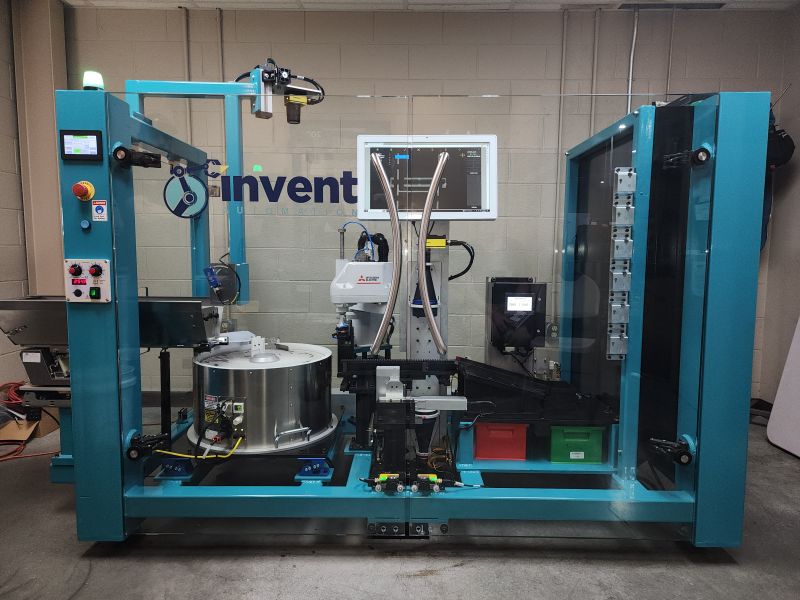
Invent Automation has built-in CapSen imaginative and prescient expertise as DENSO automates. Supply: Invent Automation
Automotive manufacturing has lengthy benefited from the considerate deployment of robotics and automation, and for good motive. Among the many many advanced manufacturing processes, some will be too troublesome or too tedious to be accomplished safely and effectively by human employees. In consequence, industrial automation applied sciences can add large worth to unique gear producers and automotive components suppliers alike in some ways. For instance, main world automotive components producer DENSO just lately sought to automate a bodily difficult and repetitive tote-handling activity.
As an alternative of letting workers proceed to load and unload giant stacks of heavy totes to and from a paint sales space (Determine 1), the firm partnered with CapSen Robotics, which custom-made its 3D imaginative and prescient, movement planning, and management software program to swimsuit the duty.
DENSO additionally partnered with methods integrator Invent Automation to develop a system that will streamline the method and permit workers to contribute on the plant flooring in additional precious, much less physically-demanding methods. The exercise contributed to DENSO’s broader efforts to enrich human work with automation for improved workforce member and firm efficiency.

Determine 1: Massive, heavy totes stuffed with automotive components are carried to and from a paint sales space on a conveyor, the place a cobot picks and place totes as a part of an automatic course of. Supply: Invent Automation
Gone in (beneath) 60 seconds at DENSO
As a part of DENSO’s operations, automotive components are painted with a low gloss, charcoal-colored paint that visually smooths out the floor for a cleaner look whereas additionally serving to to soak up gentle and scale back glare contained in the car.
Within the earlier setup, workers stacked six totes filled with plastic automotive components onto a conveyor that have been then introduced to an operator who would manually take away the components and put them right into a paint sales space station (Determine 2), then pack them again into the totes. An worker would stack or de-stack a tote each 30 seconds, day in and day trip.
This repetitive movement was recognized as an automation alternative, which might unlock workforce members to carry out extra impactful work. Nonetheless, format constraints on the store flooring made conventional types of automation troublesome, resulting in the creation of a compact and versatile system.
