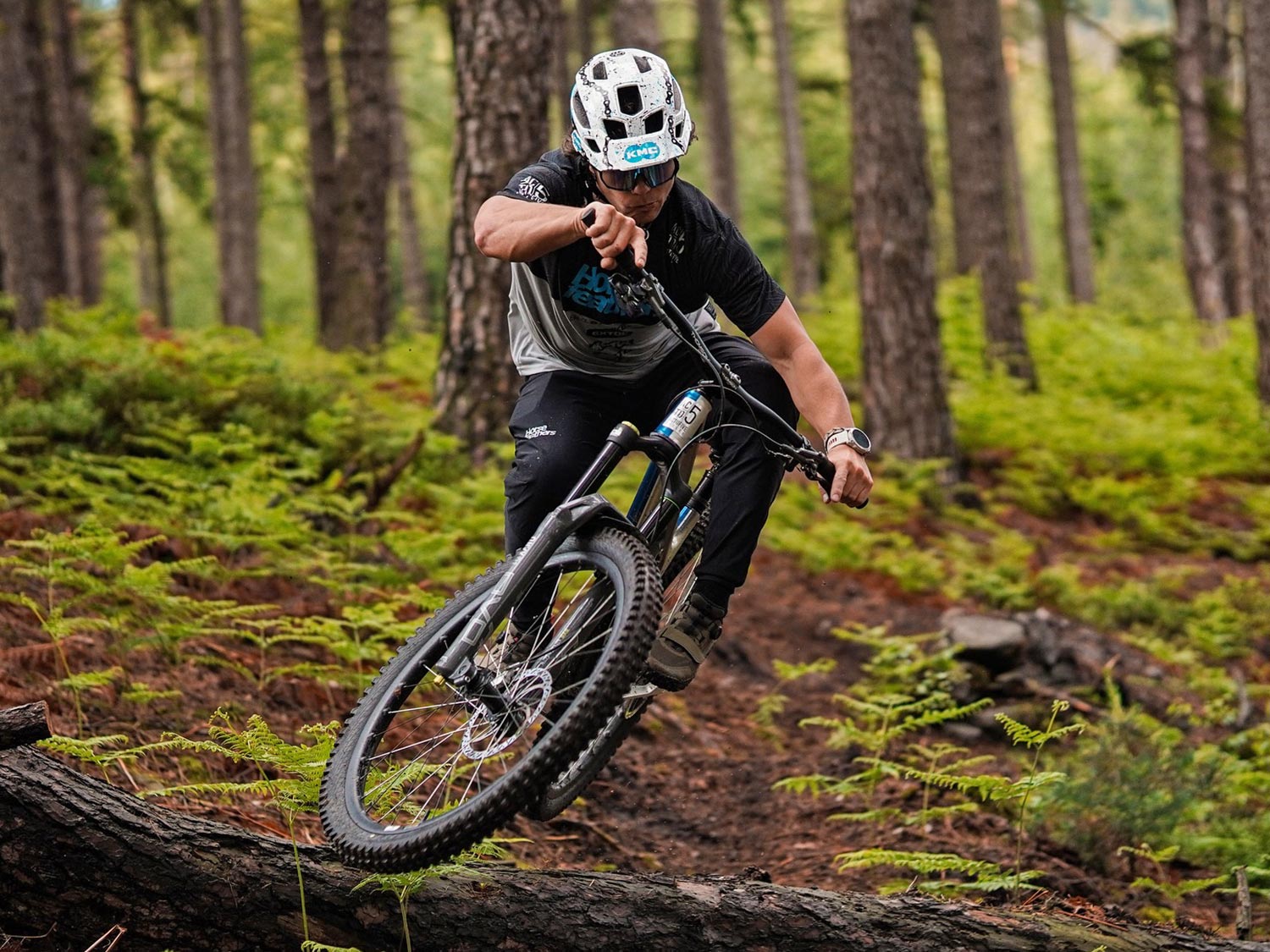
I particularly just like the half blue + half silver race bike of Czech enduro World Cup racer y Vojta Bláha/DVO who confirmed off his bike to us for the DVO Prime launch earlier this summer season.
