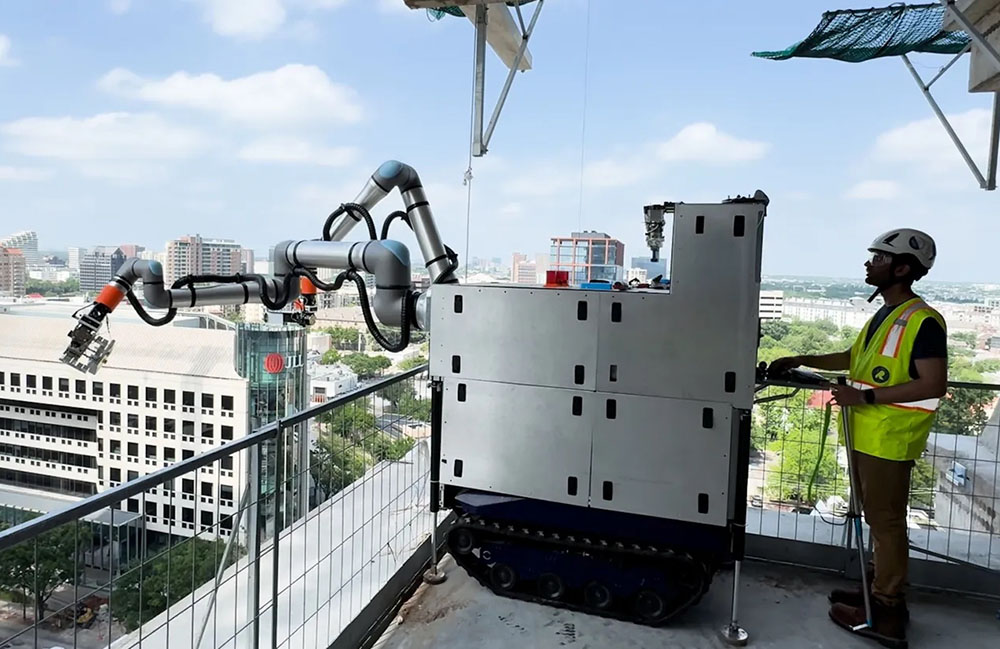
Common Robots and Increase Robotics mentioned the autonomous system pays for itself inside one 13-floor venture. | Supply: Common Robots
As much as 1,000 ft. into the air, development employees want intensive security rigging to put in glass panel brackets. This important process not solely places workers at risk, nevertheless it’s additionally repetitive and boring. To maintain employees protected and permit them to do extra high-value work, Harmon Inc., a U.S.-based glazing firm, is automating the method with expertise from Increase Robotics and Common Robots A/S.
Harmon is an early adopter of this expertise, and thus far, mentioned it has seen a quick return on funding (ROI). As well as, the Bloomington, Minn.-based constructing façade firm mentioned the robotic system has improved employee security, in addition to consistency and precision in set up. The three companions mentioned the robots present a 3x multiplier on guide labor and supply a payoff inside one 13-floor venture.
Historically, to put in fasteners for glass façade panels on high-rise buildings, employees must align, drill, and torque brackets in place to express specs, all whereas hanging off the facet of a constructing. Not solely is the job not ergonomic, however there may be additionally a big likelihood for harm if a device or bracket falls to the bottom under, the place different employees could also be.
“Security is at all times first in thoughts,” mentioned Don Birmingham, common superintendent at Harmon. “If you happen to can effectively do a job and take all the security dangers out of it, I feel any contractor would join that. So far as the employees, I feel they’d a lot slightly be contained in the handrail working a robotic than hanging off the sting of the constructing.”
Increase Robotics makes use of two UR20 arms
Increase Robotics makes use of two UR20 collaborative robotic arms from Common Robots for the modern development platform. The San Francisco-based firm has mounted these two cobots on every cellular robotic base. The small footprint and management containers of the UR20 make them simple to combine right into a cellular utility.
“As a result of Common Robots has achieved an important job of creating their arms very power-efficient, in addition to making it simple to combine right into a DC energy resolution, we are able to immediately join our arms to the battery and have our robots working absolutely, wirelessly on a development website,” mentioned Gary Chen, co-founder of Increase Robotics.
As well as, the UR20’s IP65 ranking supplies confidence for Increase’s clients in utilizing the robots even in inclement environments together with mud and rain, in addition to excessive temperatures. The corporate has run the robotic efficiently from 20°F under zero as much as 120°F.
To develop its system, Increase mentioned it used all kinds of assets from Common Robots, together with on-line technical documentation and help by way of myUR. It additionally used the boards on each the Common Robots web site in addition to their GitHub.
“Assist from UR has been implausible,” famous Conley Oster, the co-founder of Increase Robotics. “Any points that we bumped into or any questions that we had early on, we had a devoted functions engineer from UR that was in a position to assist us. The UR group and boards have been extraordinarily useful to us as effectively. We have been at all times in a position to provide you with an answer in a well timed method.”
Harmon says robotics reduces guide necessities
Harmon reported numerous enhancements since deploying the Increase Robotics system. For instance, the guide set up course of for façade brackets usually requires two to 4 employees. As compared, the robotic requires just one particular person to handle it per set up location.
“It’s a 3x multiplier on conventional labor,” mentioned Oster. That multiplier supplies quick ROI for the robotic, usually offering breakeven for the robotic at about 13 flooring based mostly on a month-to-month lease and amortizing the robotic throughout the variety of installations on every flooring.
The system didn’t simply work quicker than guide labor; it was additionally extra correct, exact, and constant, the businesses mentioned.
“In guide installs, round 30% of all fasteners usually aren’t put in in the suitable spot,” Oster mentioned. “Utilizing a robotic like ours at the side of whole stations permits us to precisely place fasteners on the constructing’s edge or inside the constructing’s core. We are able to set up inside plus or minus three-sixteenths of an inch, which is much superior to what we’ve seen in guide installations.”
Lastly, the system additionally consists of software program that gives fast perception and historic logs of on-site information. This provides actual torque values and alignment for each bracket in actual time, versus random high quality inspections which are usually achieved a number of occasions on every flooring.
Harmon had “as-built” information, which allowed its staff to regulate anchor positioning earlier than the glass partitions have been put in.
“I feel probably the most profit we received was the experiences of the place the anchors have been put in,” Harmon’s Birmingham mentioned. “The earlier we discovered any deviations past specs, the simpler it was to remove them going ahead.”
Register right now to save lots of 40% on convention passes!