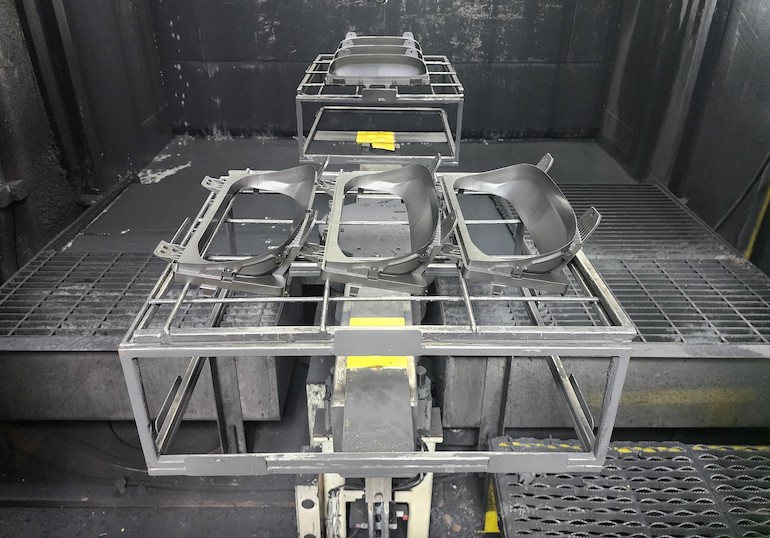
Determine 2: Automotive components are dropped at a paint sales space, the place they’ll be sprayed with a low-gloss paint that smooths out the floor and helps take up gentle contained in the car. Supply: Invent Automation
With the brand new system, an inbound conveyor transports totes of unpainted objects to a six-axis collaborative robotic (Determine 3) with an Intel RealSense 3D RGB depth digital camera connected to its finish effector. The digital camera helps the robotic visually establish the tote and measure its peak for choosing.
The CapSen PiC 2.0 software program, working on an industrial PC with a graphics processing unit (GPU), permits the robotic to plan its movement, find, decide, and manipulate the tote and transfer it towards one other conveyor headed to the paint sales space station. There, the components are unloaded, painted, put into an oven for curing, and inspected earlier than being put again into the totes and onto the conveyor going again towards the robotic, which identifies the tote and locations it onto an outbound conveyor.
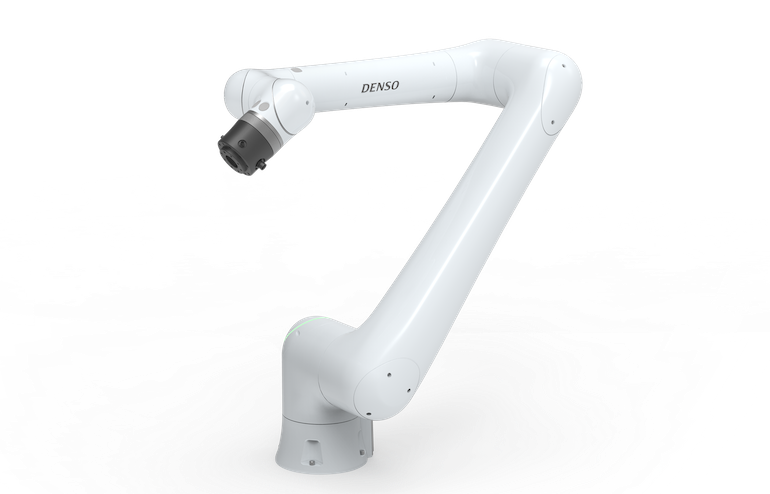
Determine 3: DENSO’s COBOTTA PRO 1300 collaborative robotic, for reference solely. Supply: Invent Automation
Companions deal with maneuverability, imaginative and prescient challenges
Exact actions alongside a number of axes are required for the robotic to select and place giant totes with out inflicting any collisions. The CapSen PiC 2.0 simulation surroundings allowed the workforce to check the robotic’s maneuverability and guarantee the whole lot was reachable and that the robotic wouldn’t collide with something.
However when the workforce examined the real-world system, it found that totes started to bend after they have been picked up by the robotic. To compensate for the tote’s weight and to make sure fluid movement with out collision inside the compact cell, the companions labored to customise the system.