Contained in the precise clamshell Actofive mountain bikes…
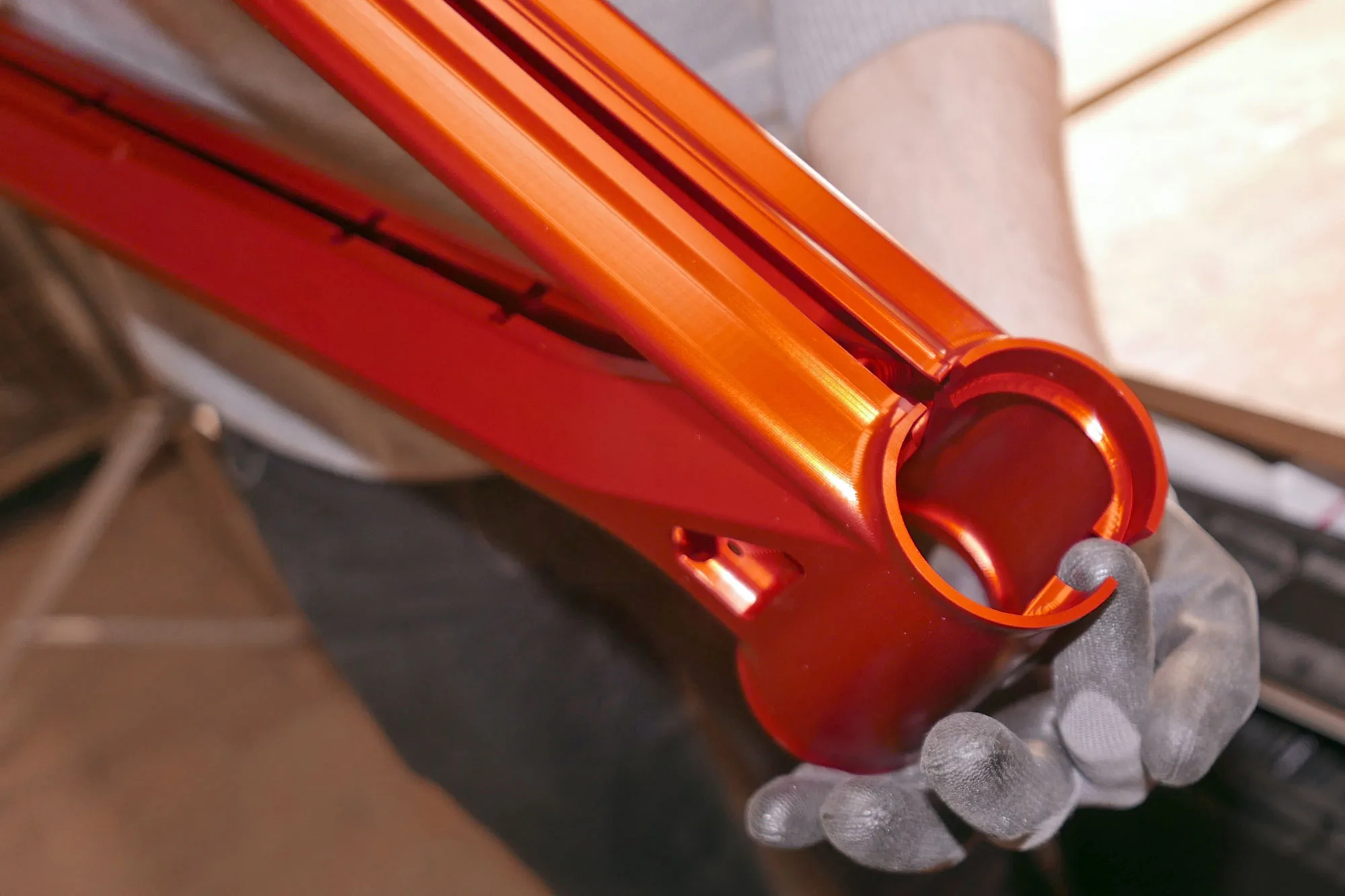
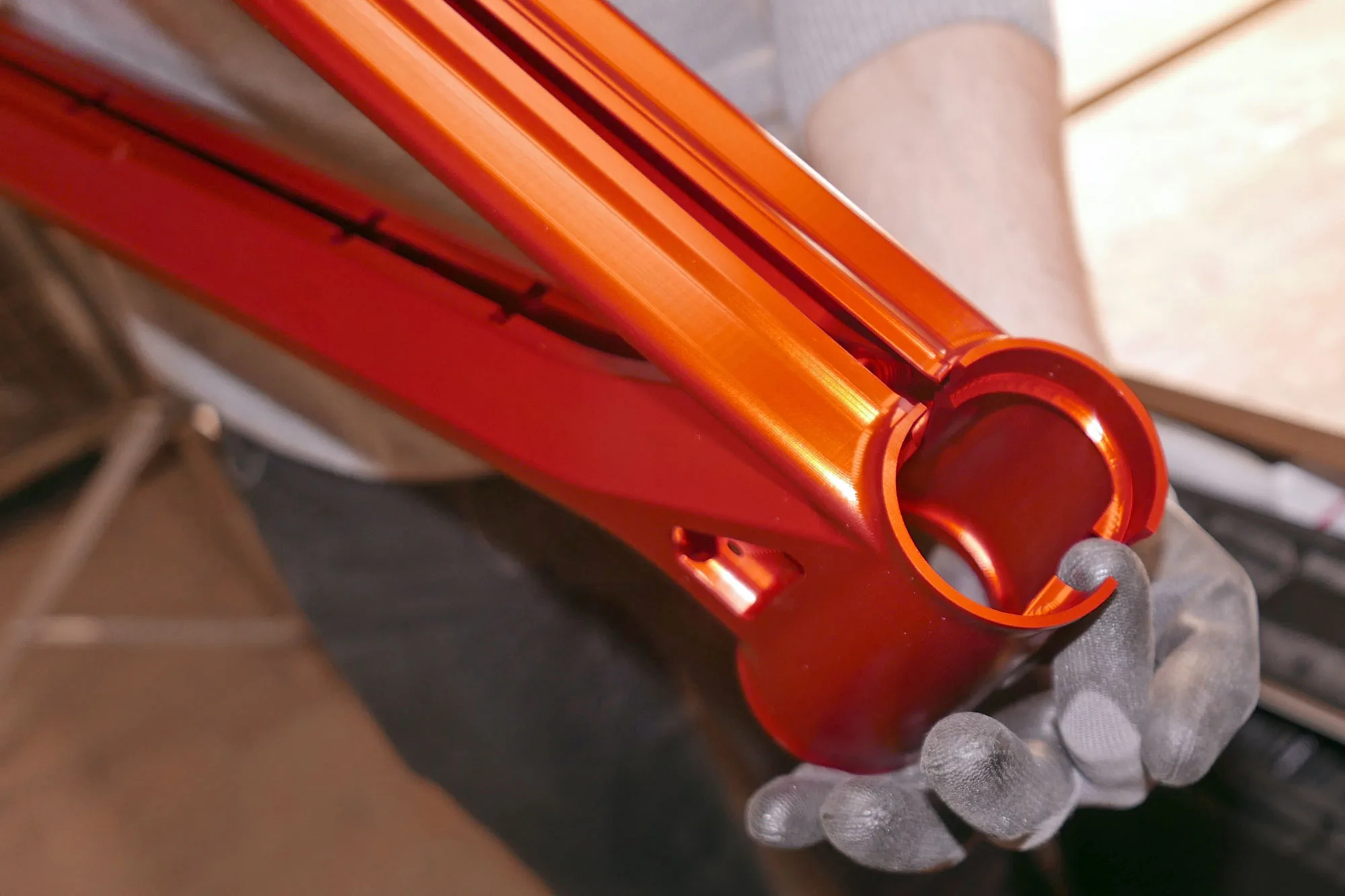
OK, so right here’s an actual uncommon sneak peek inside an Actofive…
This pink/orange I-Prepare entrance triangle is manufactured in 2 halves with a clamshell design. By machining all sides individually, Actofive can creates the precise clean outer form that they need for the bike, however can fluctuate thicknesses all through numerous sections of the body, very similar to you discover with butted tubing.
However in actuality, the within of the I-Prepare is far more complicated that that, that includes a sequence of reinforcing webs that change the tube wall thickness far more than might be achieved by any tube-to-tube type development.
After which the true secret comes with the mechanically overlapping finger joint from one facet of the body to the following. This tremendously will increase the floor contact space between the 2 halves, leading to a robust bond when the body is assembled with adhesive. And it additionally reinforces the joint on the prime and backside edges of the body, defending it towards impression with rocks or different obstacles.
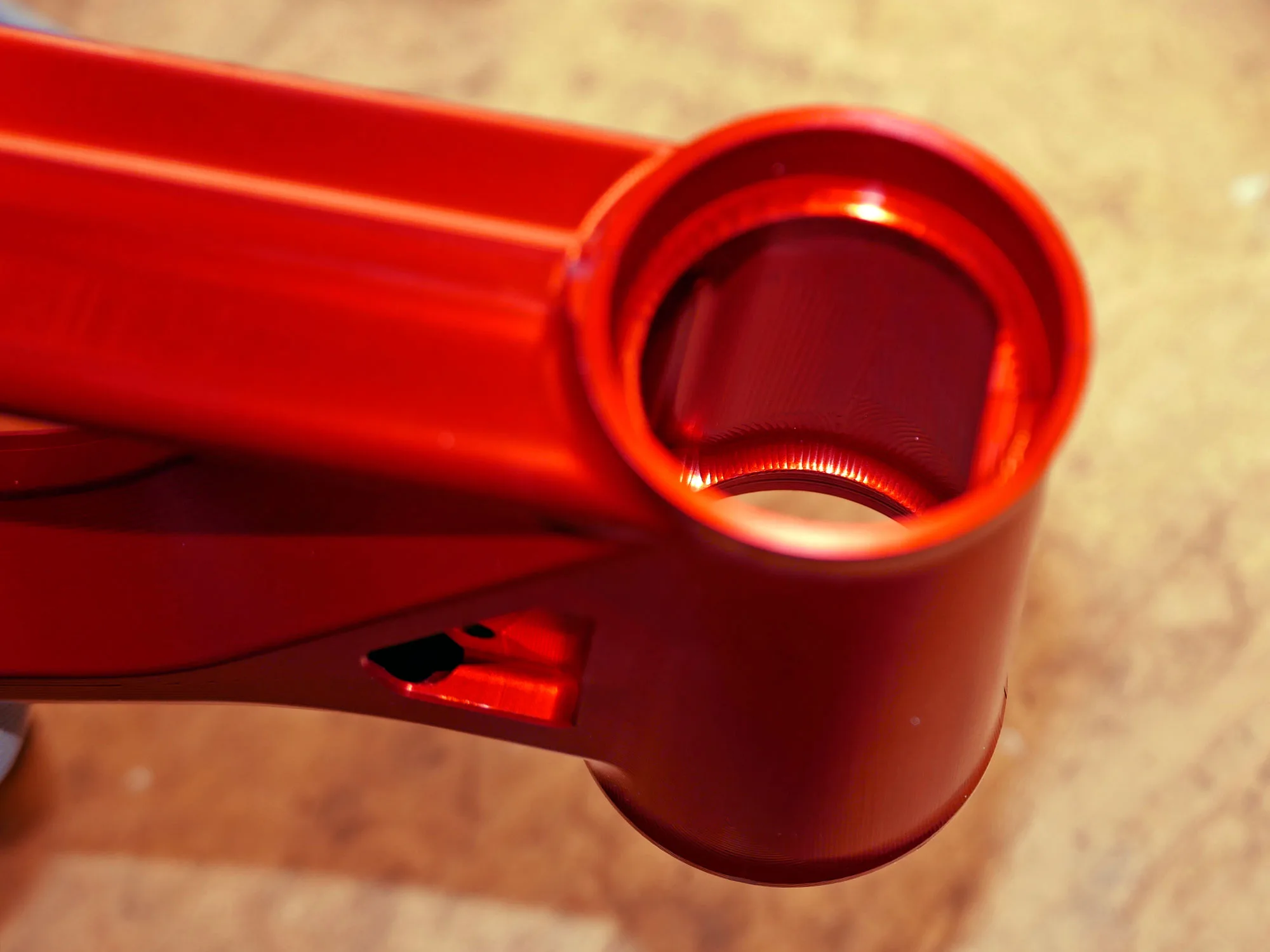
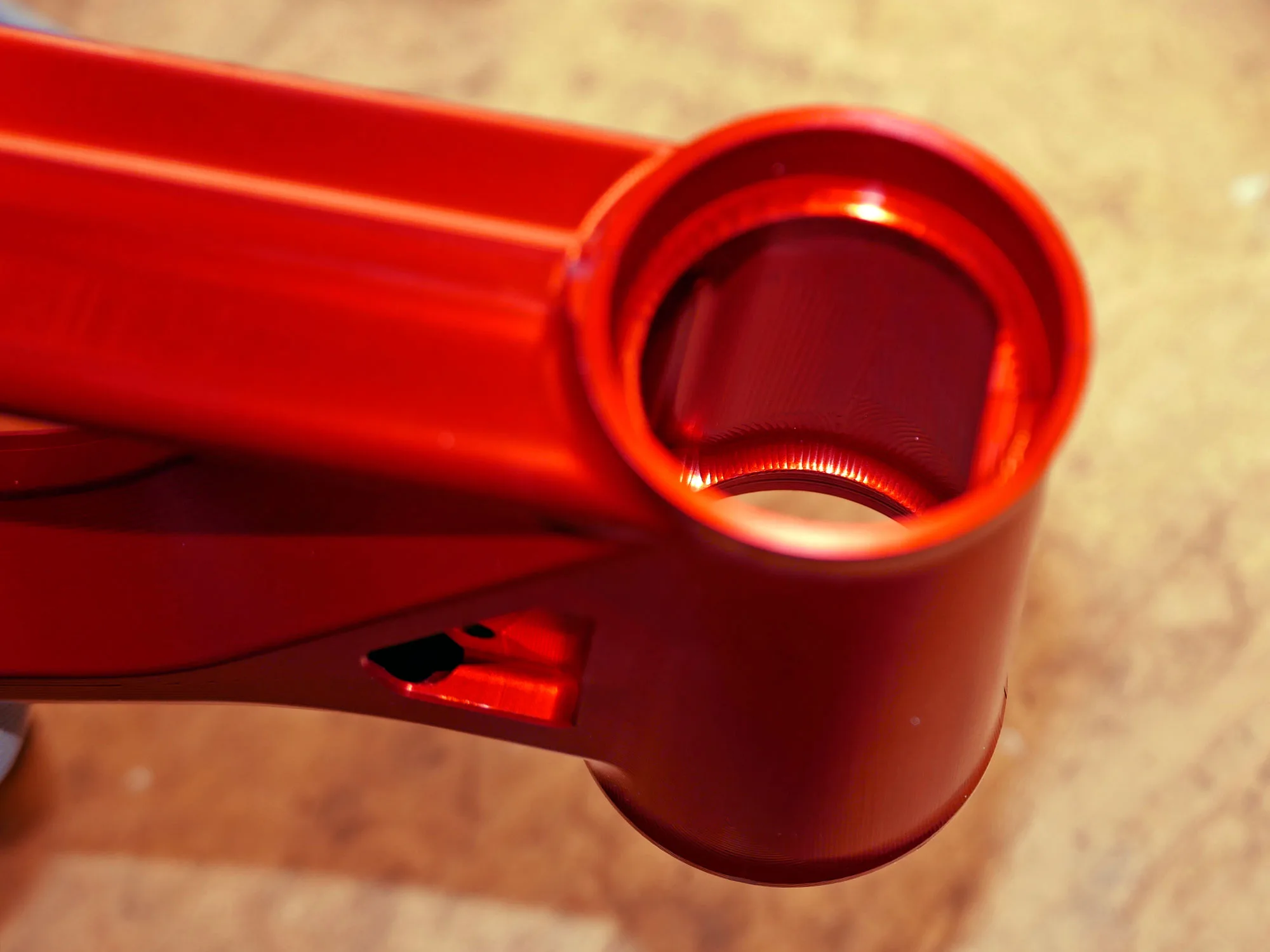
One factor I actually love about Actofive’s bikes is how one can see the machining marks that present how the CNC tooling cuts forwards and backwards into the aluminum billet. However after all, since they machine the within of the body simply as a lot as the skin, our Actofive manufacturing unit tour additionally gave us an up-close glimpse at how these software paths are even seen inside the body.
Like on the within of this I-Prepare’s headtube.
What comes subsequent for Actofive?