“We use AI in our software program to allow robots to carry out quite a lot of pick-and-place duties, together with random bin selecting, machine tending, packaging, meeting, and tote dealing with” stated Jared Glover, CEO of CapSen Robotics. “For difficult purposes, particularly these the place the simulation surroundings alone received’t suffice, we customise our AI algorithms and fashions primarily based on information from the manufacturing activity. This permits the software program to optimize the movement of the robotic to permit it to maneuver freely with out collisions and to switch the tote inside the cycle time.”
For DENSO’s tote-handling challenge, CapSen Robotics first educated its AI software program to detect and localize the tote’s deal with. The RGB-D digital camera captures photos of the deal with, and the software program runs machine studying algorithms that detect the deal with, permitting the software program to then do the movement planning for the robotic.
As soon as the robotic’s finish effector is positioned into the deal with, the load of the tote should be recognized so the robotic doesn’t cease working or make sudden jerk motions that trigger the tote to fall. As an alternative of utilizing a scale, CapSen’s software program analyzes the torque values on the motor and makes use of these values to find out the load for choosing.
“Utilizing the torque sensing of the robotic to acquire the load and naturally affirm that the tote was picked up was a precious poka-yoke that CapSen added to the system,” stated Kevin Peek, manufacturing engineer at DENSO.
As well as, some machine imaginative and prescient challenges emerged in the course of the design and set up of the system, however the collaborative workforce labored collectively to forestall them from changing into a difficulty.
“Stacks of totes can even have as much as six totes in them, so the system wanted to make sure correct stacking,” in keeping with Peek. “If there are solely two totes, possibly it’s much less of a difficulty, but when there are six totes stacked up and one will not be nested correctly, the entire stack might fall over and trigger a giant delay within the course of.”
To resolve this problem, the system is designed so that after a robotic units a tote onto a stack the robotic strikes backward barely to view the stack with the digital camera. Machine studying algorithms within the software program helped the system to search for a niche between two totes and guarantee correct stacking, whereas the software program additionally counted and verified the right variety of totes within the stack.
Register in the present day to avoid wasting 40% on convention passes!
DENSO stories zero drops, zero missed picks
Finally, the versality of the CapSen PiC 2.0 software program led to it being chosen because the software program answer for this challenge, because it permits finish customers to totally use all the information coming from the completely different items of system {hardware}. That is as a substitute of working by native programming, like when utilizing a programmable logic controller (PLC). On this software, there is no such thing as a PLC within the cupboard.

Determine 4: CapSen PiC’s intuitive HMI reveals system standing and makes the method of working the operation easy. Supply: Invent Automation
All the pieces is dealt with within the CapSen human-machine interface (HMI). Operators can use it to regulate machines, get hold of robotic calibration data, and visualize what the digital camera sees, amongst different options (Determine 4).
The person interface was designed in order that non-technical workers are empowered to function the system as a part of their each day routines with out the necessity for automation or engineering experience.
The software program can also be {hardware} agnostic, which offered a particular profit to DENSO. Actually, preliminary testing of the system concerned cellular manipulation, the place an autonomous cellular robotic (AMR) carried the robotic across the facility with the aim of transferring totes and different containers all through the warehouse.
On this configuration, CapSen’s software program controls the AMR, obtains coordinates from it, and sends correction directions to the AMR to line up the AMR to circulation rack lanes.
Whereas stacking and destacking totes is a standard software in industrial environments, this technique was designed with flexibility in thoughts, in order that it may be expanded or retrofitted to different purposes or made cellular with an AMR.
As well as, for the reason that system was put in, the robotic has not dropped one tote or missed one decide, eradicating each a bodily and metaphorical weight from the shoulders of DENSO workers.
In regards to the creator
Bo Ridley is government vice chairman at Knoxville, Tenn.-based Invent Automation. He beforehand labored as a manufacturing engineer and a machine designer at DENSO. This case examine is posted with permission.