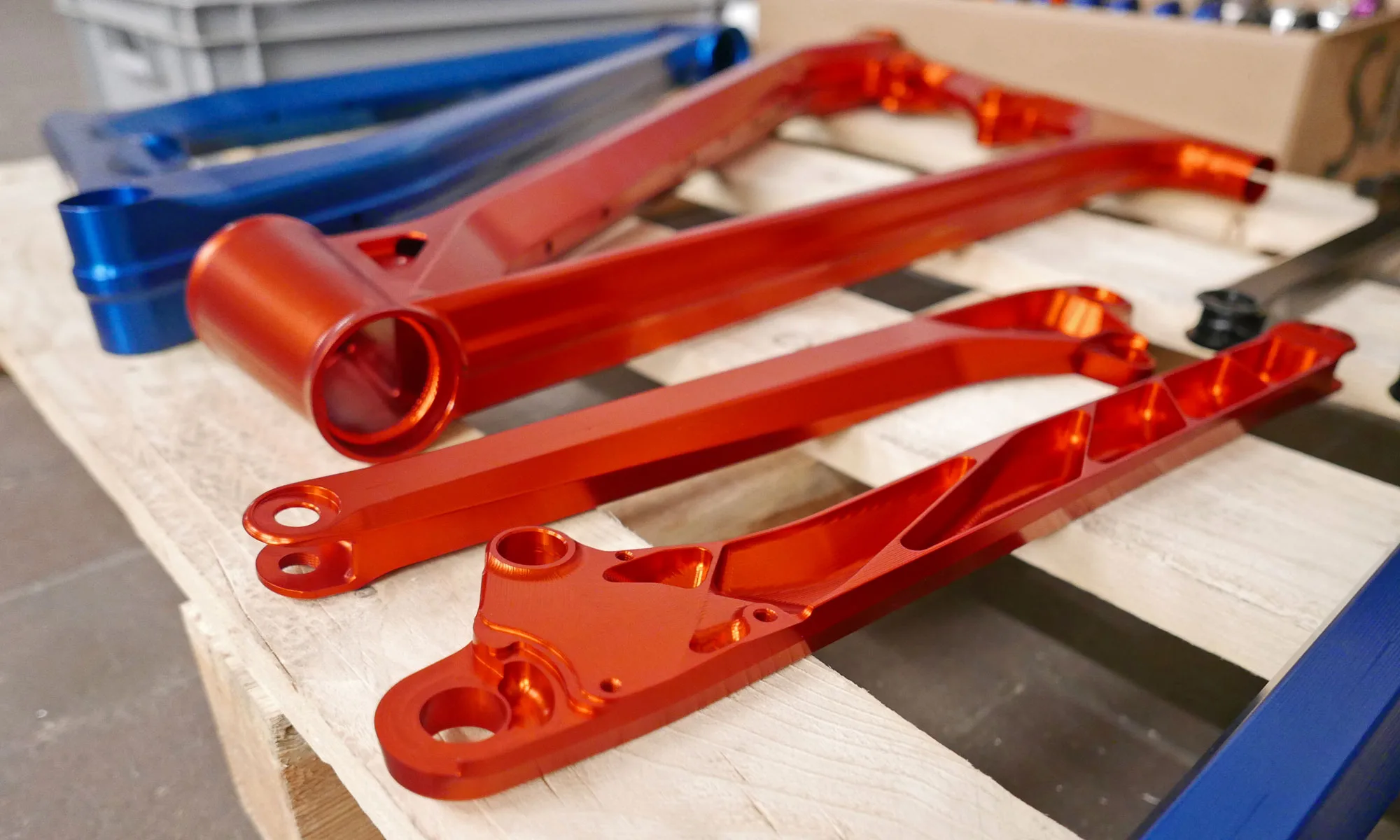
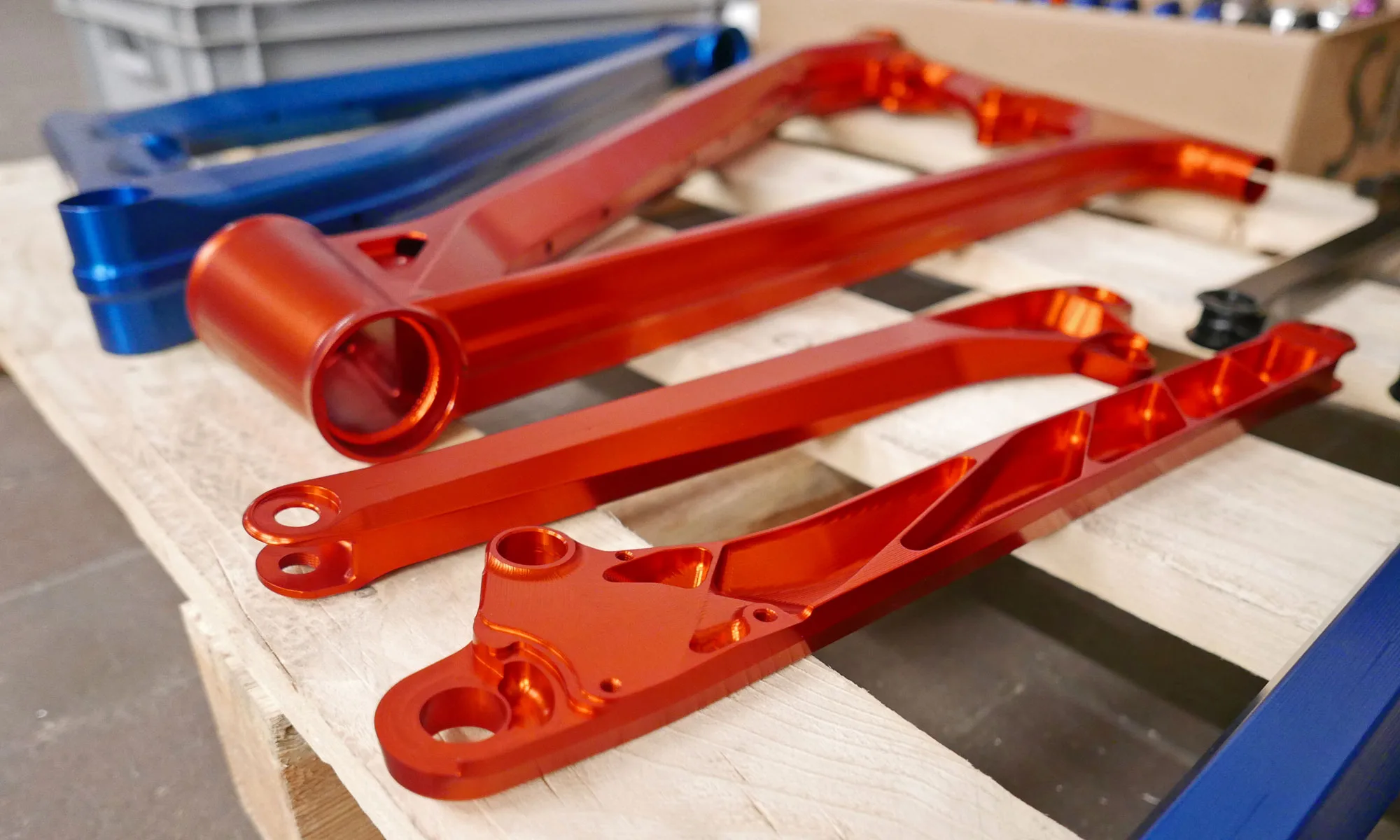
That was just about it for our Actofive manufacturing unit tour. We acquired to observe some Signature X cranksets be machined – 60 crank arms at a time in that batch. And Simon revealed us a little bit of what was coming quickly this yr. Suppose UDH compatibility throughout all frames, after all, together with the power to retrofit all the frames they’d beforehand produced. And these newly machined, open-back seatstays that changed the I-Prepare’s authentic welded tubing stays.
Plus, there’s much more that we are going to see over the approaching searching for with extra next-gen P-Prepare & I-Prepare updates.
Keep tuned for that!
Actofive after darkish
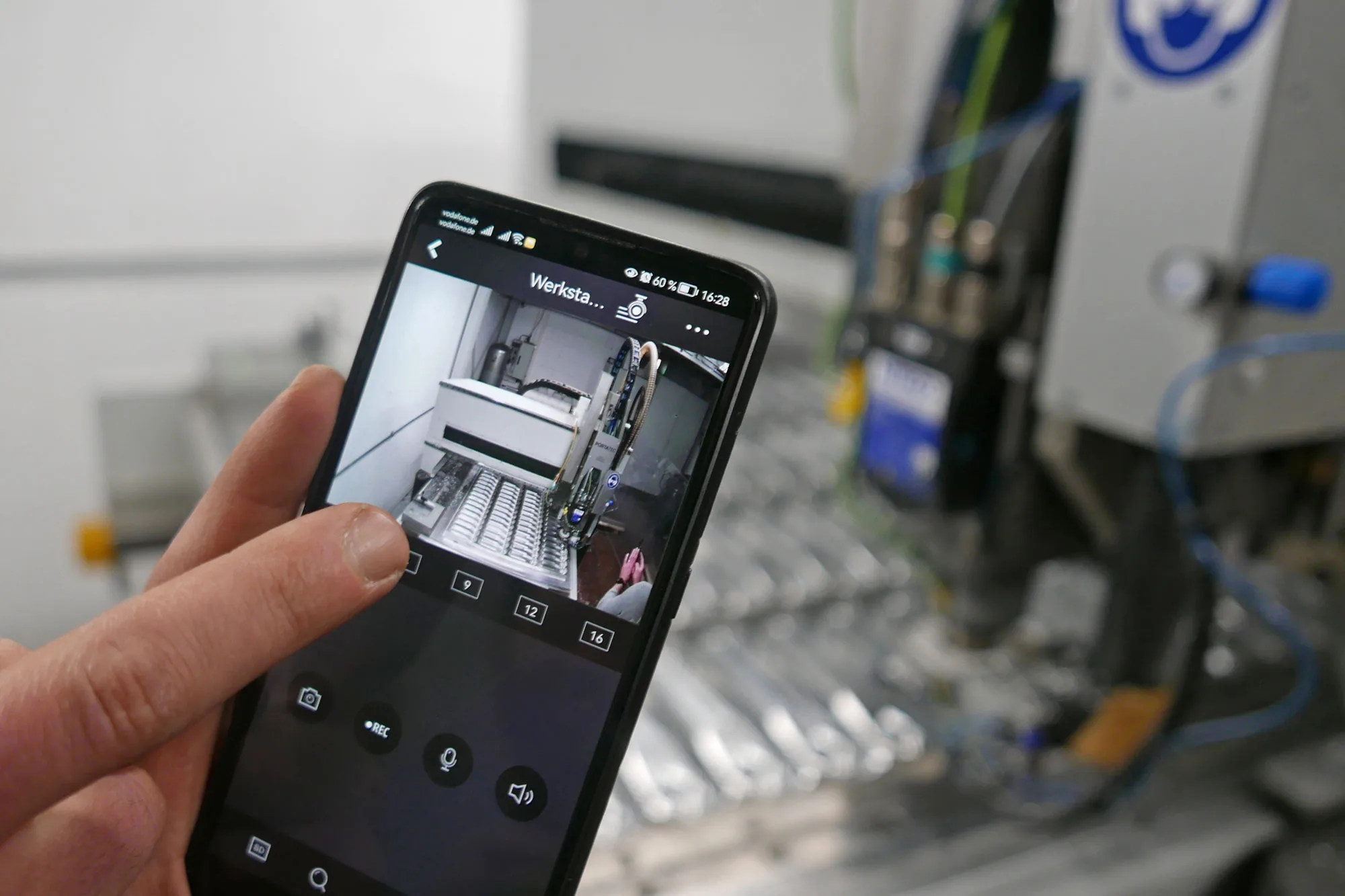
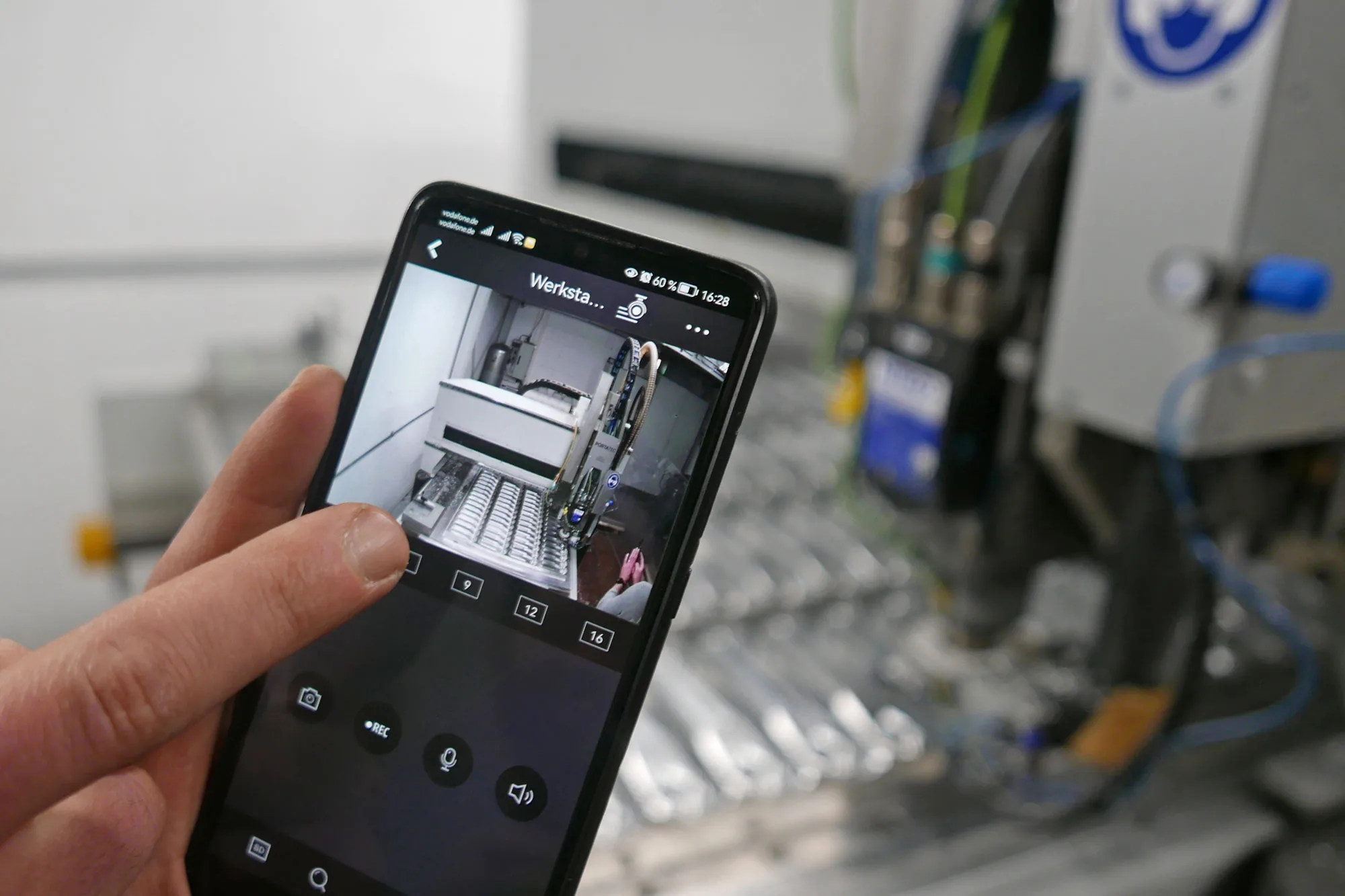
And with that, we’ll depart you with Actofive ‘After Darkish’.
A lot of Actofive’s CNC-machining processes take 8 hours or extra to finish. So Simon tries to schedule it in order that he can arrange a machining activity on the finish of his workday, to run in a single day. And he’ll typically even decreasing software speeds a bit to make sure much less probability of any hassle when the machines are left to work on their very own.
Actofive has a webcam within the machining room so Simon can dial-in to maintain tabs on progress – whether or not he’s upstairs working at his desk on one other venture, or again residence for the night time.
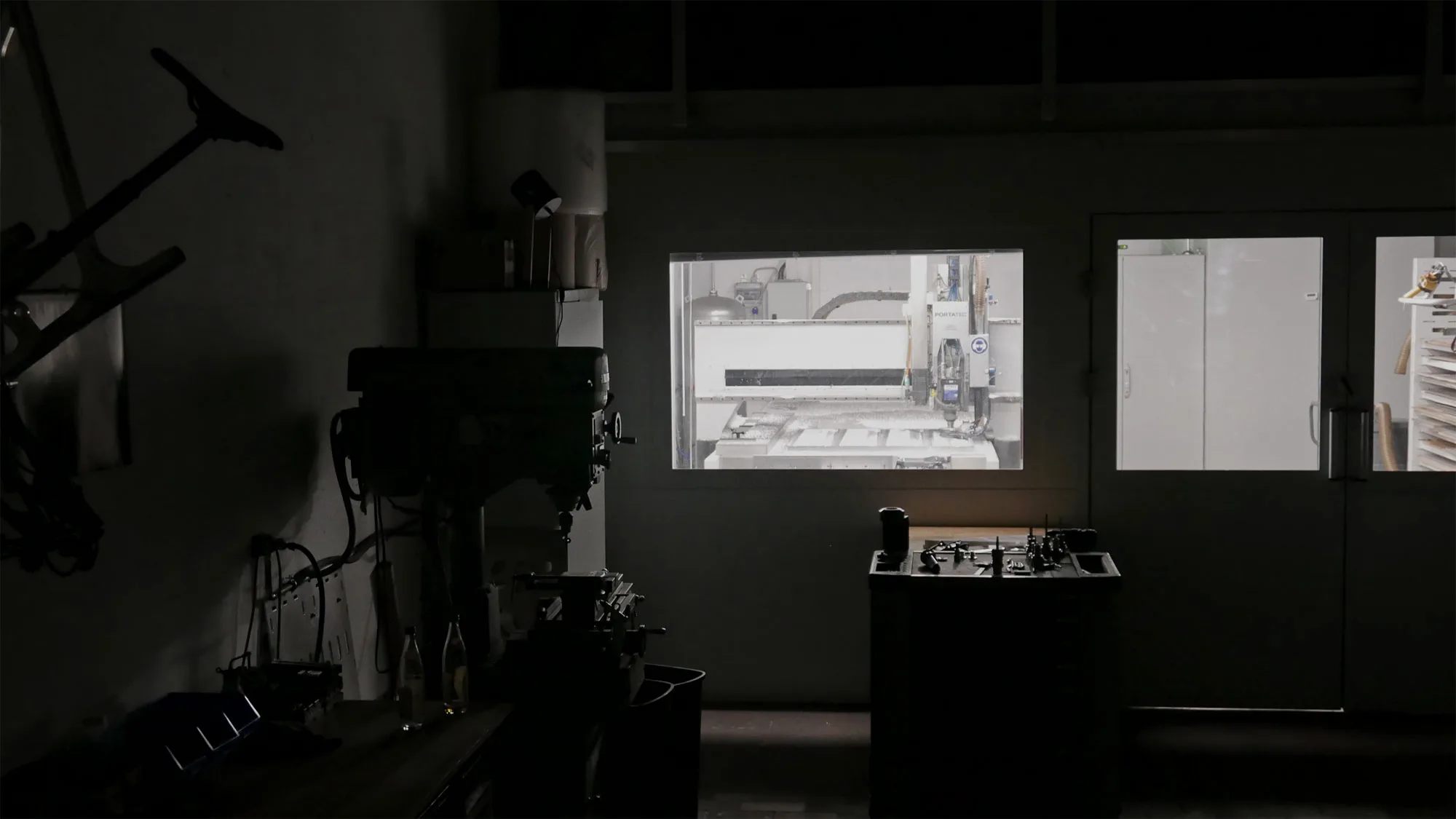
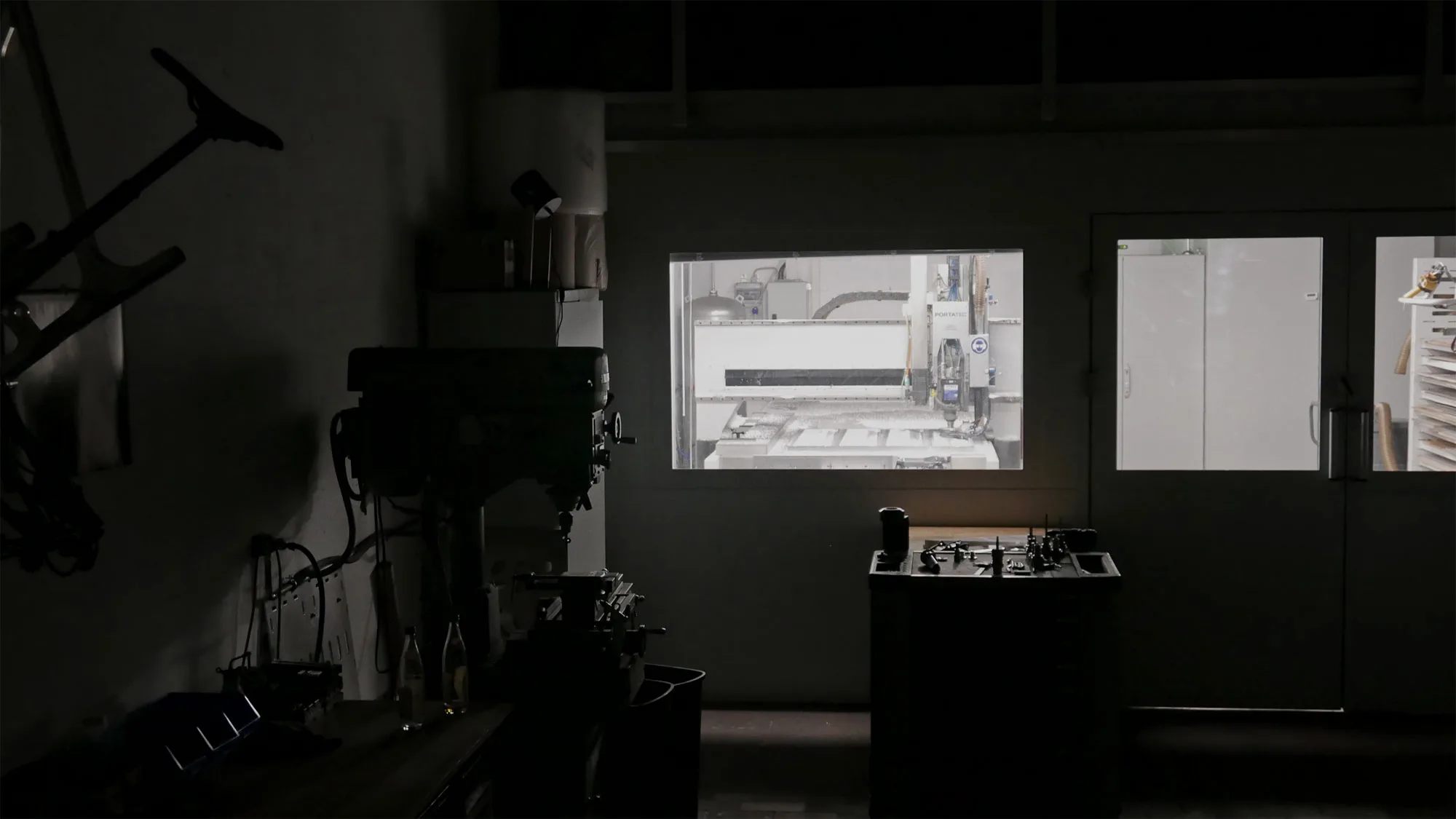
And whereas the lights exit within the human facet of the Actofive workshop, the sunshine typically stays on all night time because the CNC robotic chugs away, machining mountain bikes by way of the lonely night time.